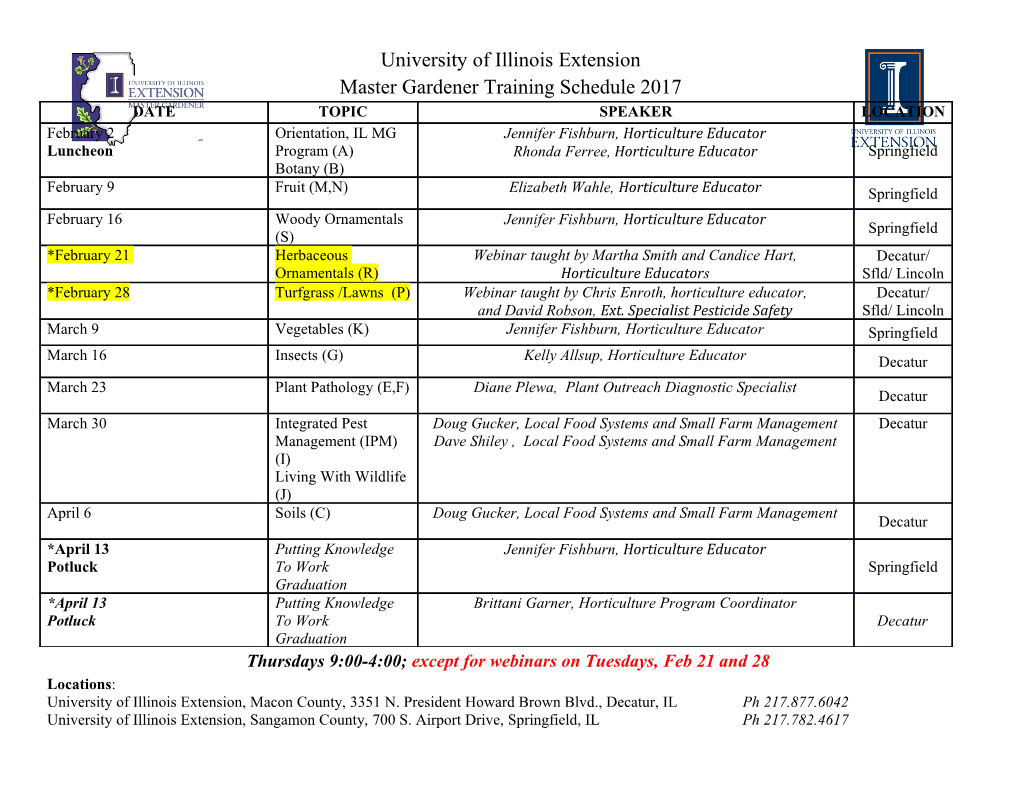
PCDD/F EMISSION FROM LEBLANC SODA FACTORIES IN GREAT BRITAIN, FRANCE AND GERMANY DURING THE 18th TO EARLY 20th CENTURY Balzer Wolfgang1, Gaus Martin1, Gaus Caroline2, Urban Ulrich3, Weber Roland4 1CDM Consult GmbH, Neue Bergstraße 9-13, 64665 Alsbach-Hähnlein, Germany 2National Research Center for Environmental Toxicology, University of Queensland, Brisbane 4108, Australia 3HIM GmbH, Waldstraße 11, 64584 Biebesheim, Germany 4POPs Environmental Consulting, Ulmenstrasse 3, 73035 Göppingen, Germany Introduction It has only recently been recognised that high concentrations of dioxins can be formed under the Leblanc Soda and associated processes1,2. The Leblanc process can be considered the birth of the chemical industry in the late 3-7 th 1700s and was used extensively untill the early 20 century to produce sal soda/sodium carbonate (Na2CO3) from sodium chloride (NaCl) as basic reagent for the soap, glass and textile industry. The HCl generated caused heavy environmental damages and was partly recycled to produce chlorine/calcium hypochlorite (bleaching powder). In the late 1980s, high levels of arsenic and lead were detected in soil from Lampertheim, Germany (approximately 60 km south of Frankfurt/Main)1 during the construction of a child care facility and playground. Subsequent investigations in the 1990s also revealed highly elevated PCDD/F levels in soil from the same estate, which was used as a residential area. Based on these findings, the German State Hessen commissioned investigations into the history of the estate, and extensive soil and groundwater analyses. These investigations demonstrated that the contamination originated from a Leblanc factory which operated from 1828 to 1927 on the estate1. The total dioxin formation (particularly PCDFs) during this operation amounted to 1-10 kg TEQ1. The facility ceased production in 1927/28, after which it was demolished and partially levelled. From the 1950s onwards, the area was opened for residential housing development and approximately 600 people live within 125 blocks on this estate today. Since the discovery of high contamination levels in residential soil, extensive securing and remediation measures are ongoing and are expected to be finalized in 20101. With the Leblanc process representing an important production process during the industrial revolution, the findings from Lampertheim suggest that other similar contaminated sites exist elsewhere. Since the Leblanc sal soda production had not previously been identified as a potential PCDD/F emission source, the associated operational settings and processes resulting in PCDD/F formation and emissions were unknown. This paper presents information from historic investigations into the development and former operations of the Leblanc factory in Lampertheim and other similar operations in Germany, France and Great Britain. Further, the PCDD/F formation potential during the different operational steps of the Leblanc factory were evaluated. These two aspects provide an important basis for identifying contaminated sites and assessing the contemporary relevance of this historical dioxin source. Materials and Methods Historical investigations were carried out by