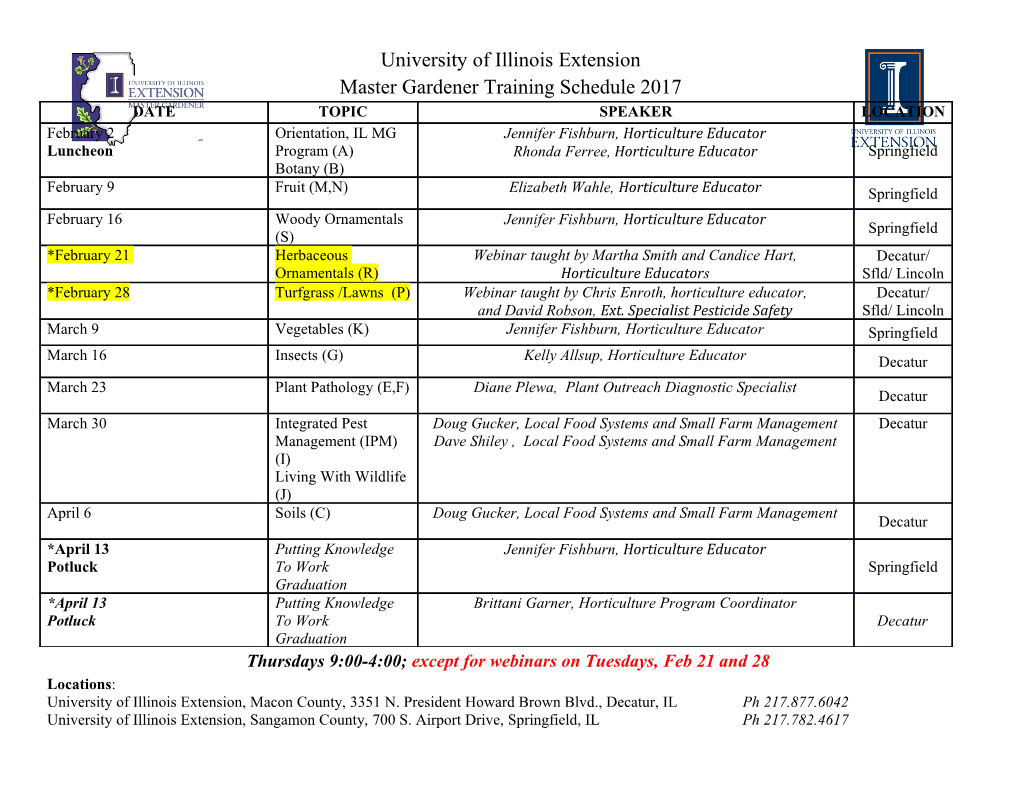
INDEX Introduction 1 In Pursuit of an Ideal Smelter 3 Basic Concept of the Mitsubishi Process 5 Advantages of the Mitsubishi Process 7 Environment /Recycling 9 Cost Competitiveness 11 Process Reliability and Control 13 Typical Plant Layout and Design Parameters 15 Mitsubishi Process Smelters in Operation around the World 17 Naoshima 19 Kidd Creek 21 Onsan 23 Gresik 25 Port Kembla 27 Company Profile 29 Available Services 30 Our atmosphere, the air we breathe, is common to all of Earth's inhabitants. Our planet provides The "Mitsubishi Continuous Smelting and Converting Process" which we have evolved from years us with abundant natural resources........clear waters........bountiful seas........fertile lands........ and of research and production experience, is the world's only commercially proven pyro-metallurgical verdant forests. All must be carefully nurtured, widely enjoyed, understood, appreciated, and most process to produce blister copper continuously from concentrates. important of all, must be protected and sustained for the benefit of future generations. Since the inception of the Mitsubishi Process, we have constantly challenged our own technology, striving to It is "THE PROCESS" for the 21st Century. make it more efficient, and ever friendlier to the environment. The Mitsubishi Process ensures environmental protection of the surrounding community, clean and safe workplace conditions, and the highest copper, gold, silver and sulfur recoveries in the copper industry. Its operating costs are low and the cost of plant construction is keenly competitive. These are but a few of the many technological aspects, which we will cover more fully in the following pages. 1 2 IN PURSUIT OF AN IDEAL SMELTER Aerial view of Naoshima smelter and refinery The Mitsubishi Process: from furnaces and ladles. Thus the Mitsubishi furnace Half a century of development A step ahead of the rest arrangement consists of three stationary furnaces, 1959 Testing of injection feeding began, one of the 1991 New larger Mitsubishi Process line with production Copper has been recognized as a valuable resource connected by enclosed launders, continuously cornerstones of the Mitsubishi Process. capacity of 200,000 MTPY started operating in since ancient times. Mitsubishi Materials has sought to producing blister copper from concentrates. 1970 Successful completion of continuous smelting and Naoshima, replacing operations using the reverberatory optimize the smelting of this valuable resource for many Furnace charging and tapping are eliminated, so no converting pilot plant testing. furnace + P.S. converters and the original Mitsubishi years. We believe the ideal smelter should be environ- ladles and cranes are required, and there are no 1974 First commercial scale Mitsubishi Process plant with Process line. mentally friendly, highly efficient, and inexpensive to fugitive emissions. These are the basic reasons why 48,000 MTPY production capacity, commenced opera- 1998 New Mitsubishi Process smelter started at Onsan, tions in Naoshima. Korea, with production capacity of 160,000 MTPY. build and operate. Our Mitsubishi Process attains all of the Mitsubishi Process is so clean to operate, and why it 1981 Second commercial scale Mitsubishi Process plant with 1998 New greenfield Mitsubishi Process smelter started at the above goals. has such an unique structure. As demonstrated daily by 60,000 MTPY production capacity, commenced opera- Gresik in Indonesia, with production capacity of 200,000 our family of smelters at Naoshima, Kidd Creek, Onsan, tions at Kidd Creek Smelter in Canada. MTPY. and Gresik, the use of the Mitsubishi Process has Unique structure that stresses 1982 Production capacity was doubled at Naoshima to 2000 The first stand alone Mitsubishi C-furnace started environmental friendliness elevated their copper smelting to "clean industry" status. 96,000 MTPY. operating at Port Kembla Copper, in Australia in place of From the start of its development, the Mitsubishi An important and lasting advantage in complying with 1988 Production capacity at Kidd Creek doubled to 125,000 previously used P.S. converters. Process has aimed at eliminating fugitive emissions more stringent environmental regulations in the future. MTPY. 2000 Naoshima's production capacity increased to 270,000 MTPY of anodes from new source. 2001 Naoshima Smelter accredited with ISO 14001. 