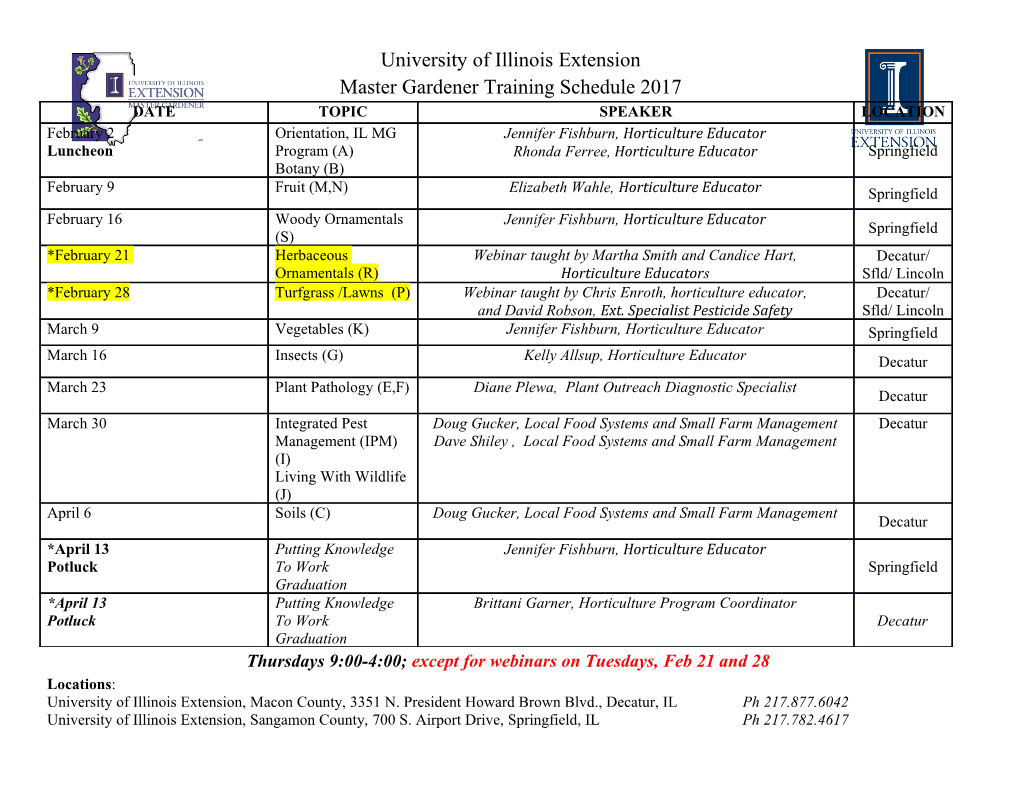
ReplacingReplacing 1,1,1-Trichloroethane1,1,1-Trichloroethane WithWith OtherOther ChlorinatedChlorinated SolventsSolvents By Vicki L. Rupp & Janet C. Hickman Cleaning and degreasing metal production stage. The process is cost- scheduled for phaseout, and are not parts before plating or coating is an effective and energy-efficient, and has subject to the excise taxes levied on important step in the manufactur- a small floor-space requirement. In ODSs. Despite their similarity to ing process. For a large percentage addition, the solvent has excellent TCA, these alternate solvents also of companies, and for a long time, cleaning capacity for greases and oils, have certain characteristics of their this has meant vapor degreasing and is not likely to cause rust damage. own that make them particularly with 1,1,1-trichloroethane (TCA, It has low toxicity, a high permissible suitable for specific types of also known as methyl chloroform or exposure level (PEL), is not flam- degreasing. MCF). Times are changing, how- mable under most conditions, and is ever. Production of TCA for listed as a non-volatile organic Methylene Chloride (MEC) emissive applications, such as compound (VOC). Consequently, for MEC (also called dichloromethane degreasing, ceases in all developed a number of years TCA had virtually and methylene dichloride) is a countries as of the last day of 1995, replaced most other solvents for the powerful and versatile chlorinated leaving many manufacturers in a vapor degreasing process, as well as solvent known for its high solvency quandary. Until recently, the Dow for cold cleaning and electronic capabilities. It has a mild ethereal Chemical Company, Midland, MI, cleaning. odor and is completely miscible with was the only U.S. chemical pro- Under the U.S. Clean Air Act a variety of solvents. ducer to manufacture a complete Amendments of 1990, however, as A clear, heavy liquid (10.98 lb/gal), line of chlorinated solvents, includ- well as the international Montreal MEC has the lowest boiling point ing TCA and carbon tetrachloride, Protocol, TCA was classified as an (103.5 °F; 39.8 °C), the lightest vapor which have been implicated in the ozone-depleting substance (ODS) and density (2.93 times that of air), and depletion of the stratospheric ozone is scheduled for production phaseout the highest solvent power of the layer. As of April 1994, the company for all emissive applications by chlorinated alternatives. It freezes at discontinued the production of December 31, 1995. In view of this -139 °F (-95 °C). TCA. Dow and other suppliers requirement, many users of the With its low boiling point and high continue to actively pursue answers solvent have been converting to solvent power, MEC is well suited for to the solvent alternatives problem. substitutes or alternatives. cleaning temperature-sensitive parts, such as thermal switches and ther- lthough recycled TCA and The Search for Alternatives mometers, and for removing tough TCA from inventories will Unfortunately, good alternatives are paint residues, hard-to-dissolve resins, A still be available after hard to find. Those based on a and gross metal fines. It can be also January 1, 1996—and although different, non-chlorinated chemistry used effectively on white metals manufacturers in developing coun- often require considerable testing, (aluminum and zinc). In vapor tries are permitted an