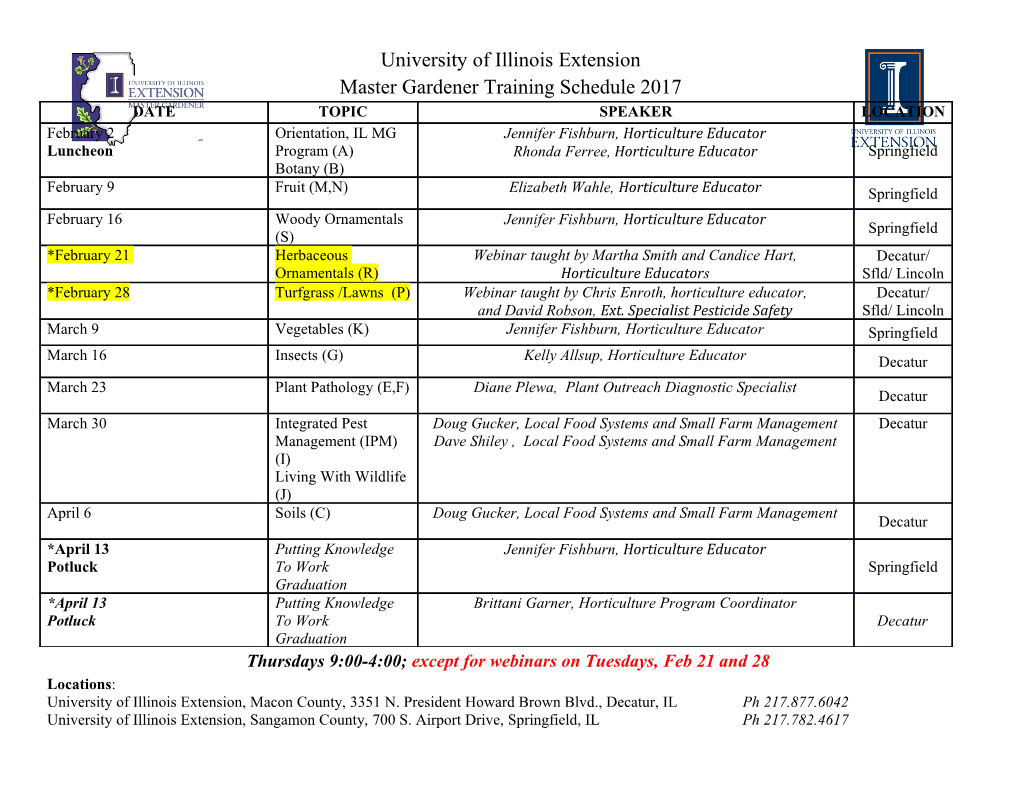
Overview Aluminum Composites The Properties and Application of Scandium-Reinforced Aluminum Zaki Ahmad Scandium-reinforced aluminum industries. The information on scandium- ADVANTAGES OF alloys represent a new generation of reinforced alloys is scanty; very little SCANDIUM ADDITION high-performance alloys that display has been published on the mechanical, numerous advantages over high-strength microstructural, and corrosion behavior Scandium-reinforced aluminum aluminum alloys. Scandium-reinforced of these alloys. The following fills alloys offer design engineers several alloys are much stronger than other this gap. significant advantages over other high- high-strength alloys, exhibit significant strength aluminum alloys, including: INTRODUCTION grain refinement, strengthen welds, and • Inhibition of recrystallization. eliminate hot cracking in welds. These Scandium, a novel alloying element Transition metals such as zirco- alloys also exhibit a good resistance to for aluminum, is mined and processed in nium, chromium, manganese, corrosion as shown by recent studies. Zhovti Vody, Ukraine, the only primary vanadium, or titanium are not very A review of their mechanical, micro- scandium mine in operation in the world. effective at inhibiting recrystalliza- structural, and corrosion characteristics The mine has a proven minable scandium tion because most of the high- shows that scandium-reinforced alloys reserve of 7.58 million t of ore grading strength and precipitation- can be usefully employed in aerospace, at 1.5 g/t of scandium, likely to yield hardenable aluminum alloys are sports, transportation, and process 907,185 t of final Al-Sc product. Initial solution-heat-treated at tempera- mining and processing of the complex ore and refining of scandium concentrates 670 —Initial Condition have resulted in the Al-Sc master alloy. ) —Cold-Rolled 84% and Heat Treated 25,000 a Ashurst Technology Ltd. developed 650 e ur 20,000 (MP il , a fully integrated program aimed at a h F 630 the worldwide commercialization of 15,000 trengt 1 es to 10,000 scandium alloys. The development of l S 610 yc ld C e Al-Sc alloys first flourished in the Soviet 5,000 Yi 590 Union, where military demand was the 0 Conventional Scandium Modified High- Medium- Medium- main driving force. At the time of the Strength Strength Strength Figure 1. The yield strength of conven- Soviet Union break-up, scandium alloys Al-Mg-Zn/ Al-Mg-Zn/ Al-Mg-Zn/Sc tional and scandium-modified experi- 5356 5356 5XXX were on the verge of major application Filler Filler Filler mental 7XXX alloy in the initial and in MIG 29 fighters because of their cold worked 84% and heat-treated Figure 3. The fatigue life of a high-strength conditions. advantages over the low density and aluminum-magnesium-zinc alloy almost high strength of Al-Mg, Al-Li, and triples when it is welded by a scandium- 370 —5356 Filler other recent alloys. Scandium, with modified 5000 series filler metal. 365 —Sc-Modified 5XXX Filler 360 ) its unique strength and weight-saving 355 80 350 characteristics, has been introduced as 345 70 —Conventional 5356 Filler a potent alloying element in several —Sc-Modified 5XXX Filler UTS (MPa 340 60 335 aluminum alloys (e.g., Al5052 and 50 330 Al7075) in recent years, bringing 40 (mm) 30 Conventional 7XXX Sc-Modified 7XXX about dramatic improvements in their 20 mechanical and physical characteristics. 