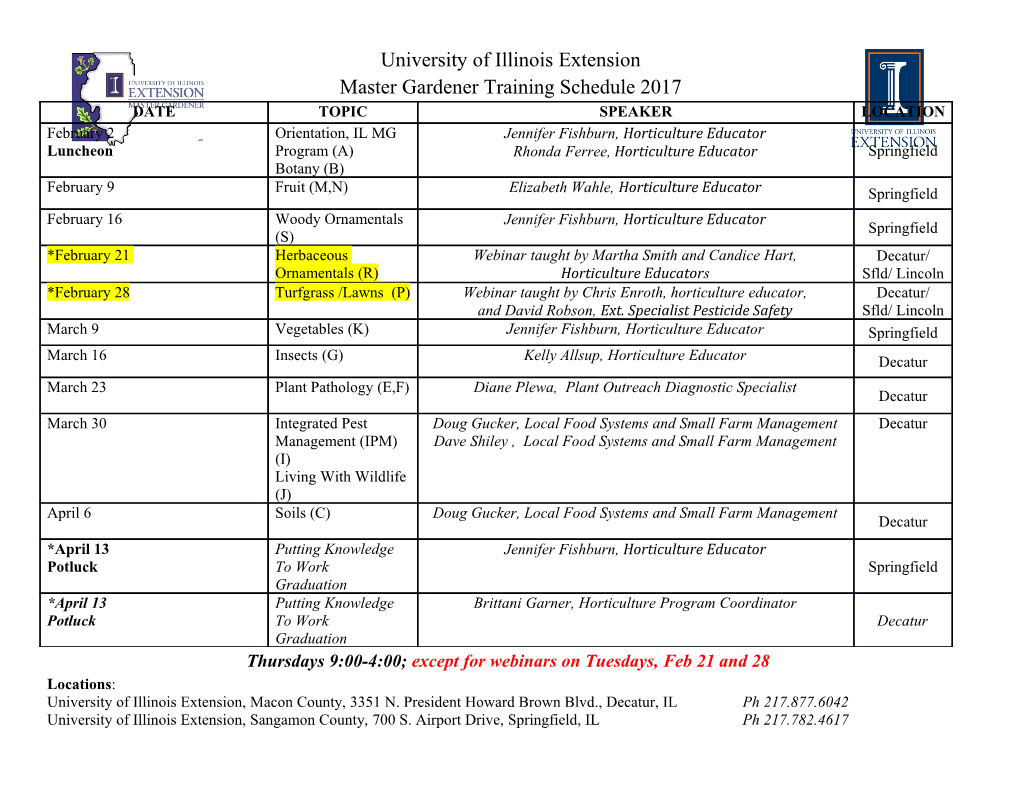
ARTICLE https://doi.org/10.1038/s41467-019-11803-8 OPEN Micro-/nano-voids guided two-stage film cracking on bioinspired assemblies for high-performance electronics Weining Miao 1,2, Yuxing Yao3, Zhiwei Zhang4, Chunping Ma4, Shengzhe Li5, Jiayue Tang6, He Liu2, Zemin Liu2, Dianyu Wang7, Michael A. Camburn8, Jen-Chun Fang8, Ruiran Hao6, Xinyu Fang8, Shuang Zheng 6, Nan Hu 4 & Xiaoguang Wang8 1234567890():,; Current metal film-based electronics, while sensitive to external stretching, typically fail via uncontrolled cracking under a relatively small strain (~30%), which restricts their practical applications. To address this, here we report a design approach inspired by the stereocilia bundles of a cochlea that uses a hierarchical assembly of interfacial nanowires to retard penetrating cracking. This structured surface outperforms its flat counterparts in stretch- ability (130% versus 30% tolerable strain) and maintains high sensitivity (minimum detec- tion of 0.005% strain) in response to external stimuli such as sounds and mechanical forces. The enlarged stretchability is attributed to the two-stage cracking process induced by the synergy of micro-voids and nano-voids. In-situ observation confirms that at low strains micro-voids between nanowire clusters guide the process of crack growth, whereas at large strains new cracks are randomly initiated from nano-voids among individual nanowires. 1 Technical Institute of Physics and Chemistry, Chinese Academy of Sciences, Beijing, China. 2 University of Chinese Academy of Sciences, Beijing, China. 3 Department of Chemistry and Chemical Biology, Harvard University, Cambridge, MA, USA. 4 Department of Civil, Environmental and Geodetic Engineering, The Ohio State University, Columbus, OH, USA. 5 Department of Mechanical Engineering, Imperial College London, London SW7 2AZ, UK. 6 Beijing National Laboratory for Molecular Sciences, Institute of Chemistry, Chinese Academy of Sciences, Beijing, China. 7 College of Chemistry, Jilin University, Changchun, China. 8 William G. Lowrie Department of Chemical and Biomolecular Engineering, The Ohio State University, Columbus, OH, USA. Correspondence and requests for materials should be addressed to S.Z. (email: [email protected]) NATURE COMMUNICATIONS | (2019) 10:3862 | https://doi.org/10.1038/s41467-019-11803-8 | www.nature.com/naturecommunications 1 ARTICLE NATURE COMMUNICATIONS | https://doi.org/10.1038/s41467-019-11803-8 eterogeneities on the micro-/nanoscale in solids, such as biocompatibility and chemical stability35–38, and ethoxylated voids and strain-induced cracks, can significantly influ- polyethylenimine (PEIE) was doped in PDMS to enhance the H 39 ence bulk electronic, optical, and mechanical properties, stretchability (Supplementary Figs. 4 and 5). Next, the formed which offers the basis of a new class of flexible devices, ranging PDMS nanowire array with a nanowire diameter of 400 nm was from wearable electronics1–6 to mechanochromisms7–9 to micro- immersed in ethanol. As ethanol evaporated, the nanowires bent scale patterning10–13. Specifically, metal film-based wearable and clustered by lateral capillary force, resulting in the formation electronic devices, while promising, typically involve use of the of bundles of close-packed nanowires with nearest neighbor nature of metal ductility, making them a fast and highly sensitive center-to-center spacing between nanowire tips ~400 nm platform for locomotion monitoring. Mechanical strain-induced (see Fig. 1a, Supplementary Note 2, Supplementary Figs. 6–9, and penetrating cracking, which refers to formation of cracks propa- Supplementary Movie 1 for details). As shown in the scanning gating perpendicularly to the strain and running throughout the electron microscopy (SEM) images of the surface morphology whole conducting metal film, however, causes low tolerable strains (Fig. 1b), native micrometer-sized voids between nanowire clus- (maximum detectable strain at which penetrating cracks form and ters and nanometer-sized voids among individual nanowires are disable the sensor) of these electronics and thus inherently limits randomly distributed over the entire nanostructured substrate. their application for monitoring full range of activities. For Finally, a 24-nm-thick Pt film was coated on this hierarchically example, numerous studies have shown that vigorous movements structured surface (see Fig. 1c and Supplementary Fig. 10). We (e.g., >30% uniaxial strain) can disable the Pt film-based wearable comment here that the Pt element was only deposited on the electronics1,14. Although past studies have investigated the process surface of the nanowire assemblies and would not penetrate into of crack initiation and penetration6,10,15–17, manipulation of crack the nano-voids between individual nanowires within the nano- retardation