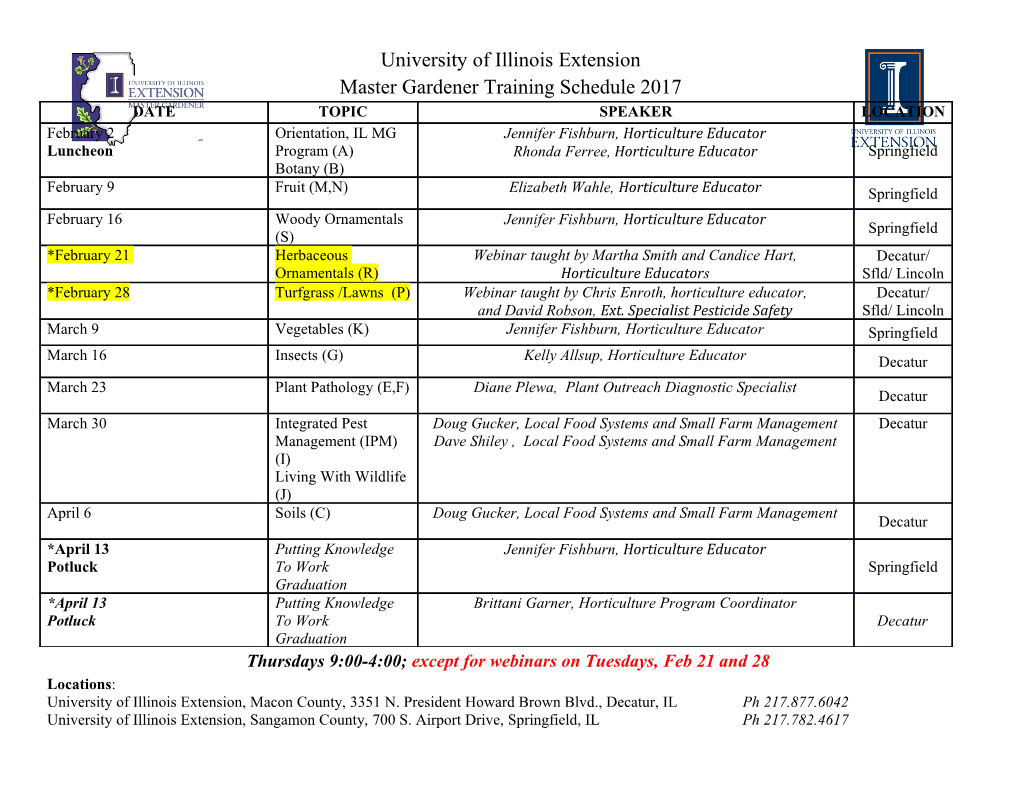
Fine �\\brking'___ _--- ----________Ma Y/JUne 1981 Wo odenJo inter How to build this essential machine by Galen Wine hip even years ago I walked into a local arrived at the design fo r the jointer cast-iron counterparts, my wooden hardware store to buy an odd assort­ shown here. It requires no exotic, hard­ jointer incorporates fo ur sets of inclined mentS of stuff. "What are you going to to-find hardware or materials, and it ways or wedge-shaped bearing blocks. make?" asked the quizzical gentleman doesn't call for any tricky methods of As shown below, these provide the waiting on me. "A wooden jointer, " I construction. Its performance rivals that means fo r raising and lowering the replied, trying to sound confident. He of an industrially produced machine, tables. The wedges on the bottom of was both astonished and skeptical, and though its price (about $350) is consid­ each table (elevation blocks) ride up did his best to persuade me to buy the erably less, and its fe el and appearance and down on the stationary ways (bear­ jointer on display in the store. Despite are friendlier. I've been using this ing blocks) attached to the frame assem­ his warning that a jointer is a precision jointer fo r about 18 months, taking it bly. This system is especially suitable for tool and not the kind of thing you just from one job site to another, and 1'm a wooden jointer because it supports throw together in your shop, I bought very happy with its design and with the each bed at fo ur points, rwo at each the items on my list and thus embarked results it produces. end, eliminating the possibility of on my first tool-building venture. Like certain of its industrial-duty, drooping tables and providing very That first jointer worked, bu t it left up� --<--up several things to be desired. So I deter­ -down Outfeed table, Infeed table� down-+ mined to make a jointer that would per­ form as well as a commercial model. I subsequently tested five designs, each Bearing blocks-0 Elevation blocks one simpler, more reliable and more (stationary) precise than the one before. Finally, I 44 Costing about $1, 000 le ss than comparable factory-built machines, this wooden-bedjo inter can be built with ordi­ nary shop tools. It joints a square, straight edge on boards fo r gluing up , and can fa ce-joint boards up to 6 in. wide. The view fr om the motor side, below, with the bed turned on edge, reveals the inclined ways that allo w both infeed and outfe ed tables to be adjusted. stable working surfaces. I've jointed a machinery distributor. The cutterhead facing. The gluelines need time to cure lot of long, heavy stock with this shaft runs in two self-aligning, ball­ thoroughly, and the laminated slabs machine, and found it can easily cut a bearing pillow blocks, which you can need time to stabilize. true edge on an 8/4 board, 8 ft. long get at any well-stocked industrial­ The tables shown here are propor­ and 10 in. wide. supply or farm-supply store. tioned to my own preferences: the in­ The cutterhead is the heart of the ma­ For driving the cutterhead, use a 1-HP feed table is 10 in. longer than the out­ chine, so you should get one that is or 1Yz-HP, 3,600-RPM motor. Select a feed because I find this easier fo r joint­ well-balanced and perfectly round pair of pulleys that will turn the cutter­ ing long, heavy stock. But you can make (square cutterheads are dangerous) and head about 5,000 RPM (about 4,000 sur­ them of equal length, as is common that has been turned and milled from a face feet per minute) . practice, or you can experiment to learn single piece of bar stock. It should have The infeed and outfeed tables are what suits you best. The same holds a cutting arc of about 3 in. and a hefty laminated from quartersawn, face­ true for the dimensions of the fe nce. shaft, % in. in diameter. Mine was glued boards. I used o/4 -in. beech, but Yo u can make one fence for the kind of turned and milled by a machinist friend, maple or another hard, heavy wood work you do most, or you can make sev­ who got the shaft too small fo r my lik­ would do. Since the finished tables are eral of different sizes fo r different jobs. ing. I'll soon make a new one with a 3 in. thick, you should rip the laminae Since you're making your own, you %-in. shaft , which will minimize vi­ to a rough width of around 3% in. to aren't limited by what some manufac­ bration and increase durability. Yo u can allow fo r a preliminary and a final