extension of plus costly re-engineering. Although degreasing, its low boiling point and several years on the phaseout—the there are no exact “drop-in replace- ability to dry quickly have permitted great majority of users are actively ments,” the closest alternatives are the high throughput at an acceptable cost. seeking a replacement for the solvent. other three readily available chlori- On the other hand, the high Fortunately, the Significant New nated solvents—methylene chloride solvency of MEC may be too aggres- Alternatives Program (SNAP), (MEC), perchloroethylene (perc or sive for some substrates, such as published by the U.S. Environmental PCE) and trichloroethylene (TCE). plastics and rubber. Further, because it Protection Agency (EPA) in March These three solvents share most of passes rapidly into the vapor phase, it 1994, has brought a long-needed the advantages of TCA, such as: is difficult to contain the vapor. When solution to the problem: Maintain the converting a degreasing system from vapor degreasing process while • Excellent solvency TCA to MEC, chillers are required to replacing TCA with one of the other • Virtually non-flammable contain the vapors, and a lip-vent chlorinated solvents. • Low toxicity when used in exhaust or vapor-removal device may accordance with established be necessary. The heat input should be TCA—Formerly safety procedures. reduced and carefully controlled to The Solvent of Choice prevent too much agitation in the The benefits of degreasing with TCA In addition, these solvents have not boiling solvent. The engineer in are well known. Parts leave the been implicated as sources of strato- charge of surface cleaning should degreaser dry and ready for the next spheric ozone depletion, are not determine whether tighter equipment 34 PLATING & SURFACE FINISHING is required, or whether a retrofit is Table 1 needed to minimize emissions. OSHA Permissible Exposure Limits (PELs) Perchloroethylene (PCE) Solvent 8-hr time-weighted Short-term exposure PCE or perc (also known as average (TWA)—ppm (STEL)—ppm tetrachloroethylene) is a clear, colorless liquid with a distinctive, Methylene Acceptable ceiling somewhat ether-like odor. Physical chloride 500* concentration: 1000 properties of PCE include: Maximum acceptable peak: 2000* • Boiling point: 250 °F (121.1 °C) Perchloro- 25** — • Freezing point: -9 °F (-22.8 °C) ethylene • Vapor density: 5.76 times that of air Trichloro- 50** 200** • Weight: 13.47 lb/gal ethylene 1,1,1-trichloro- 350 450 With the highest boiling point of ethane the chlorinated solvents, PCE is excellent for removing heavy grease *Currently under rulemaking to lower the PEL; 25 ppm has been proposed on an 8-hr and high-melt waxes. It also easily TWA, with a STEL of 125 ppm. removes moisture from wetted parts. **These limits in OSHA’s 1989 rule have been overturned. With its high solvent power, it provides extensive cleaning action. Table 2 PCE is recyclable and can be ACGIH Threshold Limit Values readily recovered by carbon adsorp- tion methods. It can also tolerate Solvent 8-hr time-weighted Short-term exposure relatively large quantities of water average (TWA)—ppm (STEL)—ppm without degrading. Because it vaporizes at a higher temperature than Methylene 50 — the other chlorinated solvents, chloride however, higher utility costs are Perchloro- 25 100 required for heating the solvent to ethylene vapor level and for cooling chill water Trichloro- 