10 It has been possible to achieve an ideal 0 Figure 2. The ultimate tensile strength of Conventional 7XXX Sc-Modified 7XXX a 7000 series weldment is considerably combination of strength, density, and higher when a scandium-modified 5000 thermal stability because of the unique Figure 4. As shown by crack length in mil- aluminum filler metal is used compared limeters, the Houldcroft test greatly favors to a conventional 5356 filler material. precipitation-hardening characteristics of the scandium-modified vs. conventional The difference is even more pronounced scandium. These alloys are gaining a wide filler metal in the welding of a 7000 series when the base metal is also modified popularity in aeronautical, automotive, aluminum alloy. by scandium. and transportation industries. 2003 February • JOM 35 1,100 filler was replaced with scandium- 1,050 modified filler. Welding studies on L L + ScAl Al 7XXX by conventional filler ) 1,000 3 alloys and scandium-modified 950 933 K 0.52 932 K fillers have shown the capability of 900 (Al) 0.38 mperature (K scandium to convert non-weldable Te 850 (Al) + ScAl 3 alloys to alloys with a promising 800 degree of weldability. In addition, 750 0.2 0.4 0.6 0.8 1.0 1.2 1.4 1.6 1.8 2.0 the weldment tensile strength of Al Scandium (wt.%) 7XXX is significantly improved Figure 5. A binary phase diagram of when welded with modified 5XXX aluminum and scandium. alloys versus conventional 5XXX tures well above their recrystalliza- filler (Figure 2).6 Strength is further tion temperatures. Surprisingly, improved when scandium is added Figure 8. A photomicrograph showing scandium increases the recrystal- to Al 7XXX. the pinning of grain boundaries by lization temperature of aluminum Because of these advantages, the dislocations. alloys to above 600°C, well above scandium-modified aluminum alloys the temperature range of heat- have a promising potential for military treatable aluminum alloys. It has and commercial aerospace applications been observed that the addition of including bulk heads, heat shields, sheet scandium with zirconium is more for upper skin, fuel and exhaust systems, effective than the addition of and in automotive and transport systems. scandium alone.2 The addition of scandium also • Small additions of scandium in the improves fatigue life.6 Medium- to range of 0.2–0.6 wt.% bring about high-strength Zr-Mg-Al alloys failed at a high specific-strengthening 16,000 cycles, indicating their limitation 3 effect. An Al-5.25Mg alloy con- for intended applications. Surprisingly, Figure 9. A TEM micrograph of Al-2.5Mg- taining 2.5% magnesium showed a the fatigue life was increased to 25,000 0.5Sc alloy showing a high dislocation yield strength of 365 MPa, more cycles with a scandium-modified filler density at the sub-grain boundaries. than double the strength of the scandium-free alloy. Scandium metal (Figure 3). In a Houldcroft welding provides the highest increment of test, cracking was significantly reduced strengthening per atom percent of by a scandium-modified filler metal. any alloying element when