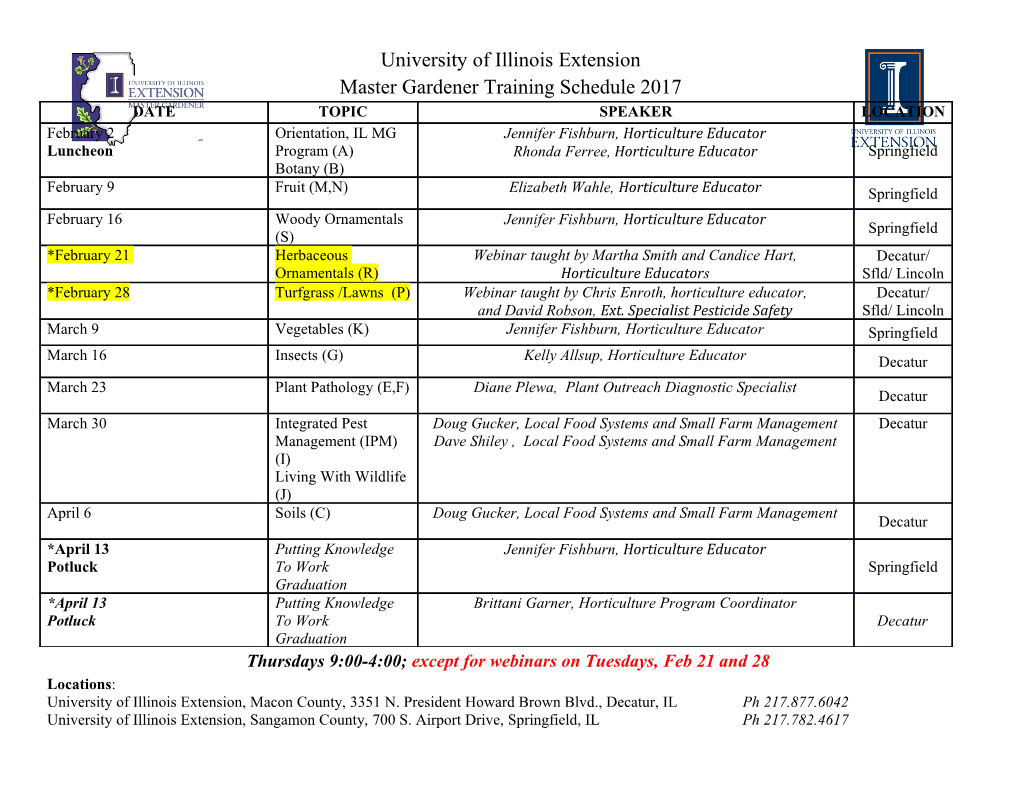
Druckfreigabe/approval for printing Without corrections/ ` ohne Korrekturen j After corrections/ 277 nach Ausfçhrung ` 1 der Korrekturen 2 3 Date/Datum: ................................... 4 Signature/Zeichen: ............................ 5 6 9 7 Biodegradable Polymer-based Nanocomposites: 8 9 Nanostructure Control and Nanocomposite Foaming 10 with the Aim of Producing Nano-cellular Plastics 11 Masami Okamoto 12 13 14 9.1 15 Introduction 16 17 The increased importance of renewable resources for raw materials and recyclability 18 or biodegradability of the material at the end of its useful life is demanding 19 a shift from petroleum-based synthetics to agro-based materials in industrial 20 applications. Increased social awareness of environmental problems posed by 21 the non-degradable, non-recyclable content of their products is forcing manufac- 22 turers to enhance the biodegradable content, which in turn favors a switch to 23 biomaterials [1]. 24 Hence, with this background, there is an urgent need to develop renewable source- 25 based environmentally benign polymeric materials (biopolymers [2]). Such materials 26 would not involve the use of toxic or noxious components in their manufacture, and 27 could allow composting to naturally occurring degradation products. 28 In todays commercial environment, biopolymers have proven to be relatively 29 expensive and available only in small quantities. This has led to limitations on their 30 application to date. However, there are signs that this is changing, with increasing 31 environmental awareness and more stringent legislation regarding recyclability and 32 restrictions on waste disposal. Cargill Dow has a polylactide (PLA) in production 33 (with the Trade Name Natureworks). Metabolix has been working on polyhydroxy- 34 alkanoate (PHA) (Trade Name Biopol) [2]. 35 Thus, the increasing application of the various intrinsic properties of bio- 36 polymers, coupled with the knowledge of how such properties can be improved 37 to achieve compatibility with thermoplastics processing, manufacturing, and en- 38 d-use requirements, has fueled technological and commercial interest in 39 biopolymers. 40 Of particular interest are the recently developed nanocomposites consisting of a 41 polymer and layered silicate because they often exhibit remarkably improved 42 mechanical and other properties [3] when compared with pure polymer or conven- 43 tional composites (both micro- and macro-composites). A primary progress in 44 45 Bio-inorganic Hybrid Nanomaterials. Edited by E. Ruiz-Hitzky, K. Ariga, Y. M. Lvov Copyright Ó 2007 WILEY-VCH Verlag GmbH & Co. KGaA, Weinheim ISBN: 978-3-527-31718-9 278j 9 Biodegradable Polymer-based Nanocomposites 1 polymer/layered filler nanocomposites (PLFNCs), a Nylon 6/layered silicate hybrid 2 [4] reported by Toyota Central Research & Development Co. Inc. (TCRD), was 3 successfully prepared by in situ polymerization of e-caprolactam in a dispersion of 4 montomorrillonite (MMT). The silicate can be dispersed in liquid monomer or a 5 solution of monomer. It has also been possible to melt-mix polymers with layered 6 silicates, thus avoiding the use of organic solvents. The latter method permits the use 7 of conventional processing techniques such as injection molding and extrusion. The 8 extensive literature on nanocomposite research is covered in recent reviews [5–7]. 