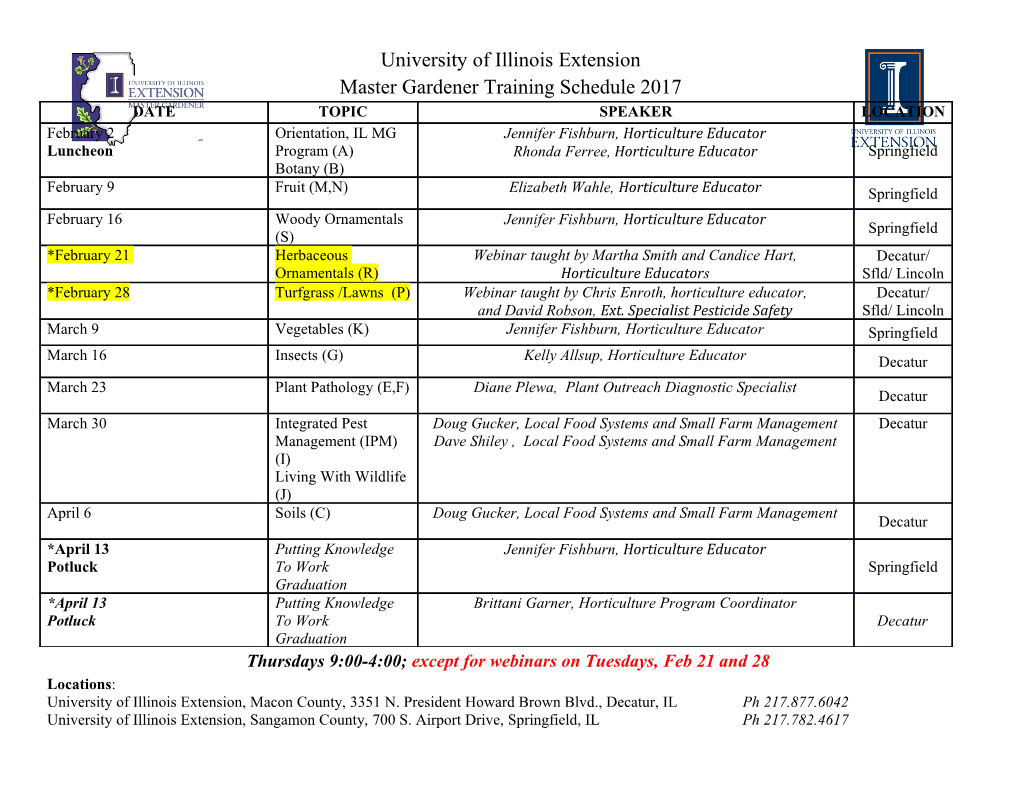
Kraft Recovery Course RecoveryRecovery BoilerBoiler January WaterWater TreatmentTreatment 2008 Presented By Sheppard T. Powell Associates, LLC Baltimore Maryland www.stpa.com Presentation Format 6 Objectives Of Treatment Program 6 Steam/Water Cycle: Basic Components 6 Top Routine Chemistry Parameters 6 Summary 1 Objectives Of Treatment Program Component Deposit Corrosion Condensate System -- Minor Feedwater System -- Minor Boiler Minor 0 or Minor Superheaters 0 0 Turbines 0 0 Boiler Deposit Example 6 Thick Nose Tube Deposits of Copper and Copper Oxides Over Mixed Iron Oxide, Hardness Phosphate and Carbon 2 Boiler Blistering Example Boiler Corrosion Example 6 Deposits After Brushing 6 Under-Deposit Corrosion 3 Turbine Deposits Example Superheater Corrosion Example 4 Steam/Water Cycle Diagram Sweetwater Condenser FW Out FW In CCNa Mill Condensate(s) Condensate Desup. CCNa S Water Steam Storage S S TU SC Boiler Steam (For Each) pH S SC S S Condensate Vent SC S Filter/Polisher S Na System CC Blowdown/Makeup Heat Exchanger pH Desuper- Deaerator heating And Storage SC Water Na S S DO S SiO2 Treated Makeup Feedwater S Makeup S Storage Heater(s) SC Usually Operated As A Grab Sample Point NaSiO2 QuestionsQuestions 5 Specific Conductivity 6 Total Conductive Solids (Salts, Acids, Alkalis) 6 High Levels Can Cause Foaming and/or Corrosion 6 Units: Usually µS/cm 6 Micromho (µmho/cm) = Microsiemen (µS/cm) 6 Millimho (mmho/cm) = Millisiemen (mS/cm) 6 1 mS/cm = 1000 µS/cm (Beware of auto-switching ranges on meter!) Specific Conductivity Normal Values, Sample Main Source µS/cm Demineralized Water 0.05 – 5.0 NaOH Leakage Condensate & 2.0 – 6.0 Amine Feed Feedwater Boiler Water 20 – 150 (a) 3 to 5 × PO4 (a) Much Higher For Low Pressure Boilers On Softened Makeup 6 Example of Amine Blend Effect on Conductivity 12 Trial A - Change in SC 10 (33.9 - 35.7°C) Trial B - Change in SC y, µS/ cm t 8 (34.0 - 36.3°C) ivi t c u 6 Co n d 4 ic cif 2 pe S 0 0 1 234567 8910 Volume of Amine Blend, ppm pH (Relative Acidity and Alkalinity) 106 105 104 103 102 10 1 1 10 102 103 104 105 106 Acid Units Base Units 01234567891011121314 pH Neutral