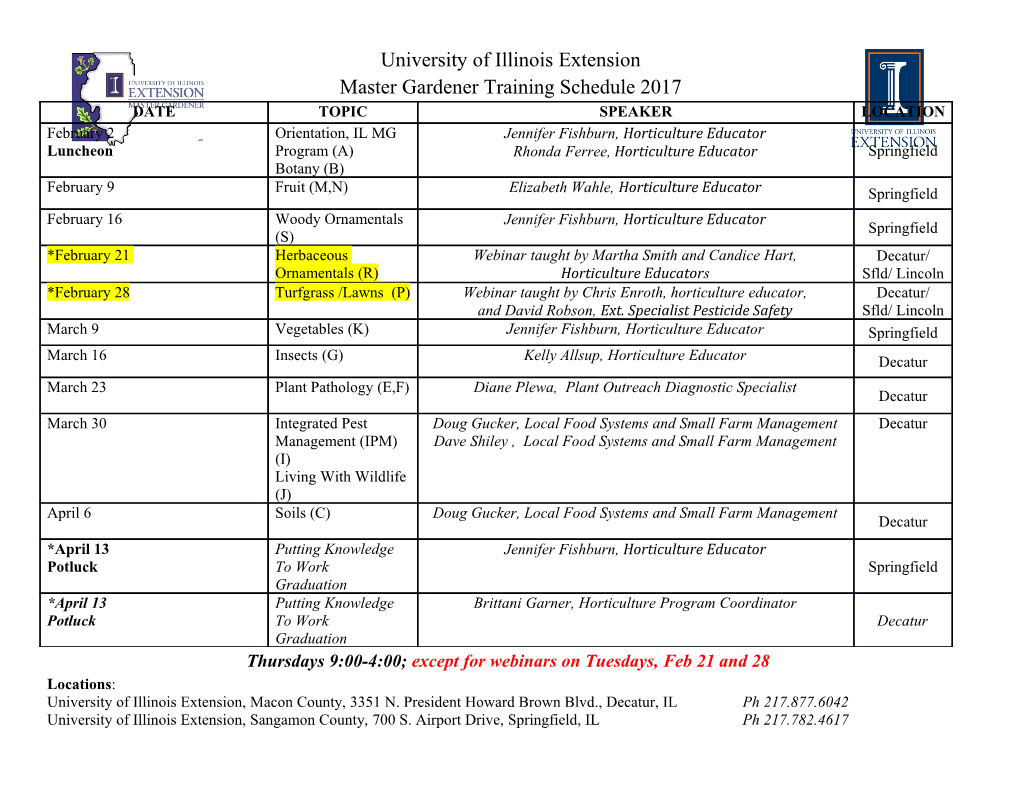
LIGHTFORM LIGHTFORM LIGHT FORM LIGHT FORM NEWSLETTER JULY 2018 Introduction Welcome to the first edition of LightForm News, our regular update on the progress of the EPSRC funded LightForm project. LightForm is a five-year multidisciplinary project with £4.8m (£5.9 FEC) core support from the EPSRC programme grant scheme, led by The University of Manchester, with partners at the University of Cambridge and Imperial College, London. Our vision is to provide the enabling science that will allow UK industry to achieve a step-change in the performance of the next generation of wrought, light-alloy, formed components, and innovate in the move to a circular economy, and digital simulation in manufacturing. We aim to exploit a new holistic manufacturing paradigm, whereby performance and efficiency can be simultaneously increased through intelligently embedding metallurgical design into the manufacturing cycle. LightForm will develop and integrate physical simulations of microstructure and texture evolution with engineering codes, allowing embedded materials engineering to be fully exploited by industry by developing the capability to accurately predict shape and properties in dynamic material systems. field-crystal plasticity modelling and will work on In addition, we are in discussion with several LAUNCH EVENT modelling titanium forging. forging companies, aerospace manufacturing end users, and the AFRC on the best route Following our launch event at the end of October Our team now also includes a research software forward to developing a large ‘MEME’ 2017, which was attended by 62 delegates engineer who is working on developing a data (Manufacturing with Embedded Metallurgical representing 22 companies across the supply chain, management framework for storing and sharing Engineering) programme on using a scientifically the academic team has been working hard on the of experimental and modelling data. His role informed approach to reducing the cost of ramp-up stage of the project. This has involved is also to ensure good engineering practice is producing forged Ti parts, by optimising the recruiting our core Post-Doctoral researchers and followed in all software development efforts. meeting with industry to discuss and organise the first process steps. phase PhD projects. We are pleased to report that we NEW PROJECTS In this first addition we are pleased to present now have a full team of seven talented researchers We have already set up nine new PhD projects an overview of our team. If you would like to with skill sets across modelling, advanced electron and two larger-scale associated projects; one with get involved we welcome contact through microscopy, in situ real-time experimental simulation the Innovate UK programme on the metallurgical our Programme Manager, Natalie Shannon techniques, forming technology and environmental underpinning research needed to qualify a high [email protected], or direct performance. deposition rate, additive manufacturing technology to the academic team. Please also visit our In addition, we have recently been joined by Dr that exploits in-process deformation, and also one Website for more detail of the project and up-to- Pratheek Shanthraj from the Max Planck Institute developing new thick section Al forging alloys with date news. Dusseldorf to take up the Airbus Research Fellowship Otto Fuchs. Phil Prangnell at Manchester. Pratheek is an expert in coupled phase Aluminium alloys are key materials in The warm forming work is a collaboration aerospace applications and are now with Constellium. It aims to improve finding increasing adoption in the our ability to warm form high strength automotive sector. In LightForm, the aim aluminium alloys by studying the effects of our aluminium research is to exploit of microstructure and alloy composition our understanding of microstruture on warm formability. This research will evolution and strengthening make extensive use of the new Interlaken mechanisms to enable the cost effective Forming Press at the Henry Royce Institute. forming of high strength alloys. We The new press, an Interlaken Servopress are interested in two main forming 225, will have temperature controlled processes: press quenching and warm dies for systematic studies of the effect of forming. forming temperature on formability and microstruture evolution. A PhD project on this topic will also start in September. Titanium These projects are being supported by Aluminium fundamental work on the interaction between deformation and precipitation research theme during worm forming. We have shown that we can measure the evolution of In LightForm, the research on titanium at Imperial and aims to use advanced research theme precipitate volume fraction and size during alloy forming is divided into two main testing and