to impart the metal film-based wearable electronics wire clusters (see Supplementary Fig. 11). with ultrastretchability as well as high sensitivity has not yet been described. To address the aforementioned issue, we seek solutions in Geometric effect of stretched bioinspired nanowire assembly. nature with examples of structural materials and systems with The premise of our design is that the presence of hierarchical hierarchical design. One of the examples is a cochlea system of an assembly of nanowires has the potential to retard penetrating inner ear that uses acoustic-responsive hierarchical assemblies of cracking under large mechanical strains. We used SEM to image stereocilia at surfaces of tympanic membranes to efficiently the morphology of nanowires at different stages of stretching convert acoustic signals into electrochemical activities and reach a process. Inspection of Fig. 2a reveals that the hierarchical compromise between detection range and sensitivity18–22 (Sup- assembly of 4-μm-length nanowires exhibited a two-stage plementary Fig. 1 and Supplementary Note 1). Other hierarchical sequential cracking process starting from stretching at micro- designs have also inspired recent advances in soft electronics23–29 voids (MVs) followed by de-bonding of nanowires at nano-voids and materials30–34 with programmable shape transformation and (NVs). Eventually, a micro-sized crack developed within a single stretchability at a wide range of scales. nanowire cluster and led to two sub-clusters at a high strain. We Inspired by the hierarchical design methodology both in nature note here that we use the term ‘voids’ and ‘cracks’ to describe the and engineered systems, here we report a design that uses hier- gaps between nanowires before and after applying strain, archical assembly of interfacial nanowires to retard penetrating respectively (Supplementary Figs. 12 and 13). cracking and significantly increase the stretchability of metal film- To understand this observed phenomenon, we performed based sensors. Finite element simulations, characterization of the nonlinear simulations through the commercial finite-element morphologies of both structured and flat surfaces under different (FE) software ABAQUS. We selected a 2D FE model that is well strains coated by nanometer-thick metal films, and conductivity approximated to plane stress conditions (i.e., the film is loaded measurements, reveal that this improvement is attributed to a uniformly through the thickness considering the film width is two-stage crack-generation synergy. At low strain, crack genera- much larger than its thickness) and computationally efficient tion occurs along micrometer-sized voids between the nanowire enough to simulate the stretching process of the film. According clusters, and at high strain, subsequent crack initiation originates to the experimental observation, all our FE models were designed from nanometer-sized voids among the individual nanowires to consist of two nanowire clusters with nanowire lengths of 4 μm within the clusters. This process is similar to the central role of and cluster sizes of 8 μm (20 nanowires per cluster, and 450 nm stereocilia bundles in the cochlea system. This two-stage cracking center-to-center spacing between the base of the nanowires) on a process allows high stretchability (130% strain) and high sensi- 6-μm-thick rectangular PDMS substrate (see Fig. 2b, Supplemen- tivity (Gauge Factor of 107.45, minimum detection of 0.005% tary Note 3 and Supplementary Fig. 14 for details). We used strain) to be combined into a single sensor. Further, we illustrate cohesive elements in the FE model to assume the adhesive force the utility of this bioinspired approach by fabricating wearable between nanowires. Nanometer-sized Pt layers were excluded in electronics such as sound detectors and soft robotics actuation our model for simplicity. The PDMS substrate was subjected to monitors, which achieve high stretchability and retain high sen- horizontal extension at the both ends, and we terminated the sitivity compared to conventional metal film-based electronics. model when six sub-clusters formed at the surface. We notice here that our model captures the characteristic parabolic shape of the nanowires at the edge of the nanowire bundles. Results Figure 2c and Supplementary Movie 2 show the simulation Fabrication of the hierarchical nanowire assemblies. In our results of the stretching process in our FE model. For strains up to experiments, we fabricated structured surfaces consisting of 20%, the applied strain was mainly accommodated by increasing nanowire assemblies that mimic the stereocilia bundles in the the gaps between neighboring clusters (i.e., MVs), which is cochlea. First,
Details
-
File Typepdf
-
Upload Time-
-
Content LanguagesEnglish
-
Upload UserAnonymous/Not logged-in
-
File Pages8 Page
-
File Size-