pH Demineralized Water Condensate/Feedwater Vinegar Boiler Water Lemon Juice Household Ammonia 5% Sulfuric Acid 4% Caustic Soda 7 Example of Amine Blend Effect on pH 9.4 9.2 9.0 H p 8.8 Trial A - pH (33.9 - 35.7°C) 8.6 Trial B - pH (34.0 - 36.3°C) 8.4 8.2 12345678910 Volume of Amine Blend, ppm Effect of pH on Copper Transport 50.0 ar e Y 2 10.0 m sion g/ ro , r o 70Cu/30Ni 9 0Cu/ 10Ni Copper C 1.0 uct Release d Pr o 0.2 7.0 8.0 9.0 10.0 pH 8 Dissolved Oxygen 6 Oxygen as O2 (from air) dissolved in water. Corrodes copper and steel (economizer shown). 6 1 ppm O2 = 1 mg/L = 1000 ppb = 1000 µg/L Dissolved Oxygen Effect on Copper Corrosion 16 14 70Cu/30Ni (Alloy 715) 3 ppb O2 100-200 ppb H y 70Cu/30Ni (Alloy 715) 200 ppb O 25 ppb H 12 2 90Cu/10Ni (Alloy 706) 3 ppb O2 100-200 ppb H ,mp 10 90Cu/10Ni (Alloy 706) 200 ppb O 25 ppb H te 2 a R 8 n sio 6 rro 4 Co 2 0 0 50 100 150 200 250 300 350 400 450 Temperature °F 9 Dissolved Oxygen 6 Normal Values ¾ Mill Water or Demineralized Water Saturated (8,000 - 14,000 ppb) ¾ Condensate: 10 - 100 ppb O2 ¾ Feedwater: <5 - 10 ppb O2 6 Sources ¾ Air Leaks Where Water Leaks Out, Air Leaks In ¾ Mill Water In-leakage 0.1% Raw Water = 8 - 14 ppb O2 Dissolved Oxygen Control: Deaerator Water Inlet Vent Distributor Nozzles Trays Steam Inlet 10 Deaerator Spray Nozzles And Trays Oxygen Scavengers – Carbohydrazide Example 6 Oxygen Scavenging (Reduces Oxygen) ¾ Oxygen + Carbohydrazide → Inerts + Carbonic Acid 6 Passivation ¾ Red Rust + Scavenger → Black Rust + Carbonic Acid 11 Oxygen Scavenger Feed 6 Underfeed ¾ Copper Corrosion in Steam/Condensate System ¾ Pitting of Economizer 6 Overfeed ¾ FAC: Flow Accelerated Corrosion and Rupture of Steel Pipe Lines (e.g., Feedwater Line) ¾ Decomposition Products QuestionsQuestions 12 Hardness In Generation Bank Tube 6 Hardness Scale In Generation Bank Tube, Dispersant Treatment 6 Without Dispersants, Gray Mayonnaise Deposits Are In Drums Hardness – Definition 6 Mainly the Calcium (Ca) and Magnesium (Mg) 6 Precipitates and Forms Hardness Scale In Boiler 6 Precipitation Can Result in Decreased Boiler pH Hardness + Phosphate → Sludge + Salt + Acid Calcium Sodium Calcium Sodium Sulfuric + → + + Sulfate Phosphate Phosphate Sulfate Acid 3CaSO4 + 2Na2HPO4 → Ca3(PO4)2 + 2Na2SO4 + H2SO4 13 Hardness - Limits 6 Expected Values (ppm CaCO3) ¾ Feedwater and Turbine Condensate: 0.0 ¾ Process Condensate 0.0 – Trace 6 Sources ¾ Mill Water In Condensate/Feedwater ¾ Problem In Makeup Demineralization System Control of Hardness: Prevent Intrusion Condensate/Feedwater Condensate/ Pump Discharge Feedwater Two Isolation Valves For HP Service Pump Seals Cooling Water Drain Drain Seal Water Throttling Valve 14 Phosphate (PO4) 6 Amount of Sodium Phosphate Dissolved in Boiler Water 6 Units: ppm PO4 = mg/L PO4 6 Purpose: ¾ Stabilizes pH ¾ Precipitates Hardness as Softer Deposits ¾ Backup Indication of Hardness Contamination Phosphate/pH Control Curves 10.5 3.0 aOH) 2.7 (1 ppm N psig um Line 800 quilibri MPa) E sig (5.5 2.4 10.0 1200 p .3 MPa) psig (8 500 1 MPa) (10.3 4 tio PO 9.5 a : H Na p olar R 9.0 M 8.5 8.0 61014 18 22 26 30 Phosphate, mg/L 15 Phosphate Effect on Boiler Water pH Sodium-To-Phosphate Molar Ratio 3.0 NaOH 2.6 2.4 TSP 2.2 DSP H 2.1 p (MSP) Blowdown 2.0 Phosphate, mg/L Summary: What Should You Know? 6 Top Chemistry Parameters in Steam/Water Cycle ¾ Conductivity µS/cm ¾ pH ¾ Dissolved Oxygen, ppb O2 (and Oxygen Scavengers) ¾ Hardness, ppm CaCO3 ¾ Phosphate, ppm PO4 6 Steam/Water Cycle, Basic Components 6 Other (See Appendices) 16 Appendices 6 A: Makeup Water Treatment 6 B: Condensate Collection and Treatment 6 C: Feedwater Treatment System 6 D: Boiler Water Treatment 6 E: Steam Purity Considerations 6 F: Additional Chemistry Testing 6 G: Preventive Maintenance 6 H: Personnel Training 6 I: Chemical Cleaning For More Information 6 TAPPI Technical Information Papers ¾ TIP 0416-03 – Water Quality and Monitoring Requirements for Paper Mill Boilers Operating on High Purity Water, 1999 ¾ TIP 0416-04 – Design Engineer Decision Tree: Paper Mill Boiler Feedwater, 1999 ¾ TIP 0416-05 – Response to Contamination of High Purity Boiler Feedwater, 2000 ¾ TIP 0416-06 – Keys to Successful Chemical Cleaning of Boilers, 2000 17.
Details
-
File Typepdf
-
Upload Time-
-
Content LanguagesEnglish
-
Upload UserAnonymous/Not logged-in
-
File Pages17 Page
-
File Size-