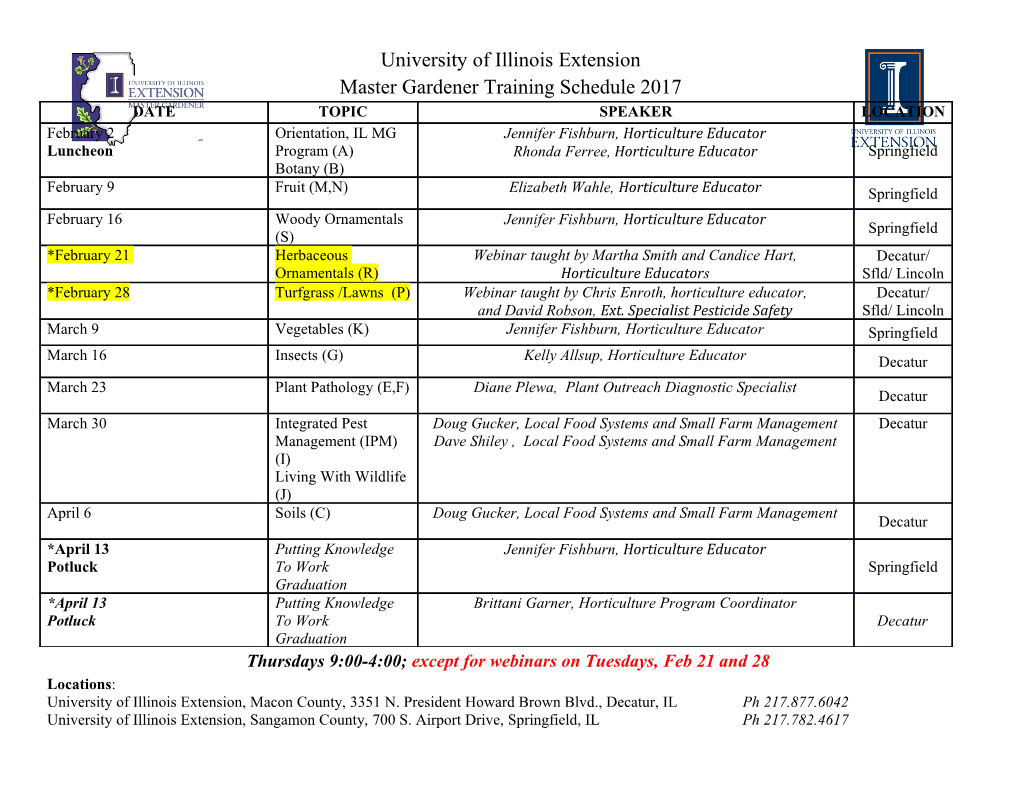
/} ..:./ J" ,.;,' [.~. u v' LfHENIICAL VAPOR DEPOSITION OF SILICON DIOXIDE THIN FILMS FOR COMPOSITE THEAAIO-OXIDATIVE DURABILIT); A dissertation presented to the Faculty of the College of Engineering and Technology Ohio university in partial fulfillment of the requirements for the degree of Doctor of Philosophy In Chemical Engineering \\ J .' ',t : ». ..,~ Sudarsan Neogi/ November, 1992 'OHIOUNIVERSITY LIBRARY ACKNOWLEDGEMENT It was a grand experience to finish such voyage. But this pilgrimage could not have been possible without the indispensable and generous help and advice from my teachers and friends. At the outset I would like to say to my advisor Dr. Daniel A. Gulino, that I consider myself really fortunate and honored to work with you. In every conceivable way I feel a deep sense of gratitude to you for your help, advice, encouragement and inculcating a deep sense of commitment for this work. Next I wish to thank my wife Swati for her enthusiasm and encouragement for my work. I am also extremely thankful' ~o Dr. David Ingram for his generous help in RBS analysis and other useful advice . .I Last but not the least, let me mention the invaluable help and advice I did receive from my good friends Jim, Harvey and Tom while pursuing this work. PUBLICATIONS/PRESENTATIONS 1. S. Neogi and D. A. Gulino, "Chemical Vapor Deposition of Several Silicon-based Dielectric Films", Materials and Manufacturing Processes, Vol. 3, No.3, 433, 1991. 2. S. Neogi, D. C. Ingram and D. A. Gulino, "Improved Adhesion of Silicon Dioxide Thin Film to Polyimide Composites by Ion Implantation". HITEMP Review 1991 (Advanced High temperature Engine Materials Technology Program), NASA CP 10082, 1991, .t-\ 11-1 to A 11-10. 3. S. Neogi and D. A. Gulino, "High Temperature Oxidation Resistance of Si02 Coated Polyimide Composite", AIChE Journal, Vol. 38, No.9, 1379, 1992. 4. S. Neogi and D. A. Gulino, "Silicon Dioxide Thin Films Deposited by PECVD onto Polymeric Composites for High Temperature Oxidation Resistance", presented at the Third Topical Conference on Emerging Technologies in Materials, AIChE Annual Meeting, Los Angeles. CA, November 17-22, 1991. 5. S. Neogi and D. A. Gulino, "Die thylsilane as a Precursor for the Low Temperature Deposition of Si02 by LPCVD onto Polyimide Composites", submitted for presentation at the AIChE Annual Meeting, to be held in Miami, FL, November 1-6, 1992. TABLE OF CONTENTS LIST OF FIGURES iv LIST OF TABLES vii 1.0 INTRODUCTION.............................................................................................. 1 2.0 LITERATURE REVIEW 11 2.1 Silicon Dioxide Films 11 2.2 eVD and Pyrolytic Silicon Dioxide 11 2.3 Plasma Deposited Silicon Dioxide 17 2.4 Surface Modification by Ion Implantation 19 2.5 Modeling of Low Pressure CVD Reactors 23 2.6 Modeling of Plasma Enhanced CVD Reactors 25 2.7 Oxidative degradation of Polyimide Composite in Space 27 2.8 Thermo-oxidative Degradation of Polyimide Composites 28 3.0 RESEARCH PLAN 30 4.0 EXPERIMENTS 33 4.1 Experiment 1: Deposition of the TEOS-Si02 Thin Film onto Silicon Substrate by LPCVD