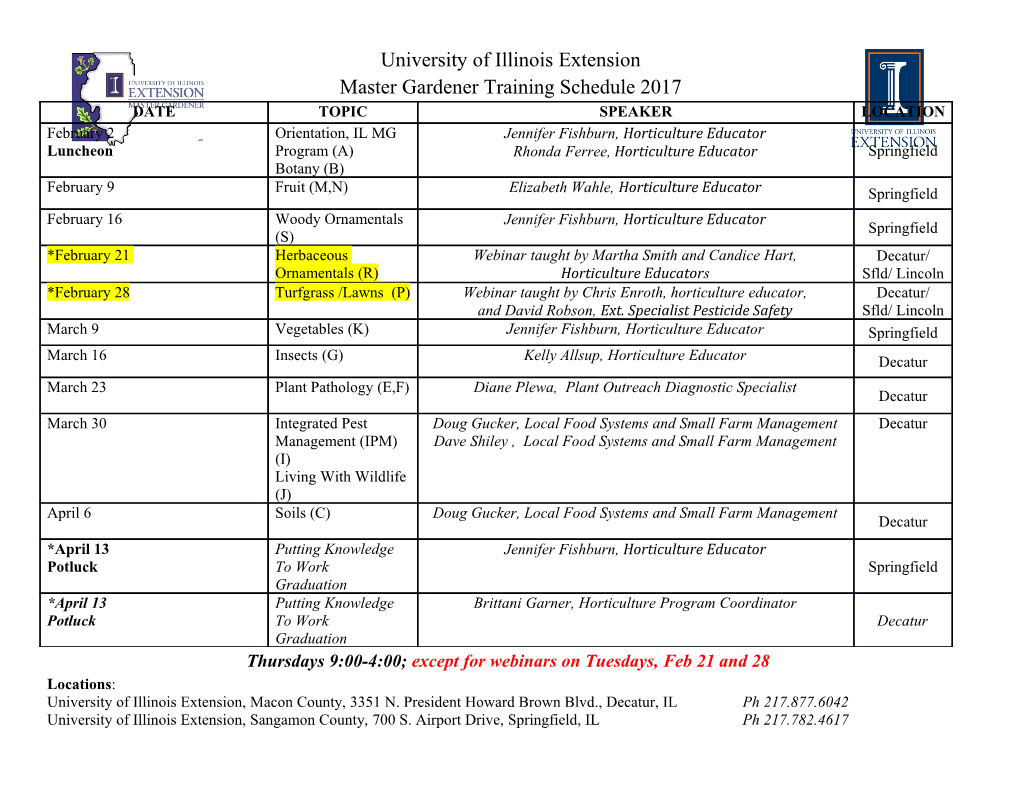
182 PHILlPS TECHNICAL REVIEW VOLUME 27 Integrated circuits with evaporated thin films E. C. Munk and A. Rademakers 539.234 :621.3.049.7 In this article we shall discuss a form of integrated itance or inductance value and the Q that can be circuit in which the conductors, the resistors and the achieved with the thin film components may be too capacitors (and in some cases the inductors as well) are limited. deposited as thin films in a pattern of strips and rec- An example of a thin film circuit is shown in jig. J. tangles on an insulating substrate. The advantages General considerations usually considered in the integration of circuits have been made sufficiently clear in the previous article [11, The integrated circuit - unlike a circuit built up and need not therefore be reiterated here. from individual components - is not flexible, and sub- The thin film technique we shall deal with in this sequent correction is acceptable only in exceptional article may be regarded as an extension of the tech- cases. This means that it is necessary to control the niques in use for making conventional resistors and production process so thoroughly as to make later Fig. I. Example of a pattern of conductors and resistors in an integrated circuit. The conductor layers (dark patches) are tinned. capacitors, in which thin layers of carbon or metal are correction unnecessary; in other words, it should be applied to an insulating body or dielectric foil. There cheaper to scrap a product that fails to meet the speci- are various methods of applying the layers, but we shall fications of the design than to correct it. be concerned only with those where the material is This lack of flexibility becomes particularly evident if evaporated on to the substrate in a high vacuum. one compares a resistor in an integrated circuit with a The su bstrates are small flat plates, or wafers. This resistor as a separate component. In both the resistive is important both in the manufacturing process, as it material is applied in the form of a thin film to an facilitates work with masks and photographic processes, insulating substrate (which is cylindrical in the separate and in the assembly of the circuits in larger systems, resistor). The val ue of the resistance is given by: since the plates can be stacked and interconnections e I R=- - made at the edges. tb' It should be emphasized that the circuits treated in this article are not completely integrated but of a where e is the resistivity, and I, band t are the length, hybrid nature. In a completely integrated circuit the width and thickness ofthe resistive film. The factor elt, active elements as well (diodes and transistors) would the sheet resistivity (also referred to as the resistance have to be made by evaporation techniques. This is per square, RO), is a property of the film itself, and the possible in principle, as explained elsewhere in this length-to-width ratio lib is called the aspect ratio. The number [21, but such elements are still at the research relative error in R is the sum of the relative errors in. the stage. In practice, the active elements are therefore sheet resistivity and the aspect ratio. A conventional added as separate components to the thin film circuit. resistor is made by first applying the resistive material Moreover, it is quite often necessary to fit separate to the body. The accuracy of the sheet resistivity is not capacitors (and possibly inductors), since the capac- critical, since the resistor is given its value with the required precision by grinding a spiral groove into the Drs. E. C. Munk is witli Philips Research Laboratories, Eindhoven, surface layer. This corrects the aspect ratio after the and Dr. A. Rademakers is with the Nijmegen Semiconductor Plant, Philips Elcoma Division. evaporation process. Precisely the opposite applies to a 1966, No. 7 TH1N-FILM INTEGRATED CIRCUITS 183 resistor in a thin film circuit: the dimensions of the nesses are still extremely small, i.e. of the order of resistor are fixed before the film is deposited on the 10 nm. substrate. If there are to be no subsequent corrections, Various other considerations besides those already the aspect ratio and the sheet resistivity are therefore mentioned play a role in the fabrication of evaporated established independently of one another, which means resistive films. In particular we should mention the that this must be done with tolerances which together efforts to achieve films of low temperature coefficient do not exceed the rated tolerance of the resistor. The and high stability: this will be discussed later. requirements for the process of applying ~he resistive If capacitors are to be built up from evaporated thin layer are therefore much stricter than