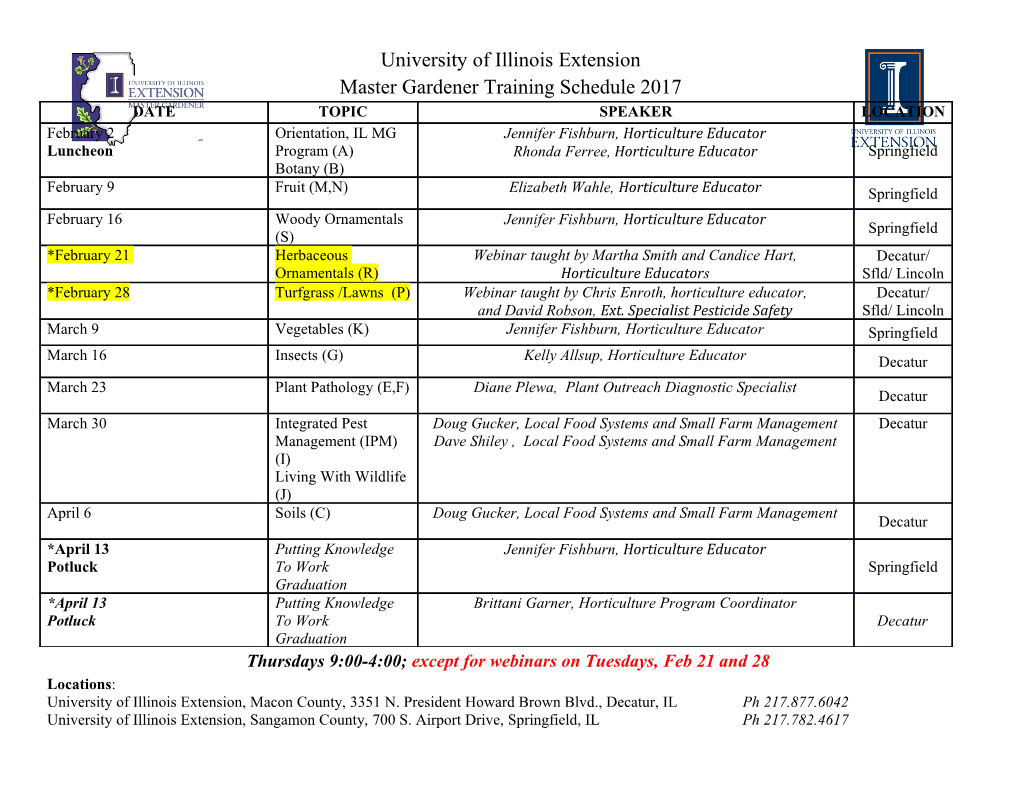
,.-­ I LJ1S'3~ jI'~~~~ A_5J_n ____~ ____________ /?(.. /I/#r I IV c:2 () (jJ IU/!II/~)/ {?p 5 r ~oo~ tJ ~y 6>] r AIAA 2000-1044 Parametric Model of an Aerospike Rocket Engine J. J. Korte NASA Langley Research Center Hampton, Virginia 38th Aerospace Sciences Meeting & Exhibit 10-13 January 2000 / Reno, NV For permission to copy or republish, contact the American Institute of Aeronautics and Astronautics 1801 Alexander Bell Drive, Suite 500, Reston, VA 20191 AIAA-2000-1044 PARAMETRIC MODEL OF AN AEROSPIKE ROCKET ENGINE J. 1. Korte* NASA Langley Research Center, Hampton, Virginia 23681 Abstract x ................. ... ....... .......... ... ..... ..... axial direction y .... .. ... .. .............. .................. .. .. normal direction A suite of computer codes was assembled to simulate the performance of an aerospike engine and to generate the engine input for the Program to Optimize Simulated Introduction Trajectories. First an engi ne simulator module was Launch vehicle performance is evaluated by developed that predicts the aerospike engine performance computing the optimum vehicle trajectory. One part of for a given mixture ratio, power level, thrust vectoring the essenti al data for an accurate trajectory simulation is level, and altitude. This module was then used to rapidly the engine performance (Fig. 1). generate the aero spike engine performance tables for axial thrust, normal thrust, pitching moment, and specific Mixture Rato Engine Design thrust. Parametric engine geometry was defined for use Power Level with the engine simulator module. The parametric model Altitude was also integrated into the iSIGHTt multidisciplinary Thrust Vectoring framework so that alternate designs could be determined. The computer codes were used to support in-house conceptual studies of re usable launch vehicle designs. Nomenclature Thrust Components Pitching Moment A ......... .... ... .. ... ... ........ ...... .. ... cross-sectional area a .............. .. ................... ... ..... constant in Eg. (7) Specific Thrust AR ....... .... ... .. ... ........ ... ........... ..... .. .. ... area ratio b ......... ............ .. ... .......... ........ constant in Eg. (7) E ............ .... .. ..... ....... ... ......... ................ energy F ....... ............................................ ..... .... force h .............. .. .. ... .. ..... ..... ...... .. .... ...... ... enthalpy M .... .............. ......... ... .... ... .... ........ Mach number rh .. .. ... .. .... .. .......... ... ........ ... ... .. ....... .. mass flow MR ......... .. ... .... .......... ...... .............. mixture ratio p ........... ........... .. .. .. .. .. ........... ............ pressure PL .... .......... .. ............... .... ......... ...... power level T ... .................. .......... ..................... temperature x ............... .... ..... ............... .. .. .... axial coordinate y ................. .. ....................... ... normal coordinate r ... .... ........ ..... ... .. .. ........ ... ... ratio of specific heats c.. .. ................ ..... .... ....... ........... constant in Eg(6) Fig. 1 Engine data needed for vehicle trajectory 7J ....••.