Technique 33 4.1.1 Materials 33 4.1.2 Analysis of the Films 36 4.1.3 Experimental Procedure 44 4.2 Experiment 2: Deposition of the TEOS-Si02 Thin Film onto Polyimide Composite Substrate by PECVD Technique 46 11 4.2.1 Materials 46 4.2.2 Analysis of the Films 50 4.2.3 Experimental Procedure 54 4.3 Experiment 3: Deposition of the DES-SiOz Thin Film onto Silicon Substrate by LPCVD Technique 56 4.3.1 Materials 56 4.3.2 Analysis of the Film 59 4.3.3 Experimental Procedure 60 4.4 Experiment 4: Ion Implantation of the Thin Films 62 4.4.1 Ion Implanter 62 4.4.2 Experimental Procedure 62 5.0 RESULTS AND DISCUSSION 65 5.1 LPCVD Process 65 5.1.1 Film Thickness 66 5.1.2 Film Composition 68 5.2 PECVD Process 73 5.2.1 Film Composition 80 5.2.2 Refractive Index 80 5.2.3 Film Density 84 5.2.4 Etch Test 85 5.2.5 Adhesion of the Films 85 5.2.6 Stress of the Films 88 5.2.7 SEM Micrographs 88 III 5.3. LPCVD Process from DES 91 5.4 Ion Implantation 93 5.5 Mass Loss Experiments 94 6.0 CONCLUSIONS AND RECOMMENDAnONS 101 REFERENCES 104 APPENDICES 108 APPENDIX I........... 108 APPENDIX II 118 APPENDIX III 123 APPENDIX IV 136 IV LIST OF FIGURES Figure 1.1. Normalized energy distribution curve for an electron and the required energy for dissociation and ionization 3 Figure 1.2. Plasma-material interactions 4 Figure 1.3. Displacement of an atoms at the interface as a result of collision with incoming ions 9 Figure 1.4. Interaction of the incoming ions with the of the electronic structure of the film and substrate 10 Figure 4.1. Reaction chamber for TEOS-Si02 deposition by LPCVD 34 Figure 4.2. Schematic diagram of the LPCYD experimental system 45 Figure 4.3. Reaction chamber for TEOS-Si02 deposition by PECVD 47 Figure 4.4. Structure of PMR-15 51 Figure 4.5. Schematic diagram of the PECVD experimental system 55 Figure 4.6. Reaction chamber for DES-Si02 deposition by LPCyD 57 Figure 4.7. Schematic diagram of the LPCYD experimental system from DES 61 Figure 4.8. Schematic diagram of Ohio University Van de Graff accelerator 63 Figure 5.1. Profile of a typical Si02 Film 67 Figure 5.2. Arrhenious plot for Si02 deposition from 69 TEOS (LPCVD). v Figure 5.3. Plot of Deposition rate vs. pressure (LPCVD) 70 Figure 5.4a. Rutherford backscattering spectrum (RBS) of a typical Si02 (LPCVD) film 71 Figure 5.4b. Proton recoil detection (PRD) spectrum of a typical SiOz (LPCVD) film 72 Figure 5.5. FTIR spectrum of a typical SiO, (LPCVD) film 74 Figure 5.6. Arrhenius plot from Si02 deposition from TEOS (PECYD) 76 Figure 5.7. Plot of deposition of rate vs. rf power (PECVD) 77 Figure 5.8. Plot of deposition rate vs. pressure (PECVD) 79 Figure 5.9a. Rutherford backscattering structure of a typical SiOz (PECVD) Film 81 Figure 5.9b. Proton recoil detection structure of a typical Si02 (PECVD) film 8'= Figure 5.10. FTIR spectrum of a typical SiOz (PECVD) film S3 Figure 5.11. SEM micrograph of as received PMR-15 composite sample 89 Figure 5.12. SEM micrograph of Si02 coated (lOOOA) PNIR-15 composite sample 89 Figure 5.13. SEM micrograph of SrO, coated (800A) PMR-15 after an exposure at 390C for 300 hrs 90 Figure 5.14. SEM micrographs of Si02 