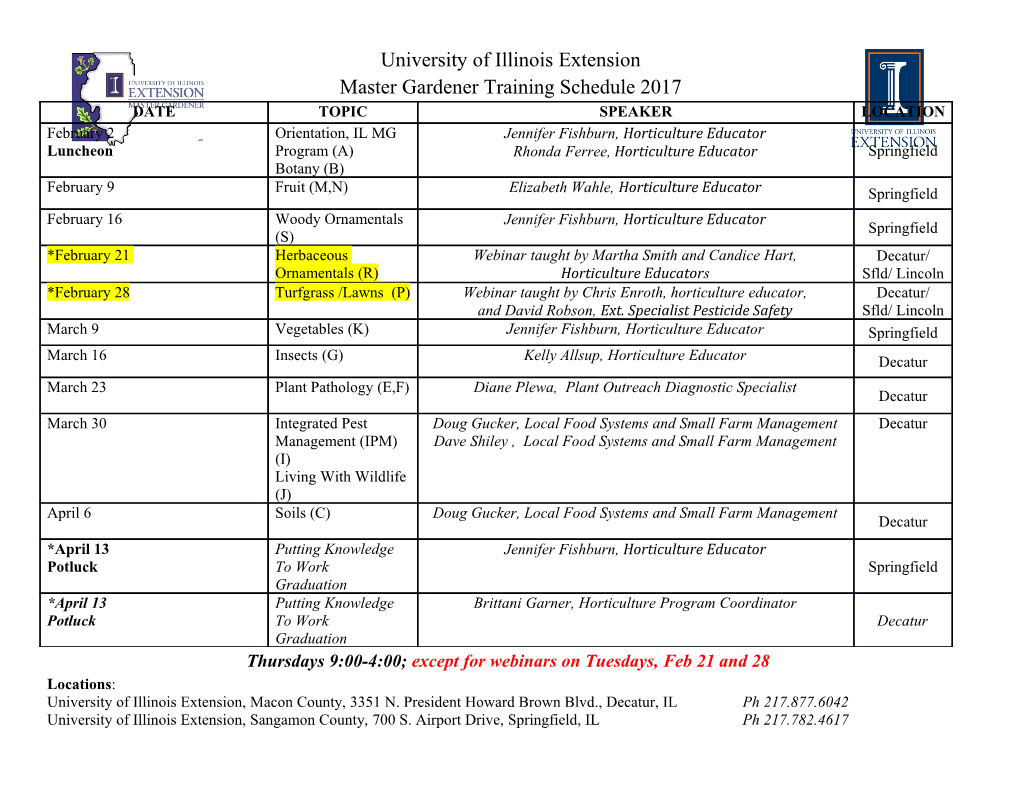
대학기계학회 2004년도 춘계학술대회 논문집 A Nanoindentation Based Study of Mechanical Properties of Al-Si-Cu-Mg Alloy Foam Cell Wall Md Anwarul Hasan*, Amkee Kim†, Chang-Hun Lee*, Hak-Joo Lee**, Soon-Gyu Ko** and Seong-Seock Cho*** 나노인덴테이션에 의한 Al-Si-Cu-Mg 합금 폼 셀 벽의 기계적 물성 연구 , ᓢᓘ, ᯧ, , ᩂ , ᧭᧟ Key Words : Nanoindentation(), Metal foam( ሬ), Mechanical properties (ࠦ ഻), Contact stiffness( ഻) Abstract Nanoindentation technique has been used to measure the mechanical properties of aluminium alloy foam cell walls. Al-Si-Cu-Mg alloy foams of different compositions and different cell morphologies were produced using powder metallurgical method. Cell morphology of the foam was controlled during production by varying foaming time and temperature. Mechanical properties such as hardness and Young's modulus were calculated using two different methods: a continuous stiffness measurement (CSM) and an unloading stiffness measurement (USM) method. Experimental results showed that hardness and Young's modulus of Al- 5%(wt.)Si-4%Cu-4%Mg (544 alloy) precursor and foam walls are higher than those of Al-3%Si-2%Cu- 2%Mg (322 alloy) precursor and foam walls. It was noticed that mechanical properties of cell wall are different from those of precursor materials. have been developed towards the goal of evaluating the 1. Introduction elastic modulus of thin films from nanoindentation load-displacement curve (7-9). Attempts have also been Indentation experiments have been being performed made to get more intrinsic properties such as yield (1,10 - for over 100 years to obtain hardness of materials (1), 13) or tensile strength (14) and even flow properties (15-20) but the recent years have seen significant improvements from indentation tests. in indentation equipments (1,2). The most latest of them So far the application of nanoindentation technique are the nanoindenter machines with which it is now has been limited to thin films and surface layers but it possible to monitor both load and displacement of an can also be used for measuring the elastic and plastic indenter during indentation experiments with high properties of cell wall material of metal foams. precision and accuracy even in submicron range (3-5). In this work we have used the nanoindentation The technique more commonly known as technique to measure the mechanical properties of cell nanoindentation technique has been widely being used wall material of closed cell Al-alloy foams. The Al-Si- now a days for measuring mechanical properties of thin Cu-Mg alloy foams of different compositions were films and surface layers (2,6). A number of techniques produced using powder metallurgical method. Hardness and elastic modulus of the precursors and foam walls † ৼ ࠦ were measured both from the unloading load- E-mail : [email protected] displacement curve and continuous stiffness TEL : (041)850-8616 FAX : (041)854-1449 measurement. The hardness and Young’s modulus * ৼ ࠦ ৼབ obtained from continuous stiffness measurement (CSM) ** ࠦ༆བ ࠦ *** ৼ ැ method were higher than that otained from the 382 대학기계학회 2004년도 춘계학술대회 논문집 Fig. 1 Cellular structure of the produced Al-Si-Cu-Mg alloy. unloading stiffness measurement (USM) method. Fig. 2 A schematic representation of the experimental apparatus. 