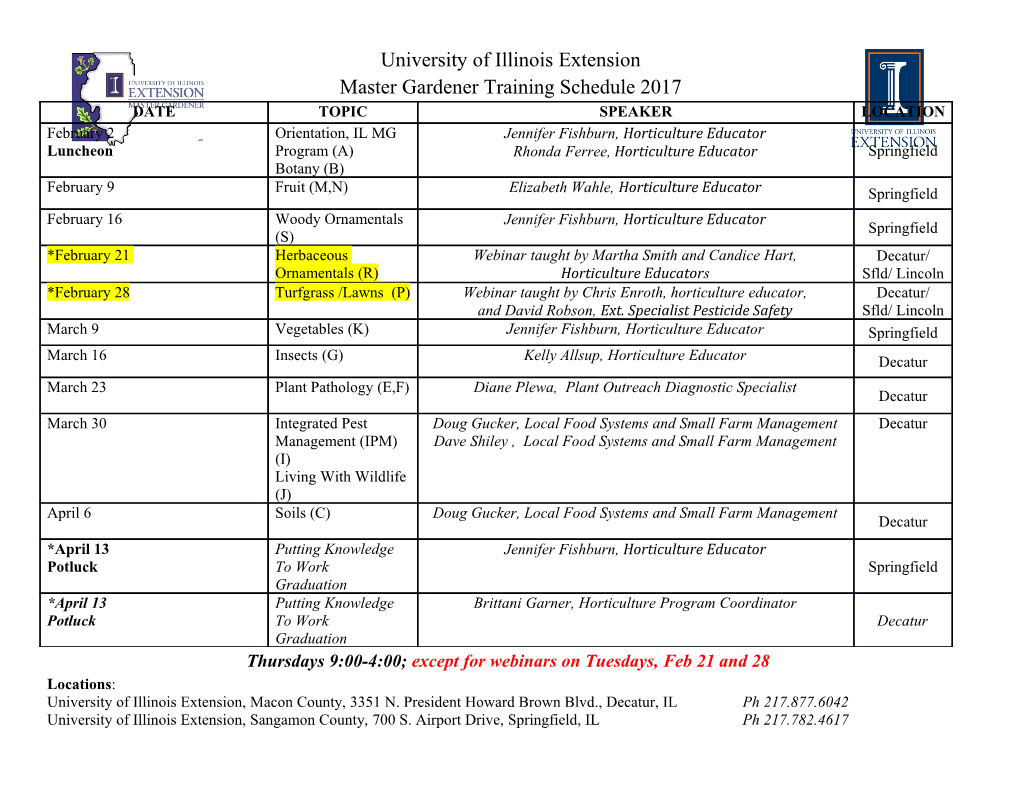
ON THE RECYCLE POTENTIAL OF PAPERMAKING FIBRES Two processes are compared BY J.L. KLOFTA, AND M.L. MILLER The first six factors represent the con- paring the pulp or paper properties of ditions present during the initial paper- recycled fibres with their virgin counter- J.L. Klofta, making from virgin pulp. The seventh parts. The “ultimate”recycle potential of factor is the only one involved in the pulp would be attained when the proper- Miami Univer- recycle process [6]. ties of the recycled paper equal or exceed sity, Oxford, OH The end use of the paper to which the those obtained from virgin pulp. Research recycle fibre is added is critical to the by Hipple and Khambadkone have shown assessment of recycled fibres. The desired recycle paper properties increase with a performance of the end product dictates specific combination of refining time, the different criteria needed for recycled fibre. amount of deinked secondary fibre and Recycle potential is measured by com- the addition of cationic starch [?I. TEST: CYCLE 0 ... r]-70/30 HW/SW I HANDSHEETSI-. TEST: CYCLE o LTHOUGH MANY RECYCLING studies appear in the literature, very few Anvestigators have specifically stud- ied the effects of deinking on the recycle potential of fibres. Most studies have con- cluded that recycling, in general, provides fibres which are somewhat detrimental in quality [ 1-51. The lower quality of recycled fibre is evident in the inferior physical and Reslush performance properties of recycled paper. The negative effects of recycling are iden- tified through such paper properties as tensile, burst and tear. These negative effects may be due to the recycling process itself or related to the manufacturing his tory of the recycled paper. andshe andsh andshe andsh Different pulps have different recycle potential. The most prominent factors affecting recycle potential are: 1. Fibre composition; 2. Degree of initial beating of the virgin pulp; 3. Extent of wet pressing; A: Pulp samples taken for testmg 4. Drying conditions; B: Sample hadgheets taka €or testing 5. Calendering effects; 6. Effects \of chemical additives; 7.Effects produced by deinking. T 320 4 PULP & PAPER CANADA 95:8 (1994) 41 This study was designed to evaluate the In order to simplify the sample was desirable. To obtain this intact state, fibre quality of inked and non-inked fibres nomenclature the following acronyms sample preparation has to employ a dehy- in pulp processed by two procedures: a are used: RS = reslushed, no ink applica- dration technique which avoids surface reslushing procedure (simulating machine tion; IRS = reslushed, with ink applica- changes as the fibres dry (i.e. surface ten- broke systems), and a deinking procedure tion on virgin sheets only; DI = deinked, sion effects). The technique commonly (reslushing with heat and chemical). As the no ink application; ID1 = deinked with used to avoid surface tension effects of pulp was recycled through a deinking pro- ink application on virgin sheets only. drying is critical point drying. Sample cess, fibre and paper characteristics were Numbers following the acronyms repre- preparation of pulp fibres was done by measured. Differences in fibre physical sent the number of recycles e.g. ID13 using a poly-L-lysine adhesion technique characteristics were related to changes in represents a handsheet that was inked [SI, followed by critical point drying. paper physical properties. Scanning Elec- and processed with 5% NaOH (deinked) Micrographs reveal individual fibres on a tron Microscopy (SEM) gave a visual repre- and recycled three times. clean background with fibrils mimicking sentation of the morphology of the fibres’ Pulp type and handsheet making: A mix- their wet-state morphology. surface in their papermaking state. ture of northern softwood and eucalyp- Image analysis on the micrographs tus hardwood in a 30:70 ratio was used. was done by scanning the images into an &E RIMENTAL Both pulps were bleached, kraft, NIST Apple Macintosh Image program. The standard reference materials. The pulp contrast levels were maximized to exag- General description: Figure 1 is a was refined to a Canadian Standard Free- gerate the difference between fibre schematic diagram of the steps involved ness (CSF) of 480 mL and handsheets surface and fibrils. The edges of the in the experiment. Two groups of inked were formed with a British Standard smooth fibre surface and the rough fib- and non-inked handsheets were pro- handsheet mold. No fillers, size, or addi- rillated surface were traced on the com- cessed through recycling stages and eval- tives were used in forming the hand- puter and measured pixel by pixel. The uated. One set, called the reslushed set, sheets. Drying was done under restraint ratio of the rough edge to the smooth was processed in the recycling stages with- at 108°C on a hot plate. The basis weight edge gives the fibrillation factor. out the deinking