50 100 above the vapor level in the degreaser. ethylene In addition, when cleaned parts are 1,1,1-trichloro- 350 450 removed from the degreaser, they ethane must be allowed to cool before they can be handled. Trichloroethylene (TCE) Because of its excellent cleaning well-documented exposure guidelines TCE is a clear, heavy liquid (12.11 lb/ properties and high solvency, TCE has and safe handling procedures. gal) with excellent solvency. Non- been considered the universal vapor- Exposure to vapor concentrations corrosive and easily recycled, TCE degreaser solvent. It is commonly within recommended guideline levels boils at 189 °F (87 °C) and freezes at used in vapor degreasers, is recy- will not result in any known adverse -124 °F (-86.7 °C). The high density clable, dries quickly and has low effects on most people. Acute over- of TCE’s vapor (4.53 times that of air) energy requirements. exposure to vapors, however, may assures low vapor loss and easy Conversion from TCA to TCE is cause anesthetic or narcotic effects recovery from vapor degreasing fairly straightforward. Heat in the (known as solvent drunkenness), systems. Carbon adsorption recovery is degreaser should be increased to 15 lb central nervous system effects, and often used with TCE to trap emissions. of steam, or equivalent electric or gas liver and/or kidney problems. Because At one time, TCE had been the heat input, and all possible methods chlorinated solvent vapors are heavier preferred solvent in the metal finish- of emission reduction should be used than air, very high concentrations can ing industry, but numerous state and to meet the lower PEL. Regular vapor accumulate in poorly ventilated areas. local environmental regulations now monitoring is suggested to help keep Exposure to such concentrations can classify it as a VOC. As a result, it the workplace within Occupational cause dizziness, unconsciousness, and had been widely replaced with 1,1,1- Safety and Health Administration even death. trichloroethane, although TCE (OSHA) limits. Small amounts of chlorinated remained in use for specialty applica- solvents that might be ingested tions, such as stripping semi-cured Health Profile inadvertently are not likely to cause varnish or paint films and removing One major benefit of chlorinated injury. Ingestion of larger amounts, heavy rosins and buffing compounds. solvents is the extensive study that however—accidentally or intention- With the phaseout of TCA, however, has been done on their safety and ally—could result in serious injury or and the impetus of EPA’s SNAP health effects. Extensive laboratory death. Occasional, brief skin contact ruling, trichloroethylene is making a and epidemiological studies have with chlorinated solvents is not likely comeback. been made, and these have resulted in to produce any significant adverse December 1995 35 effects, nor is a single, prolonged 1989, OSHA proposed a downward EPA’s SNAP Rule exposure likely to result in absorption revision of the workplace PELs for a EPA’s new SNAP rule gives industry of harmful amounts through the skin. number of substances, including the official go-ahead to consider The solvents can de-fat the skin, perchloroethylene and trichloro- MEC, PCE and TCE as acceptable however, which can cause dermatitis ethylene.
Details
-
File Typepdf
-
Upload Time-
-
Content LanguagesEnglish
-
Upload UserAnonymous/Not logged-in
-
File Pages5 Page
-
File Size-