2. Experimental of 50 nN and 0.01 nm respectively while the maximum 2.1 Materials and specimens load and displacement that can be applied are 500 mN The materials used in the study were Al-Si-Cu-Mg alloy and 500 µm respectively. The indenter was a Berkovich foam of two different compositions namely alloy 322 indenter which is a three sided pyramid with an aspect (22) (Al-3%Si-2%Cu-2%Mg) and alloy 544 (Al-5 wt% Si- ratio same as that of a Vickers indenter . 4%Cu-4%Mg) foams. Both of the foams were produced A total of 16 indentations were made in each of the using powder metallurgical method. Foam samples specimen as shown in Fig. 3 and after analysis, result of were obtained at different foaming time and different those 16 indentations were averaged to obtain the temperatures in the range 650 oC to 800 oC. mechanical properties of each of the specimen. It is (21) Specimens of 10 mm thickness were cut off from suggested that the successive indentations should be each of the foam samples and were mounted into at least 20 times the maximum penetration depth when thermo-set epoxy resin of 30 mm diameter x 15 mm using the Berkovich indenter. The maximum thickness. One face of the mounted specimens was penetration in our tests was 2000 nm, so we kept the polished to mirror surface. While preparing the distance between successive indentations to be 50 µm specimen, special care was taken so that after final which is 25 times the maximum penetration. polishing the opposite faces of the specimen are perfectly parallel to each other. A cellular structure of 2.3 Continuous stiffness measurement (CSM ) the alloy after foaming is shown in Fig.1. The contact stiffness between indenter and the specimen was continuously measured during 2.2 Apparatus and indentation procedure indentation. The continuous measurement of stiffness Experiments were performed using a Nanoindenter® was accomplished by applying a small oscillation to the XP a schematic illustration of which is shown in Fig. 2. force signal at a relatively high frequency (45 Hz). The At its most basic level the nanoindenter employs a high- amplitude of the force oscillation was 2 nm which is so resolution actuator to force an indenter into the test small that the deformation process is not significantly surface and a high-resolution sensor to continuously affected by its addition. The corresponding measure the resulting penetration. A diamond indenter displacement oscillation was monitored at the excitation is fixed to the end of the loading shaft that is suspended frequency and the contact stiffness, S was calculated on delicate leaf springs. The leaf springs are compliant from the amplitude of the displacement signal. From in the loading direction but stiff in the transverse this continuously measured stiffness the hardness and direction. The movement of the indenter toward the Young’s modulus of the specimens were obtained sample is accomplished by varying the force supplied continuously against the depth of indentation. by the magnet-coil assembly while the displacement of the indenter is measured by a capacitance displacement 2.4 Unloading stiffness measurement (USM ) gage. The system has load and displacement resolutions The unloading stiffness measurement is performed 383 대학기계학회 2004년도 춘계학술대회 논문집 specimen up to a maximum indenter tip displacement of 2000 nm. The load was then held