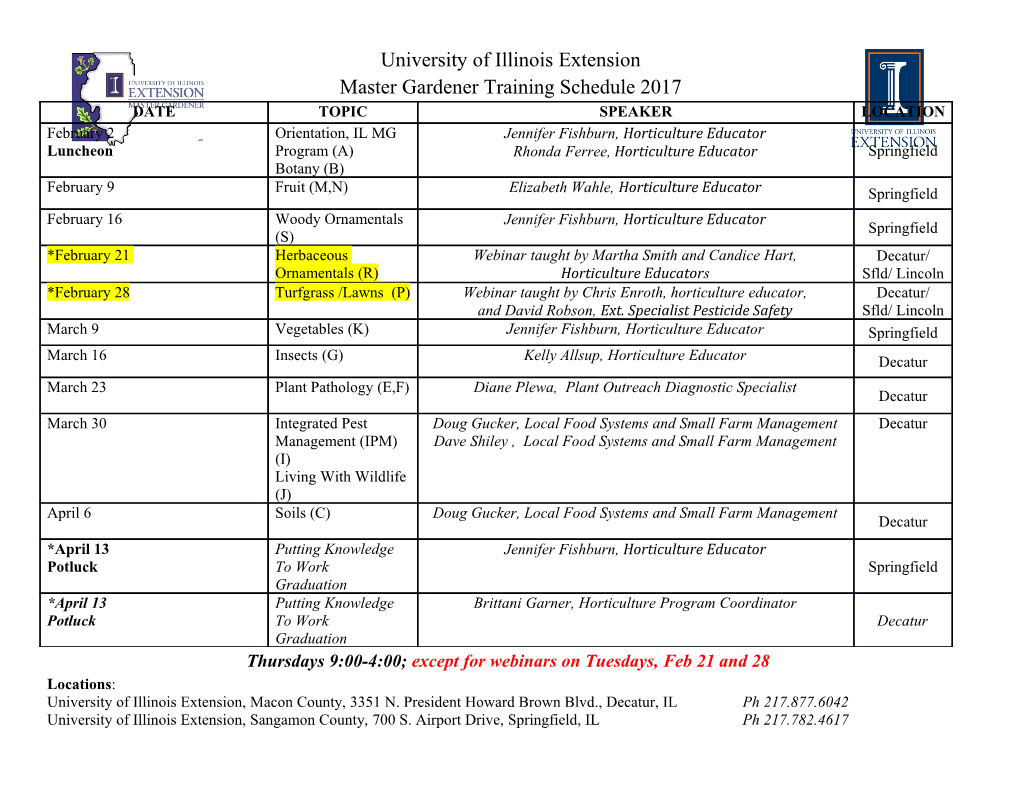
API CENTRIFUGAL COMPRESSOR OIL SEALS AND SUPPORT SYSTEMS— TYPES, SELECTION, AND FIELD TROUBLESHOOTING by Ed Wilcox Senior Staff Engineer Conoco, Inc. Westlake, Louisiana Ed Wilcox is a Senior Staff Engineer with Conoco, Inc., in Westlake, Louisiana, where he is the Reliability Engineer for Excel- Paralubes, a joint venture between Conoco and Pennzoil. He also provides technical support for the adjacent Conoco Refinery. His responsibilities include maintenance, troubleshooting, and specification of rotating equipment. Mr. Wilcox received his BSME degree from the University of Missouri-Rolla and MSME degree from Oklahoma State University. He has also done post graduate work at the Georgia Institute of Technology in the areas of machinery vibration, lubrication, and rotordynamics. He is a Vibration Institute certified Level III Vibration Specialist, a member of STLE, and a registered Professional Engineer in the State of Oklahoma. ABSTRACT Even though dry gas seals for centrifugal compressors are becoming more popular, knowledge and understanding of oil seals and their associated support systems are still very important. Many existing compressors still have oil seals; likewise, dry gas seals have pressure and surface velocity limitations that prevent them from being applied to all applications. The author describes the two most common types of API oil seals so that users can understand the fundamentals of each. Likewise, the strengths and weaknesses for each seal type are listed so users can have input into specification of their seals dependent upon their particular application. Examples are given of problematic seal designs and the changes made to improve them. The support systems for each type of oil seal are described, along with ways to specify the best Figure 1. Combined Lube and Seal Oil System. system for different applications. A step-by-step method is given for troubleshooting seals and their support systems in the field. FACE CONTACT TYPE OIL SEALS Case studies of problematic oil seal systems with solutions are Face contact oil seals are similar to pump seals where two radial presented. faces (one stationary and one rotating, items 15 and 21, INTRODUCTION respectively, in Figure 2) provide the seal between the process gas and seal oil. The stationary face moves axially with the compressor Compressor oil seals are designed around the principle of rotor. A small amount of seal oil is forced between the two sealing forcing oil into the compressor seals at a higher pressure than the faces to provide lubrication and cooling, because the seal oil is at a process gas to prevent the gas from escaping from the pressure higher pressure than the process gas (typically the seal oil casing. In fact, compressor oil seals are not gas seals at all, but differential pressure is 40 to 80 psid). This contaminated or “sour” rather liquid seals designed to minimize the amount of seal oil that seal oil comes in contact with the process gas and is drained away passes into the compressor. The seal oil is normally supplied from to the seal oil traps for reclamation or disposal. Sour oil leakage a combined lube and seal oil system, an example of one such rates are typically five to 10 gallons per day (gpd) per seal. A system is shown in Figure 1. This system is designed to keep the labyrinth seal (item 9) prevents the oil from entering the seal oil pressure above the sealed gas pressure. compressor. The stationary face has a secondary seal (item 12), Oil seals are generally grouped into two different groups: face normally made from a compatible elastomer. The secondary seal contact seals and floating ring seals. The two different types have must slide on the seal housing or stationary face as the rotor floats different strengths and weaknesses that make them attractive axially. Springs (item 10) are used to load the seal faces in addition and/or applicable to different applications. Likewise, their to the hydraulic load, as well as when the seal oil system is not in associated seal oil support systems are quite different. operation. The springs are almost always located on the stationary 225 226 PROCEEDINGS OF THE 29TH TURBOMACHINERY SYMPOSIUM face due to the high shaft rotational speeds encountered in Sweet oil compressors (i.e., high rotational speeds would cause springs to return deflect and result in an unstable seal). Face seals have maximum surface velocity and sealing pressure limitations (Table 1). Table 1. Approximate Pressure and Velocity Limitations of Face Contact Seals. Maximum Surface Velocity (fps) 300 Maximum Sealed Pressure (psia) 500-1500 A floating bushing seal (item 27, Figure 2) is normally used on the atmospheric or outer side of the seal to keep the seal housing pressurized. The seal oil that passes through the outer seal is drained directly back to the lube oil reservoir because it has not come in contact with the process gas. For this reason, it is called uncontaminated