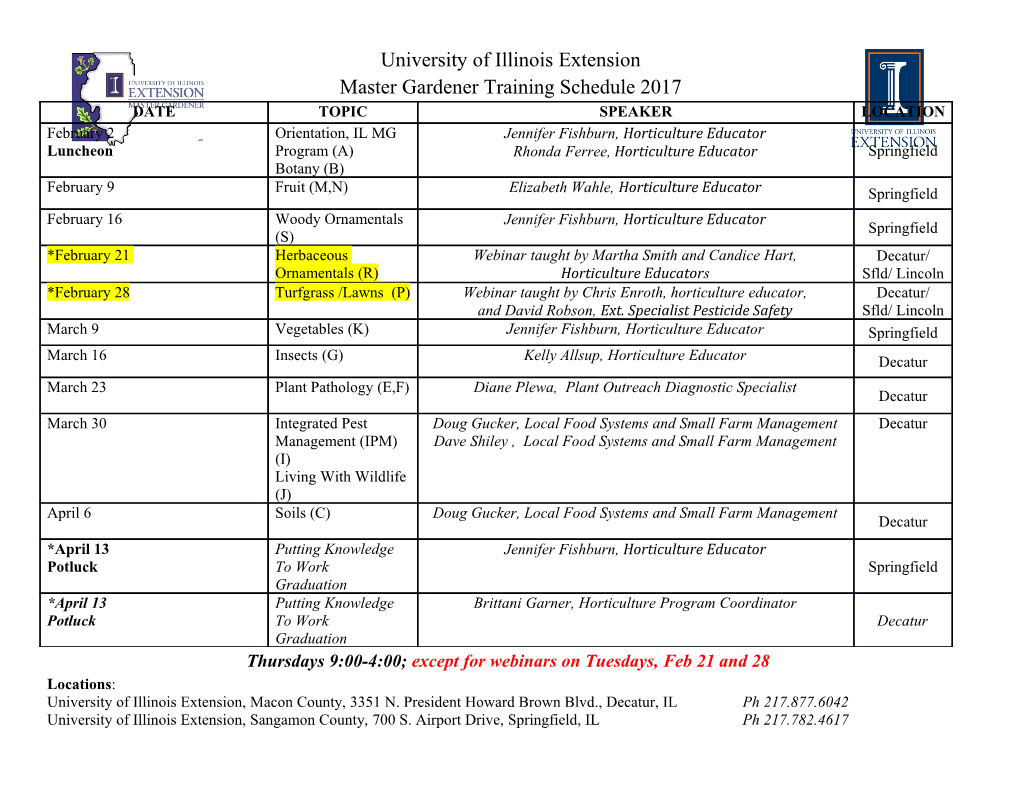
AIMS Materials Science, 5(5): 1000–1015. DOI: 10.3934/matersci.2018.5.1000 Received: 21 August 2018 Accepted: 23 October 2018 Published: 29 October 2018 http://www.aimspress.com/journal/Materials Research article The use of various peening methods to improve the fatigue strength of titanium alloy Ti6Al4V manufactured by electron beam melting Hitoshi Soyama* and Yuya Okura Department of Finemechanics, Tohoku University, 6-6-01 Aoba, Aramaki, Aoba-ku, Sendai, Miyagi, 980-8579, Japan * Correspondence: Email: [email protected]; Tel: +81227956891. Abstract: Additive manufacturing (AM) of metals is one of the foremost methods used for making medical implants and components for aviation. However, the fatigue strength of AM metals is weaker than that of the bulk equivalent. Mechanically treating the surface, such as by shot peening, can improve the fatigue strength, and novel peening methods without shot have also been proposed. In this paper, in order to demonstrate the improvements made in AM metals by various peening methods, specimens made of titanium alloy Ti6Al4V manufactured by electron beam melting (EBM) were treated by shot peening, laser peening and cavitation peening, then assessed by a plate bending fatigue test. In the case of shot peening, the shots were accelerated by a water jet to mitigate the incidence of dust during the process. For laser peening, the specimen was placed in water, and the effect of the impact produced at the target due to collapsing bubbles, which developed after laser ablation of the surface, was greater than the effect due to the laser ablation itself. For cavitation peening, the cavitation was generated by injecting a high speed water jet into water. In each case improvements in the fatigue strength of the Ti6Al4V were made. Improvements of 104% by laser peening, 84% by cavitation peening and 68% by shot peening compared with a non-peened specimen were achieved. Keywords: mechanical surface treatment; medical implant; titanium alloy; additive manufacturing; electron beam melting; fatigue strength; shot peening; laser peening; cavitation peening 1. Introduction Additive manufacturing (AM) of metals is an attractive process for manufacturing medical 1001 implants and aviation components, in the first case because it is easy to make implants that are an order more porous [1] and in the second case because the weight of components can be reduced by the increased design freedom without having to consider machining [2]. Unfortunately, the fatigue strength of AM metals is significantly less than that of their bulk counterparts [2,3]. It has been reported that mechanically treating the surface, such as by shot peening, can improve the fatigue strength of AM metals [2,3]. However, a comparison between the improvements made to the fatigue strength of AM metals by conventional shot peening and novel peening methods, such as laser peening [4–6] and cavitation peening [7], has not been done. Therefore, we carried out an experimental investigation of the use of shot peening, laser peening and cavitation peening to improve the fatigue strength of Ti6Al4V manufactured by an electron beam melting method. As is well known, additive manufacturing, which is also called direct manufacturing, such as by electron beam melting and/or selective laser melting, is suitable for the manufacture of medical implants, since porous implants can be produced and they can be made based on the needs of each individual patient. However, the fatigue strength and/or fatigue life of AM metals is much smaller than that of bulk materials because of the surface roughness. It has been reported that the fatigue life of titanium alloy Ti6Al4V produced by additive manufacturing, rolling and casting decreased as the maximum surface roughness increased [8]. Several methods, including electron beam melting (EBM), selective laser melting (SLM), laser engineered net shaping (LENS) and a wire feed method have been proposed [9,10]. The advantage of EBM is that the build rate is normally larger than that of SLM [9,11]. However, the fatigue strength of EBM materials is smaller than that of SLM materials [9,10,12], as the roughness of the surface is greater [10]. Thus, the main purpose of the present paper is to improve the fatigue strength of titanium alloy Ti6Al4V manufactured by EBM. It has been reported that the fatigue strength and/or fatigue life of titanium alloy Ti6Al4V manufactured by EBM can be improved by shot peening and cavitation peening [2,3]. The conventional method for mechanically treating a surface is shot peening. As mentioned above, shot peening can improve the fatigue strength of AM metals [2,3]. However, shot peening produces dust due to collisions between the shot, and the dust causes dust explosions [13] and a health hazard. In order to avoid these risks, a shot peening technique using recirculating shot accelerated by a water