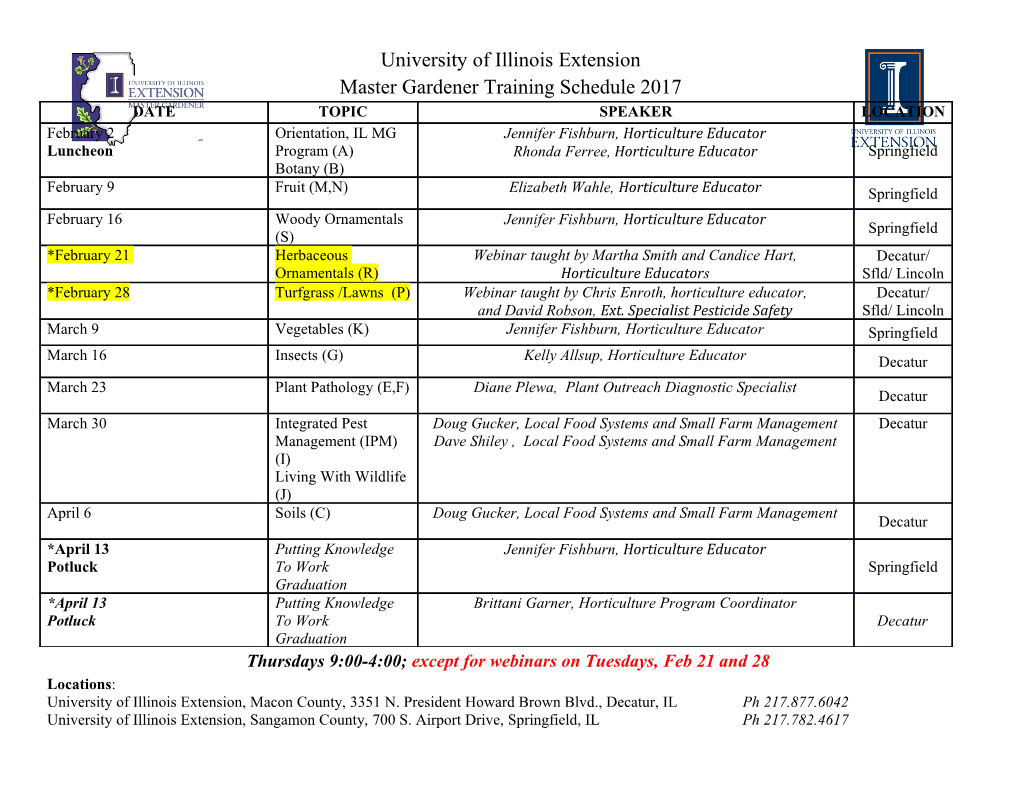
3-/L$ QJf Textile Printing ollution control and 0 the textile printerI Dr.]. R. Easton and II textile printers are very to take up the pollution control challenge. aware of the increasing In terms of dye consumption, almost Dr. J. R. Provost of pressure being placed on half of cellulose fabric is now printed with them by national and local reactive dyes; the remainder is domi- Zeneca Colours government authorities to nated by pigment printing. Reactive dye Alimit discharges to air and water and, via printing on cellulose is therefore a key pyovi,&?an overview landfill, to the ground. segment, and a useful standpoint from Of the main In the past the environmental impact of which to look at some of the pollution environmental issues production was a secondary concern to control issues facing the industry today. the textile printer compared with issues There are two fundamental approaches arising from the use such as productivity and quality. This is to address the issue of pollution control: now changing. All the participants in the source reduction (waste minimisation) of reactive dyes in industry, from the retailer all the way and waste treatment. textile pr-i back up the supply chain to the chemical Many waste treatment systems simply ---T- an machinery manufacturer, are having remove an undesirable process waste FORO Q Why do dyers dye with Foron@RD-dyes? Foron@RD dyes offer highest operating reliobiliiy ond repeotobiliiy Together with the IndosoPSF dyes the Foron@RDdyes con be opplied for dyeing PES/CEL blends by highly economicol, energy- ond woter-saving one bath processes I With the Foron@RD dyes, better economy is ottoinoble thonks to minimol mochine occupotion times Using the Foron@RDdyes reduces the occurence of seconds The Foron@RD dyes ore outstondingly suitoble for dyeing PES microfibres Dyeing is o matter of trust. The Foron@RDronge fully iustifies this trust. Day after doy. Why not coll your Sondoz technicol representative right now ? :r * rodukte (Sthweiz) AG, VoItosrrosselZ, CH-4002 Bod, lei. (061) 324 12 12 A SANDOZ Textile Printing c + from one environmental compartment Customer Printing factory d transfer it to another. An example of -7is is chemical flocculation/sedimenta- Scanner tion, a widely used waste water treat- Ink iet print ment technique which reduces the textile/paper COD/BOD/TSS load in an aqueous effluent stream but generates a sludge . disposal problem for which landfill, in Laser Calour kitchen engraving automatic Europe at least, is becoming an increas- I sampling ingly expensive solution. This highlights the importance of a Approval sample production properly constructed source reduction programme which not only offers reduced waste treatment and disposal costs but Normal bulk Colour kitchen also productivity improvements and raw b. production automatic bulk materials savings. That is to say, it has a quantifiable payback period, unlike much waste treatment which is often simply an expensive licence to operate. The main components of a source reduction programme are: raw material printing plant and in fact contributes Figure 1. Computerisation of conservation, product substitution, more colour to the effluent than the appli- the pre-print process. process and equipment modification, cation and washing-off processes. The improved materials handling, production waste derives from a number of sources of the units themselves. This sectior scheduling, and waste recovery. including: handling and dispensing of however, makes a minimal contribution For the textile printer, the problems chemicals (dyes, thickener, auxiliaries), to the aqueous pollution load. begin in the pre-print and sampling stage washing down of machinery (tubs, stir- It is at the washing-off stage that the fore production has even started. rers, filters) and returned pastes (excess next most important source of pollution >An innovative printing system for tex- paste, colour corrections). is encountered: process effluent to the tiles which could eliminate the require- A particular problem arises with reac- wastewater stream. ment for screen engraving and colour tive dye pastes where hydrolytic stability In modern textile printing plants the paste production for conventional sample of the dye in the presence of alkali is custom built, open-width washing rangc printing has long been a dream of many limited and alginate thickened pastes are has become ?he norm for washing-of* printers. Such a system is now available prone to microbial attack if not properly reactive dye prints on woven and knitted - Stork of Holland launched its TruColor protected with biocide. fabrics. Most recent development in con- printer at the 1991ITMA. The improved levels of process control tinuous open width washing ranges has Driven by digital information this ink jet made possible by modern printing been directed towards improving energy system prints onto textiles using high machines working in an integrated efficiency and reducing water consump- purity reactive dyes based on the Procion system with automated colour kitchens tion. This is not surprising as it has been liquid dyes made