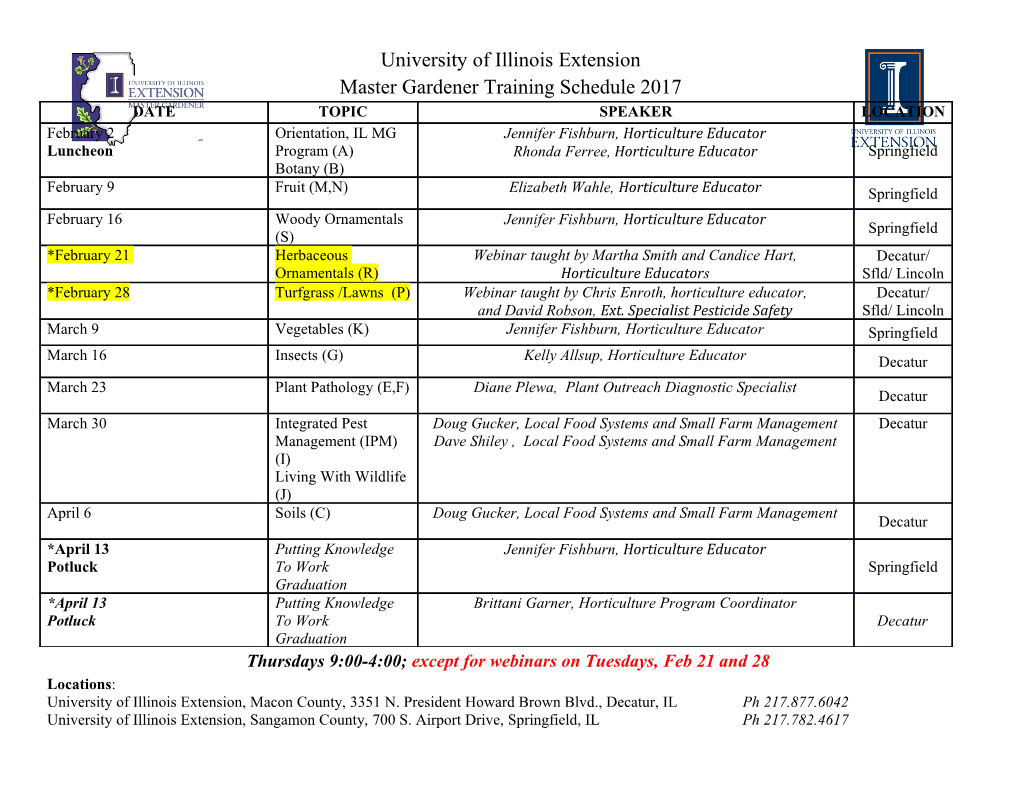
Multidisciplinary Design Optimization in Aerodynamics and Aeroacoustics Master Thesis: Analysis of the A-Pillar Neeti Shetty (neesh311) Link¨opingUniversity Division for Applied Thermodynamics and Fluid Mechanics Master Thesis 2018jLIU-IEI-TEK-A{18/03193-SE 2 Link¨opingUniversity Department of Management and Engineering Division of Applied Thermodynamics and Fluid Mechanics Master Thesis 2018jLIU-IEI-TEK-A{18/03193-SE Multidisciplinary Design Optimization in Aerodynamics and Aeroacoustics Master Thesis: Analysis of the A-Pillar Neeti Shetty (neesh311) Academic supervisor: Hossein Nadali Najafabadi Industrial supervisor: Jari Kesti Examiner: Roland G˚ardhagen Link¨opingUniversity SE-581 83 Link¨oping, Sverige 013-28 10 00, www.liu.se 2 Abstract A roof above your head, when in a car, is made possible due to the component called the A-pillar in the automotive industry. This component is not only responsible for holding up the roof but also in providing a point for the windscreen to be attached. Hence, it is definitely a part that can not be done away with and any problems aris- ing from it must be solved. The flow over the A-pillar causes formation of vortices which causes an increase in the drag generated by the vehicle. These vortices also cause a high level of noise to be generated, which can cause discomfort inside the vehicle, when it is in motion. Hence, there is a need in the automotive industry to modify the A-pillar so as to reduce the generated drag and noise caused by it. In this thesis, the flow around the A-pillar is analyzed and modifications are made accordingly to reduce the impact of the vortices formed due to it. The final re- sulting design of the A-pillar which has been modified from the aerodynamics and aeroacoustics point of view has been presented. This thesis project also includes the optimization of the method used to implement this. The method involved in obtaining an optimized design of the A-pillar started with the geometry cleaning phase in ANSA, followed by the meshing and simulation phase in FLUENT and finally concluding with the optimization phase in HEEDS. The process of doing this methodology has now been optimized resulting in lesser times between the models being cleaned and optimized. The baseline model obtained from these simulations has been validated by com- paring the flow around the vehicle to other works and literature studies. This was done to be certain that the optimization method works to provide correct and ac- curate results. The optimized design, which called for an increased height was then compared against the baseline model, to understand the flow behavior that lead to the reduction of the output variables. Keywords: Aerodynamics, Aeroacoustics, A-Pillar, Optimization Acknowledgements A reflection on everyone who's been a part of the last twenty weeks worth of work and helped make this project what it is, today. - My teammate in this thesis project, Mattias Stridh for the endless discussions and efforts spent in helping bring this thesis project to completion. - My supervisor at CEVT, Jari Kesti for the vital support, guidance and assis- tance rendered throughout the project. - The team of CAE-Energy at CEVT for their valuable insights and pleasant com- pany, that made working on this thesis a pleasure and