• .....•.........•...•. .. •... ................... efficiency simulation. e .... ........... .. .. .. .......... ........... .... thruster ti lt angle Lockheed Martin'st reusable launch vehicle concept, the p .......... .. .......... ........... ... ... .......... ........ density VentureStar™,I .2 proposes to use an aerospike rocket subscripts engine. The aerospike engine performance is b . .............. ... ..... .... ... ... ........ ..... .... ... .. ...... base signjficantl y more compli cated than a traditional bell c ..... ...... ............ , .... ....................... , .. combustor nozzle rocket engine3 si nce the proposed aerospike cowl .... ............. ........ .. .. ... ....... .. .. .. ... ....... cowl engine has variable mixture ratio and power levels, is f ......... ....... .. ................. .......... ... ..... ... fuel (H2) capable of thrust vectoring, and has a complex flow g ... ... ..... ..... ... .... ..... ....... ... ... ... .. .. .. gas generator o .... ... .. ................... ........... ....... .. oxidizer (02) structure that affects the performance of the engine as the t ... .. .. ... .. .. .. .. .. ......................... ....... ...... turbine vehicle ascends through the atmosphere. T ................. .. ........ ........ ...... ...... .............. total The aerospike rocket engine consists of a gas thr ........... ............. ... .. .... .... .. ...... ....... ... thruster generator, turbopumps, combustor, rocket thruster, w .... ........ ... .. ......... ... ...... .. ....... ............... wall cowl, aerospike nozzle, and plug base region (Fig. 2) . ' Senior Research Engineer, Multidi sciplinary Optimization Branch, Mail Stop 159, Senior Member AIAA. tTbe use of trademarks or names of manufacturers in this report is for accurate reporting and does not constitute an official endorsement, either expressed or implied, of such products or manufacturers by the National Aeronautics and Space Administration. Copyright © 2000 by the American institute of Aeronautics and Astronautics, Inc. No copyri ght is asserted in the United States under Title 17, U.S. Code. The U.S. Government has a royalty-free li cense to exercise all ri ghts under the copyri ght claimed herein fo r Governmental purposes. All other rights are reserved by the copyright owner. The gas generator and turbopumps are packaged between Programme" for European Space Agency. They are also the upper and lower aerospike nozzle surfaces (Fig. 3). being studied in Japan.' 2,13 In support of the NASA RLV program, a group was formed at NASA Langley Research Center to help mature the VentureS tar vehicle concept with Lockheed Martin Thruster '4 (primary now) Skunkworks and their partners. Conceptual vehicle analysis typically uses simplified relationships for propulsion data accurate for bell nozzle rocket engines but eaS8 ",'/ not applicable for predicting thrust vectoring capability of bleed / ___ ._ _ __ J-->,"- _ 11 ,,- an aerospike rocket engine. This paper addresses the Plug base ~~ Recirculation region problem of generating an aerospike engine database for Fig. 2 Aerospike components and flow-field use in the POST (Program to Optimize Simulated characteri stics shown for the upper half of the