extensive searches of archives as well as the scientific literature. Based on these investigations, detailed analyses of surface and subsurface soil as well as production residues from the residential estate and nearby former landfill of the factory in Lampertheim were undertaken during 1994 to 1999. More than 600 soil cores of a total length of 3 km were taken on and near the estate and more than 3,500 soil analyses were carried out for a range of organic and inorganic1 contaminants. Selected samples (approx. 500) were also analysed for PCDD/PCDF according EN 1948 by commercial laboratories. Results and Discussion Analyses of soil from the Lampertheim estate confirmed that the entire surface and subsurface soil, in some locations up to a depth of approximately 8 meters, was highly contaminated with PCDD/Fs, heavy metals and arsenic, the latter in bioavailable form1. Since a range of chemical processes are employed in a Leblanc factory, the individual steps and processes were evaluated with respect to their PCDD/F formation potential. Four distinct Leblanc operational steps could be identified that have a high potential to result in PCDD/F formation and were further evaluated: Organohalogen Compounds, Volume 70 (2008) page 000809 1) The production of sodium sulphate and sal soda within ”sulphate ovens” and flame ovens3: A main part of all Leblanc processes is the production of sodium sulphate (Na2SO4) and HCl from sodium chloride (NaCl) and sulphuric acid (H2SO4). In the first step of this production process, NaCl reacts with H2SO4 in iron pans at 200 °C (“sulphate ovens”). This results in the release of approximately two thirds of the added chloride, mainly as HCl3. The sulphate ovens were impregnated with coal tar to protect from HCl3 corrosion, providing the most basic conditions known to result in PCDD/F formation (i.e. chlorine, coal tar and heat). In a second step, the remaining NaCl was converted to Na2SO4 in flame ovens operating at 600 °C. The surfaces of 3 the ovens were frequently cleaned from deposits. The Na2SO4 were converted with coal and calcium carbonate 3 to NaCO3 in soda ovens at 900 °C . Residues from these processes were contaminated with up to 95 ng TEQ/kg. 2) The processes used for condensation and purification of hydrochloric acid3 In the Lampertheim factory the hydrochloric acid produced in the above step was condensed in coke towers for further processing. In these towers, mineral oil in counter flow, was used to remove arsenic. The pipes and condensation chambers leading from the sulphate and flame ovens to the coke towers were mainly constructed of clay soaked with coal tar. The temperature in the off-gases was 160 °C from the sulphate ovens and 360 °C from the flame ovens. The cooled gases were adsorbed in a concurrent water flow to produce HCl and for the further production of chlorine. Conditions favouring PCDD/F formation during the condensation and purification of HCl are confirmed by PCDD/F contamination in soil where the piping system and the coke towers were formerly located. PCDD/F concentrations in these soils were above the German soil guidelines for industrial sites (>10,000 ng TEQ/kg). 