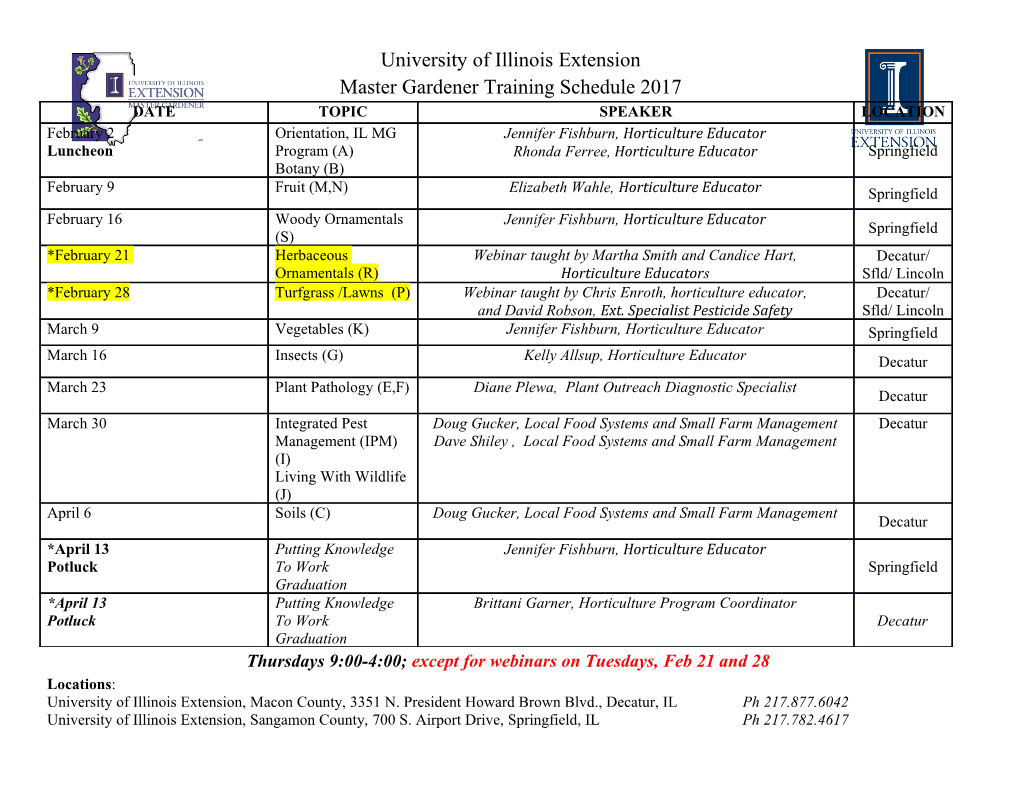
Surface & Coatings Technology 200 (2005) 1872 – 1878 www.elsevier.com/locate/surfcoat CVD diamond tool performance in metal matrix composite machining YR Kevin Chou *, Jie Liu Mechanical Engineering Department, The University of Alabama, Tuscaloosa, AL 35487, United States Available online 13 September 2005 Abstract Metal matrix composite (MMC) has found increasing usages in the industry for lightweight high-strength applications. However, because of abrasive nature of the reinforced phase in MMC, machinability is poor, tool wear is rapid, yet only diamond tools are technically suitable to MMC machining. Furthermore, diamond coatings seem to be more economically viable than polycrystalline diamond for MMC machining. In this study, CVD diamond-coated tools, 30 Am thick on a tungsten carbide substrates, were investigated by outside diameter turning of MMC of aluminum-alloy reinforced with silicon-carbide particles. Cutting conditions ranged from 1 m/s to 6 m/s of cutting speed, 0.05 mm/ rev to 0.3 mm/rev feed, and 1 mm to 2 mm depth of cut. Tool wear was measured and compared at different machining conditions. Worn diamond-coated tools were extensively characterized by scanning electron microscopy. Cutting forces, chip thickness, and the chip–tool contact area were also measured for cutting temperature simulation by finite element analysis. The results show that tool wear is sensitive to cutting speed and feed rate, and the dominant wear mechanism is coating failure due to high stresses. The catastrophic coating failure suggests the bonding between the coating and substrate is critical to tool performance. High cutting temperatures will induce greater interfacial stresses at the bonding surface due to different thermal expansions between the coating and substrate, and plausibly result in the coating failure. A thermal management device, heat pipe, has been demonstrated for cutting temperature reductions. D 2005 Elsevier B.V. All rights reserved. Keywords: Composite; Cutting temperature; CVD; Diamond coating; Machining; Tool wear 1. Introduction The ceramic reinforcement has greater hardness than conventional tool materials, e.g., 2400 Hv of SiC vs. 1800 Metal matrix composite (MMC) is a category of Hv of tungsten carbide (WC) [2], rendering only diamond engineering materials with growing applications in industry tools able to achieve economical tool life in machining such as automotive and aerospace. Examples of MMC ceramic reinforced MMC [2]. Diamond-coated tools, by applications include engine parts, brake system, drive shaft, chemical vapor deposition (CVD), have been investigated as and others such as pump housing and supercharger an economical alternative to brazed polycrystalline diamond compressors [1]. The advantage of MMC is the possibility (PCD) tools for machining advanced materials such as of tailoring material properties by combining matrix alloys MMC [3]. El-Gallab and Sklad reported, in a study of wear and reinforcement phase. The reinforcement phase in MMC mechanism of diamond tools in machining MMC, that can be presented in the form of particulate, short fiber and abrasion/adhesion by reinforced particulates are the domi- whisker, continuous fiber and monofilament. One