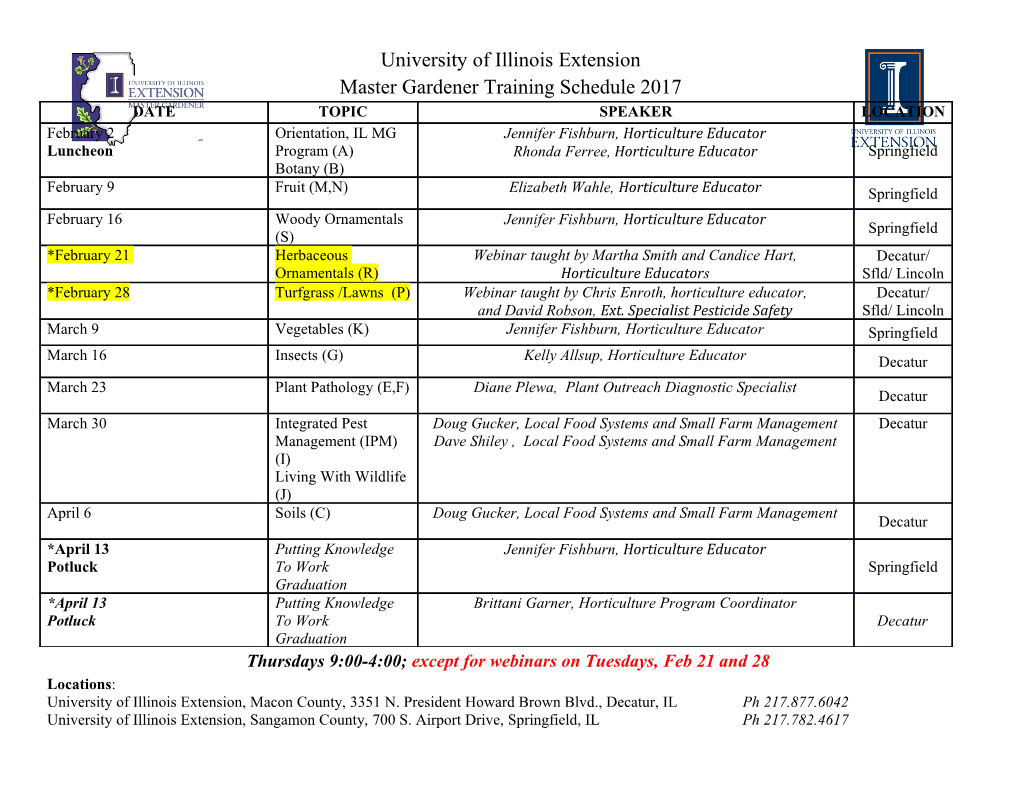
YCAS0250-0440 60 HZ, YCAS0218-0328 60HZ, YCAS0693-1263 50 HZ, YCAS0685-1215 50HZ, START-UP CHECKLIST SERVICE POLICY & PROCEDURES Supersedes: Nothing Form 201.19-CL2 (309) COMMISSIONING References to IOM in this document are as Valves follows: Open each compressor suction, economizer, and dis- YCAS0250-0440 (60Hz-R22) - 201.19-NM2 charge valve fully (counter-clockwise) then close one YCAS0218-0328 (60Hz-R407) - 201.19-NM4 turn of the stem to ensure operating pressure is fed to YCAS0693-1263 (50Hz-R22) - 201.19-NM6 the pressure transducers. Open the liquid line service YCAS0685-1215 (50Hz-R407) - 201.19-NM8 valve fully and ensure the oil return line ball valve is open in each system. PreparaTION Commissioning of this unit should only Compressor Oil be carried out by YORK Authorized To add oil to a circuit - connect a YORK hand oil pump personnel. (Part No. 470-10654-000) to the 1/4" oil charging valve on the oil separator piping with a length of clean hose or copper line, but do not tighten the flare nut. Using clean oil of the correct type (“L” oil), pump oil until all The Millennium Microcomputer Control System air has been purged from the hose then tighten the nut. Operating Instructions must be read in conjunction Stroke the oil pump to add oil to the oil system. The oil with this section. level should be between the middle of the lower and middle of the upper sight glasses of the oil separator. PreparaTIOn – POWER OFF Approximately 5 gallons is present in the entire chiller The following checks should be made with the customer system, with 1-2 gallons in the oil separator. supply/supplies to the unit switched “OFF”. Fans Inspection Check that all fans are free to rotate and are not dam- Inspect unit for installation damage. If damage is found aged. Ensure blades are at the same height when rotated. take action and/or repair as appropriate. Ensure fan guard is securely fixed. Refrigerant Charge Isolation/Protection Units are normally shipped as standard with a full Verify that all sources of electrical supply to the unit refrigerant operating charge. Check that refrigerant are taken from a single point of isolation. Check that pressure is present in both systems and that no leaks are the maximum recommended fuse sizes have not been apparent. If no pressure is present a leak test must be exceeded. Reference the Technical Data Section in the undertaken. The leak(s) should be located and repaired. IOM Repaired systems and units supplied with a nitrogen holding charge must be evacuated with a suitable vac- Control Panel uum pump/recovery unit as appropriate to below 100 Check the panel to see that it is free of foreign materials microns. (wire, metal chips, etc.) and clean out if required. Do not liquid charge with static water in the evaporator. Power Connections Care must also be taken to liquid charge slowly to avoid excessive thermal stress at the charging point. Once the Check to assure the customer power cables are connected vacuum is broken, charge into the condenser coils with correctly. Ensure that connections of power cables within the full operating charge. Reference the Technical Data the panels to the circuit breakers, terminal blocks or Section in the IOM. switch disconnectors are tight. FORM 201.19-CL2 (309) Grounding Compressor Heaters Verify that the unit’s protective terminal(s) are properly Verify the compressor heaters are energized. If connected to a suitable grounding point. Ensure that all the ambient temperature is above 96°F (36°C) the unit internal ground connections are tight. compressor heaters must be on for at least 8 hours before start-up to ensure all refrigerant liquid is driven out of Overloads the compressor. If the ambient temperature is below 86°F (30°C) then allow 24 hours. Ensure that the fan overloads settings are correct for the type of fan fitted. Water System Supply Voltage Verify that the chilled liquid system has been installed correctly, and has been commissioned with the correct Verify that the site voltage supply corresponds to the direction of water flow through the evaporator. The inlet unit requirement and is within limits. Reference the should be at the refrigerant pipework connection end of Technical Data Section in the IOM. the evaporator. Purge air from the top of the evaporator using the plugged air vent mounted on the top of the Control Transformer evaporator body. Flow rates and pressure drops must The 3-wire control transformer is mounted external to be within the limits given in the Technical Data Section. the panel. It is important to check that the correct primary Operation outside of these limits is undesirable and could tapping has been used: cause damage. With the supply voltage to the unit turned off, remove Flow Switch the lid to the transformer