coated (lOOOA) PMR-15 after an exposure at 390C for 300 hrs 90 Figure 5.15. FTIR spectrum of a typical Si02 (LPCYD) film from DES 92 Figure 5.16. Adhesion improvement by ion implantation 94 VI Figure 5.17. Effect of exposure to ambient atmosphere at elevated temperature on the mass of Si02 coated samples of PMR-15 composite samples 96 Figure 5.18. Percent mass loss at 300 hrs exposure to ambient atmosphere at 390C as function of Si02 film thickness 97 Figure 5.19. Effect of exposure to ambient atmosphere at elevated temperature on the mass of PMR-15 polyimide cornposue· samp1'"es twice coatedwiWIth S'O1 2 . 98 Figure 5.20. Effect of exposure to air plasma on the mass of PMR-15 polyimide composite samples 100 VII LIST OF TABLES Table 1.1. Plasma material interactions and their effects 5 Table 2.1. Comparisons of Si02 films from various organosilanes 16 Table 2.2. Data showing the cases where electronic energy loss causes enhancement of adhesion 21 Table 4.1. Typical beam parameters in RBS analysis 39 Table 4.2. Film thickness vs. color 42 Table 5.1. Deposition parameters of the LPCVD process 65 Table 5.2. Process conditions for TEOS-Si02 film deposition by the LPCVD process................................................................................. 66 Table 5.3. Deposition parameters of the PECVD process 73 Table 5.4. Process conditions for TEOS-Si02 film deposition by the PECVD process 78 Table 5.5. Refractive index vs. deposition temperature 84 Table 5.6. Film density vs. deposition temperature 85 Table 5.7. Peel adhesion ("Scotch tape") test results 86 Table 5.8. Scratch test conditions for a typical PECVD film 87 Table 5.9. Deposition parameters of the DES-Si02 film 91 Table 5.10. Process conditions for DES- Si02 film deposition by the LPCVD process 93 1 1.0 INTRODUCTION The technology of thin film deposition has advanced dramatically over the past twenty years. The advancement was driven primarily by the need for new products and devices in the electronics and optical industries. Thin films are also being applied as anticorrosive coatings for turbine blades, hard coatings for machine tools, and others. Now they are also being proposed to be applied for protection from oxidation of space station components parked in low earth orbit. Chemical vapor deposition (CYD) has emerged as a very important route for creating thin films on a variety of substrate materials. The synthesis is accomplished by a technique in which a gas or a mixture of gases interacts with the surface of a substrate at a relatively high temperature, resulting in the decomposition of some of the components of the gas and leading to the formation of a solid film or coating of a metal or compound on the substrate. The first application of CVD can probably be traced back to the prehistoric times, when the caveman used soot formed out of incomplete oxidation of firewood to paint and draw figures in the walls of the caves. Perhaps this is the first application of pyrolytic carbon.
Details
-
File Typepdf
-
Upload Time-
-
Content LanguagesEnglish
-
Upload UserAnonymous/Not logged-in
-
File Pages145 Page
-
File Size-