in the manufac- films (a dielectric layer between two metal layers) ture of separate resistors. These requirements become similar considerations indicate the requirements to be even harder to meet if the films for the resistors in a met in the control of the evaporation process, in large number of circuits are to be evaporated simul- particular for the deposition of the dielectric layer. For taneously. The resistive layer must then not only be the conductors, the process is of course less critical. extremely homogeneous over the entire surface of each For inductances the thin-film technique is by its substrate, but must also be identical from one substrate nature not particularly suitable. Without going into to another. These requirements can be met by using the detail, two points may be mentioned in passing: the evaporation technique. three-dimensional character is of more significanee with the inductor than with other elements, and it is The problem can be solved in an entirely different way if difficult to concentrate magnetic energy in a small subsequent individual corrections to the sheet resistivity are allowed. The methods developed by IBM and the Bell Laborator- volume. For simple requirements, inductors may be ies are examples of this approach [3][4]. In both methods evaporated in the form of spirals. In practice this relatively thick films are used, and the thickness is reduced after method cannot be used for inductances greater than a deposition in the required pattern. In the IBM method the few tens of (.LHat the most, and to achieve a fairly resistive material, in the form of a paste, is screen-printed in the reasonable Q the films have to be thickened, e.g. with required pattern upon ceramic wafers. After heat-treatment, the resistance is corrected by sand-blasting. In the second method the a layer of gold. resistive material (tantalum with tantalum nitride TaN) is applied Thin-film effects to wafer substrates by sputtering in a gas discharge. After de. position, part of the film is converted by electrolytic oxidation Before going further into the production of thin-film into non-conducting Ta205. The latter process can now be so circuits, we shall first discuss some physical peculiarities well controlled that a very high accuracy can be achieved. During the process, however, each resistor has to be individually checked. of thin metal films. Moreover, optimum properties can only be obtained provided the The resistance of thin metal films is usually greater sheet resistivity is given a relatively Iow value (e.g. 40 Q). This than the value calculated on the basis of the film thick- means that resistors with a high nominal value can only be ness and the resistivity of the metal; in other words the produced if the aspect ratio has a high value, and this makes it "effective resistivity" of the film is greater than that of difficult to meet the requirement for small dimensions. the bulk metal. An effect of this nature is to be expected in principle By way of introduetion to the subject, let us make an from the theory of electrical conduction in metals. Here estimate of the thicknesses of the films used in these if the thickness of the films becomes smaller than the techniques. Suppose that we wish to form a combi- mean free path of the conduction electrons, the scatter- nation of resistors with a tolerance of 5%, the highest ing of the electrons at the surface will make a percep- nominal value among them being 10 000 0. We tible extra contribution to the resistance. It has in fact choose for this a strip 1 cm long and 100 (.Lmwide. proved possible to determine fairly accurately the mean The aspect ratio is then 100 and so the sheet resistivity free path from resistance measurements on thin films, at is 100 0. If we now unsuspectingly put in the bulk least for very pure metals in virtually ideal thin films. resistivity value for say aluminium (2.5 X 10-8 Om), we Ideal films, that is to say films that are continuous, arrive at a film thickness of 0.25 nm! The tolerance of uniform and homogeneous, are however very rarely 5 % now has to be shared between the aspect ratio and encountered. Usually resistance anomaly in thin films the sheet resistivity. This implies that we have to reproduce not only the width of 100 (.Lmbut also the [1] P. w. Haaijman, Integration of electronic circuits, Philips tech. Rev. 27, 180-181, 1966. thickness of 0.25 nm with a tolerance certainly below [2] H. C. de Graaff and H. Koelmans, The thin-film transistor, 5%. This is scarcely practicable, and it follows that Philips tech. Rev. 27, 200-206, 1966. [3] E. M. Davis, W. E. Harding, R. S. Schwartz and J. J.
Details
-
File Typepdf
-
Upload Time-
-
Content LanguagesEnglish
-
Upload UserAnonymous/Not logged-in
-
File Pages10 Page
-
File Size-