box. Verify a chilled water flow switch is correctly fitted in Check that the tapping used conforms to the site supply the customer’s pipework on the evaporator outlet, and voltage. After the tapping is verified, replace the lid. wired into the control panel correctly using shielded cable. There should be a straight run of at least 5 pipe Switch Settings diameters on either side of the flow switch. The flow switch should be connected to terminals 13 and 14 in Ensure that the unit ON/OFF switch on the display door the micro panel. and the micro board system switches S2 through S5 are set to “0” (OFF). Set the red handled emergency stop Temperature Sensor(s) device on the options panel to “1” (ON). For units fitted with door interlocked circuit breakers the power panel Ensure the leaving liquid temperature sensor is coated doors must be closed and the devices set to “1” (ON). with heat conductive compound (part no. 013-00890- The customer’s power disconnection devices can now 000) and is inserted in the water outlet sensor pocket be set to ON. of the evaporator. This sensor also acts as the freeze protection thermostat sensor and must always be in the The machine is now live! water OUTLET sensor pocket. Control Supply Verify the control panel display is illuminated. Programmed Options The unit is fitted with an under voltage circuit in each panel and it may take between 5 to 10 seconds for its Verify that the options factory programmed into the contacts to close and energize the unit’s electronics, Microcomputer Control Center are in accordance with including the display on the main panel. the customer’s order requirements by pressing the “Op- tions” key on the keypad and reading the settings from the display. 2 JOHNSON CONTROLS FORM 201.19-CL2 (309) Programmed Settings Start-up Ensure the system cut-out and operational settings Remove the locking device from the unit Auto/OFF are in accordance with the instructions provided in switch which prevents unauthorized starting of the unit Section 8 of the IOM and with the general chiller op- before commissioning. Press the “Status” key, then turn erational requirements by pressing the “Program” key. the unit switch to the “1” position to start the unit (there The chilled liquid temperature control settings need to may be a few seconds delay before the first compressor be set according to the unit model and required operat- starts because of the anti-recycle timer). Be ready when ing conditions. each compressor starts, to switch the unit OFF immedi- ately if any unusual noises or other adverse conditions Date and Time develop. Use the appropriate emergency stop device if necessary. Program the date and time by first ensuring that the CLK jumper J18 on the microprocessor board is in the Oil Pressure ON position (top two pins). Then press the “Clock Set Time” key and set the date and time. When a compressor starts, press the relevant “System Pressures” key and verify that oil differential pressure Start/Stop Schedule develops immediately (Discharge Pressure minus Oil Pressure). If oil pressure does not develop, the automatic Program the daily and holiday start/stop by pressing the controls will shut down the compressor. Under no cir- “Set Schedule/Holiday” key. cumstances should a restart attempt be made on a com- pressor which does not develop oil pressure immediately. Setpoint and Remote Offset Switch the unit switch to the “0” position (OFF). Set the required leaving chilled liquid temperature Refrigerant Flow setpoint and control range. If remote temperature reset (offset) is to be used, the maximum reset must be pro- When a compressor starts, a flow of liquid refrigerant grammed by pressing the “Remote Reset Temp” key. will be seen in the liquid line sight glass. After several minutes operation and providing a full charge of refrig- FIRST TIME START-UP erant is in the system, the bubbles will disappear and be replaced by a solid column of liquid. During the commissioning period there Fan Rotation should be sufficient heat load to run As discharge pressure rises, the condenser fans oper- the unit under stable full load opera- ate in stages to control the pressure. Verify that the fan tion to enable the unit controls, and operation is correct for the type of unit. system operation to be set up correctly and a commissioning log taken. Be Suction Superheat sure that the Micro Panel is properly Check suction superheat at steady full compressor programmed and the System Start-up load only. Measure suction temperature on the copper Check List is completed. line about 6" (150 mm) before the compressor suction service valve. Measure suction pressure at the compres- Interlocks sor service valve.
Details
-
File Typepdf
-
Upload Time-
-
Content LanguagesEnglish
-
Upload UserAnonymous/Not logged-in
-
File Pages9 Page
-
File Size-