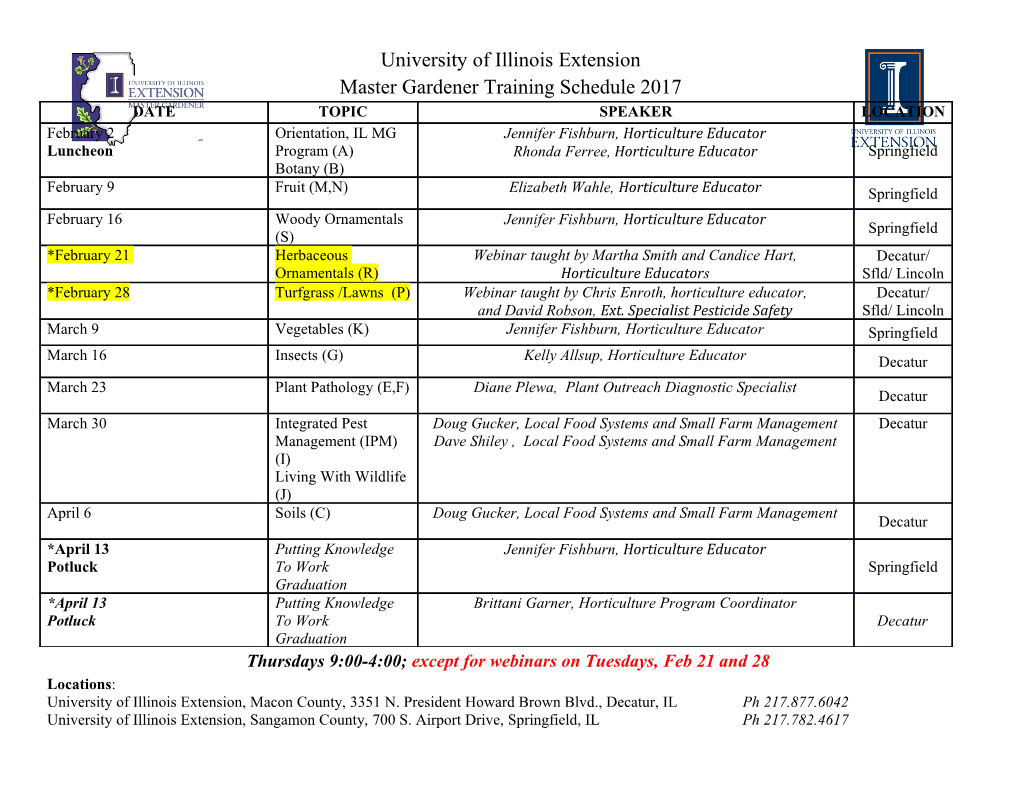
University of Pennsylvania ScholarlyCommons Department of Chemical & Biomolecular Senior Design Reports (CBE) Engineering 4-2014 Production of Acrylic Acid from Ethylene Patricia Campos University of Pennsylvania Minsik Jun University of Pennsylvania Rahul Puranmalka University of Pennsylvania Follow this and additional works at: https://repository.upenn.edu/cbe_sdr Part of the Biochemical and Biomolecular Engineering Commons Campos, Patricia; Jun, Minsik; and Puranmalka, Rahul, "Production of Acrylic Acid from Ethylene" (2014). Senior Design Reports (CBE). 61. https://repository.upenn.edu/cbe_sdr/61 This paper is posted at ScholarlyCommons. https://repository.upenn.edu/cbe_sdr/61 For more information, please contact [email protected]. Production of Acrylic Acid from Ethylene Abstract A preliminary process design and economic analysis into the possible threat of ethylene- based acrylic acid manufacture is presented. Pipeline ethylene is fed at 14,000 ft2/hr to the first block of this process. The epoxidation of ethylene to ethylene oxide takes advantage of microchannel technology and eliminates the need for inerts, thus decreasing equipment sizing downstream while achieving a yield of 80% overall. The resulting ethylene oxide stream is carbonylated in a liquid phase, homogeneous reaction. The β-propiolactone is then rearranged in phosphoric acid to produce 37,000 lbs of acrylic acid per hour for a yearly rate of just over 300M pounds at greater than 99.4% mass purity. The product contains 300 ppm mono-methyl ether hydroquinone to prevent the product from polymerizing and entering the explosive limits. Using an after tax discount rate of 15%, the NPV is -$50M in December, 2014, 35 years from construction start date. The IRR is 13.84% and confirms the notion that a microchannel costs need to be further evaluated to determine the profitability. In the project, the EO plant accounts for 90% of the equipment cost and 50% of the total invested capital cost. A cost plus analysis of ethylene oxide costs was determined and IRR data was determined based on the variability of ethylene prices and the cost-plus price of producing ethylene oxide. It was determined that the project has an IRR of 42.17% with a NPV of $288M when an after tax cash flow analysis was conducted with an after tax discount rate of 15%. It was concluded that the feasibility of this project depends heavily on the cost of the microchannel reactors, and at this stage, the costs of the microchannel do not outweigh the advantages offered by the new reactor. It is recommended that further analysis be done to more accurately cost the microchannel reactor and to investigate the benefits of increasing the per pass conversion of ethylene. Further analysis on the reactor designs and rates for the carbonylation step and rearrangement step could help hone in the reality of an ethylene based acrylic acid process. Most importantly, further economics should be conducted to see if the best-case scenario assumptions used in this paper are too ideal. The new economics should be compared to the sensitivity analysis conducted in this study. Disciplines Biochemical and Biomolecular Engineering | Chemical Engineering | Engineering This working paper is available at ScholarlyCommons: https://repository.upenn.edu/cbe_sdr/61 Mr. Leonard Fabiano University of Pennsylvania School of Engineering & Applied Science 220 S 33rd Street Philadelphia, PA 19104 Dear Mr. Fabiano, Enclosed is our design for an ethylene based acrylic acid production plant in fulfillment of the design problem proposed by Mr. John Wismer. In this report, we investigate the potential for ethylene based acrylic acid to pose a threat to the propylene based business due to the natural gas boom in the US. The investigation involves designing the epoxidation of ethylene using microchannel technology, carbonylation of ethylene oxide to β-propiolactone using a homogeneous, cobalt catalyst, and acid catalyzed rearrangement of β-propiolactone. The report focuses on plant design and an economic analysis to determine the threat posed in the US by recent price changes in the cost of ethylene due to shale gas. The plant is designed to operate 24 hours a day for 350 days a year, with a yearly production rate of 300M lbs of acrylic acid. Economics were calculated based on the entire plant and based on ethylene-oxide cost plus analysis. For the entire plant, total permanent investment would entail $ $560M with profitability depending closely on the total permanent investment. Using present ICIS commodity chemical pricing, the Project has an IRR of 13.48% with a NPV of -$50M after 35 years. Using cost plus analysis, the non-EO section of the plant has a total capital investment of $120M with an IRR of 42.17% and an NPV of $288M over 35 years. Details regarding the process