added When both the filler and base metal are to aluminum.4 Al-Mg-Sc alloys are modified by scandium, cracking is capable of developing strength and eliminated (Figure 4).6 fracture toughness similar to that OPTIMUM AMOUNT OF of Al 2024-T3 alloy. The effect of SCANDIUM scandium addition on the yield strength of conventional and The Al-Sc binary phase diagram is scandium-modified experimental shown in Figure 5.7 As observed from 7XXX alloys is shown in Figure 1.2 the figure, Al-Sc is slightly hyper- • Scandium has the ability to refine 10 µm eutectic and hence, very small amounts grain size. It is a strong modifier of Figure 6. A SEM micrograph showing of Al Sc precipitate could form prior to 3 Mg2Si (dark) precipitates. Black (Fe) and cast structure, and the addition of white particles contain Mg, Ti, and Sc. the solidification of the aluminum phase. scandium makes it possible to The aluminum-rich side of the Al-Sc obtain continuously cast billets with phase diagram shows a eutectic point at a non-dendritic structure.5 655°C. The system has also a very narrow • Reduction and elimination of hot freezing range. The maximum equilib- cracking in welds. The scandium rium solubility of scandium in aluminum modification of welding filler alloys is 0.35–0.4 wt.%. With cooling rates in as well as base alloys are capable of solidification corresponding to the preventing hot cracking. Aluminum continuous casting of ingots, a super- alloy 2618 is known to be hot-crack saturated solution of scandium (up to sensitive, and, when welded with 0.6%) with aluminum is obtained.5 An conventional filler, it develops a 10 µm equilibrium phase Al Sc with Li 3 2 high level of cracking.2 However, Figure 7. A SEM micrograph showing structure precipitates in cast alloys. The rectangular precipitates enriched in Ti, its cracking susceptibility was Al, and Sc. supersaturated solution of scandium in reduced when the conventional aluminum is unstable compared with 36 JOM • February 2003 the solid solution of other transition zirconium is effective in inhibiting metals. The rate of incubation preceding recrystallization through the formation Table IV. Corrosion Rates of Al-Mg-Sc Alloys in 3.5 wt.% NaCl17 decomposition is three to four orders of of extremely fine Al (Zr Sc ) particles. 3 x 1-x Corrosion Rate magnitude shorter compared to Al-Mn These particles are less prone to coagulation compared to Al Sc particles. Alloy (mm/year) (mdd) and Al-Zr alloys and the rate of 3 decomposition is five to six times higher Al-2.5Sc 0.023 1.477 MICROSTRUCTURE 8 Al-2.5Mg-0.10Sc 0.031 1.980 compared to Al-Mn and Al-Zr alloys. Al-2.5Mg-0.15Sc 0.046 2.914 The stability of a solid solution of A microstructural examination by Al-2.5Mg-0.30Sc 0.038 2.460 scandium in aluminum drops with an optical microscopy reveals little in alloys containing less than 0.6 wt% of scan- increase in scandium content under Table V. Pitting Data conditions of long, high-temperature dium. Al-Mg alloys containing 6% on Al-Mg-Sc Alloys17 heating such as those as encountered in magnesium show β-Al-Mg (Al Mg ) E E E 8 5 p pp corr production of billets.
Details
-
File Typepdf
-
Upload Time-
-
Content LanguagesEnglish
-
Upload UserAnonymous/Not logged-in
-
File Pages5 Page
-
File Size-