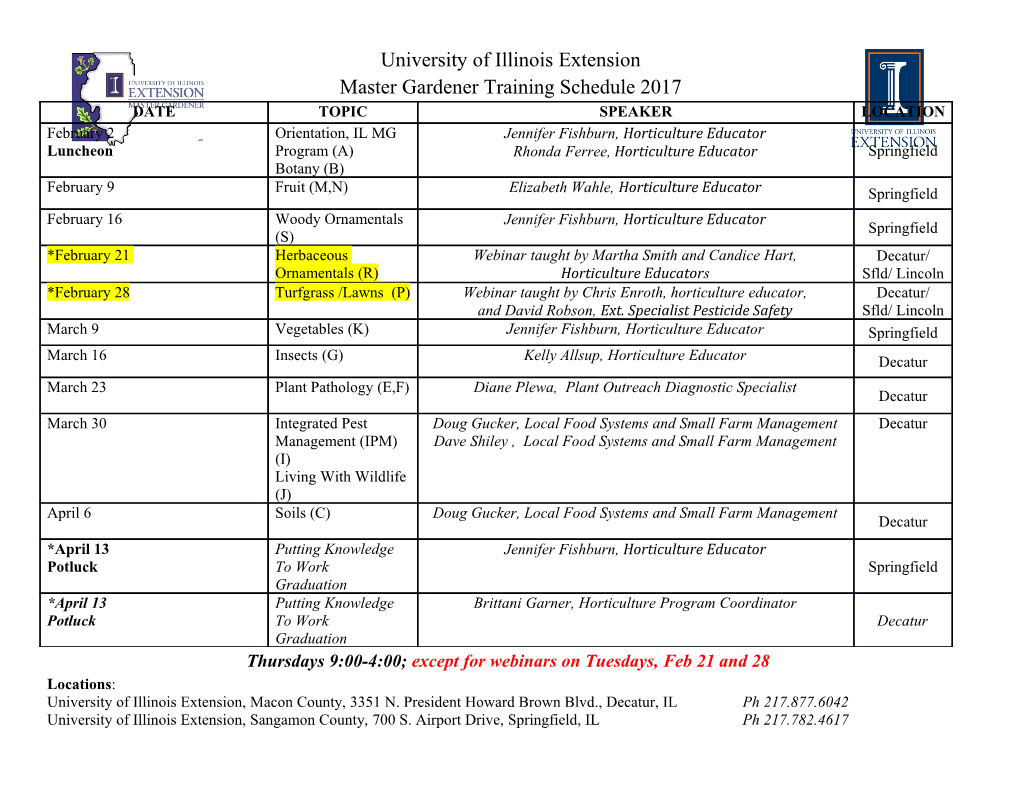
The Merits of Multifunctional Machining Flexibility and Productivity Make Solid Case for Machine Tool Integration Matthew Jaster, Associate Editor The design of EMAG’s VSC 400 DUO WF multifunctional machine is based on the pick-up principle of the EMAG single-spindle turning machine and features both gear turning and gear hobbing operations (courtesy of EMAG). Increased business in the aerospace, once again matched the same level as investing in the latest technology is the power generation, shipbuilding, auto- that seen at AMB 2008 when the econ- key to being competitive,” says Peter motive and alternative energy indus- omy was still booming,” says Ulrich Eelman, IMTS vice president of exhi- tries has led many manufacturers to Kromer, managing director of Messe bition and communications. believe that 2011 might be as good a Stuttgart. Higher productivity, faster setup time as any to invest in new machine Machine tool investments were times and single unattended operations tools. This was certainly the case last also a hot topic at IMTS in Chicago are just a few of the capabilities gear fall at AMB 2010 in Germany, where as “sold” signs popped up through the manufacturers seek in the multifunc- 60 percent of attendees planned to duration of the show. “Those searching tional machine tool market. make machine investments in the next for confirmation that manufacturing in Though more expensive and robust six months and 30 percent in the next the United States is not dying or dead than dedicated machine tools, many twelve. “According to the results of our found that it is robust and poised for believe these machines represent the survey, visitors’ propensity to invest growth. They clearly understand that continued www.geartechnology.com January/February 2011 GEARTECHNOLOGY 27 ments in gear hobbing have been in the areas of high-speed, dry and hard machining. “The driving force behind such innovations is usually the desire for cost reduction or product qual- ity improvement without attendant cost escalation. These new areas of application for gear hobbing operations have depended—to a large degree— on developments and innovations in machine design, tooling materials and tool coating technologies,” Loeztner says. The design of EMAG’s VSC 400 DUO WF multifunctional machine is based on the pick-up principle of the EMAG single-spindle turning machine. Both turning and gear hobbing opera- tions are of equal status. The VSC 400 The multifunctional capabilities of the SAMP HG 1200 Invento was on display at allows for the second operation in the IMTS 2010 in Chicago (courtesy of MAG). same set-up. “Spline and some gear cutting are By utilizing the VSC 400, Agco already done using Tsugami screw Fendt, a manufacturer and distribu- machines, Mazak Integrex, Bonfiglio tor of farm equipment, has brought an lathes and other turning centers,” Cluff overall cost savings of 18.5 percent adds. “This has been going on for some compared to the previous manufac- time, but in the 500 mm and above, turing process that used individual combo machines for turning, milling machines. The cost of machining an and hobbing are not yet a large influ- internal clutch plate carrier on the VSC ence in the technology of gear manu- 400 is only 71.5 percent of what it was facturing. Combination machines one when the component was made on a meter and above will have the greatest number of different machines. impact in large gear manufacturing in Loetzner believes that the benefits the next few years.” and limitations of process integration The Art of Integration are workpiece- and company-specif- Combination machines. Inte- ic. “This calls for close scrutiny of all grating a number of different manu- advantages and disadvantages with Gleason’s Agilus features a high- facturing technologies into a sin- individual processes on one hand and speed tool turret to locate fixed or gle machine tool is a growing trend multifunctional processes or machines driven tools for the complete range of at EMAG LLC. “Multifunctional on the other.” turning, drilling and milling operations (courtesy of Gleason). machine tools make an important con- Machine tool integration in both tribution to the consolidation of pro- large and small gears is definitely cess streams in both soft and hard becoming more feasible in today’s future of gear manufacturing altogeth- machining, as they combine turning, manufacturing environment, according er. milling, gear cutting and grinding oper- to Johannes Brogni, technical director Brian Cluff, vice president at Star- ations,” says Peter Loetzner, CEO of at Gleason Pfauter Maschinenfabrik in SU, thinks they will be most relevant EMAG. Studen, Switzerland. In early 2010, in the big gear industry. “The people Apart from eliminating transport Gleason unveiled the Agilus 180TH, a we talk with in the large gear market and wait-times, they also shorten inci- combination of a lathe