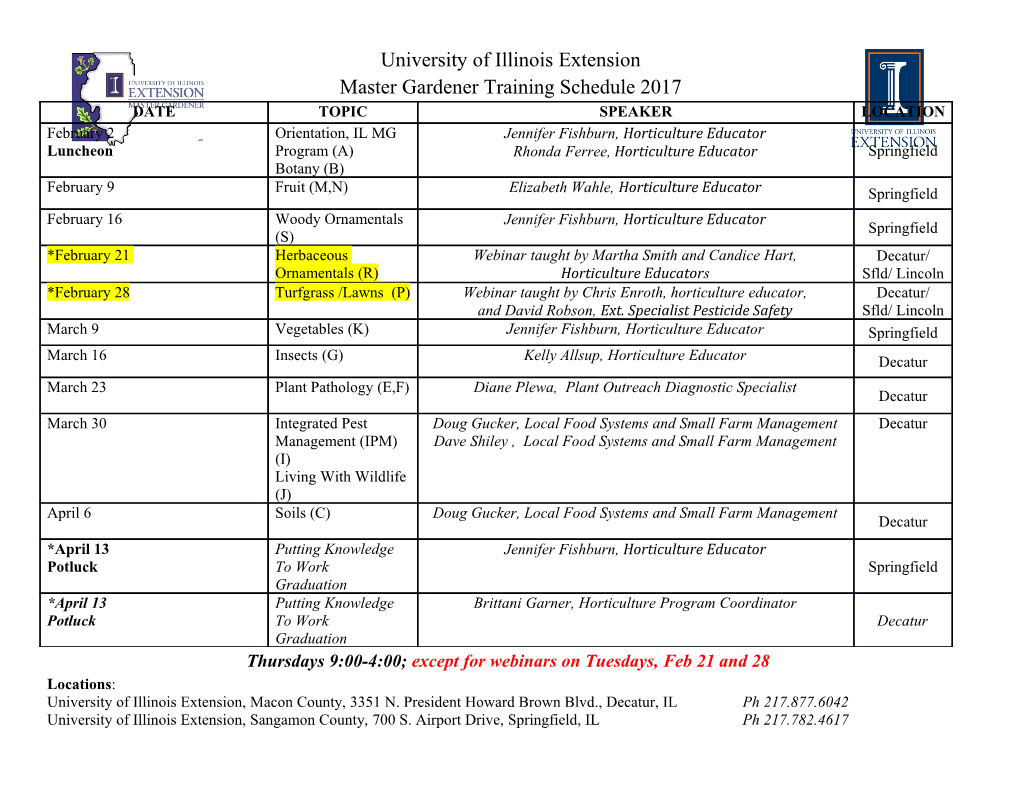
Original Article Proc IMechE Part K: J Multi-body Dynamics 2015, Vol. 229(3) 304–317 A frequency-based substructuring ! IMechE 2014 Reprints and permissions: approach to efficiently model sagepub.co.uk/journalsPermissions.nav DOI: 10.1177/1464419314562264 position-dependent dynamics in pik.sagepub.com machine tools Mohit Law and Steffen Ihlenfeldt Abstract Structural deformations of machine tool components that translate and/or rotate relative to each other to realize tool motion results in tool point dynamics varying along the tool path. These changing dynamics interact with the cutting process and the control loop of the drives to limit machine performance, making it necessary to virtually characterize these interactions such as to guide design decisions. To facilitate rapid evaluation of these varying dynamics, this paper describes a generalized frequency-based substructuring approach that combines the position-invariant component level receptances at the contacting interfaces between substructures to obtain the position-dependent tool point response. Receptances at the contacting interfaces are approximated by projecting them to a point to facilitate a multiple point receptance coupling formulation. Complete machine behavior is represented by just a few sets of receptances, making the model computationally more efficient than full-order finite element models and other dynamic substructuring methods. Position-dependent dynamic behavior for a representative three axis milling machine is simulated and numer- ically verified. Rapid investigations of the varying dynamics assist in virtually characterizing machine performance before eventual prototyping. Keywords Machine tool, dynamic substructuring, receptances, position-dependent dynamics, modular synthesis Date received: 21 August 2014; accepted: 10 November 2014 Introduction in which all major machine elements are modeled with Machine tools are essentially a collection of intercon- finite elements (FE). Machine FE models are often on nected deformable bodies that undergo large transla- the order of 1,000,000 degrees of freedom (DOF) or tional and/or rotational motion with respect to each more. This size makes position-dependent response other to realize tool motion. Structural deformations analysis that is based on adaptive/re-meshing strate- of the machine tool substructures undergoing large gies for every discrete position rather cumbersome; see motion results in tool point dynamics varying along Figure 1(a) for the sequence of modeling steps the tool path. The changing structural dynamics inter- involved. The adaptive/re-meshing strategies can act with the cutting process and the feed drive control. take up significant portion of total manpower and These interactions may limit the machine tool per- computational effort required for the design and ana- formance due to position-varying cutting stability of lysis of machine tools,1 limiting the analyses to one or the system and/or due to the position-varying con- two design concepts and at only a few discrete trol–structure interactions further limiting the pos- itioning speed and accuracy. To avoid these issues in Department of Machine Tools and Automation, Fraunhofer Institute for the development of high performance machines, it has Machine Tools and Forming Technology IWU, Chemnitz, Germany become increasingly necessary to virtually evaluate this position-varying performance to guide design Corresponding author: Mohit Law, Department of Machine Tools and Automation, Fraunhofer improvements before eventual physical prototyping. Institute for Machine Tools and Forming Technology IWU, Modeling the position-dependent dynamics often Reichenhainer Str. 88, 09126 Chemnitz, Germany. necessitates a flexible multibody modeling approach Email: [email protected] Downloaded from pik.sagepub.com at INDIAN INST TECH KANPUR on December 3, 2015 Law and Ihlenfeldt 305 Figure 1. Sequence of modeling steps required to obtain the position-dependent response: (a) traditional method; (b) dynamic substructuring approach, and (c) frequency-based substructuring approach. positions. For machine tool manufacturers to better into several smaller substructures for which the respond to the changing manufacturing paradigms, behavior is generally easier to determine.9,10 As there is need for more efficient models and methods such, these bottom-up substructuring approaches that facilitate rapid exploration of design alternatives facilitate modularity by synthesizing the position- while allowing for modularity and reconfigurability in invariant response of the main machine tool compo- the design process. To address this, several dedicated nents to obtain the position-dependent tool center research effort has been expended in recent years;2–8 point (TCP) response; see Figure 1(b) for the sequence