equipment and plant profitability are enclosed, along with safety requirements. Based on this analysis, further design work must be taken verify the assumptions that have been made for this process. Determining the price and effectiveness of the microchannel reactor is key for evaluating the benefits of using a process that is void of inerts and diluents. It is crucial that pilot plant work should be undertaken to understand the true kinetics behind the carbonylation of β-propiolactone since the kinetics determine the necessary resonance time, the reactor size, per pass conversion, and overall efficiency. Pilot plant testing should be undertaken to determine the ratio of β-propiolactone to phosphoric acid needed for rearrangement on a larger scale. Reconciling this information with the data in this project would paint a clearer picture to the profitability of ethylene-based acrylic acid using cost-plus analysis. At this stage, the group concludes the idea that ethylene based acrylic acid could be a threat to propylene based manufacturers cannot be disqualified and should be further investigated. Sincerely, Rahul Puranmalka Minsk Jun Patricia Campos Production of Acrylic Acid from Ethylene Campos, Jun, Puranmalka Table of Contents Section 1 – Abstract ........................................................................................................................ 6 Section 2 – Introduction .................................................................................................................. 8 2.1 Product .................................................................................................................................. 9 2.2 Current Methods of Production ........................................................................................... 10 2.3 Proposed Production Method .............................................................................................. 10 2.3.1 Step 1: Oxidation of Ethylene ...................................................................................... 11 2.3.2 Step 2: Carbonylation of Ethylene Oxide ..................................................................... 13 2.3.3 Step 3: Acid-Catalyzed Rearrangement of β-Propiolactone ........................................ 15 2.4 Customer Requirements ...................................................................................................... 16 2.5 Commercial Applications .................................................................................................... 16 2.6 Project Charter..................................................................................................................... 17 2.7 Innovation Map ................................................................................................................... 18 Section 3 – Process Description .................................................................................................... 19 3.1 Overview ............................................................................................................................. 20 3.2 Block 100: Epoxidation of Ethylene to Ethylene Oxide ..................................................... 21 3.2.1 Microchannel Reactor ................................................................................................... 22 3.2.2 Ethylene Oxide Scrubbing ............................................................................................ 22 3.2.3 Ethylene Oxide Purification ......................................................................................... 23 3.2.4 CO2 Separation ............................................................................................................. 23 3.3 Block 200: Carbonylation of Ethylene Oxide to β-Propiolactone ...................................... 25 3.4 Block 300: Acid Catalyzed Rearrangement of β-Propiolactone to Acrylic Acid ............... 27 3.4.1 Reactor and Purification of Acrylic Acid ..................................................................... 28 3.4.2 Acrylic Acid Storage and Handling .............................................................................. 28 1 Production of Acrylic Acid from Ethylene Campos, Jun, Puranmalka Section 4 – Flow Sheets and Stream Reports ............................................................................... 30 4.1 Section 100 - Epoxidation of Ethylene ............................................................................... 31 4.2 Section 200 - Carbonylation of Epoxide ............................................................................. 35 4.3 Section 300 - Acid Catalyzed Rearrangement ...................................................................
Details
-
File Typepdf
-
Upload Time-
-
Content LanguagesEnglish
-
Upload UserAnonymous/Not logged-in
-
File Pages261 Page
-
File Size-