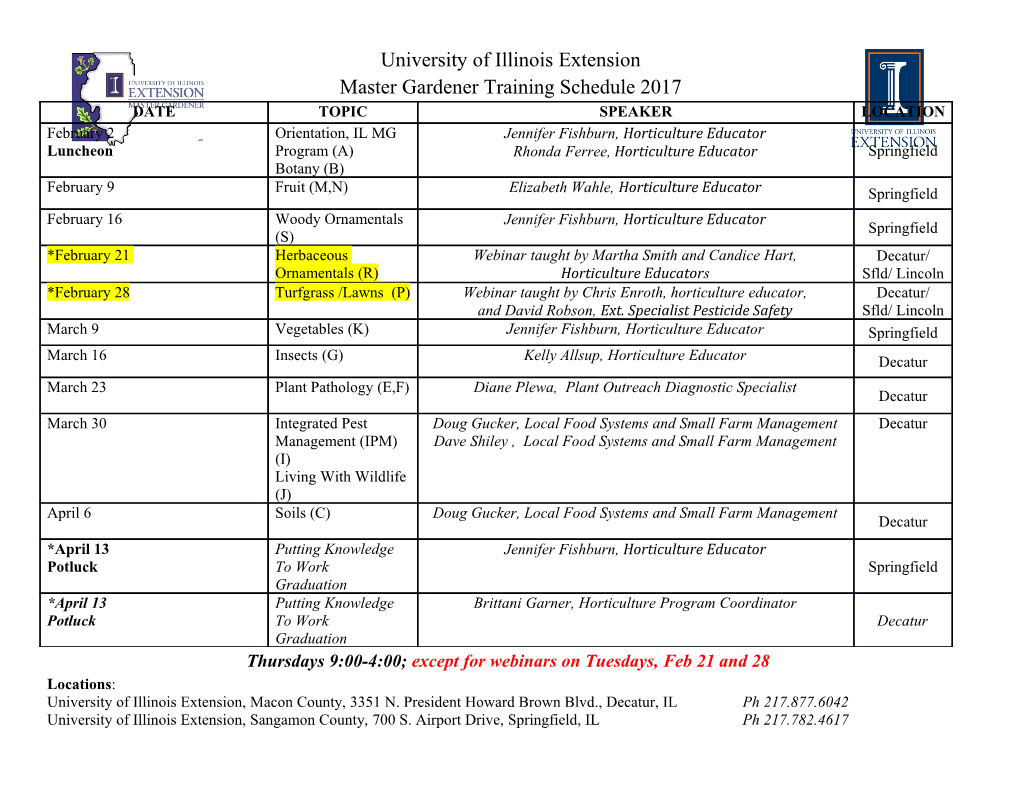
metals Article Mechanical Behavior and Microstructure Evolution of a Ti-15Mo/TiB Titanium–Matrix Composite during Hot Deformation Sergey Zherebtsov 1 , Maxim Ozerov 1,*, Margarita Klimova 1, Dmitry Moskovskikh 2 , Nikita Stepanov 1 and Gennady Salishchev 1 1 Laboratory of Bulk Nanostructured Materials, Belgorod State University, Belgorod 308015, Russia; [email protected] (S.Z.); [email protected] (M.K.); [email protected] (N.S.); [email protected] (G.S.) 2 Centre of Functional Nanoceramics, National University of Science and Technology, Moscow 119049, Russia; [email protected] * Correspondence: [email protected]; Tel.: +7-919-223-8528 Received: 26 September 2019; Accepted: 29 October 2019; Published: 31 October 2019 Abstract: A Ti-15Mo/TiB titanium–matrix composite (TMC) was produced by spark plasma sintering at 1400 ◦C under a load of 40 MPa for 15 min using a Ti-14.25(wt.)%Mo-5(wt.)%TiB2 powder mixture. Microstructure evolution and mechanical behavior of the composite were studied during uniaxial compression at room temperature and in a temperature range of 500–1000 ◦C. At room temperature, the composite showed a combination of high strength (the yield strength was ~1500 MPa) and good ductility (~22%). The microstructure evolution of the Ti-15Mo matrix was associated with the development of dynamic recovery at 500–700 ◦C and dynamic recrystallization at higher temperatures ( 800 C). The apparent activation energy of the plastic deformation was calculated and a processing ≥ ◦ map for the TMC was constructed using the obtained results. Keywords: titanium–matrix composite; deformation; microstructure evolution; mechanical properties 1. Introduction Due to a combination of high specific strength, excellent corrosion properties, and remarkable biocompatibility, titanium alloys are widely used in industry (e.g., shipbuilding, aircraft building, chemistry, food industry, etc.) and medicine (e.g., orthopedic and dental implants, surgery instruments) [1,2]. However, the absolute strength and hardness of titanium alloys are rather low and that limits their utilization for certain applications, especially in the case of most biocompatible pure titanium and some low-alloyed titanium alloys. A considerable increase in strength can be attained by complex alloying; however, the most accepted alloying elements (e.g., Al, V) can substantially deteriorate biocompatibility [3]. Searching for new titanium alloy compositions with satisfactory properties is still a challenging problem attracting a great deal of interest from materials scientists. Another promising way to attain high strength and hardness without loss of biocompatibility and corrosion properties is associated with the production of titanium-based composites [4,5]. Among a variety of reinforcements, TiB seems to be the most suitable option due to very similar properties (density, thermal expansion coefficient, good crystallographic matching) with the Ti matrix [5,6]. Titanium–matrix composites (TMCs) can be produced using traditional metallurgical methods through the addition of B into melted Ti [6]. However, powder metallurgy is more preferable in order to obtain a finer microstructure. In this case, TiB reinforcements form in the Ti matrix during the in-situ 3Ti + TiB2 = 2Ti + 2TiB reaction [6–8]. Due to high heating rate and high pressures, the spark plasma Metals 2019, 9, 1175; doi:10.3390/met9111175 