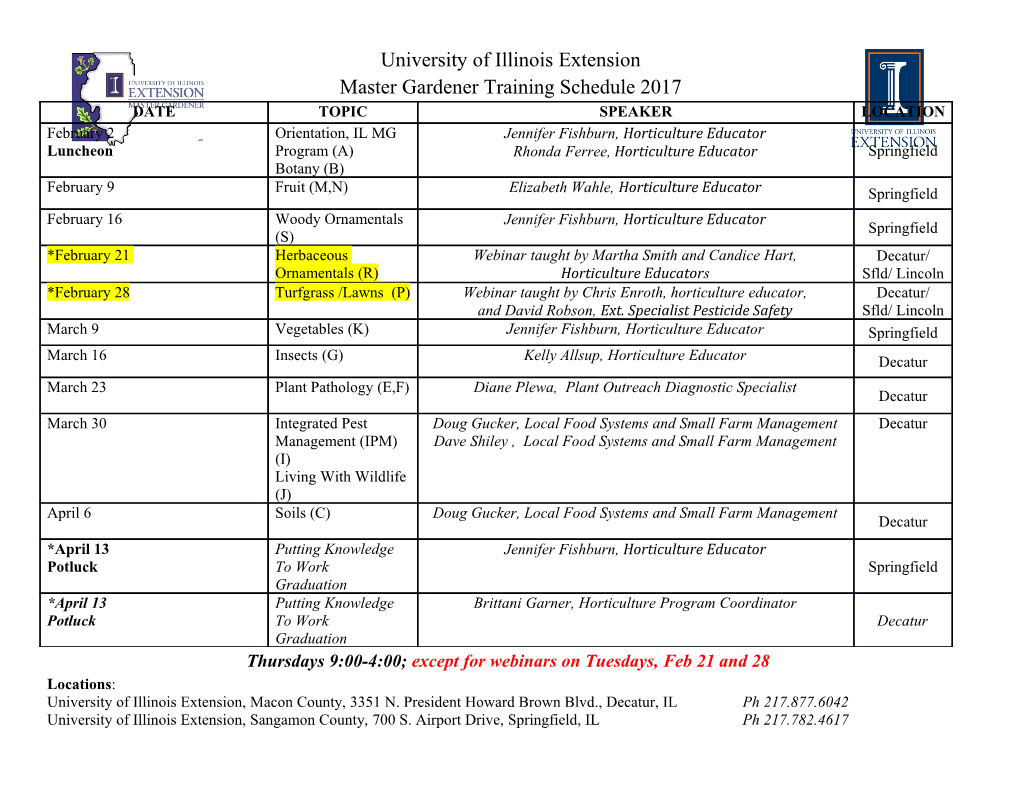
5th International & 26 th All India Manufacturing Technology, Design and Research Conference (AIMTDR 2014) December 12 th –14 th , 2014, IIT Guwahati, Assam, India EFFECT OF HYDRAULIC ACCUMULATOR ON THE SYSTEM PARAMETERS OF AN OPEN LOOP TRANSMISSION SYSTEM M. K. Barnwal 1, N. Kumar 2, Ajit Kumar 3*, J. Das 4 1ISM, Dhanbad, 826004, India, E-mail: [email protected] 2ISM, Dhanbad, 826004, India,E-mail: [email protected] 3*ISM, Dhanbad, 826004, India, E-mail: [email protected], 4ISM, Dhanbad, 826004, India, E-mail: [email protected] Abstract This paper denouements the study of operating parameters of a hydraulic transmission system with and without the application of hydraulic accumulator. In this respect, the hydraulic system, designed in the open circuit mode, consists of the fixed displacement hydraulic pump which gives pressured fluid to the hydro-motor and charges the accumulator as well. The load on the motor is controlled hydraulically by coupling the motor with the loading pump, which discharges the fluid through the Pressure Relief Valve (PRV). The pressure decay of the accumulator in the hydraulic system has been analysed and the parameters affecting the pressure decay has been sorted out. The effect of pressure damping in the hydraulic system has also been investigated for different sizes of accumulators under different loading conditions. The proposed hydraulic system is modelled using MATLAB-SimHydraulics software. The study concludes with the identification of some major operating parameters which affects the performance of the Bladder type Accumulator. 1. Introduction in the hydraulic circuit can be reduced by using Hydraulically driven systems are a drive or accumulator of appropriate capacity with properly transmission system that uses pressurized hydraulic located in the system otherwise if the amplitudes of fluid to drive hydraulic machinery. The open circuit pulsating pressure increase remarkably; it may lead to and closed circuit hydrostatic transmission system the system failure. Accumulators act pulsation have now became a subject for analysis based on its absorbers and surge absorber caused by rapid performance and suitability in Heavy Earth Moving operation or sudden opening and closing of valves Machineries (HEMM) industries. Hydrostatic in a hydraulic circuit [4]. Transmission Systems are considered to be the most efficient energy saving system now-a-days. Their Nomenclature response to system performance is very fast and Vf : Volume of fluid flow in accumulator precise. Efficiency of the main power source can be Pf : Fluid pressure in accumulator improved by HST system. Also, the HST system is P1 : Initial Pre -charge pressure of accumulator P : Maximum system pressure of hydraulic energy regenerative and under partial loading 2 system conditions, the system is highly efficient. A hydraulic P3 : Minimum working pressure ofhydraulic accumulator can be added to the HST circuit to system improve the efficiency of the system in low-speed, V1 : Initial volume of gas in hydraulic high-torque situations. The accumulator can also be accumulator used to recover the kinetic energy without making the V2 : Volume of gas during fully fluid flow reversion. charged(compression)condition of hydraulic In all fluid power applications as Hydrostatic accumulator Transmission (HST) system, pumps are used to V3 : Volume of gas