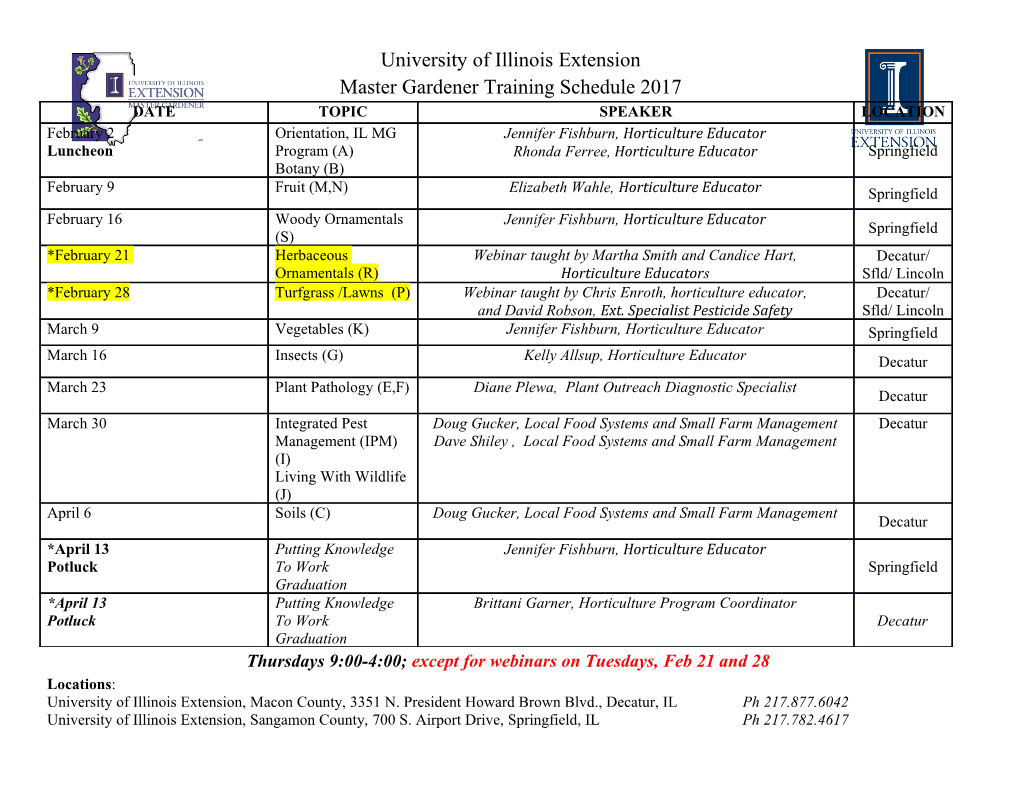
Chemo-Thermal Micromachining of Glass: An Explorative Study A thesis submitted to the Graduate School of the University of Cincinnati in partial fulfilment of the requirements for the degree of Master of Science In the Department of Mechanical Engineering of the College of Engineering and Applied Sciences by Arham Ali Bachelor of Technology in Mechanical Engineering Motilal Nehru National Institute of Technology Allahabad, India November 2018 Committee Chair: Dr. Murali Sundaram ABSTRACT Engineering materials such as glass and ceramics are finding numerous applications in electronics and communication, optics, chemical, aerospace and medical industries. Glass being a hard and brittle material poses huge machining challenges especially during micromachining. Traditional machining of glass by methods such as drilling or milling are generally difficult to achieve due to reasons ranging from excessive tool wear to abrupt breakage of glass. Chemical etching techniques can produce smooth machined surface on glass. Yet, chemical machining process is usually slow and often fail to produce high aspect ratio unless combined with some other additional masking techniques which are usually expensive. Laser beam machining when performed on glass produces micro-cracks along the machined edge due to uneven temperature distribution and residual stresses due to heat affected zones (HAZ). Wet laser beam machining, i.e. laser beam machining when performed under water instead of air results in considerable reduction in thermal defects. However, portion of laser energy is wasted in wet laser machining as heat loss in water. The motivation of this study is to use to minimize this loss and explore the possibility of utilizing this laser energy being absorbed by the medium to further increase machining. To achieve this, a novel chemo-thermal machining process is proposed in this work. Chemo-thermal micromachining is a laser beam machining process in wet condition where laser beam machining is performed on glass specimen submerged in NaOH solution. Material removal mechanism in chemo-thermal micromachining process is a combination of laser ablation and chemical machining. When laser beam is incident on glass workpiece submerged under NaOH solution, a part of laser energy is absorbed by the electrolyte solution ii thus raising the electrolyte temperature locally thus increasing rate of chemical reaction as chemical machining process is highly dependent on temperature. The feasibility of the process was studied, and it was found that there was considerable reduction in the micro cracks formed along the machine surface. When laser beam machining on glass was performed in air about 20- 23 micro cracks were observed which were reduced to 1-5 when machining was performed using chemo-thermal process. Also, average length of cracks was reduced by about 90%. The effect of machining parameters on material removal rate (MRR) and surface quality that involves surface cracks and built-up edges along the machine surface was further studied using a four-level full factorial experimental design. A finite element model was created and chemo-thermal process was simulated to predict the material removal on borosilicate glass. The predictions made by the simulation were compared with the experimental results and the variations were found to be within 5%. iii iv ACKNOWLEDGEMENT I would first like to thank my thesis advisor Dr. Murali Sundaram for his continuous support. The door to Prof. Sundaram’s office was always open whenever I ran into a trouble spot or had a question about my research or writing. He is not only an excellent academic advisor but also an amazing person. He not only guided me for this research work but also helped me develop a professional and methodical problem-solving approach towards any problem. It is because of him I got the opportunity to work on the laser beam machine at Micro and Nano Manufacturing Laboratory to carry out top quality research. I am thankful to all my lab mates from UCMAN lab for their support. I would specifically like to thank Ketaki Kolhekar, Vamshi Kore, Abishek Kamaraj, Anne Brant, and Andrea Grisell for the numerous discussions and constructive criticism of my work which has helped me. I am grateful to University of Cincinnati for providing me with a generous scholarship reducing my financial burden. Financial support provided by the National Science Foundation under Grant Nos. CMMI-1833112, and CMMI-1454181 is acknowledged. Finally, I am grateful to the most important people in my life, my parents and my brother who have always been a source of motivation. I dedicate this thesis to Dr. Atiya Zaidi, Dr. G R Syed and Atyab Ali Zaidi. v Table of Contents 1 Introduction ............................................................................................................................. 