delight. - My supervisor Hossein Nadali Najafabadi and examiner Roland G˚ardhagen at LiU for their valuable inputs and advice on improving the work and report. Thank You, Everyone. Neeti Shetty Gothenburg, 2018 Nomenclature Abbreviations and Acronyms Abbreviation Meaning ASPL A-Weighted Sound Pressure Level CAA Computational Aero Acoustics CEVT China Euro Vehicle Technology CFD Computational Fluid Dynamics CFL Courant Friedrichs Lewy CPU Central Processing Unit DES Detached Eddy Simulations DDES Delayed Detached Eddy Simulations DNS Direct Numerical Simulations DoE Design of Experiments FFT Fast Fourier Transforms FWH Ffowcs William Hawkings HEEDS Hierarchical Evolutionary Engineering Design System IDDES Improved Delayed Detached Eddy Simulations LES Large Eddy Simulations LiU Link¨opingUniversity MDO Multi Disiplinary Optimization PIV Particle Image Velocimetry RANS Reynolds Averaged Navier Stokes RSO Response Surface Optimization SHERPA Systematic Hybrid Exploration that is Robust, Pro- gressive and Adaptive SPL Sound Pressure Level SRS Scale Resolving Simulations SST Shear Stress Transport URANS Unsteady Reynolds Averaged Navier Stokes Notation Symbol Description Unit A Frontal Area m2 c Speed of Sound [m=s] CD Drag Coefficient [−] Cdes Calibration Constant [−] D Drag [N] k Turbulence Kinetic Energy m2=s2 Lt Turbulent Length Scale [m] M Mach Number [−] P Pressure [P a] Symbol Description Unit 2 Tij Lighthill Stress Tensor N=m v Velocity [m=s] Yk Dissipation term of k [−] β Volumetric Thermal Expansion K−1 δ Kronecker delta K−1 ∆ Characteristic Filter Width [−] Turbulence Dissipation Rate m2=s3 2 νt Kinematic Turbulent Viscosity m =s ! Turbulence Frequency s−1 ρ Density kg=m3 σ Stress Tensor N=m2 Subscripts and Superscripts Character Meaning 0 Reference i, j, k Corresponding x, y and z Directions n Component Normal to the Surface Contents 1 Introduction 1 1.1 Background . .1 1.2 Previous Work . .2 1.3 Aim . .3 1.4 Scope and Limitations . .3 1.5 Problem Formulation . .4 1.6 Report Outline . .5 2 Theory 6 2.1 Flow Around Bodies . .6 2.1.1 Airflow Around a Ground Vehicle . .6 2.1.2 A-Pillar Vortex . .7 2.1.3 Drag . .8 2.1.4 Sound Pressure Level . .8 2.2 Turbulence Modeling . .9 2.2.1 Realizable k- (RKE) . .9 2.2.2 Delayed Detached Eddy Simulations (DDES) . 10 2.3 Computational Aeroacoustics . 11 2.3.1 Lighthill's Analogy . 12 2.3.2 Ffows-Williams Hawkings . 12 2.4 Multi-Disciplinary Optimization . 13 3 Methodology 15 3.1 Geometry . 16 3.1.1 Morphing . 16 3.2 Mesh . 17 3.2.1 Aerodynamic Simulations . 17 3.2.2 Aeroacoustic Simulations . 19 3.3 Solver Settings . 20 3.3.1 Aerodynamic Simulations . 20 3.3.2 Aeroacoustic Simulations . 21 3.4 HEEDS Optimization . 22 3.5 Overall Optimization Method . 23 4 Results and Discussion 25 4.1 Baseline Design . 25 4.1.1 Pressure and Velocity Flow Field . 25 4.1.2 Vorticity . 27 4.1.3 Total Pressure on an Iso-surface of Q-Criterion . 28 4.2 Optimized Design . 29 4.2.1 Design of Experiments . 29 4.2.2 Parameter Optimization . 30 4.3 Comparison between the Results from the Baseline and Optimized Design . 34 4.3.1 Drag . 34 4.3.2 SPL . 35 5 Conclusion 38 5.1 Future Work . 39 5.2 Perspectives . 39 References 40 Appendix A Mesh (Aerodynamic Simulations) 42 Appendix B Frequency Range (Aeroacoustic Simulations) 43 List of Figures 1 Flow around the A-Pillar . .7 2 Project Workflow . 