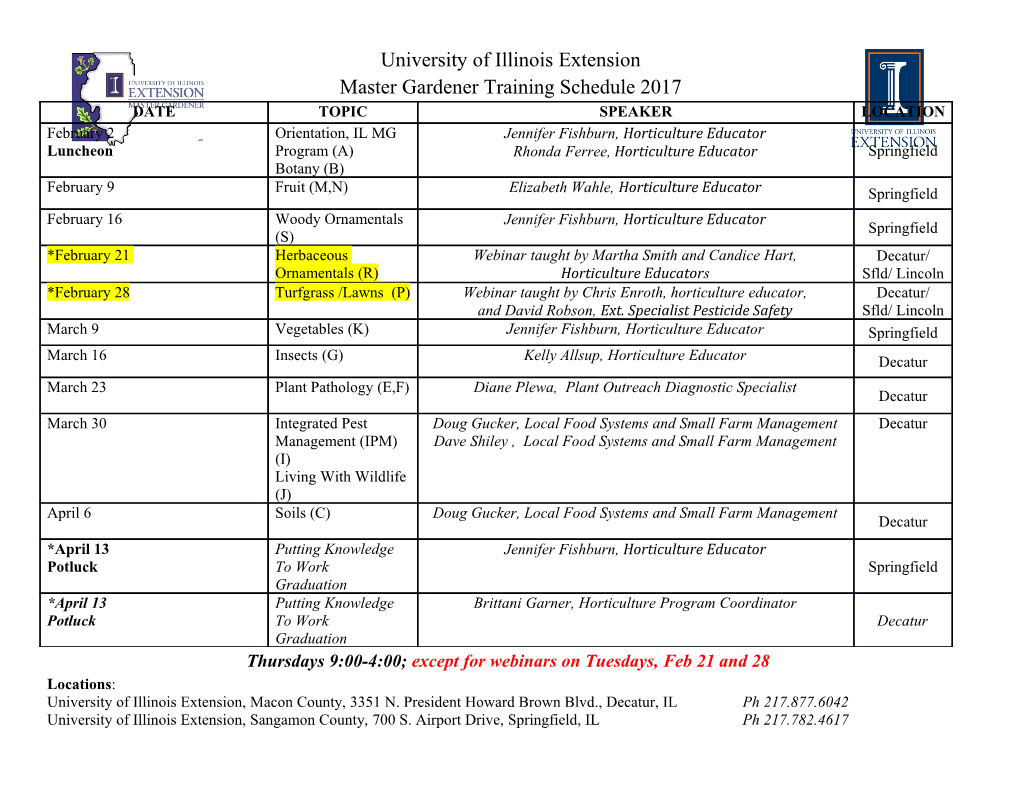
International Journal of Turbomachinery Propulsion and Power Article Investigation on the Flow in a Rotor-Stator Cavity with Centripetal Through-Flow † Bo Hu *, Dieter Brillert, Hans Josef Dohmen and Friedrich-Karl Benra ID Department of Mechanical Engineering, University of Duisburg-Essen, 47057 Duisburg, Germany; [email protected] (D.B.); [email protected] (H.J.D.); [email protected] (F.-K.B.) * Correspondence: [email protected]; Tel.: +49-203-379-1703 † This paper is an extended version of our paper in Proceedings of the European Turbomachinery Conference ETC12, 2017, Paper No. 97. Academic Editor: Claus Sieverding Received: 31 July 2017; Accepted: 6 October 2017; Published: 19 October 2017 Abstract: Daily and Nece distinguished four flow regimes in an enclosed rotor-stator cavity, which are dependent on the circumferential Reynolds number and dimensionless axial gap width. A diagram of the different flow regimes including the respective mean profiles for both tangential and radial velocity was developed. The coefficients for the different flow regimes have also been correlated. In centrifugal pumps and turbines, the centripetal through-flow is quite common from the outer radius of the impeller to the impeller eye, which has a strong influence on the radial pressure distribution, axial thrust and frictional torque. The influence of the centripetal through-flow on the cavity flow with different circumferential Reynolds numbers and dimensionless axial gap width is not sufficiently investigated. It is also quite important to convert the 2D Daily and Nece diagram into 3D by introducing the through-flow coefficient. In order to investigate the impact of the centripetal through-flow, a test rig is designed and built up at the University of Duisburg-Essen. The design of the test rig is described. The impact of the above mentioned parameters on the velocity profile, pressure distribution, axial thrust and frictional torque are presented and analyzed in this paper. The 3D Daily and Nece diagram introducing the through-flow coefficient is also organized in this paper. Keywords: rotor-stator cavity; centripetal through-flow; axial thrust; frictional torque 1. Introduction In radial pumps and turbines, the leakage flow (centripetal through-flow) is quite common from the outer radius of the impeller to the impeller eye, which has a major impact on the pressure distribution, axial thrust (Fa) and frictional torque. Von Kármán [1] and Cochran [2] gave a solution of the ordinary differential equation for the steady, axisymmetric, incompressible flow. Daily and Nece [3] examined the flow of an enclosed rotating disk both analytically and experimentally. They distinguished the four flow regimes, shown in Figure1, by correlating different empirical equations of the moment coefficients. Kurokawa et al. [4–6] studied the cavity flow with both centrifugal and centripetal through-flow. Schlichting and Gersten [7] organized an implicit relation based on the results of Goldstein [8] for the moment coefficient under turbulent flow conditions. Poncet et al. [9] studied the centripetal through-flow in a rotor-stator cavity and obtained an equation of the core swirl ratio K based on the local flow rate coefficient (Cqr) for Batchelor type flow [10]. For Batchelor type flow, the centrifugal disk boundary layer and the centripetal wall boundary layer are separated by a central core. Debuchy et al. [11] derived an explicit equation for K which is valid over a wide range of Cqr. Launder et al. [12] provided a review of the current understanding of instability pattern that are created in rotor-stator cavities leading to transition and eventually turbulence. Recent experimental Int. J. Turbomach. Propuls. Power 2017, 2, 18; doi:10.3390/ijtpp2040018 www.mdpi.com/journal/ijtpp Int. J. Turbomach. Propuls. Power 2017, 2, 18 2 of 17 thatInt. are J. Turbomach.created Propuls.in rotor-stator Power 2017 , cavities2, 18 leading to transition and eventually turbulence. Recent2 of 17 experimental investigations up to circumferential Reynolds numbers Re = 5 × 108 with and without through-flow have been conducted by Coren et al. [13], Long et al. [14] and Barabas et al. [15]. The 8 scopeinvestigations