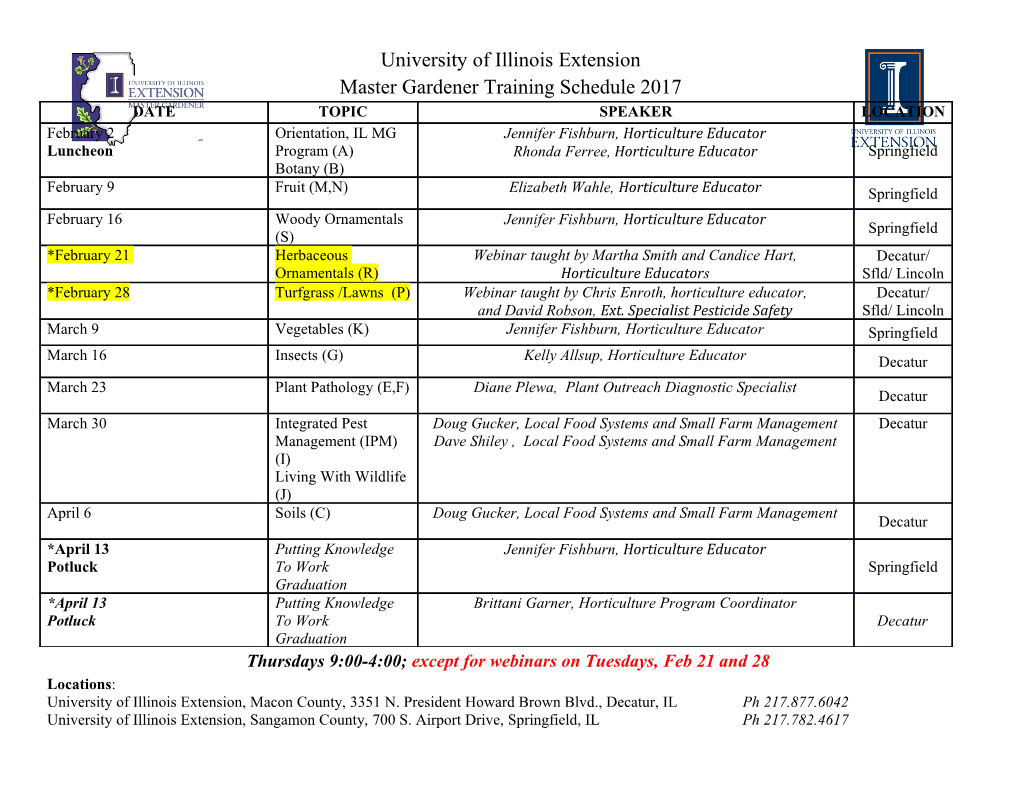
OPERATION AND INSTALLATION MANUAL Company Information Eaton’s Cutler-Hammer business is a worldwide leader providing customer-driven Solid State solutions. From power distribution and electrical control products to industrial automation, the Cutler-Hammer business utilizes advanced product DC Injection Brake development, world-class manufacturing and offers global engineering services and support. To learn more about Eaton’s innovative Cutler-Hammer products and solutions call 1-800-268-3578, for engineering services call 1-800-498-2678, or visit www.cutler-hammer.ca . Eaton Corporation is a global $7.3 billion diversified industrial manufacturer that is a leader in fluid power systems; electrical power quality, distribution and control; automotive engine air management and fuel economy; and intelligent truck systems for fuel economyand safety. Eaton has 48,000 employees and sells products in more than 50 countries. For more information visit www.eaton.com. Eaton Corporation Cutler-Hammer Group 3228 South Service Rd. Burlington, ON L7N 3H8 Canada 905-333-6442 www.cutler-hammer.ca ©2001 Eaton Corporation All Rights Reserved Printed in Canada Cutler-Hammer IL.TS-001A December 2002 Cutler-Hammer FOR YOUR SAFETY Only qualified personnel should install this equipment, after first reading and understanding all the information in this manual. All instructions should be strictly adhered to. The user should consult Cutler-Hammer or a representitive for clarification of the contents of this manual should any doubt or questions arise. The installation of this equipment must be conducted in accordance with all national, regional and local electrical codes. All drawings and technical representations included in this manual are for typical installations and should not in any way be considered for specific applications or modifications. Consult Cutler-Hammer for supplemental instructions. Cutler-Hammer Canada accepts no liability for any consequences resulting from inappropriate, negligent or incorrect installation, application or adjustment of this equipment. The contents of this manual are believed to be correct at the time of printing. In following with our commitment to the ongoing development and improvement of our products Cutler-Hammer reserves the right to change the specification of this product and/or the content of this instruction manual without notice. TABLE OF CONTENTS 1 DESCRIPTION ................................................. PAGE 1 1.1 OVERVIEW ................................................................ PAGE 1 1.2 APPLICATION NOTES ..................................................... PAGE 2 1.3 CONTROLS ................................................................ PAGE 3 1.3.1 CA398-3 LOGIC .............................................................. PAGE 3 1.3.2 CA398-3 REGULATION ..................................................... PAGE 3 2 SPECIFICATIONS ............................................. PAGE 5 2.1 POWER RATING ........................................................... PAGE 5 2.2 CURRENT AND FUSE RATING ............................................ PAGE 5 2.2.1 NOTES ....................................................................... PAGE 5 2.3 SERVICE CONDITIONS .................................................... PAGE 6 2.4 DIMENSIONS .............................................................. PAGE 6 2.5 SCR INSTALLATION SPECIFICATIONS ................................... PAGE 7 2.5.1 SCR TIGHTENING PROCEDURE ........................................... PAGE 7 3 CARD FUNCTIONS ............................................ PAGE 9 3.1 CARD LAYOUT ............................................................ PAGE 9 3.2 LED AND NEON INDICATIONS ............................................ PAGE 9 3.3 ADJUSTMENTS .......................................................... PAGE 10 3.3.1 POTENTIOMETERS ....................................................... PAGE 10 3.3.2 LINK SELECTION ......................................................... PAGE 10 3.3.3 PUSHBUTTON ............................................................. PAGE 10 3.4 TERMINALS ............................................................. PAGE 11 3.4.1 CUSTOMER TERMINALS ................................................. PAGE 11 3.4.2 TERMINALS FOR INTERNAL USE ....................................... PAGE 11 3.5 FAULTS .................................................................. PAGE 12 3.5.1 PHASE LOSS ............................................................... PAGE 12 3.5.2 INSTANTANEOUS OVER CURRENT (IOC) .............................. PAGE 12 TABLE OF CONTENTS 4 INSTALLATION AND START UP ............................... PAGE 13 4.1 INSPECTION ............................................................ PAGE 13 4.2 SAFETY PRECAUTIONS ................................................. PAGE 13 4.3 MOUNTING GUIDELINES ................................................ PAGE 13 4.4 WIRING GUIDELINES ................................................... PAGE 14 4.5 START UP ............................................................... PAGE 14 4.5.1 CHECKS BEFORE POWER-UP ............................................ PAGE 14 4.5.2 WITH POWER ON ......................................................... PAGE 15 5 TYPICAL CONNECTIONS ..................................... PAGE 17 5.1 STAND ALONE DC INJECTION UNIT WITH ZERO SPEED DISABLE .... PAGE 17 5.2 TRU-START STARTER WITH DC INJECTION ....................... .... PAGE 18 5.3 REVERSING TRU-START STARTER WITH DC INJECTION, 125 AMPS .. PAGE 19 AND BELOW ............................................................. 5.4 REVERSING TRU-START STARTER WITH DC INJECTION, 200 AMPS.... PAGE 20 AND ABOVE .......................................................... 6 SPARE PARTS ............................................. .. PAGE 21 1 DESCRIPTION 1.1 OVERVIEW The TRU-START DC Injection braking units provide smooth braking for AC induction motor. The brake units offer adjustable braking because they are current controlled. Unlike a mechanical brake, an electrical brake will never wear out. The brake operates by injecting DC current in two phases of the motor to rapidly decelerate it to zero speed. These units can be supplied as an option to the TRU-START solid state starter, or as stand alone units for new or retrofit installations. Cutler-Hammer TRU-START DC Injection braking modules offer a unique combination of features that make it very reliable, easy to use, and energy efficient. These features include: Closed Loop Current Regulation: The brake, operating with a closed loop current regulator, provides consistent torque every time. This torque is independent of line voltage variations. Direct Power Connection: The brake's power input is connected directly to the AC line, and the power output is connected directly to the motor, no contactors are required. The unit adapts itself to any input voltage between 200 and 600 VAC with no adjustments required. Efficient Power Circuit: The power circuit is an efficient four Silicon Controlled Rectifier ( SCR ) configuration which uses some of the SCR's as a "free wheeling diode", thus maximizing the DC current through the motor coils generated by the AC input current. With every benefit there is usually a trade-off. Although the TRU-START DC Injection brake unit will neverwear out like a mechanical brake, the trade-off is that should there be a loss of power, the brake unit will not operate without battery back-up. Cutler-Hamer can supply a reliable battery back-up to overcome this disadvantage. Braking is initiated when the motor starter is opened and the voltage across the motor has dropped to below 30% or 80% of the line supply. DC injection is removed after an adjustable period has elapsed. It does not provide zero speed sensing, although a normally closed contact from a zero speed switch may be connected to the Disable Input. If braking is released before the motor stops, the motor will coast to rest. If the braking remains on after the motor stops, the DC supply will provide a holding brake. PAGE 1 1.2 APPLICATION NOTES The motor torque/speed characteristic of an induction motor under DC supply is similar to the normal curve published for constant frequency, at 50 or 60 Hz, but this time having "synchronous speed" zero RPM. This is illustrated below. For smooth braking the DC current is typically adjusted to 300% of the motor nameplate current. The stopping time depends on the torque setting and also the inertia of the mechanical system. Electric braking is not recommended for continuous or repetitive operation. The kinetic energy of the mechanical system is transformed into heat during braking ( energy conservation ). That heat is dissipated in the rotor of the motor. On wound rotor motors the external rotor resistance will absorb most of the energy. On squirrel cage motors, overheating of the motor is a real danger if frequent operation is used. Keeping DC current on the motor stator for a short time after the motor has stopped is quite acceptable. The heat produced by the I2R losses are not significant, and they are dissipated in the stator only, not in the rotor where the rotational energy is dissipated. PAGE 2 1.3 CONTROLS The OP-STOP unit contains two major parts, the power circuit and the control card. The power circuit is a 4 SCR single phase full wave controlled rectifier. This configuration optimizes the DC current injected to the motor per input current. The control is contained in a single PC board, CA398-3. This board is
Details
-
File Typepdf
-
Upload Time-
-
Content LanguagesEnglish
-
Upload UserAnonymous/Not logged-in
-
File Pages27 Page
-
File Size-