modelling to develop new warm forming using small angle X-ray areas: predicting the microstructure processes for hot forming of Ti sheet, In our press quenching research, we scattering experiments at the Diamond during hot bulk forming and supported by in-situ experiments. are collaborating with our partners Light Source and are now planning a predicting the ductility (forming limits) The advanced characterisation Impression Technologies to characterise programme of experiments to investigate of titanium alloys and the hot forming techniques used in Ti alloy research the microstructure of formed parts, effects of alloys composition, strain path, of titanium alloy sheet. and to understand and predict the texture and thermal history. include in-situ measurements of microstructure evolution during ageing In the bulk forming work we are microstructure evolution using and its impact on properties and This experimental work is being supported combining advanced microstructure synchrotron X-rays, detailed 3D corrosion performance. High resolution by computational modelling of formability. and mechanical characterisation characterisation using electron SEM and TEM investigations of formed We have started work on building a crystal with computational modelling of microscopy, bulk texture measurements parts are under way, complemented plasticity framework for virtual formability deformation and annealing to develop using neutron diffraction and by preliminary corrosion testing. This testing and, in parallel, we are developing models that can be used to predict thermomechanical simulation using a work will be continued by an Impression materials models for forming process microstructure in forged parts using deformation dilatometer and a Gleeble. Technologies sponsored PhD student simulations, with the aim to improve shape commercially available codes. The The computational modelling effort starting in September. prediction and predict the properties of the ductility research is mostly driven will address both deformation at the formed material. by Rolls-Royce and TIMET and has microstructural scale, using crystal the aim of understanding how the plasticity finite element modelling and ductility of an alloy depends on phase field modelling at Manchester, and the microstructure of the material. at the macroscopic, process scale using The plan is to use high resolution finite element modelling at Cambridge. digital image correlation (HRDIC) to Our industrial partners in titanium quantify deformation localization at forming research are Rolls-Royce, the microstructural scale and then TIMET, Doncasters and Airbus and also link it to the failure mechanisms via SEM image showing the the AFRC. We are working to grow this correlative microscopy and micro microstructure of a warm list and hope to recruit two more PhD X-ray tomography. We have recently formed aluminium alloy, students on this topic in the second year recruited a PhD for this project, showing precipitation at the of the project. who will start in September. The hot grain boundaries. sheet forming work is led by Nan Li NEW TEAM MEMBERS Dr Pratheek Shanthraj Dr Jinghua Zheng Dr Christopher Stuart Daniel Dr Patryk Jedrasiak Airbus Research Fellow - Pratheek has 10 completed a PhD in Mechanical Engineering recently obtained his EngD from the University of completed an MPhil in Engineering and a PhD years’ experience in computational mechanics, at Imperial College London, during which she Manchester with a thesis on the development of in numerical modelling of friction welding at the microstructure physics and scientific software developed a constrained ageing technique for crystallographic orientations (textures) during hot- University of Cambridge, where he is now a Research development at leading institutes in the US, residual stress reduction in aluminium aircraft rolling of dual-phase zirconium alloys. In LightForm, Associate. Patryk’s research experience includes a Germany and Japan, he has joined us from the Max- components. She also established and validated Christopher leads the in-situ characterisation fellowship at Harvard University, focusing on a novel Planck-Institut für Eisenforschung, to take up the physically-based constitutive equations for FE of light alloys and is working to develop in-situ Eulerian numerical method for simulating elastoplastic Airbus Research Fellowship at Manchester. Pratheek models of residual stress and yield strength characterisation capabilities for studying the micro- solids, 3 years part-time at the industrial sponsor of his obtained his PhD in Electro-Thermo-Mechanical distributions in components. Based at Imperial mechanics of deformation at elevated, hot and PhD, The Welding
Details
-
File Typepdf
-
Upload Time-
-
Content LanguagesEnglish
-
Upload UserAnonymous/Not logged-in
-
File Pages5 Page
-
File Size-