and a hobbing are looking to combine operations into dental set-up and non-productive times. machine that accommodates shaft-type a single unit to minimize capital invest- When optimally equipped, they can be parts and is capable of producing disc- ment, maximize machine utilization used as full-fledged turning machines type parts as well. and reduce space and energy costs for or full-fledged gear hobbing machines. “The biggest advantage of this manufacturing very large gearing,” “The machines can be tailored to suit type of machine is that you can load Cluff says. “In the medium size gear the application, offering the optimal a forged blank that has been cut to market users are arranging machines to solution for a large variety of manufac- length and centered, and you get a fin- be automatically loaded (pallet loaders, turing requirements,” Loetzner says. ished part ready for heat treatment,” gantry loaders) to reduce changeover In the case of multifunctional tech- Brogni says. “This concept reduces the and idle times. nology, the most important develop- throughput time tremendously, provid- 28 GEARTECHNOLOGY January/February 2011 www.geartechnology.com ing the gear producer with a significant hobbing, chamfering and deburring the the soft blank to the finished gear. This cost reduction, especially when he is part, and then finish hobbing so that puts the company in the unique posi- producing smaller lot sizes of 50 to 500 the deburred flank is still large enough. tion to offer a wide array of multifunc- pieces.” When we are looking to machining tional equipment. With a long track record in gear centers for rotary symmetrical parts we The SAMP HG 1200 Invento, for processes, Gleason developed the can see that lathes today are capable example, addresses the requirements of Agilus for the single setup of all shaft- of performing many more processes large gears with diameters up to 1,200 and disc-type cylindrical gears up to beyond turning, like drilling, milling, mm and module 35.0 (40.0) in the 180 mm in diameter with shaft lengths rolling, etc. I think it is logical that this energy, transport and construction sec- up to 500 mm. It features a high-speed will also be the case with gears.” tors. It features a twin-table concept, tool turret to locate fixed or driven With the acquisition of SAMP’s enabling the operator to execute the tools for the complete range of turning, gear hobbing line, MAG IAS is able to complete setup and centering process drilling and milling operations. provide solutions for all processes from continued “One customer running an Agilus machine recently reported that the throughput time of his parts has been reduced from five days to one day, and that he was able to reduce the manufac- turing time by 45–50 percent, depend- ing on the parts,” Brogni says. “This reduction came primarily from the fact that the operator was able to optimize the process sequence very easily, with- out the need to consult others.” Additionally, the company has developed the ability to combine the Agilus cell with other manufacturing cells. “This means that we can place other machines like long hole drilling machines, dedicated turning machines, etc., enabling the manufacture of a part from the blank stage until the part is complete and ready to be hardened,” Brogni says. One key to making this technol- ogy work is the software. Brogni says the software is one of the major components to the success of the machine—it’s also a key challenge. “Two approaches were considered at Gleason; using turning software as the base and adding hobbing software or using Gleason-Pfauter hobbing soft- ware as the base and adding turning features. Either approach can work but we chose the latter so that the gear- related technology data and corrections can be handled easily and the hob man- agement is integrated into the software. This has the advantage that the turning programs, which are becoming very simple, can be created on external ISO program generators.” Brogni believes the benefits of multifunctional machines will drive a significant change in manufacturing thinking in the future. “It is possible to integrate processes that could not have been done before, like rough-cut www.geartechnology.com January/February 2011 GEARTECHNOLOGY 29 in masked time while the manufactur- cessing speed and higher throughput. 1,000 mm machines and are expanding ing process proceeds on the second In addition, part accuracy benefits from the technology to larger machines and work table. Reduction of setup time is the one setup process since you don’t gears.” not only possible for mass production have the errors inherent in multiple set- The company has an extremely but also for the manufacturing of small ups. There’s also a lower initial invest- wide range of products including ver- lots.
Details
-
File Typepdf
-
Upload Time-
-
Content LanguagesEnglish
-
Upload UserAnonymous/Not logged-in
-
File Pages8 Page
-
File Size-