9 The study of nanocomposites has gained greater momentum. This new class of 10 materials is now being introduced in structural applications, such as a gas barrier 11 film, a flame retardant product, and other load-bearing applications [8]. 12 This chapter is intended to highlight the biodegradable polymer-based nanocom- 13 posites with the primary focus on nanostructure control and the foam processing 14 operation with the aim of producing nano-cellular plastics. Development of nano- 15 composite foams is one of the latest evolutionary technologies of polymeric foam 16 through a pioneering effort by Okamoto and his colleagues [9,10]. 17 18 19 9.2 20 Nano-structure Development 21 22 9.2.1 23 Melt Intercalation 24 25 Since the possibility of direct melt intercalation was first demonstrated [11], melt 26 intercalation has become a method of preparation of the intercalated polymer/ 27 layered silicate nanocomposites (PLSNCs). This process involves annealing, stati- 28 cally or under shear, a mixture of the polymer and organically modified layered 29 fillers (OMLFs) above the softening point of the polymer. During annealing, the 30 polymer chains diffuse from the bulk polymer melt into the nano-galleries between 31 the layered fillers. 32 In order to understand the thermodynamic issues associated with the nanocom- 33 posite formation, Vaia et al. have applied the mean-field statistical lattice model and 34 found that conclusions based on the mean field theory agreed nicely with the 35 experimental results [12,13]. The entropy loss associated with confinement of a 36 polymer melt is not prohibited to nanocomposite formation because an entropy gain 37 associated with the layer separation balances the entropy loss of polymer intercala- 38 tion, resulting in a net entropy change near to zero. Thus, from the theoretical model, 39 the outcome of nanocomposite formation via polymer melt intercalation depends on 40 energetic factors, which may be determined from the surface energies of the polymer 41 and OMLF. 42 Nevertheless, we have often faced the problem that the nanocomposite shows fine 43 and homogeneous distribution of the nanoparticles in the polymer matrix (e.g., poly 44 (L-lactide)) without a clear peak shift of the mean interlayer spacing of the (001) plane, 45 as revealed by wide-angle X-ray diffraction (WAXD) analysis [14]. Furthermore we 9.2 Nano-structure Development j279 1 sometimes encounter a decrease in the interlayer spacing compared with that of 2 pristine OMLF, despite very fine dispersion of the silicate particles. For this reason, 3 information on the structure of the surfactant (intercalant)–polymer interface is 4 necessary to understand the intercalation kinetics that can predict the final nano- 5 composite morphology and overall materials properties. 