with the dynamic substructuring approach fast emer- of modeling steps involved with this approach. ging as an efficient alternative to facilitate modularity To facilitate such dynamic substructuring, which is and evaluate position dependency.4–8 akin to a generic component mode synthesis,11 the Dynamic substructuring facilitates evaluation of substructures are independently reduced before syn- large and/or complex structures by dividing them thesis. Since the quality of the reduced model Downloaded from pik.sagepub.com at INDIAN INST TECH KANPUR on December 3, 2015 306 Proc IMechE Part K: J Multi-body Dynamics 229(3) influences the assembled response, several recent dynamics under varying base/part/contact character- investigations have focused on developing improved istics. This paper builds on these earlier formula- variants of reduced models that are better able to tions21,22 to model substructures that are approximate the full model behavior.4,7,12 simultaneously in contact over multiple interfaces Furthermore, synthesizing these reduced models at with changing compatibility conditions associated the contacting interfaces is nontrivial, especially so with tool motion. An overview of the modeling steps when the substructures have been modeled separately required to obtain the position-dependent TCP FRFs (modular design), resulting in different mesh reso- with the proposed approach is shown in Figure 1(c). lutions at the contacting interfaces. Assembly of Proposed approach is demonstrated by modeling models with nonconforming discretizations has been the position-dependent dynamic behavior for a repre- shown possible by approximating compatibility by sentative three axis milling machine. Since the sets of algebraic constraint equations,7,8 or by approx- approach is based on approximating point-to-point imating the displacement fields using shape function compatibility between substructures, receptances at definitions,13–15 or by interface reduction.16,17 the contacting interfaces are projected to a point to Though the bottom-up dynamic substructuring facilitate a multiple point RCSA formulation. This approach based on substructural synthesis of reduced treatment tolerates mesh-incompatibility issues, if models has proved effective, its dependence on the any, during synthesis—something that was nontrivial quality of the reduced models, numerical challenges with earlier methods. The proposed approach does with approximating displacement compatibility for not require model reduction of any kind and is nonconfirming meshes and the need to solve the shown to be computationally more efficient than reduced synthesized equations of motion for every full-order models and other dynamic substructuring different position, has largely limited its effective dif- methods. The framework is first used to evaluate posi- fusion in practice. To overcome these issues, this tion-invariant substructural characteristics that are paper describes an alternate frequency-based dynamic subsequently synthesized to obtain position-depen- substructuring approach to model position depend- dent behavior. This is followed by discussions on ency. As opposed to the ‘‘time-domain’’ dynamic sub- modeling considerations and the main conclusions. structuring methods used earlier4–8,12 that rely on solution to the reduced synthesized equations of Generalized frequency-based motion described by their spatial mass, damping, substructuring for machine tools and stiffness matrices, the frequency-based substruc- turing method describes each subsystem in terms of its A representative three axis milling machine is selected receptances, i.e. frequency response functions (FRFs) to allow for easy comparison of its position-depen- of the uncoupled systems.18 To obtain the synthesized dent behavior with other state-of-the-art results position-dependent TCP response, position-invariant reported in the literature.7 Since position dependency component level receptances are only required at the for the machine under consideration is primarily due coupling locations between the substructures as well to the motion of the spindle–spindle housing (sub- as at any point where the assembly response is to be structure I) in contact with and moving over a vertical predicted. column (substructure II), at first only these substruc- This frequency-based substructuring method, tures are modeled and combined—as shown schemat- otherwise also referred to as the receptance coupling ically in Figure 2. substructure analysis (RCSA) method been success- The spindle assembly that includes the tool, tool- fully used to obtain assembled TCP response by com- holder, and the spindle shaft are all modeled with bining response of arbitrary tools to the
Details
-
File Typepdf
-
Upload Time-
-
Content LanguagesEnglish
-
Upload UserAnonymous/Not logged-in
-
File Pages14 Page
-
File Size-