major nant wear mechanisms and severe machining conditions division of MMC is aluminum-alloy matrix composite with will result in chipping in PCD and peeling of CVD diamond ceramics particulate reinforcement such as silicon carbide coating [4,5]. PCD tool is found to outperform CVD (SiC) and alumina. diamond coated tool and ceramic tools in machining of aluminum matrix composites, however, not economical [6]. Andrewes et al. also studied tool wear in machining Al/SiC * Corresponding author. composites using diamond tools and reported that mild E-mail address: [email protected] (Y.K. Chou). machining conditions are necessary to obtain economical 0257-8972/$ - see front matter D 2005 Elsevier B.V. All rights reserved. doi:10.1016/j.surfcoat.2005.08.094 Y.K. Chou, J. Liu / Surface & Coatings Technology 200 (2005) 1872–1878 1873 (a) perform better than smaller nose radii, due to increased resistance to plastic deformation [11]. Tool wear, in general, increases with increase of weight percentage and size of the reinforcement phase. However, there seems to exist a critical weight percentage of reinforcement above which abrasive wear would accelerate according to Li and Seah [12]. Cheung et al. studied reinforcement phases in MMC machining [13], and found that machinability is sensitive to the particle size and fraction. A higher amount of SiC will avoid large deformation and lead to better surface finish [13]. Applying cutting fluid in machining of aluminum MMC was reported, by Hung et al., to have no noticeable effects on tool performance [14]. On the other hand, in Cronja¨ger’s study, coolant and lubricant were only found to (b) accelerate tool wear in drilling and milling tests because the cutting fluid mixed with broken reinforcements forms abrasive emery fluid around the cutting zone [15]. MMC machining by CVD diamond tools have been reported with some mixed results. Due to the harder reinforcement phase, machinability of MMC is generally unfavorable and tool performance is sensitive to cutting parameters. Tool wear is complicated by abrasion from the hard ceramic phase, adhesion to the soft matrix material, and the bonding between the coating and substrate. In this study, machining of Al/SiC composite by CVD diamond tools was investigated with cutting force and temperature measured. Tool wear was also evaluated at different 40 µm cutting conditions and characterized by scanning electron microscopy (SEM). Finite element simulation of cutting Fig. 1. Tool and work material characteristics, (a) cutting edge of a CVD temperatures was also conducted to evaluate process diamond insert, and (b) MMC microstructure. parameter effects and to offer insight of CVD tool wear mechanisms. diamond tool life [7]. The authors found that tool wear involves two stages, one being initial flank wear caused by abrasion of hard particles, and the other combined adhe- 2. Experimental procedures sion–abrasion when the work materials start accumulatively adhering to the tool wear-land. Joshi et al. reported that For the machining test, cutting inserts used were CVD diamond tool wear is very sensitive to process commercial diamond coated inserts from sp3 Inc. The insert parameters [8,9]. Davim studied the influence of cutting substrate is 6% cobalt