during generate the required power to run the hydraulic discharge(expansion)condition of motor in a hydraulic system [1]. The pumps deliver hydraulicaccumulator this power in a pulsation of fluid flow. The piston ∆V : Change in velocity a pump, as commonly used for higher pressures, tends : Speed of sound β : Bulk modulus of fluid to produce pulsation detrimental to a high pressure ρ : Fluid density system [2]. The periodical pulsations of liquid γ : Isentropic coefficient dynamically damage the elements in the hydraulic system and reduce the service life causing significant sound sources [3]. The amplitudes of pressure pulses 304-1 EFFECT OF HYDRAULIC ACCUMULATOR ON THE SYSTEM PARAMETERS OF AN OPEN LOOP TRANSMISSION SYSTEM Hydraulic accumulator stores the energy of the fluid by compressing the spring used in piston type accumulator or gas in bladder type accumulator. The gas accumulators are mostly used in mobile equipment where an elastic diaphragm separates gas and fluid working environment. The accumulators use nitrogen to keep the hydraulic fluid pressurized. When the fluid is flow into an accumulator, the nitrogen (N ) inside the accumulator is compressed by 2 Fig. 1. Physical system of open-loop hydraulic reducing its volume. The accumulators are based on the principle accumulator that gas is more compressible than mineral oil, used in The main theme of this paper is to find out the the hydraulic system. Energy is stored by the volume suitable size of accumulator which will give less of the hydraulic fluid that compresses the gas under pulsation as pulsation cannot be removed by 100% pressure. If the fluid is released, it will flow out but can be filter to negligible level. The amount of quickly, under the pressure of the expanding gas. The pulsation absorb is also a function of pre-charge rate at which the compression and expansion of the pressure. gas takes place affects the gas state – which is defined The specifications of the components used in the by volume, pressure and temperature [5]. simulation of the Hydrostatic System (HST) system A hydraulic system is considered energy are tabulated in the table shown below: saving if it will have the following capabilities. First, Table 1.Specification of hydraulic system it must improve the efficiency of the power source of Component parameter value Unit the system or next, it must be a regenerative system to Displacement of hydraulic pump 19.8 Cc/rev recover energy during degeneration or while the load Displacement of hydraulic motor 12.0 Cc/rev is lowered. An energy saving HST system using Displacement of loading pump 11.0 Cc/rev accumulator was investigated through analysis and Valve pressure setting 50.0 Bar modelling [6]. 3. Principle of operation 2. Physical model of hydraulic system The bladder type accumulator consists of a synthetic The present study deals with the surge polymer rubber bladder like chloroprene, nitrile, etc. absorbing characteristics of a hydraulic accumulator. inside a metal (steel) shell. The bladder is filled with For this purpose, an open loop hydraulic system is compressed gas. A poppet valve located at the considered which has some basic hydraulic discharge port closes the port when accumulator is components as shown in fig. 1. The hydrostatic completely discharged. This keeps the bladder from system consists the variable speed electric motor (1) getting out into the system. The