15 3 Vehicle geometry considered for simulations . 16 4 Changes due to Morphing . 17 5 Mesh showing refinement regions and inflations layers considered for aerodynamic simulations . 18 6 Mesh showing refinement regions considered for aeroacoustic simulations 19 7 Schematic of the domain and boundary conditions considered for the aerodynamic simulations . 21 8 Workflow of the optimization process in HEEDS . 22 9 Normalized contours of Pressure Coefficient along the car and Velocity Magnitude across a plane at the center of the car . 25 10 Velocity Pathlines along the junction between the windshield and A- Pillar . 26 11 Formation of vortices around the car plotted on an iso-surface of total pressure=0 . 27 12 Normalized Total Pressure plotted on a iso-surface of Q-criterion=1·106 s−2 ..................................... 28 13 Comparison of the effects the input parameters have on the outputs 29 14 Bubble Plot representation of the data in Table 2 . 31 15 Model of the optimized design superimposed on the baseline design (5 evaluations) . 33 16 Model of the optimized design superimposed on the baseline design (10 evaluations) . 33 17 Normalized Turbulent Viscosity Ratio plotted against sections along the Y-Z plane . 34 18 Normalized Total Pressure plotted on an iso-surface of Q-criterion=1·106 s−2 for the optimized design . 35 19 Normalized SPL contours in octave bands . 36 20 Wall Y+ around the car . 42 21 Contours of mesh cutoff frequency on a plane drawn at 700mm from the centre along Y-axis . 43 22 Plot of pressure monitored at four points in the wake behind the side mirror . 44 23 Normalized SPL contours in octave bands . 45 List of Tables 1 Influence of input variables on the desired output values . 29 2 Influence of input variables on the desired output values . 31 3 Normalized drag values . 35 4 Normalized area-weighted average SPL values on the front side window 37 5 Mesh Sensitivity Study for the baseline model (Aerodynamic Simula- tions) . 42 1 Introduction This Master Thesis Project was carried out at CEVT (China-Euro Vehicle Technol- ogy AB), Gothenburg in 2018. Computational Fluid Dynamics (CFD) and Multidis- ciplinary Optimization (MDO) between aerodynamics and aeroacoustics is the focus of this thesis. It deals with the optimization of the A-pillar in terms of aerodynamics and aeroacoustics and also includes the optimization of the method in itself that is implemented to achieve this. This section includes a basic introduction to the A-pillar and the impact the com- ponent as such has on the aerodynamic and aeroacoustic performance of the car. This lays the path for the motivation and aim behind this project followed by the implemented methodology. 1.1 Background A moving vehicle causes the displacement of the surrounding air and generates a resultant resistive force called drag which accounts for the major chunk of the to- tal resistance to the motion of the vehicle. The study of this flow behavior falls under the study of aerodynamics while, the sound caused due to the flow behav- ior which includes the various mechanisms like vortex shedding and separated flow is under the domain of aeroacoustics (a combination of aerodynamics and acoustics).
Details
-
File Typepdf
-
Upload Time-
-
Content LanguagesEnglish
-
Upload UserAnonymous/Not logged-in
-
File Pages59 Page
-
File Size-