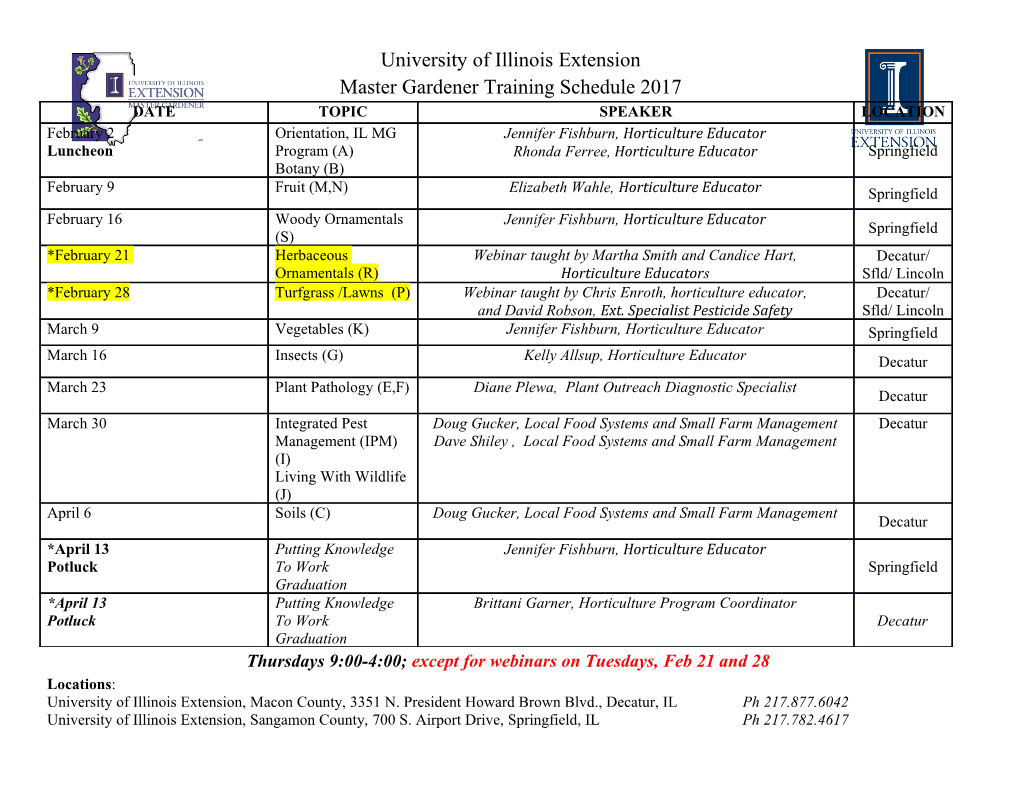
technical Influences of the Residual Stress Condition on the Load-Carrying Capacity of Case-Hardened Gears C. Güntner, T. Tobie and K. Stahl Introduction stresses can also be used to repair grind- Characterization of Residual Highly loaded gears are usually case- ing burn or to avoid facing edge tooth Stresses hardened to fulfill the high demands on flank fractures. Residual stresses are stresses which the load-carrying capacity. Several fac- All in all, the investigations show that occur in a component that is not loaded tors, such as material, heat treatment, or shot peening can significantly increase by any force or torque. There are ten- macro and micro geometry, can influence the load-carrying capacity of case-hard- sile and compressive residual stresses. the load-carrying capacity. Furthermore, ened gears. Furthermore, correlations Both kinds of residual stresses are bal- the residual stress condition also signifi- between the residual stress state and anced within a component. Compressive cantly influences load-carrying capacity. the load-carrying capacity limits were residual stresses in the surface layer typ- The residual stress state results from heat determined. This paper will provide an ically have a positive influence on the treatment and can be further modified by overview of the main results of different load-carrying capacity, whereas tensile manufacturing processes post heat treat- investigations and discuss influences of residual stresses in the surface layer can ment, e.g. — grinding or shot peening. the residual stress condition on different significantly reduce load-carrying capac- A variety of investigations was per- failure modes of case-hardened gears. ity. The residual stress state is influenced formed in several research projects con- Case-hardening is a typical heat treat- by the manufacturing process, which cerning the influence of residual stresses ment process used to achieve an adequate includes soft-machining, heat treatment, on the load-carrying capacity limits of load-carrying capacity of highly loaded and finishing. The “case-hardening” heat gears. The investigations were focused components, such as gears. The chal- treatment process usually leads to com- on the tooth root bending strength as lenge is always either to minimize the size pressive residual stresses in the surface well as the flank load-carrying capacity. of the component to transfer the same layer and tensile residual stresses in the The gears were analyzed in un-peened, torque or force, or to be able to transfer core. The residual stresses take only small mechanical-cleaned, and shot peened a higher torque or force using the same compressive stress values in a range of condition. The investigations included size of the component. Several factors about −200 up to −400 N/mm2. During different materials, e.g. — 16MnCr5 or influence the load-carrying capacity of quenching the component does not cool 18CrNiMo7-6 — and different gear sizes. gears, such as material, heat treatment, or down uniformly, so a volume difference Compressive residual stresses gener- macro and micro geometry. Furthermore, occurs whereby residual stresses arise; ated by shot peening, for example, result the residual stress condition has a signifi- furthermore, austenite transforms into in an increased tooth root bending cant influence on load-carrying capacity; martensite. Both microstructures have strength. The tooth root bending strength the residual stress state is changed during different yet specific volumes that result of shot peened gears can be increased the manufacturing process by the heat in additional residual stresses. All in all, by more than 50% compared to gears in treatment and a possible downstream the residual stress state results from a the un-peened condition. Per mechan- shot peening. combination of quenching and volume ical laws, the increase of the load-car- Within the scope of this paper will be change. rying capacity is limited. In the case of shown the influence of the residual stress Usually the gears are subjected to a highly loaded shot peened gears, other state — especially influenced by a peening shot blasting or peening process after failure mechanisms may arise, such as process — on the load-carrying capac- case-hardening. There is therefore a dis- subsurface-initiated cracks. Shot peening ity of gears. The main focus is set on the tinction between mechanical cleaning can also significantly increase the flank tooth root bending strength. Besides this, and shot peening. In both cases the gen- load-carrying capacity. Due to a shot influences on the tooth flank character- eration of the residual stresses is based on peening process, the surface of the gears istics will also be discussed. This paper the model representation of Wohlfahrt is influenced. As a consequence, other will summarize the main results of differ- (Ref. 26). For case-hardened steels (e.g., failure mechanisms can occur, such as ent, previously published investigations. 