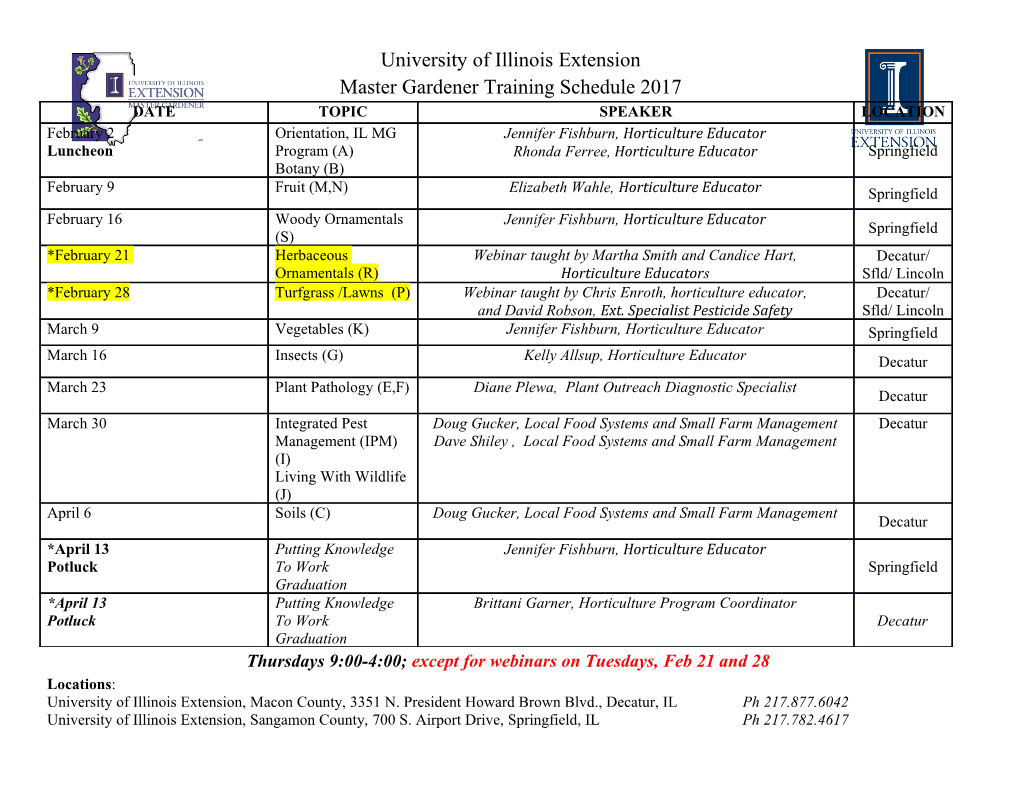
CHAPTER 3 PRECISION CLEANING APPLICATIONS 3.1. BACKGROUND Precision cleaning applications are characterised by the extremely fine level of cleanliness required to keep delicate instruments and surfaces operating effectively. Although precision cleaning is needed in a wide variety of industries, several key factors define the applications where precision cleaning is required. These include those applications in which (1) critical cleanliness standards of particulate and/or organic contaminants need to be satisfied, (2) components have sensitive compatibilities, (3) components I $ have physical characteristics such as geometry and porosity which make dewatering crucial in the cleaning process, and (4) components being cleaned are costly. A variety of particulate and nonparticulate contaminants are removed in precision cleaning operations. Particulate contamination includes scrap material created during cutting, drilling, grinding, and buffing of precision parts (e.g., silicon wafers and aluminum storage disk substrates). Nonparticulate contamination includes waxes, finger print oils, and other contaminants. As the term suggests precision cleaning involves cleaning components to extremely strict standards of cleanliness. A good indication of the cleaning ability required for precision cleaning processes is provided in Figure 111-1, which shows the clearance on a computer disk drive relative to the size of various contaminants. The factor that made CFC-113 the precision cleaning solvent of choice is its remarkable chemical stability (manifested directly in its compatibility to structural materials), its low toxicity, and zero flammability. This has * 1991 UNEP SOLVENTS. COATINGS, AND ADHESIVES REPORT * -1 31- Figure III-I SIZE COMPARISON OF COMPUTER DISK DRIVE HEAD CLEARANCE WITH VARIOUS CONTAMINANTS ' !! allowed closed, superclean, white-room assembly areas to be operated safely and effectively. Probably the most essential example of solvent compatibility is provided by CFC-113 in cleaning beryllium, particularly in the inertial sensor industry. As the performance requirements of gyros increased for both defence and aerospace applications, the need for a structural material that combined low density with high dimensional stability also increased. Hot pressed beryllium has provided that material with a range of properties unique among materials. It has one distinct disadvantage -- chemical reactivity, especially with ionic chlorine. The viability of CFC-113 as a pure, stable solvent has allowed beryllium to be widely used as a structural material. It I should be noted, however, that-mixturesof CFC-113 with methanol will attack beryllium very vigorously. 1,l.l-Trichloroethane is the solvent of choice in some precision cleaning applications. Several of its physical properties -- higher solvency, moderate evaporation rate, and higher boiling point -- make it a unique product for cleaning some soils, such as heavy grease. A number of companies have successfully tested and are currently using CFC-113 and l,l,l-trichloroethane alternatives to clean precision instruments. Companies also are implementing conservation and recovery practices to reduce solvent use in the short-term. Possible alternatives include solvent and nonsolvent options. Solvent options include aqueous and semi-aqueous, alcohols, perfluorocarbons, synthetic aliphatic hydrocarbons, HCFCs and their blends, and other miscellaneous solvents. Nonsolvent options include supercritical fluid cleaning, W/Ozone cleaning, pressurized gases, and plasma cleaning. Although much testing still needs to be done for specific applications , the Committee consensus is that alternatives will be Testing needs to be done. not only to determine cleaning effectiveness but cost and environmental effects as well. * 1991 UNEP SOLVEKTS, COATINGS, AND ADHESIVES REPORT ~ 1 QC substituted for CFC-113 and l,l,l-trichloroethanein virtually all precision cleaning applications by the year 2000. 3.2 CFC-113 AND 1.1,1-TRICHLOROETHANEUSE IN PRECISION CLEANING APPLICATIONS 3.2.1 Precision Cleaninp Processes and Equipment To describe "precision cleaning" in a simple succinct way is difficult. To overcome this difficulty an integrated manufacturing system is described in which the differences in "metal cleaning" and "precision cleaning" become apparent by the nature of the components and the cleaning process. Figure 111-2 shows a diagram of such a plant in which parts are manufactured, deburred, gauged, cleaned, and stored. In the assembly areas, usually a clean room, parts and components are passed through a-preliminary "goods inwards" cleaning process and then into final assembly and test. In the final assembly stages, mostly manual, multiple operations are carried out on a given item and the parts are repeatedly cleaned, during and after