constant for a period of 10 second. Peak load hold period in the load sequence diminishes the time dependent plastic effect and thus error caused by non elastic effect is minimized (8). Peak load hold period also provides a means for accounting the thermal effect in terms of drift rate (21). In the load displacement curve of Fig. 4. The differences in hardness of the materials are apparent from the difference in the peak load needed to attain maximum indentation. From the figure it is apparent that as the foaming time is increased at any foaming temperature, the load–displacement curve shifts upward Fig. 3 Nanoindentation marks on the foam cell walls indicating that a higher load is required for same of alloy 322 foam, T = 800oC / t = 4.5 min indentation. The Young’s modulus of alloy 322 and alloy 544 by obtaining a complete set of (both loading and precursors (material before foaming) are shown in Fig. unloading) load – displacement data and measuring the 5 while the hardness of both precursors are shown in slope of the initial portion of the unloading curve, S = Fig. 6. It is evident from Figs. 5 and 6 that alloy 544 dp/dh. also known as the elastic stiffness of contact. 160 From this elastic contact stiffness, it is possible to Alloy 322 Foam 140 determine the hardness and elastic modulus of the 322 Precursor 650-10 material being tested. The equations used for this 120 650-11 purpose are given by: 650-13 100 650-15 750-5 80 750-7 dp S = = 2 E A (1) 750-8 dh π r 60 800-4.5 Load (mN) 800-5.5 800-7 40 − ν 2 − ν 2 1 1 = 1 + i (2) 20 E E E r i 0 0 500 1000 1500 2000 2500 H = P (3) Indentation (nm) A Where S is the experimentally measured stiffness of Fig. 4 The load-displacement curves of Alloy 322 foams obtained from nanoindentation test. contact, Er is the reduced modulus (a parameter defined to account the effects of non rigid indenter on the load- displacement behavior) A is the projected area of elastic 80 β contact and is a constant that depends only on the 76 geometry of the indenter. The quantities E and υ are the Young’s modulus and Poisson’s ratio for the specimen, 72 Ei and υi are the same parameters for the indenter, H is 68 hardness, P is the applied load and A is the projected 64 area of indentation. Incorporating the values of Er (obtained from Eqn. 1), Ei, υi and υ in equation 2 gives 60 the Young’s modulus of elasticity of the material being 56 tested while Eq. 3 gives the value of hardness. Young's Modulus (GPa) USM method CSM method Alloy 544 Alloy 544 52 Alloy 322 Alloy 322 02468101214 3. Results and Discussion Test Sequence Fig. 4 represents experimental load-displacement curves for alloy 322 foams. The indenter load was Fig. 5 Young’s modulus of Al-Si-Cu-Mg alloys before increased gradually starting from the surface of the foaming 384 대학기계학회 2004년도 춘계학술대회 논문집 1.04 80 Alloy 322 78 0.96 76 0.88 74 0.80 72 70 0.72 68 0.64 66 0.56 64 USM method CSM method o o USM method CSM method Young's Modulus (GPa) 62 T=650 C T=650 C 0.48 544 Precursor 544 Precursor T=700oC T=700oC Nanoindentaion Hardness (GPa) 322 Precursor 60 o o 322 Precursor T=800 C T=800 C 0.40 58 02468101214 0 2 4 6 8 10 12 14 16 Test Sequence Foaming Time (min) (a) Fig.
Details
-
File Typepdf
-
Upload Time-
-
Content LanguagesEnglish
-
Upload UserAnonymous/Not logged-in
-
File Pages6 Page
-
File Size-