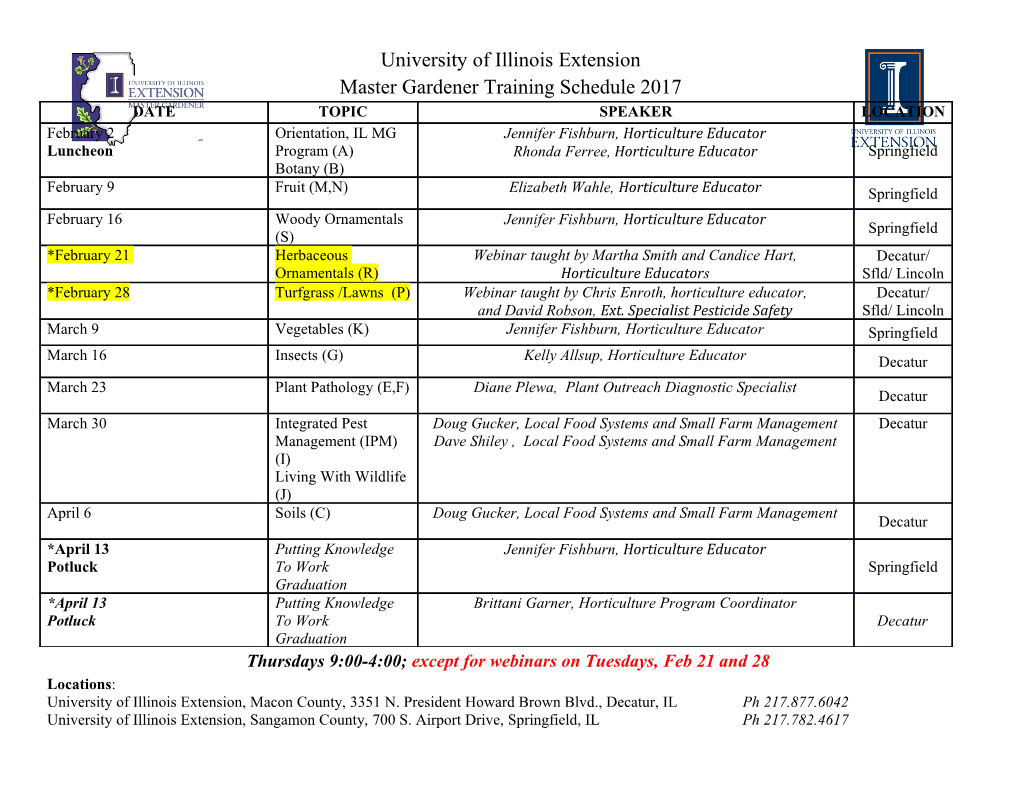
The Laser Microphone Authors: Mark Chounlakone, Julian Alverio Filtering Section: Justin Tunis Abstract The human voice can generate sound waves in the range of 300 Hz to 3400 Hz [8]. These sound waves vibrate nearby objects, making it possible for an analog electronic device to convert these vibrations into an audio signal[1]. One way to accomplish this conversion from movement to audio is to use a "laser microphone", which reflects a laser off the vibrating object and uses a receiver to capture the laser's reflection. The reflection of the laser gets deflected as vibrations shift the surface of the vibrating object. Therefore, if a receiver takes in the oscillating laser signal from a fixed location, the receiver will detect the laser deflections caused by the vibrations that were originally produced from an audio signal. The receiver can then filter and amplify this signal, and output it as audio. Through this process the laser microphone effectively reproduces the audio that induced the object's vibrations. The laser microphone is able to reproduce audio detected from a vibrating surface with relatively high accuracy: less than 8% distortion. As an additional feature, the laser microphone is also able to transmit audio via amplitude-modulated laser signal, capture the laser signal, and output the audio. Thus by using a laser based system that captures oscillations in the position of the laser, the laser microphone is able to accurately reproduce both the audio that induced an object's vibrations and audio transmitted via laser communication. Introduction Human speech is composed of sound waves that vibrate the objects nearby. The goal of this project is to create an analog electronic device that can read in a signal from a vibrating object and reproduce the audio that originally caused it to vibrate.This project achieved this goal with the laser microphone, which is a device that shoots a laser at the vibrating surface and captures the reflection with a receiver. The vibrating surface translates the position of the laser's reflection, thus allowing the receiver to output the laser input signal through speakers as audio. Thus the laser microphone can reproduce the original audio signal that induced the object's vibrations through a speaker. To function as desired, the device needed to be able to filter out all frequencies in the input laser signal outside of the human speech frequency range. Secondly, the device needed to be able to output audio through a class D amplifier using a switching frequency of at least 400 KHz. Additionally, the device needed to be able to support direct laser-to-receiver audio communication. In order to meet these functional requirements, the electronic part of the system is composed of four stages. The first stage is laser transmission, where the laser will be amplitude-modulated if the device is transmitting directly from laser to receiver. The second stage is a laser reception stage, with a reverse-biased photodiode in a transimpedance amplifier. This transimpedance amplifier offers high common mode gain rejection and high gain. The third stage is a high order signal filter. The last stage is a class D audio amplifier, which switches at a frequency of at least 400 KHz and outputs audio at a maximum voltage swing of at least 8 Vpp. While the main focus of the project is exploring the design of circuitry used to reproduce speech from a captured signal, some mechanical characteristics of the system are also key to the system's success. There are two key mechanical properties that the laser microphone depends on. The first is the acoustic properties of objects which generate vibrations from sound waves. The second is the reflectivity of the object’s surface. Figure 1 Depiction of how a laser can be used to detect mechanical deflections. Figure 1 shows both of these mechanical properties at work. As the surface shown on the left shifts, the reflected beam of the laser changes position. Since this project was focused around the electronics, we chose to simplify the mechanical challenges by building a few setups with ideal mechanical properties. These setups are described in the system design. System Design Figure 2 A flow diagram of audio reconstructed from the laser microphone The laser microphone is a very sensitive device which must detect minute surface deflections caused by audio. The detection is done using a photodiode and a transimpedance amplifier. The signal observed by the photodiode is a noise injected version of the audio signal of interest. Noise is injected through mechanical vibrations, ambient light, and the photodiode itself. To produce a coherent reconstruction of speech, the l laser microphone filters out the noise in the transimpedance amplifier and the preamplifier. Once the audio signal has been cleaned, it is sent through the class D