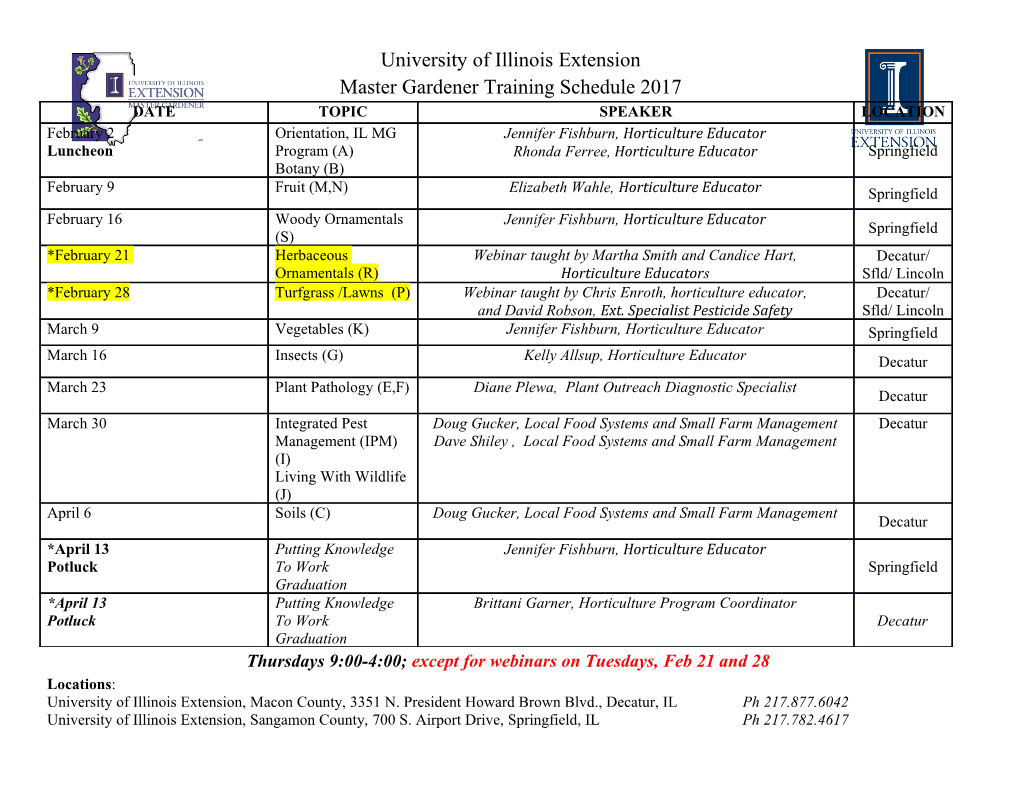
omi.qxp 12/17/2008 10:36 AM Page 1 Of Material Interest Stock car drivers and hot rod racers mix it up on the bobsled track ASCAR and NHRA drivers will square off against one another in a race that has it all – speed, danger, technique, high-performance machines, and merciless punishment for mistakes – in the Geoff Bodine Bobsled Challenge. The event raises funds to advance bobsled technology, and to provide U.S. Olympic athletes with the best possible American-made equipment. Geoff Bodine, winner of the 1986 Daytona 500, started the Bo-Dyn Bobsled Project Nin 1992 to apply NASCAR technology to bobsled design. The teams had been competing with used European sleds, and had not won an Olympic medal since 1956. Since 1994 the teams have been racing sleds designed and built by NASCAR builder, Chassis Dynamics, with support from Whelen Engineering. The long medal drought was broken in 2002 when the teams brought home 3 medals – silver and bronze for the men and gold for the women. All details of sled construction are regulated by the sport’s governing body, the International Bobsleigh and Tobogganing Federation (FIBT). The sleds built for the U.S. bobsled team are constructed of a propriety hybrid fiber composite cowling with a urethane finish using traditional lay-up methods. The cowling is supported by a continuous, TIG welded steel chassis. The steering controls are aluminum; the fasteners are steel. The runners for all competition sleds are made of a steel alloy specified by the FIBT. No post-processing treatments to alter the physical, compositional, or structural characteristics of the steel are allowed, nor is coating or plating of the runners allowed. Within the narrow constraints of the FIBT rules, great care is taken to select the best materials for each component based on such properties as elasticity, vibration absorption, strength, etc. Much research is dedicated to geometric design of the runners and cowling, within the tight dimensional parameters dictated by FIBT rules. Designs are evaluated with computer simulation, wind tunnel testing and, of course, track testing. Not including R&D, a 2-man sled costs about $30k and a 4-man runs about $40k. Each part of the sled is validated by the FIBT before racing with laser-induced breakdown spectroscopy (LIBS) and x-ray fluorescence spectroscopy. The FIBT’s LIBS instrument was designed by a team of Los Alamos engineers to withstand track-side environments without losing analytical capability. With new rigs that take advantage of NASCAR know-how, the U.S. bobsled teams expect to collect some gold, silver, and bronze at the 2010 Vancouver Games. The 4th Annual Geoff Bodine Bobsled Challenge takes place Jan. 2-4. Websites: www.bodynbobsled.com, www.fibt.com Another way down the mountain … … is on the new Makboard, a clear, soft flex snowboard made of a Bayer MaterialScience polycarbonate resin. The Makboard is the only snowboard made from a single material, thus, there are no metal edges to rust or break from impact, nor is delamination a threat. The edges can be sharpened with a standard file, improving edge control on hard pack snow. The board has a tri-hulled bottom, making it more stable than traditional boards when carving turns or going straight. In powder, the concave bottom channels snow through two slots in the tail for better stability. Compared to traditional snowboards, the Makboard ride is smooth and has less chatter. The snowboards are fabricated with a standard injection molding process, weigh about 9.5 lb., and range in thickness from 0.25 in. to 0.50 in. As outdoor enthusiasts, snowboarders will appreciate that the Makboard is 100% recyclable. Websites: www.makboard.com; www.bayermaterialsciencenafta.com. ADVANCED MATERIALS & PROCESSES/JANUARY 2009 9.
Details
-
File Typepdf
-
Upload Time-
-
Content LanguagesEnglish
-
Upload UserAnonymous/Not logged-in
-
File Pages1 Page
-
File Size-