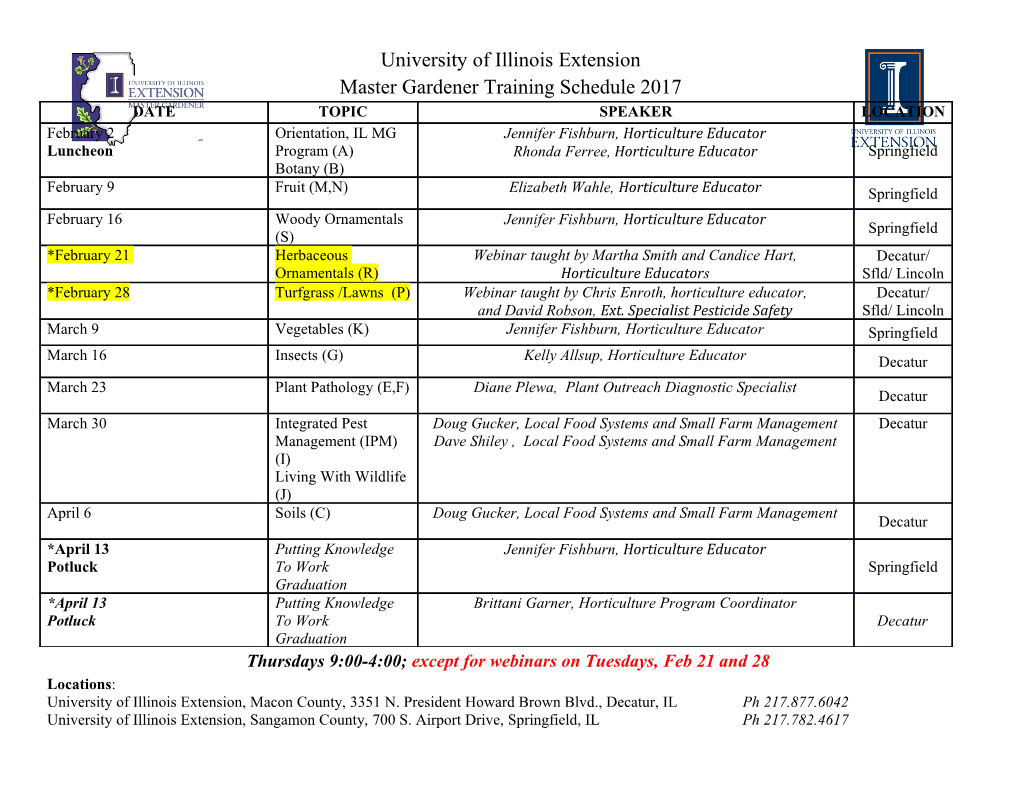
Akbulut and Ayrilmis J Wood Sci (2019) 65:46 https://doi.org/10.1186/s10086-019-1822-4 Journal of Wood Science ORIGINAL ARTICLE Open Access Some advantages of three-layer medium-density fbreboard as compared to the traditional single-layer one Turgay Akbulut and Nadir Ayrilmis* Abstract The aim of the study was to develop three-layer medium-density fbreboard (MDF) manufacture by adding the coarse fbres in the middle layer, like three-layer particleboard. The liquid urea–formaldehyde (UF) resin was reduced from 10.5 to 6.5 wt% in the middle layer of the MDFs. The UF resin content was kept constant at 10 wt% in the surface layers of all the MDFs. Moreover, the average density of MDFs was decreased from 730 to 650 kg/m3. The internal bond strength of three-layer MDFs decreased with decreasing UF resin content (10.5 to 8.5 wt%) in the middle layer. However, the decreases in the internal bond strength were statistically not signifcant. The internal bond strength values of the MDFs having density between 730 and 675 kg/m3 did not show signifcant diferences. The cost savings of the resin were 20% when the amount of resin was reduced from 10.5 to 8.5 wt%. Three-layer MDFs had lower resin consumption at lower densities over traditional single-layer MDFs produced in the same plant with the same mate- rial components without decreasing their technological properties. In conclusion, it can be said that three-layer MDF could be produced at a lower cost than traditional single-layer MDF. Keywords: Three-layer fbreboard, Coarse wood fbres, Technological properties, Density, Resin Introduction by the wood-based panel industry. Lightweight boards Medium-density fbreboard (MDF) is the second most such as light-fbreboard and light-particleboard have used wood-based composites in furniture production gained a great interest in the furniture industry due to and interior decoration behind three-layer particleboard their signifcant advantages such as light furniture, low which has signifcant advantages such as lower den- production cost, low transportation cost, low wood con- sity and lower production cost. In 2017, the largest cat- sumption, and energy savings [2]. In particular, increas- egory by volume in Europe (+EFTA) was particleboard ing costs of wood material and transportation force (31.2 million cubic metres), followed by MDF (12.3 mil- manufacturers to decrease the density of panels possess- lion cubic metres) [1]. Particleboard takes up the largest ing acceptable technological properties. portion of the market of wood-based composites. In the Te surface quality of MDF is better than that of traditional MDF production, surface and middle layers the particleboard [3]. Tis is because the fbre size is are composed of uniform fne wood fbres. However, the quite smaller than the surface particles of the particle- surface layers are made from small particles and the mid- boards [4]. Particleboard meets the minimum physical dle layer is made from coarse wood particles in the par- and mechanical requirements for panel-type furniture ticleboard production. Due to shortage of wood material although its middle layer is produced from the coarse worldwide, lightweight design concept, as a promising particles. To achieve a smooth surface for the MDF, the alternative to conventional panels, has been considered surface layers should be prepared from fne fbres. How- ever, the fbres in the core layer do not directly afect the *Correspondence: [email protected] surface properties of the MDF. As a result, the core layer Department of Wood Mechanics and Technology, Forestry Faculty, of the traditional single-layer MDF can be prepared from Istanbul University-Cerrahpasa, Bahçeköy, 34473 Sarıyer, Istanbul, Turkey © The Author(s) 2019. This article is distributed under the terms of the Creative Commons Attribution 4.0 International License (http://creat iveco mmons .org/licen ses/by/4.0/), which permits unrestricted use, distribution, and reproduction in any medium, provided you give appropriate credit to the original author(s) and the source, provide a link to the Creative Commons license, and indicate if changes were made. Akbulut and Ayrilmis J Wood Sci (2019) 65:46 Page 2 of 7 coarse fbres, which may result in a lower resin consump- PR 48/50) in MDF factory in Turkey called Kastamonu tion as compared to the fbres of surface layers due to Integrated Wood Company (Kocaeli city, Turkey). decreasing surface area. Rotational speed of the disc and grinding chamber Resin is the next expensive raw material after wood temperature of the defbrillator (Pallmann™ model: PR material. As compared to the single-layer MDF, three- 48/50) were 1500 