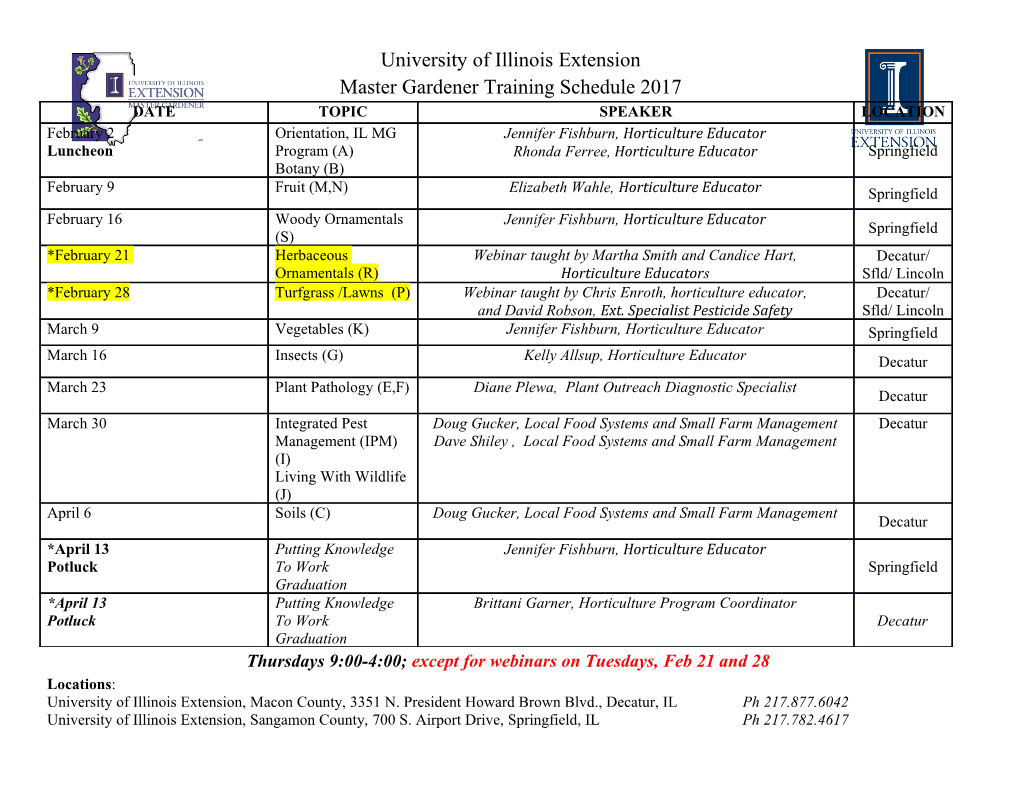
x. AIRCRAFT SYSTEMS, This section is intended to identify the shortcomings of the aircraft systems installed on the accident aircraft and those system’s roles in the chain of events that led to the accident. Conclusions: l The failure of the autopilot to adequately maintain aircraft attitude played a significant role in this accident. l The failure of the autopilot to warn the flightcrew of an impending disconnect played a significant role in this accident. l The lack of an ice detection system played a significant role in this accident. l The lack of adequate visual icing cues and the lack of adequate pneumatic ice protection system operation guidance played a significant role in this accident. l The failure of the regulators philosophy regarding operation and certification of the aircraft’s systems (i.e. anti-deicing equipment) in icing conditions played a significant role in this accident. A. EMB-120 AIRCRAFT AND INSTALLED SYSTEMS The aircraft involved within the accident was a standard EMB120RT and was equipped with a standard avionics suite (Collins Pro Line III) flight director system and autopilot (APS-65). It differed in no conceivable form from any other EMB 120 in the Comair Airlines fleet. As far as ALPA can determine, all systems on the aircraft were operated properly by the crew as required by the Comair Flight Standards Manual (FSM) and all applicable Federal Aviation Regulations and yet the aircraft crashed. Therefore, it is imperative that we not only examine the operation of the aircraft, but also its systems. To do a factual analysis we must analyze data we have collected from the systems that affected the outcome of the accident. We will examine: Autopilot system. Stall warning system. Pitch trim system. Ice detection system or lack thereof. De-ice/anti-ice system (ice/rain protection). A-56B conductive edge sealer. Recording systems FDR, CVR, and potentiometers. Fast/Slow indicator. 1. Autopilot System The autopilot system on the EMB120 is the Collins APS-65 autopilot system. In this accident, it operated normally for its design parameters. The Collins APS-65 autopilot system met all the applicable certification standards when it was designed for commercial use. It was-approved and installed in the EMB-120 aircraft as a part of the aircraft’s initial certification. 45 FDR data showed that the autopilot was being operated by the flight crew with the following modes engaged: heading, pitch, altitude, preselect, (through the altitude alerter) and altitude hold (automatic A/p function after capture). The A/p leveled the aircraft at 4,000 feet, as programmed. The autopilot was then commanded to turn left using the heading mode to achieve the turn the autopilot initiated a left wing down (LWD) roll angle to a maximum target of 25’ (the altitude hold mode was engaged). As the roll angle reached about 20’ LWD, the autopilot inputs started moving in a direction to command right wing down (RWD) to slow the LWD rate. The left roll angle gradually increased beyond the autopilot target of 25” LWD as the autopilot continued to increase RWD input. FDR data also showed that the autopilot was commanding nose-up trim at an increasing rate during the turn (pitch remained about 3”nose up) as the roll angle exceeded 45” LWD the autopilot disconnected and the stick shaker momentarily activated. At this point the control wheel abruptly deflected 20” right to 20” left (40’ total) and aircraft pitch went from 3” nose-up to 50’ nose down handing the flight crew an out of trim, uncontrolled aircraft in an unusual attitude close to the ground. The autopilot, in this accident, did meet the FAA’s certification requirements. ALPA believes these certification requirements need to be changed to eliminate problems identified in this and previous accidents. Autopilot systems need to be certified by the FAA with proper failure “warnings”. Currently there are no requirements for a “soft” failure or warning mode for autopilot systems. An aural or visual warning prior to reaching a servo or bank/pitch limit may have alerted the crew to a possible control problem or performance degradation of the aircraft prior to the upset. This problem does not just exist in the EMB-120 but is in ALPA’s opinion an industry wide problem that effects many aircraft that are equipped with “older” design autopilot systems. Page 18 of the Embraer Operations Bulletin 120-002/96 (attached) refers to “Flight in Normal Icing Conditions”. Page 19 (attached) has a section titled “Climb/Cruise” which has multiple references to autopilot operations which are recommended for flying through normal icing conditions. Page 19 of the Operations Bulletin states: i “Climb mode,mainly on thoseMOD 67G autopilotswith 155 KIAS climb speed,is not recommended.Instead, useIAS modeat 170KIAS. With AP engaged. UseHDG and % Bank mode. Continuouslymonitor airspeedand autopilot operation. Be alert for mistrimmedcondition that may be maskedby the autopilot. Periodicallydisengage the autopilot and checktrims - keep