3) The production of chlorine A) Manganese oxide based processes Before the chloro alkali processes was invented I) Direct oxidation around 18902, chlorine was produced via MnO2 + 4 HCl → MnCl2 + Cl2 + 2H2O manganese oxide by direct or indirect oxidation II) Indirect oxidation of HCl (Figure 2). In 1868, Deacon invented the MnO2 + 2 NaCl + 2 H2SO4 → MnSO4 + NaSO4 + Cl2 +2H2O oxidation of HCl using CuCl catalysts as an (Walter Weldon improved 1870 the manganese process by 2 recycling of the MnCl via air oxidation in alkaline solution) alternative process. In Lampertheim, the direct 2 B) Deacon process manganese oxide method was used for chlorine 4HCl + O → 2Cl + 2H O (400 – 450 ºC; CuCl2 catalyst) production from HCl. Neither the Deacon 2 2 2 Figure 1: Chlorine production processes used before the process nor a chloro alkali was operated on the invention of the chloro alkali process site. For this manganese oxide method, the chlorine cells were built from sand stone. 0,4 Chloralkali Coal tar was used as filler material (approx. 2 cm) between the stones3. Additionally, the Soil near Sulphate Oven 0,3 stones were soaked with coal tar for Residue near Chlorine 3 protection of corrosion . It is obvious that Prod. (MnO-process) this process had a high potential for 0,2 PCDD/F and other Cl-PAH formation from coal tar and elemental chlorine. This process reached temperatures of up to 90 °C with a 0,1 residence time of 12 hours.3 These conditions are similar to those employed by the chloro alkali electrolysis using coal tar 0 D D D D F F F DD D D D DD DF DF DF DF containing graphite electrodes. In C CD C CD CD CDF C C C C CD 2,3,7,8-Congener Distribution Distribution (mass) 2,3,7,8-Congener T eC x xC xC p T e e x O - OCDD P P H ,8 -P -H H H -H ,8- - - - -Hx -Hp -Hp Lampertheim, the vicinity of the area where 7 8 8- 9- 8 7 ,8 ,9 ,8-HxCDF8 ,9 , , , , , , 7, ,3 ,7,8 ,8 ,7 ,7,8 ,7 ,8 7 , ,8 2 ,3,7 4 ,6,7 ,7 ,6 2,3 3 ,6 ,7 ,6, ,6 ,7 the chlorine/chlorinated chalk were formerly ,2 ,3, 3 ,3 ,4 ,2, ,3 1 ,2, ,2 ,3 1 2,3,4,7,8 ,2 ,2,3 ,3,4 ,3,4 ,3,4 1,2 1 1 ,2 1,2,3,4,7,8-HxCDF1 1 2 2 ,2 produced, high contaminated residues with 1 1, 1 TEQ levels above 200,000 ng TEQ/kg were Figure 2: 2,3,7.8-congener pattern of soil near former sulphate ovens found. The PCDD/F pattern of these and residues near former chlorine production (manganese method) residues are similar to those characteristic of compared to chloro alkali electrolysis. the chloro alkali process. Organohalogen Compounds, Volume 70 (2008) page 000810 4) The production of calcium hypochlorite (bleaching powder) Calcium hypochlorite was produced from Ca(OH)2 and elemental chlorine in chlorine chambers. For this, wood, stone or lead/iron chambers were commonly used. The wood and stone chambers were completely covered with coal tar. After distributing the Ca(OH)2 on the floor of these chambers (75-100 mm), they were filled with chlorine for a reaction time of approximately 24 hours under an average operating temperature between 55-90 °C and peak temperatures of up to 120°C3. Based on this, this process can be considered having optimized conditions for PCDD/F formation when coal tar was used as insulation material.
Details
-
File Typepdf
-
Upload Time-
-
Content LanguagesEnglish
-
Upload UserAnonymous/Not logged-in
-
File Pages4 Page
-
File Size-