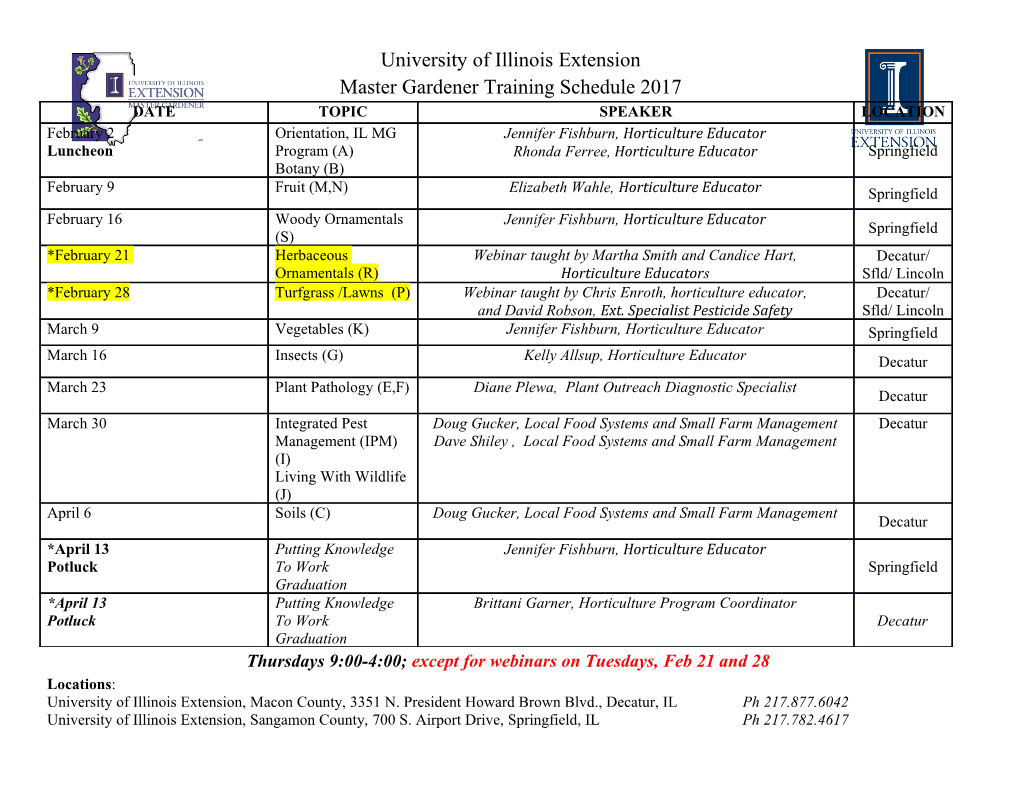
Differentiating Inclusions in Molten Aluminum Baths and in Castings Rafael Gallo Pyrotek Inc. OH, USA ABSTRACT It is well accepted that a variety of inclusions are present in liquid aluminum baths. Their source derives from the type of metal charge, alloying additions, melting practices, liquid metal treatments, and molten handling practices. The presence of unwanted second phase particles in solidified castings such as non-metallic inclusions or undesirable foreign material particles usually causes castings to be rejected. Successful elimination of inclusion related defects in castings requires proper collection and analysis of data. Finding the root cause of inclusions defects poses great complexity, because of the wide range of interdependent molten metal and casting process contributing factors. Having a notion of the level of molten cleanliness is just a part of a solution to eliminate inclusions related scrap in castings. Equally important parts of the solution are to establish a correlation between the inclusion defects seen in the castings with the inclusions present in the molten metal (molten cleanliness level), and to correlate in which part of the casting process the defect occurred. Without a proper correlation, it is very typical that the molten bath be incorrectly blamed for casting defects. Thus, the relevant questions that have to be answered at that time are: A) Are the inclusions from the molten bath the same as the inclusions seen in the casting? B) How does the casting defects correlate to the molten metal cleanliness? C) When was the manufacturing date, and how it correlated to casting process information? With present technologies commercially available for removing inclusions from the molten bath, a wide range of levels are achievable. Current analytical techniques for assessing the cleanliness of molten aluminum baths provide a foundry with practical information about the melting process. Metallurgical casting defect analysis by chemical analysis, microscopic examination, destructive testing, and non-destructive testing allow correct diagnosis on inclusion defects in a casting. The four objectives of this article are: 1) to improve the understanding of the difference between metal quality and molten cleanliness level, and their relationship with casting process and molten metal treatment variables, 2) to discuss recent technological advancements made in assessing inclusion levels in molten baths, 3) to present several examples of inclusions in molten metal, and in actual castings, and 4) to provide food for thought to value the benefits of using quantitative and qualitative inclusion data on molten metal and actual castings, to find the root cause of the scrap. Keywords: Inclusions, Oxides, Molten Cleanliness Assessment, Molten Quality, Casting Defects, Metallographic Analysis. 1 INTRODUCTION Molten Quality Hydrogen absorption, formation of oxide films, dross, metallic and non-metallic inclusions, and oxide build up are inherent characteristics when melting and handling molten aluminum, regardless of the melting and/or holding furnace design, or the energy used (gas or electricity). Therefore, it is critically important to understand and control such intrinsic characteristics, because they will greatly affect the overall quality of the molten bath, which in turn impacts the final casting quality with respect to porosity, shrinkage, oxides and inclusions. The level of quality of a molten aluminum bath is based on the degree to which the chemical and the physical properties are controlled to meet specific customer’s requirements. While the term chemical properties refers to the chemical element compositional levels, the physical properties imply hydrogen content, dissolved chemical impurities, and inclusions. For the majority of foundries, the concept of molten metal cleanliness is a segment of the overall melt quality of the bath. It takes into account the amount of “impurities” present in the molten bath before it is cast. The term “impurities” also implicate hydrogen gas, dissolved chemical impurities, and inclusions. To avoid misinterpretations and misunderstandings, the word “impurities” must not be confused with inclusions only. The molten metal cleanliness level is determined by the molten metal processing treatments performed to minimize, remove, and control hydrogen gas levels, the percentage of dissolved chemical impurities, and the amount of oxides and inclusions present in the molten bath before it is cast. Aluminum foundries could implement easier practical, feasible, and robust molten metal treatment and handling processes to minimize inclusion defects by advancing their comprehension on the molten cleanliness level being delivered by their melting department, and by better understanding how their casting technology