www.mdpi.com/journal/metals MetalsMetals2019 2019, 9, 11759, x FOR PEER REVIEW 2 of2 11 of 10 methods through the addition of B into melted Ti [6]. However, powder metallurgy is more sinteringpreferable (SPS) in order process to canobtain be useda finer for microstructure powder consolidation. In this case, at relativelyTiB reinforcements low temperatures form in the and Tifor shortmatrix time during intervals, the in-situ thereby 3Ti preserving + TiB2 = 2Ti a very + 2TiB fine reaction microstructure [6–8]. Due in theto high specimen heating [8 ].rate Hard and fibers high of TiBpressures, increase thethe strengthspark plasma and hardness sintering of TMC,(SPS) howeverprocess can the ductilitybe used offor the powder composite consolidation can decrease at to nearlyrelatively zero [9low,10]. temperatures and for short time intervals, thereby preserving a very fine microstructureSome improvement in the specimen in both [8]. Hard ductility fibers of and TiB technologicalincrease the strength properties and hardness was attained of TMC, in thermomechanicallyhowever the ductility treated of the TMCscomposite [11– can17] duedecrease to the to shorteningnearly zero and[9,10]. redistribution of TiB whiskers, along withSome the improvement development in of dynamicboth ductility recrystallization and technological in the titanium properties matrix. was Another attained promising in waythermomechanically to improve ductility treated of the TMCs composite [11–17] can due be associatedto the shortening with an and increase redistribution in plasticity of TiB of thewhiskers, titanium matrixalong by with adding the development a β-stabilizing of dynamic element. recrystallization In this case, a hard-to-deform in the titanium hexagonalmatrix. Another close-packed promising (hcp) latticeway shouldto improve become ductility more of ductile the composite due to thecan greaterbe associated number with of slipan increase systems in in plasticity a body-centered of the titanium matrix by adding a β-stabilizing element. In this case, a hard-to-deform hexagonal close- cubic (bcc) lattice [1]. Meanwhile, there is a lack of information on both the mechanical properties packed (hcp) lattice should become more ductile due to the greater number of slip systems in a of β-Ti-based TMCs and an influence of thermomechanical treatment on structure and properties of body-centered cubic (bcc) lattice [1]. Meanwhile, there is a lack of information on both the these materials. mechanical properties of β-Ti-based TMCs and an influence of thermomechanical treatment on In this work a bcc Ti-15 (wt.%)Mo matrix (which is widely used for bio-medical applications) was structure and properties of these materials. reinforcedIn this by work 8.5 vol.% a bcc of Ti-15 TiB. (wt.%)Mo This amount matrix of TiB(which was is selected widely used using for literature bio-medical data applications) for hcp Ti/TiB compositeswas reinforced to attain by 8.5 a combinationvol.