jet was established [14]. This technique was used in this study for shot peening. In the case of laser peening, there are two major methods. One method is to use a powerful pulsed laser, such as one with several J per pulse, to treat the surface, which is covered by a sacrificial layer of tape or paint. In this method, a liquid film is formed on the surface [4,6]. The other method is submerged laser peening which obviates the need for a sacrificial layer [5]. In either case, it is considered that a laser induced shock wave in the liquid results in the material being treated. As is well known, in the case of submerged laser peening, a bubble is generated after laser ablation, and this bubble develops, then collapses, and as its collapse it erodes the surface, the same as cavitation bubble [7]. Thus, in this paper, this process, which follows laser ablation, is called “laser cavitation”. Using a submerged shock wave sensor to measure the pressure amplitude in the water showed that the pressure induced by laser ablation was larger than that by laser cavitation [15]. However, when the force due to the impact was measured by a special homemade sensor developed to evaluate cavitation impact [16,17], the amplitude of the impact induced by laser cavitation was 1.5 times larger than that due to laser ablation [7]. That is, when laser cavitation is considered and optimized, we get two hits, i.e., from laser ablation and laser cavitation, with a single pulse. Thus, in AIMS Materials Science Volume 5, Issue 5, 1000–1015. 1002 the present experiment, the submerged laser peening system was used. In the case of cavitation peening, shots are not required. Thus chemical cleaning to remove material transferred to the surface from the shots is unnecessary. Moreover, since cavitation peening can be used to treat the inner walls of a tube by placing it parallel to the jet axis [18], it can be used in the manufacture of porous medical implants. It has been reported that the fatigue strength of spinal implants made of titanium alloy was improved by cavitation peening [19]. Note that the mechanism for cavitation peening is different to that of water jet peening, in which the impacts of water columns are used to create plastic deformation [20]. Even though the water jet is submerged, the surface can be treated by water jet peening. In the case of water jet peening, a powerful plunger pump with an injection pressure of several hundreds of MPa is required. On the other hand, in the case of cavitation peening, the injection pressure required for a cavitating jet is about one tenth of the pressure required for water jet peening [21]. Thus, risk of surface damage to the implants by cavitation peening is negligible compared to water jet peening, and also the initial and running costs of cavitation peening are less than one tenth of those of water jet peening. Thus, in the present experiments, the effect of cavitation peening using a submerged water jet was investigated. As mentioned above, the impact mechanism to produce local plastic deformation is different for each peening method [20]. The impact of shot with the surface is used in shot peening, whereas the impact induced by laser ablation and laser cavitation are utilized for submerged laser peening, and the impact induced by cavitation bubbles collapsing is used in cavitation peening. Thus, the strain rate for each peening method is different. It has been reported that the plastic deformation in the material and the surface roughness are different when the strain rate of the peening method is different [22]. Thus it is worthwhile investigating the improvements made in the fatigue life and/or fatigue strength of the AM metals used for medical implants by the different peening methods. In this study, to compare the improvements made in the fatigue strength of an AM metal manufactured by EBM by the various peening methods, we used fatigue test specimens made of titanium alloy Ti6Al4V. These specimens were treated by shot peening, submerged laser peening and cavitation peening, then assessed by a plate bending fatigue test. Note that all the test specimens were heat-treated to improve the fatigue strength, as the fatigue strength of specimens without heat-treatment was considerably smaller than that of heat-treated specimens. 2. Experimental apparatus and procedures 2.1. Titanium alloy Ti6Al4V manufacture by EBM Figure 1 illustrates the geometry of the specimens used for the plate bending fatigue tests. All the specimens were manufactured by EBM. The powder used in the EBM process was made of Ti6Al4V and had an average diameter of about 75 m. The spot size of the electron beam for selective melting was 0.2 mm in diameter, and the stacking pitch was 90 m. The specimens, as shown in Figure 1, included 4 holes.
Details
-
File Typepdf
-
Upload Time-
-
Content LanguagesEnglish
-
Upload UserAnonymous/Not logged-in
-
File Pages16 Page
-
File Size-