main advantage of which gives variable mechanical power to the bladder type accumulator is that it responds quickly variable displacement pump (2). The pump gives for receiving and expelling oil flow of oil [8]. It has pressured flow to the hydraulic motor (5) through the lighter weight, lower cost, and compactness. The gas check valve (3). An accumulator (4) is used at the usually nitrogen is pre-charged during empty of suitable location of the system, where availability of hydraulic fluid and it should never be less than ¼ th surge is maximum. To generate fluctuating load to the of the working pressure [9]. Nitrogen is used due to hydraulic system, a loading pump (6) is mechanically non-poisonous, not combustible and does not connected with the hydro-motor; the loading pump combine easily with other element i.e. inert. The gives flow to the PRV (7). The load at the motor is initial pre-charge gas pressure p1 is normally 90% of adjusted by adjusting the set pressure of the PRV. the minimum working pressure P3 of the hydraulic The hydraulic accumulator is installed in system. This is to prevent the accumulator bladder between them to absorb pressure pulsation and shock. constantly closing the anti-extrusion check valve. The Also, it stores potential energy from the surge, which maximum system pressure P2 is the fluid pressure will be used during emergency condition. The surge when the accumulator is fully charged. P2 should not in the system may come from the pulsating flow or be greater than 3 times the minimum working the fluctuating load [7]. For instance, with a five pressure or the elastomeric material of the bladder cylinder piston pump there will be five pulsations per may be damaged. revolution which is unimportant. However, an external disturbance is introduced in the system, through the electric motor, to generate the surge in the present system. Accumulator positioned upstream of the pump acts as a pulsation damper. 304-2 5th International & 26 th All India Manufacturing Technology, Design and Research Conference (AIMTDR 2014) December 12 th –14 th , 2014, IIT Guwahati, Assam, India The pressure surge generated in the system due to sudden closure of valves, travelled back and forth till energy is expended. Pressure generated due to sudden closure is given by: ∆P = ρ a ∆V (5) 5.0 a = β ρ (6) (a) (b) Fig. 2 (a) Bladder type hydraulic accumulator; (b) Schematic diagram showing working of a 5. Simulation of hydraulic circuit hydraulic accumulator The proposed hydrostatic system is modeled in MATLAB R with sim-hydraulics. The hydraulic 4. Modeling of accumulator system consists of basic components like hydraulic pump connected with a variable angular velocity Accumulator is storage vessel and have source. The output of sine wave is given to variable significant role in hydraulic system. When the system angularvelocity source to introduce the pressure-surge pressure is greater than pre-charge pressure than gas in the system. A PRV is set across pump for system is compressed and oil is flow in accumulator. If the safety to relief excess pressure of system. The process of variation is slow it is considered as upstream pressure comes in the form of pulsation isothermal compression otherwise it can be which is sensed by pressure sensor.
Details
-
File Typepdf
-
Upload Time-
-
Content LanguagesEnglish
-
Upload UserAnonymous/Not logged-in
-
File Pages5 Page
-
File Size-