procedure. The hand- of the handsheets averaged 112 g/m2. Water retention values: The ratio of the sheets were reslushed by mixing with The handsheets were conditioned and grams of water remaining to the grams of deionized water in a TAF’PI disintegrator tested under TAPPI-specified conditions. fibre after centrifugation at standard con- until completely defibered. Samples were Ink application: A common lithographic ditions is termed the water retention value taken for testing while the remaining ink obtained from Wikoff Color Corpo- (WRV). TAPPI Useful Method 256 was fol- slurry was made into handsheets. The ration was applied by screen printing. lowed with a few minor adjustments to other set, called the deinked set, was The entire side of each handsheet was determine WRV. Pulp pads of about 1400 deinked using a deinking procedure sim- completely covered with ink and the g/m2 were made by filtering the pulp sus- ulating the process used at Cross Pointe amount of ink applied was approxi- pension through a tared crucible while Paper Company in West Carrollton, OH. mately 15% of the total sheet weight. applying a slight vacuum. Because begin- Deinking The paper was disintegmted at a Sheets from the virgin pulp were inked ning pad moisture may affect results, each consistency of 4% with 5% NaOH byweight and then recycled without application of sample was filtered until the surface of the and TEXO surfactant (6 drops/ 2 litres). ink between recycles. pad showed the first dry spots. The sam- Temperature was 60°C and the deinking Scanning electron microscopy/image ples were centrifuged at 900 g force for 30 time was 30 minutes. The pulp was washed analysis: Because one of the goals of these minutes. The moisture content of the cen- in a Bauer-McNett fibre classifier with a 100- experiments was to examine (under the trifuged pulp samples is expressed in g/g mesh screen until there was no ink in the fil- SEM) individual fibres in their “paper- of dry fibre. trate upon visual examination. making state”, an intact, wet fibre surface Fibre length and fibre coarseness: An Andritz-Sprout Bauer FibreScan length and width analyzer was used for fibre length measurements. Coarseness values were obtained from a correlation curve where Kajaani coarseness values of stail- dard pulps were plotted versus the width index obtained from the FibreScan. Fibre length, fibre coarseness, WRV and zero span tensile were measured to observe changes in fibre characteristics with recycling. The results for these fibre parameters are reported in Table 1. Fibre length and coarseness were not measured for the legs containing ink since there was concern that the ink would contaminate and confuse the instrument. As expected, fibrc length and coarse- ness did not change with an increase in recycle times. There was no mechanical treatment to produce changes in either fibre length or coarseness. Even though 75% of fines were lost in the deinking process for the DI leg, it did not affect the measured length factor much since it is a weighted average. 42 PULP & PAPER CANADA 95:8 (1994) 4 T321 -4 .I The zero span data in Table I indicate would be expected that ink, a hydropho- rebound. The DI leg of the exneriment that fibre strength remained essentially con- bic substance, might lower the surface stant for the RS and DI pathways. This result holding capacity of fibres for water. Loss would indicate that there has been no obvi- of surface area through the drying of fib- ous fibre weakening after four cycles of dis rils down onto the fibre's surface, loss of integrating, reforming, and drying even in fines and a loss of internal structure from the DI leg which involved 5% NaOH treat- intrafibre bonding during drying proba- ment, elevated temperature, and fines bly account for most of the loss in WRV. removal during the washing stage. However, regardless of why the fibres The two legs which contained ink, lose their water-holding capacity, recy- however, indicate that there was some cled fibres are likely to exhibit reduced fibre strength loss with recycling. This conformability and thus less bonding decrease in zero span value was attributed unless something is done to restore the to be an effect of the ink present in these wet compactability of the fibres. sheets. The ink probably acted as a lubri- Table I1 contains the apparent density, cant and allowed the fibres to slide past tensile index, and paper modulus for one another, and thus produced a lower paper recycled through four stages of zero span value. It appears that after suffi- reslushing and/or deinking. There was a cient ink was removed form the ID1 leg, decrease in each of these properties as the the zero span value was beginning to number of cycle times increased for each approach the values attained for the non- leg of the experiment.
Details
-
File Typepdf
-
Upload Time-
-
Content LanguagesEnglish
-
Upload UserAnonymous/Not logged-in
-
File Pages4 Page
-
File Size-