tungsten carbide of triangular shape. conditions on turning of aluminum matrix composites The diamond coating, from chemical vapor deposited (A359/SiCp/20), and concluded that cutting speed shows (CVD), has a nominal thickness of 30 Am, and the cutting more significant influence to tool wear than feed rate in edge radius is about 30 Am with grain size of 15 Am. Fig. 1a turning of A356 matrix composite [10]. El-Gallab and Sklad is a scanning electron micrograph of a CVD diamond further reported that a ‘‘protective’’ work material layer (not cutting edge. One-inch thick steel tool-holder was used and well-defined though) at the tool surface would form under the combination of the tool-holder and cutting insert forms high cutting speeds because of high cutting temperatures 0- and 11- of rake and relief angles, respectively. Work- associated. The authors also found an optimal rake angle, pieces were 47 mm round bars made of A359/SiC/20p bar 0-, to tool performance, and claimed that larger nose radii (cast and T6), which is A359 aluminum alloy reinforced Table 1 Temperature-dependent thermal conductivity, k (W/mIK), of diamond coating, WC substrate, and steel tool-holder T (-C) 25 100 200 300 400 500 600 700 800 900 1000 CVD diamond 2008 1344 306 93 WC 78.6 70.0 67.1 68.7 68.6 65.6 62.5 59.3 Tool-holder 42.7 42.3 37.7 33.1 1874 Y.K. Chou, J. Liu / Surface & Coatings Technology 200 (2005) 1872–1878 0.4 v = 6 m/s, f = 0.05 mm/rev depth of cut (d). No coolant was used in machining. A v = 6 m/s, f = 0.2 mm/rev triaxial piezoelectric force sensor (Kistler 9257B) with a v = 2 m/s, f = 0.05 mm/rev 0.3 v = 2 m/s, f = 0.2 mm/rev data acquisition system was used to measure three compo- nents, i.e., tangential, radial and axial, of cutting forces. Cutting temperature was also monitored using K type 0.2 thermocouples, attached to the tool surfaces, around 3 to 4 VB (mm) mm from the cutting edge. Tool–chip contact length and chip thickness were measured by optical microscopy to 0.1 evaluate the rake face heat-source area and the chip velocity. Tool wear, in flank wear-land width (VB), was periodically 0 measured through the machining test. Worn tools were also 0 5 10 15 20 25 thoroughly examined by scanning electron microscopy t (min) (SEM) to characterize the wear patterns, including material Fig. 2. Tool wear (VB) development at different cutting conditions. deposition, and wear mechanisms of CVD diamond tools in machining MMC. with 20% SiC particles. Fig. 1b shows the mcirostructure of the work material. OD turning of MMC bars by diamond-coated tools was 3. Heat transfer in the cutting tool system carried out on a precision CNC lathe. Machining parameters ranged from 1 m/s to 6 m/s of cutting speed (V), 0.05 mm/ Considering the cutting tool system, heat transfer in the rev to 0.3 mm/rev of feed rate ( f), and 1 mm to 2 mm of cutting insert and tool holder is by conduction. Heat transfer between the cutting tool system and the ambient media is by (a) 250 Fr Ft (a) Fa 200 150 F (N) 100 50 0 (2,0.05) (2,0.2) (6,0.05) (6,0.2) (b) 120 (b) T_rake T_flank 100 80 C) ° 60 T ( 40 20 0 (2,0.05) (2,0.2) (6,0.05) (6,0.2) Fig.
Details
-
File Typepdf
-
Upload Time-
-
Content LanguagesEnglish
-
Upload UserAnonymous/Not logged-in
-
File Pages7 Page
-
File Size-