influences the molten cleanliness level as the melt is poured. However, implementation of any given molten process would not be sufficient to guarantee success if intentional or unintentional changes in the melting and/or casting operations occur without revaluating the established process. Degassing Basics Typical foundry techniques for lowering the concentration of dissolved hydrogen to satisfactory low hydrogen content before casting include three different methods. The most popular method includes the use of graphite and/or ceramic components to inject a purging inert or reactive gas or a combination of them via lances, porous plugs, rotary impellers and molten metal pumps. The most effective and efficient techniques to degas are via rotary impellers and/or molten metal pumps. While rotary impeller degassing is the most popular technique being used by high-pressure die casting, low pressure, permanent mold, green sand, and dry sand foundries, molten metal pump degassing is the preferred method being used by aluminum smelters. Depending of the particular rotating impeller used by each technique, the introduced purging gas could be sheared into a variety of fine bubbles and distributed at different rates and uniformity patterns throughout the molten bath. Foundries need to take into account that a degassing operation not only reduce the hydrogen content in the melt, but also that a robust degassing process will greatly impact the flotation of inclusions, and in addition, if a rotary degassing process is properly combined with flux injection, the molten cleanliness will improve further as a result of more inclusions removal. Alkali Elements Although alkali elements are part of the chemical composition, usually they are referred as chemical impurities. Because of the deleterious effects that they could cause, they have to be controlled to very low levels. Due to the difficulty in separating these impurities, they are best handled by a policy of avoidance (i.e., foundry having and adhering to a well –defined incoming material specification sheet with respect to elements and levels accepted). Nevertheless, there are generic treatments that can be employed to deal effectively with potential contamination by each element. Inclusions in Molten Aluminum It has already been established in the technical literature that a variety of inclusions exists in molten aluminum alloys. Their source derives from the type of metal charge, alloying additions, melting practices, and liquid metal treatments and handling practices. Inclusions can be broadly classified as intermetallic and non-metallic. Intermetallic inclusions are primary compounds that result as a consequence of the precipitation, and growth phenomena from the liquid state. However, not all of them are necessarily detrimental to the quality of the molten bath. While presence of TiB2, and AlB2 for grain refining in hypoeutectic alloys, and AlP for silicon modification hypereutectic alloys are not detrimental, TiAl3 particles in excess of 10µm can cause inclusion related defects. In addition, sludge formation (Cr-Fe-Mn) is also detrimental. Non-metallic inclusions can be present in the form of films, fragments, particles, and clusters. The inclusions can have different composition, texture, morphology, and appearance. Common types of non-metallic inclusions are: borides, carbides, nitrides, oxides, and salts. While the existing types of inclusions that would be present at the different molten stages will vary from foundry to foundry, their removal is essential for proper molten metal cleanliness. A number of commercially accepted melt treatment techniques are being used to remove and separate inclusions from the molten aluminum alloy prior to casting. These include various different methods of fluxing, degassing, and filtration in the furnaces and in the gating system. Any of these techniques will have an impact on the melt cleanliness of the molten aluminum alloy. However, the effectiveness to evaluate their removal would rely on the melt cleanliness measurement technique being used. Ideally, the optimum technique would provide assessment of three inclusions parameters: size, distribution, and composition. Inclusions in Castings Early in the casting process, foundries may scrap castings due to inclusions (foreign particles) when they are relatively easily seen by the naked eye during visual inspection on the as-cast condition. As the castings flow upstream in the process, inclusions could be detected during radiographic and/or fluorescent penetrant inspection. The next operation at which the majority of inclusions are detected is after the machining operation. It is not uncommon to find out that more than 50% of the inclusion
Details
-
File Typepdf
-
Upload Time-
-
Content LanguagesEnglish
-
Upload UserAnonymous/Not logged-in
-
File Pages22 Page
-
File Size-