or “sweet” seal oil. The bushing seal clearance is sized to maintain the correct differential pressure on the process seal while at the same time providing enough flowrate through the seal housing to cool the seal (normally around five to 10 gpm). Alternatively, some seal designs use a second contact seal on the atmospheric side (Figure 3). This is usually required at high surface velocities, if the oil flow cannot be controlled adequately enough with a bushing seal. Depending upon the seal design and application, the sweet seal oil flow may require a separate drain to the reservoir. The flow through this separate drain is either restricted by an orifice or regulated by a control valve to maintain the seal oil differential pressure. Sour oil Seal oil Sweet oil (Sweet Oil Drain) drain Supply drain (Reference Gas) Figure 3. Double Mechanical Contact Seal. (Courtesy of Flowserve) Process Atmosphere Gas Process Atmosphere Gas (Sour Oil Drain) Figure 2. Mechanical Contact Seal. (Courtesy of Kaydon Ring and Seal) Figure 4. Contact Seal with Center Carbon Ring. (Courtesy of To lower the relative surface velocity between the rotating and Elliott Co.) stationary faces, some face type oil seals include a floating nonmetallic ring (usually carbon, item 1, Figure 4) between the two shutdown pistons (item 14, Figure 6). If the seal oil pressure faces. This ring normally spins at approximately one-half the shaft differential drops to a few psid, the pistons will move in the rotational speed. This lowers the relative velocity between the seal outboard direction and push the seal retainer against the rotating faces to approximately half of the shaft speed. The carbon ring is seat. Alternatively, some seal designs incorporate a separate sealing normally scalloped on the inside diameter to make sure a pressure face for shutdown protection (item 1, Figure 7). This design differential does not exist across it and pressed inside a steel ring prevents process gas from escaping by closing the additional seal (Figure 5). However, the lower velocity does not come without a face on the outside of the contact seal. At the same time it pushes cost, it does add an additional sealing face that can leak as well. the contact seal together. Face seals provide positive shutoff; i.e., they will contain the process gas if the seal oil differential is lost. This is very important Balance in hazardous applications, even if buffer gas is used on the seals. Seal balance or balance ratio is the ratio of the seal face closing Positive shutoff is maintained by the springs as well as a set of area to seal face contact area (Figures 8 and 9, and Equation (1)). API CENTRIFUGAL COMPRESSOR OIL SEALS AND SUPPORT SYSTEMS— 227 TYPES, SELECTION, AND FIELD TROUBLESHOOTING Balance ratios’ for compressor oil seals typically range from 60 to 80 percent, which means that there is a slight closing bias. Leakage rates for compressors are much higher than pumps (typically gallons per day for compressors compared to parts per million (ppm) for pumps) because the faces require more lubrication and cooling. Typically, most compressor seals are designed for a complete liquid film across the entire seal face, in comparison to pumps where it is common for the sealed liquid to vaporize at the inside diameter of the seal faces. The liquid film provides for a much longer operating life. closin garea r 2 Ϫ r 2 Balance = B = = o .b (1) contact area 2 Ϫ 2 ro ri Oil Process gas Figure 5. Relief on Inside Diameter of Center Carbon Ring. ro r ri Figure 8. Balance Dimensions for Outside Pressurized Face Seal. Oil Process gas ro ri r Figure 9. Balance Dimensions for Outside Pressurized Seal. Seal Face Loading The hydraulic axial load on the seal faces is a function of the seal balance, face orientation, differential pressure, and pressure profile across the seal faces (Figure 10). The shape of the pressure profile across the seal faces is a function of the seal face orientation. The seal faces are never exactly parallel. A divergent face profile is Figure 6. Contact Seal Showing Shutdown Piston. (Courtesy of unstable and results in face wear and short run-life. The parallel or Elliott Co.) slightly convergent face profile results in lower leakage rates and is the normal design case (Table 2). Figure 10. Axial Hydraulic Load Distribution on Face Seal. A nonparallel face orientation is not due solely to manufacturing tolerances or installation errors. The seal face runs warmer on the inside diameter because the oil film is thinner on the inside than the outside (Figure 11). Additionally, there is a large temperature gradient in the axial direction as well. These temperature gradients tend to deflect the seal faces in a convergent direction (Figure 12). Likewise, pressure induces moments on the stationary seal faces that “tips” or deflects the seal faces (Figure 13).
Details
-
File Typepdf
-
Upload Time-
-
Content LanguagesEnglish
-
Upload UserAnonymous/Not logged-in
-
File Pages14 Page
-
File Size-