16MnCr5 or 18CrNiMo7-6), the residual micropitting. Furthermore, shot peening Therefore, the different projects are com- stresses are generated by the elastic-plas- and the resulting compressive residual pared by showing the main results. tic deformation of the surface. Due to the Printed with permission of the copyright holder, the American Gear Manufacturers Association, 1001 N. Fairfax Street, Fifth Floor, Alexandria, VA 22314-1587. Statements presented in this paper are those of the author(s) and may not represent the position or opinion of the American Gear Manufacturers Association. [www.geartechnology.com] 60 GEAR TECHNOLOGY | August 2018 local stresses that exceed the yield point case-hardened gears of material qual- component. Therefore, the steel balls are of the material, compressive residual ity MQ are purposefully achievable with accelerated by jet nozzles. The size and stresses arise. Furthermore, as mentioned mechanical cleaning. hardness of the steel balls can be varied above, the retained austenite transforms as well as the ejection speed (Fig. 2) and into martensite during the shot peening Shot Peening the duration of the process. Before the process. Due to different specific vol- Shot peening differs from mechanical component is shot peened, a measure- umes of the microstructures, compressive cleaning. As opposed to blast cleaning, ment of the intensity is done; on the basis residual stresses arise (Ref. 22). several parameters — such as blasting of this measurement the peening time is During the “grinding” finishing pro- material, hardness of the blasting mate- determined. With these parameters the cess, the residual stress state also changes rial, size of the material, degree of cov- depth of the maximum and the maxi- in that the surface layer is mechanically erage, and intensity — are defined and mum value of the residual stresses can be and thermally influenced (Ref. 21). Due monitored. According to ISO 6336 varied within some limits. Furthermore, to the mechanical influence of the grind- (Ref. 4), “The recommended minimum the steel balls underlie a continuous pro- ing wheel, compressive or tensile resid- control should be based on SAE AMS cessing in order to maintain a constant ual stresses may be generated. Excessive 2430 (Ref. 16), SAE AMS 2432 (Ref. 17) result of the shot peening process. Due to heat exposure during the grinding process or SAE J 2241 (Ref. 18).” The blast mate- the comprehensive monitoring, the pro- results in tensile residual stresses. The rial in this case is steel balls, with the aim cess can achieve reproducible results. To residual stress condition post grinding of a specific increase of the compressive achieve the expected results of the shot is a result of a superimposition of both residual stresses. The steel balls have to peening process, the component has to be influences. The process parameters have a be round and the hardness of them has to cleaned in advance. significant influence on the residual stress be at least identical to the hardness of the In Figure 3 typical residual stress values state. In the surface layer, tensile as well as compressive residual stresses may arise. Mechanical Cleaning The aim of the mechanical cleaning pro- cess is to remove the scale layer and clean the component after heat treatment. The process is mostly done by an impel- ler; a schematic presentation is shown (Fig. 1). The blasting material is mostly cut wire or glass beads. The process is not defined; only the process time and the speed of the impeller are controlled and monitored (e.g., 5 minutes-per-side). By this process, compressive residual Figure 2 Schematic presentation of the shot peening by jet nozzle (Ref. 10). stresses are induced that have a posi- tive effect on the load-carrying capacity. Furthermore, according to ISO 6336-5 (Ref. 4), the bending stress numbers for Figure 1 Schematic presentation of the mechanical cleaning Figure 3 Comparison of the residual stresses in the un-peened, mechanical- by an impeller (Ref. 10). cleaned, and shot peened condition (measurement results, exemplary presentation) (Ref. 22). August 2018 | GEAR TECHNOLOGY 61 technical in the surface layer are plotted for gears in the residual stress states of different shot peening process often leads to a higher the un-peened, mechanical-cleaned, and peening processes are compared to the surface roughness compared to the shot peened condition. The influence of un-peened condition. Here, a shot peen- grinded condition (Refs. 10 and 6). In increased residual stresses due to mechan- ing process with big steel balls (diameter Table 1 the surface roughness of a ical cleaning or shot peening is limited to of 0.8 mm) is combined with a shot peen- grinded tooth surface is compared to a only a depth of about 0.1-0.15 mm. The ing process with small steel balls (diam- grinded surface with an additional shot highest compressive residual stresses are eter 0.1 mm), which is called WHSP. By peening (after grinding). Due to the shot achievable with shot peening.
Details
-
File Typepdf
-
Upload Time-
-
Content LanguagesEnglish
-
Upload UserAnonymous/Not logged-in
-
File Pages10 Page
-
File Size-