by Zeneca Colours (for- offer a significant potential for waste estimated that 30% of the total water merly ICI). This digitalisation of the pre- reduction in the colour shop. consumption in textile printing is used at production/sampling stage means that The modern rotary screen printing the wash ing-off stage. samples can be generated quickly, and machine actually contributes relatively Reducing water consumption at this cleanly, as shown in Figure 1. little to the total pollution load from the stage concentrates the chemical pollu- The figure also shows how the com- print works. Nevertheless, improvements tion load from the washing machine and puter system could control other produc- have been made by the use thermo- permits a more efficient pretreatment tion functions, such as laser engraving, plastic gluing systems and by minimising prior to mixing with the main effluent colour match prediction and print paste the volume of pipework and "dead stream. preparation in the colour shop. The space" in the machine to reduce colour In the case of all-in printing with reac- increasing use of computer control in the paste losses when changing colourway. tive dyes, then dye, thickener, alkali, pre-production phase of textile printing Again it must be stressed that delivery urea, and auxiliaries (solvent) will all gen- will have a significant beneficial effect by of the correctly prepared paste from the erally be present in the recipe. liminating waste colour paste at the colour kitchen in a timely manner is a Soda ash as alkali in all-in printing Jampling stage and reducing, via laser precondition for reducing the pollution recipes does not represent a major engraving techniques, the discharge of load arising from the print machine. problem for the industry and solvent toxic chemicals. The main concerns arising from the based systems have largely been elimi- The conventional colour kitchen is the print dryer and fixation unit are airborne nated in North America, Europe and ' main producer of waste in the textile emissions and the energy consumption 0 Turn to page 25 I*> 3 Textile Printing h 1 From P9e 22 is available which would permit its reuse. consumption may be more than offset by an, due to flammablllty hazards, air Paradoxically, size recovery systems are the problems associated with a highly 2lSSion regulations and toxicity consid- in use, and there seems no reason why alkaline effluent containing sodium erations. Similarly, there is little problem the same principles cannot be applied to silicate. with auxiliaries since types are now avail- recover sodium alginate. Complete or partial substitution of urea able which avoid the Use of alykylphenol Due to limitations placed on the by a more environmentally acceptable ,thoxylates, substances whlch have nitrogen content of aqueous effluents in chemical would be an ideal solution. limited biodegradability and led, in the areas sensitive to eutrophication, the use However, work to date by the major past, to foam problems on waterways. of urea is a particular concern for printers dyestuff and auxiliary manufacturers has The other components of the recipe are in Western Europe, the USA and Japan at highlighted the well known interaction of more problematical. the moment. Urea reduction is now one reactive dyes with primary hydroxyl With the reactive dyes currently avail- of the major discussion areas with reac- groups as a major obstacle to finding a able, between 10% and 40% of the colour tive dye printers in these areas. replacement product. A large number of remains unfixed after Processing and In reactive dye printing urea acts as a possible alternatives have therefore been must be removed from the fabric to swelling agent for cellulose, it disaggre- ruled out, and so far no simple chemical ensure adequate wet fastness. gates and solubilises dyestuffs, retards substitute for urea has appeared on the Reactive dyes In effluent are not easily evaporation of water during drying, and market. removed by conventional municipal increases condensation of water during Zeneca Colours (formerly ICI) has sewage treatment plants and with steaming. The benefits for the printer are undertaken process optimisation studies increasing pressure to reduce visually an increased solubility of the reactive dye and recommends the partial substitution offensive colour in waterways, printworks in the print paste, improved colour yield, of urea by dicyandiamide which reduces will be forced to give some form of pre- and better levelness and smoothness of the total nitrogen load to the effluent. treatment to reduce or eliminate colour the print, particularly on rayon. With all This system is operating in bulk but from waste water streams prior to dis- these benefits, and the low price of urea, requires careful control of the drying and charge. The C0"OnlY available options it will be extremely difficult to find a tech- steaming operations in order to achieve for this task are: chemlcal destruction nically acceptable and cost-effective good results.
Details
-
File Typepdf
-
Upload Time-
-
Content LanguagesEnglish
-
Upload UserAnonymous/Not logged-in
-
File Pages3 Page
-
File Size-