sur­ turer decides is the average size. have a machinist do this work for you as facing of both sides. Use yellow (ali­ The jointer frame consists of two sides I did , or you can buy a cutterhead as a phatic resin) glue, and allow the tables and three sets of blocks-two pairs of replacement part from a woodworking- to sit fo r several weeks before initial surr bearing blocks and a pair of clamping Photos. except where nOted: Pett Krumhardt 45 Jointer tables and frame assembly % 4 Outfeed table, x bolt epoxied 3 x 6 x 26 into guard Cutterhead guard Elevation block "-11_ Chip Guard mount --- �deflector 1'/. Infeed table,� 3x6x33 • • Fence support • top '/. • x 3 % hanger4 bolt '/·X2 n- .carriage x lag bolt I bolt in counterbore for attaching '/. box to frame x 2Y, dowelDetermine '� d by � adding '/,6 indis?arre<z. to dis ft m� Frame side from top edge of fra me �--:t. d Bearrng block to top of outfeed table. 5f ' '/4 4 � Make all parts of fence x wedged dowel ""C:::!I, assembly except fence and runners from 3f.-in. birch plywood. Cut fence and runners from hard­ wood to size you need. Ta ble/frame assembly in elevation % '/. 7 x carriage bolt x 6 hanger bolt Y4-in. plywood chip deflector I Elevation bloc7k. ,- Clamping block % ·Cutterhead not shown. T-nut epoxied into wing Tzlting fe nce assembly consists ofa sliding table, a slzding tzlt base, a tzlt bracket and a fe nce, which can vary in size to suit the needs of the operator. Removing the fe nce-support top gives access to V-belt and arbor pulley. 46 blocks. The top edges of the bearing blocks are beveled at 30·, and the clamping blocks are slotted for clamp­ ing bolts. The clamping blocks, though not beveled, are set at a 30· angle to the top of the frame. The drawing (facing page) dimensions and locates these parts. Make sure when cutting duplicate parts that their dimensions and angles are precisely the same. This can be done by ripping and beveling a single board and then crosscutting identical parts to finished length. All the blocks must be oriented at a true 90· to the frame sides, and the clamping blocks ought to be positioned as close as possible to the center bearing blocks. The outer bear­ ing blocks should be flush with the ends of the frame sides. To add strength and to help position the parts during clamping, I cut narrow tenons on the bearing blocks and dadoes in the frame sides to house them. But you need not go to this trouble to get similar results-just clamp the frame Particleboard base contains separate compartments fo r the motor andfo r chips and shavings. sides together with the bearing and Door to shavings bin slides up and do wn in ra bbeted cleats. Opening in side under the infeed clamping blocks between, and then tap table gives quick access to the wing nut that must be loosenedfo r making changes in depth of cut. The T configuration of the base concentrates the machine 's weight on three points, them into their exact positions with a eliminating the need to le vel it to the floor. mallet. This done, tighten the clamps, and bore for dowels through the frame Jointer base 16 x16x22 sides into the- blocks as shown in the Motor enclosure. drawing (% in. dia. holes fo r the bear­ }'.X }'. ing blocks, %-in. dia. holes for the clamping blocks) . The dowels will let cleat you place the parts accurately when glu­ 9Y, x 48 x 22 --'!oJ ing up and will reinforce the frame as­ Base cabinet sembly. The �4 -in. dowels are slotted and wedged. Since you're gluing end grain to long grain, epoxy is best; size the end grain before gluing and clamp­ ing. When the glue has set, sand the dowels flush with the frame sides. The base, which you'll probably want �-t-_-+_ to make while your table laminations Access area to infeed table are aging, is of %-in. high-density par­ clamping nut ticleboard. Plywood will suffice, but it's Shavings more expensive and not as rigid or removal door heavy. With a plan view that resembles Relief cut a T, the stand is constructed using cor­ ner cleats, screws and yellow glue. This type of base has several advantages. One jointer wider than the one you're mak­ both tables through the thickness is that the motor is enclosed in a ing. If you can't find a friend who'll let planer for several light passes to bring separate compartment, protected from you use his, or a school shop where you them within lja in.
Details
-
File Typepdf
-
Upload Time-
-
Content LanguagesEnglish
-
Upload UserAnonymous/Not logged-in
-
File Pages7 Page
-
File Size-