the aircraft trimmed all the time. With autopilot on or off, increaseairspeed if buffet onsets.? It is important to note that ATC predicates all handling in the terminal environment based on standard rate turns. It is curious that Embraer does not recommend manually flying the aircraft at a reduced bank angle limit (‘/z bank mode). Also there is no prohibition against operating the MOD 46 67G autopilot in “normal ice” in the climb mode, which will maintain 155 KIAS to Flight Level @X) 200 (20,000’) and decreasesto 135 KIAS at FL320 (32,000’). ALPA believes the above statements show Embraer’s knowledge of autopilot deficiencies gleaned from information discussed in the incident section of this report along with Embraer internal documents. On March 21,1997 ALPA requested that the NTSB consider making the following urgent safety recommendation affecting autopilot operation: “The FAA should immediately require that all operators of the EMB-120prohibit autopilot operation while the aircraft is accreting ice of any intensity. ” This ALPA recommendation was prompted by the documented incident history of roll upsets while operating in icing conditions with the autopilot engaged. ALPA believes that limiting the use of the autopilot in icing conditions is the most prudent course of action to take until the interactions between the aircraft and the autopilot are fully understood. This ALPA recommendation went unanswered by the NTSB and was not addressedin the NTSB’s urgent safety recommendations of May 1997. It is ALPA’s belief that Embraer is aware of the problems in the autopilot system. ALPA also believes that the FAA must certify autopilot systems with proper “warnings” built into the system. Currently there is not an autopilot “soft failure” or warning of impending failure/disconnect required for certification of the autopilot system. Had a aural/visual warning been available to the CMR 3272 crew to warn them of the impending autopilot disconnect due to a servo or bank angle limit being reached, the crew would have been alerted to the state of the autopilot operation prior to the abrupt, uncommanded disconnect. There are several simple modifications that could be made to provide such a warning. 2. Stall Warning System The stall warning system on the EMB120 is designed to prevent the aircraft from attaining high angles-of-attack, which could result in high bank angles or potential loss of longitudinal control. It is ALPA’s belief that this system in its present configuration is inadequate for flight in 14 CFR Part x 25, Appendix C icing conditions. Currently the system is unable to compensate for any aerodynamic degradation. Other aircraft currently use a “biased” stall system to reduce the triggering threshold when the de-ice : /anti-ice system is engaged to account for aerodynamic changes, such as increased stall speed, that may occur when flying in icing conditions. The EMB 120 is currently not equipped which such a biasing system that would help to prevent a loss of aircraft control in icing conditions. ALPA believes a biased stall system would have been a beneficial tool in preventing this accident, and recommends the immediate installation of such a system all EMB-120 aircraft. 47 3. Pitch Trim System Currently, the EMB-120 is not equipped with an aural trim-in-motion system. Therefore, it is not readily apparent to me flightcrew that the autopilot is applying pitch trim unless this information is acquired visually by purposely looking down and noticing the manual trim wheel to be rotating. Currently, many flightcrews, in an effort to adapt to the lack of an aural warning, place their leg against the manual trim wheel to assesswhen the system is in motion, which is inadequate. It is ALPA’s contention that the addition of an aural trim-in-motion annunciation system would greatly enhance flightcrew situational awarenessnot only during normal operations, but in times of i increased workload such as approaches, adverse weather, and trim system malfnnctions. 4. Ice Detection System * The EMB 120 was not equipped with an ice detector system and relied solely on visual cues by the flight deck crew to determine when to operate the ice/rain protection systems of the aircraft. ALPA believes Embraer determined during tanker testing that visual cues were no longer adequate for icing identification and detection, and in April of 1996 issued Operations Bulletin 120~002/96 entitled Operation in Icing Conditions. This document recommended changes to the operation of the ice/rain protection system from one of deicing to anti-icing due to the previous tanker testing. However, distribution of this document to flight crews was not mandatory. In fact, the accident crew never saw this information. It is obvious from the aircraft’s previous icing encounter and roll-off history that techniques for detection and evaluation of ice accretion on this airplane were not effective.
Details
-
File Typepdf
-
Upload Time-
-
Content LanguagesEnglish
-
Upload UserAnonymous/Not logged-in
-
File Pages12 Page
-
File Size-