amplifier which then plays back the signal on a speaker. Laser Transmitter The first stage of the laser microphone is the transmitter. For this project, there were two modes of transmission, each built separately. The first mode was reflected transmission. This is the mode that has been discussed the most so far. The laser is shot at a vibrating surface and the receiver captures the reflection. The circuit was simply a 5mW red laser pointer connected directly to a 5v supply which is not shown. Figure 3 A depiction of the circuit used to directly communicate to the receiver with the transmitter The second mode of laser transmission was a direct communication mode. In this regime, the laser is modulated with an audio signal and the receiver captures the beam directly. The circuit used for direct communication is shown in Figure 3. The laser diode is depicted as an LED, D1. The power output of the laser had to be modulated with the signal being sent so that the circuitry on the receiving end could reconstruct the signal. To do this an audio signal centered around 5V was sent through a simply op amp buffer which drove the laser diode. By driving the laser diode with a modulated voltage around it’s operating voltage, the power is modulated. While this circuit works, it is not the most elegant way to modulate the laser. Laser diodes are fairly sensitive devices and will die without a proper current regulating circuit. This laser diode was not a laser pointer so it used a as resistor a current regulator rather than a proper laser driver. A smarter design would use a voltage controlled current regulator to modulate the current at a fixed voltage. Laser Receiver Figure 4 A depiction of the photodiode and transimpedance amplifier used to receive the signal. The second stage of the device was the laser receiver. This stage was designed to capture the reflected laser signal and turn it into a voltage. The receiver was composed of a photodiode and a transimpedance amplifier (TIA). In Figure 4, the photodiode is depicted as a normal diode between the inverting inputs of two op amps. The photodiode is the sensor that captures the laser signal. In reverse biased mode, the photodiode has a reverse current which is linearly related to the light irradiance. Once a reverse current is generated, the TIA the current into a voltage. The TIA topology shown in Figure 4 incorporates a differential amplifier. The differential amplifier gets rid of interference caused by ambient light using common mode rejection.The reason the is necessary is explain later in this section. This TIA topology can be described in two parts. The first part is composed of two op amps to create two inverted signals. The non-inverting inputs of the op amps are set to 5v and 0v such that the photodiode is reverse biased. When light generates a reverse current in the photodiode, the current must pass through both resistors. Ohm’s law states that V= IR, so the current passing through the resistors generates proportional voltage signals. The photodiode’s datasheet states that the reverse current is on the order of tens of microamps, so 920K resistors were selected to gain the current. The output of the bottom op amp is the inverse of the top op amp’s output with some dc offset. These two signals are then ac coupled by the 1mF/2.2M capacitor resistor pair, which gets rid of the offset. The capacitor and resistor pairs are ac couplers which also act as high pass filters. I just choose a frequency, .07 Hz, below the vocal range as a corner frequency. The second stage of the transimpedance amplifier is a differential amplifier which was previously described. Figure 5 A depiction of the photodiode and the original transimpedance amplifier design. So why was the differential topology chosen? Originally we had a different design. This one was more simple but without the second stage of the amplifier, ambient light was interfering with the signal. The difficulty with the ambient light did not come from the steady state offset, but from changing ambient light. Just moving around the photodiode would change the amount of ambient light detected, causing the entire signal to shift. Originally we built a box to isolate the photodiode from ambient light, but alignment became much more difficult. Professor Jacob White proposed this new topology as an elegant solution to the ambient light issue. So to reduce the amount of time spent fixing a mechanical issue, the design was expanded to compensate for the interference and the box was no longer necessary. Another nice attribute of the circuit above was that it doubled the signal we received since the current flowed through two resistors. This topology is also able to add more gain in the differential amplifying stage.
Details
-
File Typepdf
-
Upload Time-
-
Content LanguagesEnglish
-
Upload UserAnonymous/Not logged-in
-
File Pages21 Page
-
File Size-