3 4 As mentioned previously, the Mitsubishi Process con- 150 to 200 m/s. The concentrates are bath-smelted two pairs of three. Here the mixed matte and fayalite researched, and pioneered the use of limestone for the sists of three stationary furnaces in cascade, connected instantly, producing a high grade matte of around 68% slag (2FeO・SiO2) separate by difference in specific continuous conversion of matte to blister. This lime- by launders. By adopting this multi-furnace system, copper and silicate slag. The use of top blowing lances gravity. The lighter slag contains about 0.6% copper, ferrite slag (Cu2O-CaO-Fe3O4) has a lower viscosity and smelting, slag cleaning, and converting operations can ensures that the melt is always well mixed and makes and continuously overflows from the CL-furnace into a a much higher solubility for magnetite than silicate type be carried out continuously under "ideal conditions" for the Mitsubishi S-furnace one of the most efficient and fast flowing flume of water where it is instantly granulated, slags. The choice of limestone as the C-furnace flux efficient copper recovery and removal of impurities. compact copper smelting units in the world. It also and can then be either sold or discarded without any was one of the key factors in the successful develop- Furthermore, the adoption of top blowing lances, and a ensures very high capture of the feed solids, with less additional treatment. Meanwhile the heavier matte sinks ment of the Mitsubishi Process, still the only technology special type of slag for the C-furnace are integral items than 3% solids (plus volatiles) carried over with the to the bottom of the furnace and siphons continuously to embody continuous converting. The relatively small S-furnace C-furnace Lance blowing air Flux & Concs, (50-60% O2) coolant coal, flux & Lance blowing air C-slag (30-35% O 2 ) Scrap copper Offgas Lance Anode scrap Slag & matte Electrode Offgas Lance Matte Blister copper S-furnace CL-furnace CL-furnace C-furnace Anode copper Anode Anode casting Anode furnace C-slag recyled to Discard slag Anode casting wheel S-furnce S-furnace lances that make continuous operations possible. furnace offgases into the from the bottom of the furnace to a covered launder, tonnage of converter slag (carrying about 14% copper) The following section describes the Mitsubishi waste heat boiler. The main flowing continuously into the C-furnace. overflows the C-furnace, and is water granulated, dried Process in more detail. heat source for smelting comes from the oxidization of and recycled to the S-furnace. Blister with about 0.6 to iron and sulfur in concentrate, and the balance made up C-furnace 0.7% sulfur siphons up out of the furnace, and is S-furnace by coal. The matte and slag formed continuously The Converting furnace (C-furnace) removes the continuously delivered to the anode furnaces for pyro- Dried concentrates (containing roughly 30% copper, overflows together from the S-furnace, down an remaining iron and sulfur from the copper matte, refining to anode copper. Anodes for the tankhouse can 25% iron, and 30% sulfur, and moisture content about enclosed launder into the CL-furnace. producing "blister" copper (about 98.5% Cu). The C- be cast in moulds mounted on a large diameter wheel, 0.5%), are mixed with coal, silica sand and recycled furnace is similar to the S-furnace, but smaller in or through a Hazelett Twin-Belt caster and Mannesmann CL-furnace converter slag. The mixed feed is injected into the diameter, and uses identical vertical blowing lances to "flying" shear. Smelting furnace (S-furnace) through vertical lances, The slag cleaning furnace (CL-furnace) is a quiescent inject limestone flux, coolant, and oxygen enriched air. together with oxygen enriched air, at a velocity between electric furnace powered by 6 electrodes arranged in Over 30 years ago, Mitsubishi carefully selected, 5 6 Today, Pierce-Smith converters (P.S. remelting of anode scrap and purchased copper converters) coupled with various types of scrap, while avoiding the associated fugitive smelting units, are used in most of the emissions of traditional reactors like P.S. converters. world's smelters. However, due to "batch" processing and problems associated with Steady state operation fugitive emissions during the transfer of melt "Steady State" furnace operation at constant and blowing stages, this arrangement will not bathline contributes to furnace integrity and be acceptable in the future. simplifies refractory design. Since the bathline is constant, protection is only required for a small area Modern day alternatives include the to counter the "wave" motion of the melt. In Mitsubishi Process, Outokumpu Flash contrast, all tapped furnaces require protection over Smelting and Flash a much wider area, since the Converting Process, the bathline changes during opera- Noranda Process, and tions. Our C-furnace bathline, the Ausmelt Process. will now give 3 or 4 years Only the Mitsubishi operation between bathline Process is a "truly con- repairs, due to advances in tinuous" smelting and furnace design and refractory converting operation cooling. producing a constant
Details
-
File Typepdf
-
Upload Time-
-
Content LanguagesEnglish
-
Upload UserAnonymous/Not logged-in
-
File Pages16 Page
-
File Size-