aerospike Trajectories).'5 engine. Method The aerospike nozzle is a truncated spike (or plug nozzle) An aerospike rocket engine of the type required for that adj usts to the ambient pressure and potentially powering a VentureS tar class vehicle has not been tested integrates well with launch vehicles. The flow-field or designed in detail. Typical engine data for an RLV structure changes dramatically from low altitude to high class vehicle is given in Table 1. Part of the conceptual altitude on the spike surface (Fig. 3) and in the base vehi cle design process is determining both the required 4 region. -{; Figure 3 shows the pressure contours for the engine thrust and the number of engines needed. During hot exhaust gas expanding along the aerospike nozzle the conceptual design of a vehicle, a number of different surface for different altitude conditions. The top contour engine designs were evaluated. For each new aerospike is for an altitude slightly less than the nozzle design engine, the conceptual design team obtained limited condition (at the design condition, the upper boundary performance estimates at five critical trajectory points would be parallel to the vehicle centerline). The bottom from Rocketdyne, the propulsion contractor. Initially, contour is for an altitude near sea level. Near sea level, these estimates were limited due to the concentration of the atmospheric pressure is close to the exhaust gas resources on the development of the X-33 RLV. These pressure such that it does not expand significantly, and initial estimates were based on engine gas generator cycle therefore follows the nozzle contour until the flow has analysis and a calibrated approximation of an aerospike turned enough to create a shock near the end of the nozzle's performance (from extrapolation of experimental nozzle. data). The initial, limited propulsion data did not include the nozzle forces and moments necessary for controlling vehicle pitch angle along a trajectory. In addition to nozzle forces and moments for controlling pitch, more data points were needed to accurately optimize the vehicle trajectory. For these reasons, an alternate but compatible method was developed for predicting aerospike engine performance. Table 1: Aerospike Engine Description Data RS-2200 Engine I At Sea Level I In Vacuum Thrust, lbf 520,000 J 564,000 342 456 Fig. 3 inviscid pressure contours for the Specific Impulse, sec I exhaust gasses at different altitude conditions. The Propellants Oxygen, Hydrogen Upper half of figure shows a pressure contour near the Mixture Ratio (O/H) 6.0 I 5 .5 design point and lower half of the figure, near sea level. Chamber Pressure, psia 2,250 I 1,950 Cycle Gas Generator The base region creates an aerodynamic spike? at high Area Ratio 193 altitudes (giving the aerospike its name), thus maintaining Throttling, Percent Thrust 20-100 I 20-84 the base pressure and the contribution of the base region Dimensions, inches Forward End 294 wide x 96 long In to the aerospike thrust. the early 1960's, aerospike Aft End 120 wide x 96 long and plug nozzles were the focus of development
Details
-
File Typepdf
-
Upload Time-
-
Content LanguagesEnglish
-
Upload UserAnonymous/Not logged-in
-
File Pages10 Page
-
File Size-