1 1.1 Motivation ........................................................................................................................ 2 1.2 Objectives ......................................................................................................................... 3 1.3 Outline .............................................................................................................................. 4 2 Literature Review.................................................................................................................... 5 3 System Design for Chemo-Thermal Machining Process ...................................................... 13 4 Proof of Concept ................................................................................................................... 23 5 Experimental Study of Chemo-Thermal Machining Process ............................................... 27 5.1 Materials and Method..................................................................................................... 27 5.2 Input parameters and their levels ................................................................................... 28 5.3 Material removal mechanism ......................................................................................... 29 5.4 Study of Built-up edges .................................................................................................. 30 5.5 Cracks formed along the machined surface ................................................................... 33 5.6 Chemical composition of glass ...................................................................................... 36 5.7 Circularity of the hole and surface roughness ................................................................ 39 5.8 Material Removal Rate (MRR) ...................................................................................... 40 5.9 Major findings of Experimental Study ........................................................................... 42 6 Chemo-Thermal Micromachining Simulation ...................................................................... 43 6.1 Material Removal due to chemo-thermal micromachining............................................ 43 vi 6.2 Simulation Results and Validation Experiments ............................................................ 51 6.3 Major Findings from Simulation Study ......................................................................... 53 7 Conclusions and Future Work .............................................................................................. 55 7.1 Conclusions .................................................................................................................... 55 7.2 Future Work ................................................................................................................... 56 8 References ............................................................................................................................. 58 APPENDIX A: List of Publications vii LIST OF FIGURES Figure 1: Power density vs interaction time for different modes of laser machining. .................. 10 Figure 2 Microfluidic mixer[32] and micro needles(scale = 250m)[33] .................................... 12 Figure 3: Schematic of laser reflection and focusing.................................................................... 14 Figure 4: Laser Engraving on Wood ............................................................................................. 15 Figure 5: Experimental Set-up ...................................................................................................... 16 Figure 6: X and Y axis movement controller................................................................................ 17 Figure 7: Condensation of NaOH fumes on focusing lens. .......................................................... 18 Figure 8: Laser Head Annular Air Jet ........................................................................................... 18 Figure 9: Horizontal Air Jet .......................................................................................................... 19 Figure 10: Schematic of 3D printed laser head ............................................................................. 20 Figure 11: 3D printed laser head ................................................................................................... 21 Figure 12: Gap Increase by longer focal length ............................................................................ 22 Figure 13: Laser beam machining performed in air ...................................................................... 24 Figure 14: Laser
Details
-
File Typepdf
-
Upload Time-
-
Content LanguagesEnglish
-
Upload UserAnonymous/Not logged-in
-
File Pages75 Page
-
File Size-