each assembly stage. When complete the finished item is passed through factory or PT' "acceptance" testing and then delivered either to detailed functional testing or direct to the customer, who might be another part of the same manufacturing complex or another company. Functional rejects, occurring during acceptance testing are often torn-down, the parts recleaned, and returned to the assembly process. r: In the first stage, parts manufacturing, single parts will be formed by machining, stamping, pressing, etc. The cleaning requirements include the removal of burrs and other mechanical residues as well as the removal of gross residues of machining oils or other processing residues. In this stage, vapour degreasing with l,l,l-trichloroethaneis virtually universal. Within the second clean room assembly area, CFC-113 is pre-eminent. Its particular properties of nonflammability, low toxicity, and * 1991 lJ?TEP SOLVENTS, COATINGS, AND ADHESIVES REPORT * -In, - !! m x a3 K S 0 P - L low odour allow it to be used in small cleaners within laminar flow cabinets or in bench tops close to the operator's working position. Typical devices made in such areas usually contain a very wide range of materials. In addition, many items are fixed using synthetic resins, local soldering operations on custom-built hybrid devices are required, and many solvent sensitive polymers such as polycarbonate and polyether sulphones can be used. The availability of CFC-113 has obviously been vital in such an operation. Replacement of currently used solvents is relatively easy in the "parts cleaning" stage of manufacture. Because the basic components are usually one I part items, they can be cleaned very effectively using alternatives such as aqueous and semi-aqueous systems. If this system is incompatible with the i parts, due to corrosion sensitivity or shape limitations, then solvents such P , 7 as alcohols, HCFCs, and hydrocarbons can be used, particularly if modern, seafed cleaning equipment is available. Introducing alternative cleaning materials or processes is particularly I difficult in the final assembly precision cleaning area. This is not due to il the nature of the soils involved, but to the very wide range of materials used in the manufacture of the assemblies and the minute clearances and complexity found in such devices. Thus a possible definition of precision cleaning might include: 0 Assembled units with complex shapes and very small clearances L 0 A wide range of metallic and nonmetallic components, including many elastomeric materials 0 Blind holes and galleries with capillary gaps which make evaporation of low vapour pressure fluids such as water impossible. Such work pieces are not always small; complete auxiliary power generators and military aircraft generators can be immersion cleaned using CFC-113 during maintenance operations, 'thus avoiding costly and risky disassembly and reassembly of the units. Alternative cleaning materials or * 1991 UNEP SOLVENTS, COATINGS, AND ADHESIVES REPORT * processes, therefore, are required to have low surface tension, low viscosity, and relatively high vapour pressure, or must be designed with new cleaning and drying technologies which can be applied to alternatives such as aqueous and semi-aqueous cleaning systems. The standard equipment used in precision cleaning is a vapour degreaser comprised of a boiling sump, a hot clean rinse stage with ultrasonic generators, and a vapour blanket. These units are often fitted with mechanical handling equipment and installed at the incoming location adjacent to clean areas, so that parts, sub-assemblies, and proprietary components can be cleaned and sealed in bags being transferred to the clean room assembly area. Within clean room assembly areas, smaller CFC-113 and l,l,l- trichloroethane vapour degreasers with ultrasonic generators are often installed close to inspection and assembly areas, so that local batch cleaning F can be performed. Bench-top ultrasonic cleaners are used in clean rooms and are often < installed within laminar flow boxes. These ultrasonic units are cold cleaners in which water is used as the energy coupling medium. Clean glassware containing a small volume of CFC-113, often no more than 100 mls, is placed in the water such that ultrasonic energy can agitate and clean the individual components when they are placed in the solvent. This *e of cleaning has a high loss to evaporation; 100 percent of the evaporated solvent is lost to the atmosphere because there are no cooling coils or other forms of vapour containment or collection. Often this technique is combined with particle counting in which the whole CFC-113 cleaning charge is filtered through an ultra-filter after cleaning so
Details
-
File Typepdf
-
Upload Time-
-
Content LanguagesEnglish
-
Upload UserAnonymous/Not logged-in
-
File Pages112 Page
-
File Size-