% of TiB. ofThis high amount strength of TiB and was satisfactory selected using ductility literature [6]. Itdata was for selected hcp toTi/TiB investigate composites the mechanical to attain a properties combination of theof high TBC atstrength room temperature,and satisfactory to studyductility the [6]. eff ectIt was of hot deformation at 500–1000 C and strain rates in the interval 5 10 4–10 2 s 1 on microstructure selected to investigate the◦ mechanical properties of the TBC at room× temperature,− − − to study the effect evolutionof hot deformation and mechanical at 500–1000 behavior. °C and The strain obtained rates results in the will interval be used 5 × for10−4 the–10− development2 s−1 on microstructure of a proper thermomechanicalevolution and mechanical treatment behavior. of the TMC. The obtained results will be used for the development of a proper thermomechanical treatment of the TMC. 2. Materials and Procedure 2. Materials and Procedure Powders of Ti (99.1% purity), Mo (99.95% purity), and TiB2 (99.9% purity) were used for the sinteringPowders of the Ti-15Moof Ti (99.1%/TiB compositespurity), Mo with (99.95% the bcc purity), Ti matrix. and TiB The2 average(99.9% purity) sizes of were the Ti, used Mo, for and the TiB 2 particlessintering were of the 25, Ti-15Mo/TiB 3, and 4 µm, compos respectivelyites with (Figure the 1bcc). ATi mixture matrix. ofThe the average powders sizes containing of the Ti, 80.75Mo, and wt.% Ti,TiB 14.252 particles wt.% of were Mo, 25, and 3, 5 and wt.% 4 ofμm, TiB respectively2 (to obtain (Figure a Ti-15wt.% 1). A mixture Mo alloy of with the powders 8.5 vol.% containing of TiB) were produced80.75 wt.% using Ti, a14.25 Retsch wt.% RS200 of Mo, vibrating and 5 wt.% cup of mill TiB (RETSCH,2 (to obtain Haan, a Ti-15wt.% Germany) Mo inalloy ethanol with 8.5 ata vol.% milling rotationof TiB) speed were ofproduced 700 rpm. using The mixinga Retsch duration RS200 wasvibrating 1 h. cup mill (RETSCH, Haan, Germany) in ethanol at a milling rotation speed of 700 rpm. The mixing duration was 1 h. (a) (b) (c) Figure 1. SEM images of (a) Ti, (b) Mo, and (c) TiB2 powders. Figure 1. SEM images of (a) Ti, (b) Mo, and (c) TiB2 powders. CylindricalCylindrical Ti-15Mo Ti-15Mo/TiB/TiB TMC TMC specimens specimens measured measured 15 15 mm mm in in height height and and 19 19 mm mm in in diameter diameter and wereand produced were produced using theusing SPS the process SPS process under vacuumunder vacuum on a Thermal on a Thermal Technology Technology SPS 10-3 SPS machine 10-3 machine (Thermal Technology, LLC, Santa Rosa, CA, USA) at 1400 °C and 40 MPa for 15 min. Then, (Thermal Technology, LLC, Santa Rosa, CA, USA) at 1400 ◦C and 40 MPa for 15 min. Then, the sintered the sintered samples of the composite were homogenized at 1200 °C for 24 h and cooled in air. To samples of the composite were homogenized at 1200 ◦C for 24 h and cooled in air. To prevent oxidation duringprevent the oxidation homogenization during the annealing, homogenization the specimens annealing, were the sealed specimens in vacuumed were sealed quartz in vacuumed tubes filled quartz tubes filled with a titanium getter. The homogenized condition of the TMC is referred to as with a titanium getter. The homogenized condition of the TMC is referred to as the initial one hereafter. the initial one hereafter. Specimens 7 10 mm in high were cut from the homogenized composite using a Sodick AQ300L ; × electro-discharge machine (Sodick Inc., Schaumburg, IL, USA). Then, the specimens were isothermally strained by compression in air at 20, 500, 600, 700, 800, 900, or 1000 ◦C on an Instron mechanical Metals 2019, 9, x FOR PEER REVIEW 3 of 11 Specimens ∅7 × 10 mm in high were cut from the homogenized composite using a Sodick AQ300L electro-discharge machine (Sodick Inc., Schaumburg, IL, USA).
Details
-
File Typepdf
-
Upload Time-
-
Content LanguagesEnglish
-
Upload UserAnonymous/Not logged-in
-
File Pages10 Page
-
File Size-