6 7 9.2.2 8 Interlayer Structure of OMLFs and Intercalation 9 10 9.2.2.1 Nano-fillers 11 In characterizing layered silicate, including layered titanate (HTO), the surface 12 charge density is particularly important because it determines the interlayer structure 13 of the intercalants as well as the cation exchange capacity (CEC). Lagaly proposed a 14 method of calculation consisting of total elemental analysis and the dimensions of 15 the unit cell [15]: À 16 Surface charge : e =nm2 ¼ x=ab ð1Þ 17 18 where x is the layer charge (1.07 for HTO, 0.66 for synthetic fluorine hectrite (syn-FH) 19 and 0.33 for MMT. a and b are cell parameters of HTO (a ¼ 3.782 Å, b ¼ 2.978 Å [16]), 20 syn-FH (a ¼ 5.24 Å, b ¼ 9.08 Å [17]), and MMT (a ¼ 5.18 Å, b ¼ 9.00 Å [18]). For syn- + 21 FH, however, about 30 % of the interlayer Na ions are not replaced quantitatively by 22 intercalants since they do not take part in ion-exchange reactions [17]. For HTO, only + + 23 27 % of the interlayer H (H3O ) is active for ion-exchange reactions [14]. Thus the 24 incomplete replacement of the interlayer ions is ascribed to the intrinsic chemical 25 reactivity. The characteristic parameters of two nano-fillers are also summarized in À 2 26 Table 9.1 [18]. HTO has a high surface charge density of 1.26 e /nm compared with À 2 À 2 27 those of syn-FH (0.971 e /nm ) and MMT (0.780 e /nm ). From these results, we 28 can estimate the average distance between exchange sites as 0.888 nm for HTO, 29 1.014 nm for syn-FH and 1.188 nm for MMT. This estimation assumes that the 30 31 Tab. 9.1 Characteristic parameters of nano-fillers. 32 33 Parameters HTO syn-FH MMT 34 Á 35 chemical H1.07Ti1.73O3.95 0.5H2ONa0.66Mg2.6Si4O10(F)2 Na0.33(Al1.67Mg0.33) 36 formula Si4O10(OH)2 – – – 37 particle size/nm 100 200 100 200 100 200 2 38 BET area/m /g 2400 800 700 CEC/meq/100 g 200 (660) 120 (170) 90 (90) 39 À e /charge/nm2 1.26 0.971 0.708 40 density/g/cm3 2.40 2.50 2.50 41 20 refractive index (nD ) 2.3 1.55 1.55 42 pH 4–69–11 7.5–10 43 a Methylene blue adsorption method. The values in parentheses are calculated from the chemical 44 formulae of the nano-fillers. 45 Source: Reprinted with permission from [18] Ó 2006, Wiley-VCH. 280j 9 Biodegradable Polymer-based Nanocomposites 1 cations are evenly distributed in a cubic array over the silicate surface and that half of 2 the cations are located on the one side of the platelet and the other half reside on the 3 other side. 4 5 9.2.2.2 Molecular Dimensions and Interlayer Structure 6 The calculated models of the intercalant structures are presented in Figure 9.1. For + 7 octadecylammonium (C18H3N ), the molecular length, thickness and width are 8 2.466, 0.301 and 0.301 nm, respectively. Since the length of all alkyl units is more than 9 2 nm, these spacings (distance between exchange sites) of 0.888–1.188 nm do not 10 allow parallel layer arrangement like flat-lying chains [15] in each gallery space of the 11 nano-fillers. All the intercalants are oriented with some inclination to the host layer in 12 the interlayer space to form an interdigitated layer. This is suggested by the paraffin- 13 type layer structure proposed by Lagaly, especially in the case of clay minerals with 14 high surface charge [15]. 15 WAXD patterns for three OMLF powders are presented in Figure 9.2.
Details
-
File Typepdf
-
Upload Time-
-
Content LanguagesEnglish
-
Upload UserAnonymous/Not logged-in
-
File Pages43 Page
-
File Size-