rpm and 150 °C. Te wet fbres were layer MDF can reduce resin consumption in the mid- dried in a wood dryer (Selnikel™) to 2–3% moisture dle layer due to decreasing surface area of wood fbres. content. Te fan speed and air fow rate were 990 rpm Urea–formaldehyde (UF) is the most used resin among and 400.000 m3/h, respectively. Te digester was set to the thermosetting resins in the production of wood-com- 8 bar, 170 °C, and 4 min. Te defbrillator gap distance posite panels for use in dry conditions Te signifcant was kept constant at 0.4 mm for the production of the advantages of UF resin are lower price, easy supply, trans- surface layer fbres, while it was kept at 0.8 mm for the parent colour, lower pressing temperature and time, and production of the middle layer fbres. Te length and good mechanical properties in dry conditions. thickness of the fbres were measured from a hundred In the present study, it was aimed to develop three- fbres. Te specimens were randomly selected from the layer MDF manufacture by adding the coarse fbres in the coarse fbres. Tis procedure was applied for the fne middle layer. Te surface layers of the MDFs were pro- fbres. Te fne fbres of pine wood were used in the duced from fne fbres and the middle layer was produced surface layers, while the coarse fbres of beech wood from the coarse fbres. Te efects of resin content in the were used in the core layer. Te average length and middle layer and average panel density on the some tech- thickness of the middle layer fbres were found to be nological properties of MDFs were determined. 11.5 mm and 0.73 mm, respectively; while the average length and thickness for the surface layers fbres were Materials and methods 4.30 mm and 0.51 mm, respectively (Fig. 1). Wood fbres Te wood chips of softwood (Pinus sylvestris) and hard- wood species (Fagus orientalis Lipsky) were used in the Resin production of MDFs. Te round woods having about UF resin (E1 grade) with solid content of 50 wt % 20–25-cm diameter were fed into the drum type chip- acquired from the MDF factory of Kastamonu Inte- per with three knives using automatic belt feeding sys- grated Wood Company was used in the production of ™ tem (Pallmann model: PHT 500 × 1050, motor force: MDF panels. Liquid ammonium chloride with solid 500 kW, knife angle: 30°). Wood fbres were produced content of 20 wt% was added to the UF resin as a by thermo-mechanical defbrillator (Pallmann™ model: catalyst. Fig. 1 a Fine wood fbres (pine) used in the face layers of MDF. b Coarse wood fbres (beech) used in the core layer of MDF Akbulut and Ayrilmis J Wood Sci (2019) 65:46 Page 3 of 7 Manufacturing of three‑layer MDFs used on the caul to prevent bonding between the mat and Te surface layers of the MDFs were produced from the cauls. Following the pre-pressing, the mats were put in fne fbres while the middle layer was produced from the the hydraulic hot press (Cemil Usta company, model: SSP coarse fbres (Fig. 2). In the frst phase of the study (MDFs 180). Te mats were hot pressed at 3.5 N/mm2 and 190 °C coded from A to E), the resin content in the middle layer for 480 s to obtain MDFs having a density of 700 kg/m3. was reduced from 10.5 to 6.5 wt%, but the 10.5 wt% resin Te diferent densities of the MDFs were made by adjust- was maintained in the surface layers. In the second phase ing pressure. Te maximum hot-press pressure was grad- (MDFs coded from F to I), the density of the MDF was ually decreased from 3.5 to 3.1 N/mm2 to obtain diferent gradually decreased from 730 to 650 kg/m3. Te contents MDF densities ranging from 700 to 650 kg/m3. Hot-press of wood fbres and UF resin in the surface and middle pressure for the MDFs having 730 kg/m3 was increased layer were gradually decreased (Table 1). Te shelling to 3.6 N/mm2. Tree panels were produced from each ratio (surface/middle layer) of all the MDFs was kept type of MDF (Table 1). Te fnal thickness of all the MDF constant at 1:1. Te amount of the UF resin in the sur- panels was 10 mm. Te specimens were conditioned at face layers was fxed at 10.5 wt% for all the MDFs. As a standard atmospheric condition having 20 °C and 65% catalyst, aqueous ammonium chloride (at 1 wt% of solids relative humidity. content of resin) was incorporated into the UF resin. Te middle-layer fbres were put in the drum type Determination of technological properties of MDF blender (Altrad™; model: 250 L). Ten, the UF resin was Twenty-four-hour thickness swelling (TS) of the MDF applied by a nozzle spray gun on the wood fbres for specimens was determined in accordance with EN 317 5 min.
Details
-
File Typepdf
-
Upload Time-
-
Content LanguagesEnglish
-
Upload UserAnonymous/Not logged-in
-
File Pages7 Page
-
File Size-