of the present up study to circumferential is shown in Figure Reynolds 1. numbers Re = 5 × 10 with and without through-flow have been conducted by Coren et al. [13], Long et al. [14] and Barabas et al. [15]. The scope of the present study is shown in Figure1. Figure 1. Flow regimes according to Daily and Nece [3]. Figure 1. Flow regimes according to Daily and Nece [3]. TheThe main main dimensions dimensions of the of therotor-stator rotor-stator cavity cavity are areillustrated illustrated in Figure in Figure 2. This2. This study study focuses focuses on on the theinfluence influence of non-pre-swirl of non-pre-swirl centripetal centripetal through-flow through-flow on the on thecavity cavity flow. flow. Based Based on the on theresults results from from 0 previousprevious studies, studies, CD (through-flow(through-flow coefficient)coefficient) maymay have have a largea large influence influence on the on moment the moment coefficient, 0 coefficient,noted as notedCM. Uncertaintiesas . Uncertainties still exist still in exist the effectin the ofeffectCD ofon CM onwith different with different values values of Re and of G Re and(dimensionless G (dimensionless axial axial gap). gap). This This study study is aimed is aimed to provideto provide more more results results to to increase increase the the dataset dataset and andto to better better understand understand the the influence influence of of above above parameters parameters on onC p(pressure (pressure coefficient), coefficient),CF (axial (axial thrust thrustcoefficient) coefficient) and andCM . The. The definitions definitions of the of significantthe significant dimensionless dimensionless parameters parameters in this in study this study are given are ingiven Equations in Equations (1a)–(1k). (1a–k). Figure 2. Main dimensions of the test rig. a: Hub radius; b: outer radius of the disk; r: radial Figure 2. Main dimensions of the test rig. a: Hub radius; b: outer radius of the disk; r: radial coordinate; coordinate; s: axial gap of the front chamber; sb: axial gap of the back chamber; t: thickness of the disk; s: axial gap of the front chamber; : axial gap of the back chamber; t: thickness of the disk; z: axial z: axial coordinate. coordinate. ∙W · b2 Re = = (1a) (1a) v 2 ∙W · r Re=j = (1b) (1b) v s G = (1c) b Int. J. Turbomach. Propuls. Power 2017, 2, 18 3 of 17 = (1c) Int. J. Turbomach. Propuls. Power 2017, 2, 18 3 of 17 = (1d) ∙ . 0 m 2∙∙(CD = −)∙d (1d) = m· b (1e) ∙ ∙ b Z 2 · p · (pb.− p) · rdr CF = ∙ (1e) = r · w2 · b 4 (1f) a 2∙∙∙ 0.2 Q· Rej Cqr == (1g)(1f) 2 ·p · W · r3 z z = (1g) = s (1h) r x = (1h) 2∙|b | = (1i) ∙2·∙jM j C = (1i) M r · W2 · b5 ∗ = p p∗ =∙ ∙ (1j)(1j) r · W2 · b2 ∗ ∗ ∗ ∗ C=p = p(=1(x =)1−) − (p)( x) (1k)(1k) 2. Theoretical Analysis 2. Theoretical Analysis 0 In this study, the values of Q (volumetric through-flow rate), CD and Cqr are negative for In this study, the values of Q (volumetric through-flow rate), and are negative for centripetal through-flow. Using a two-component Laser Doppler Anemometer (LDA) system, centripetal through-flow. Using a two-component Laser Doppler Anemometer (LDA) system, Poncet Poncet et al. [9] correlated Equation (2a) to evaluate the core swirl ratio K (the ratio of the angular et al. [9] correlated Equation (2a) to evaluate the core swirl ratio K (the ratio of the angular velocity of velocity of the fluid to that of the disk at z = 0.5) with centripetal through-flow when Cqr ≥ −0.2. the fluid to that of the disk at =0.5) with centripetal through-flow when −0.2. Debuchy et Debuchy et al. [11] determined Equation (2b) to calculate the values of K for a wider range Cqr ≥ −0.5 al. [11] determined Equation (2b) to calculate the values of K for a wider range −0.5 with a with a two-component LDA system. The results from Equation (2b) are smaller than those from two-component LDA system. The results from Equation (2b) are smaller than those from Equation Equation (2a) at large values of Cqr , compared in Figure3. (2a) at large values of , compared in Figure 3. 5 7 K = 2 · −5.9 · Cqr + 0.63 − 1(2a) (2a) =2∙−5.9∙ + 0.63 −1 5 −8.85 · C + 0.5 4 −8.85 ∙ qr+0.5 K = (2b) = (−1.45Cqr) (2b) e. Figure 3. Comparison of results from Equation (2a,b). K: core swirl ratio at =0.5; : local flow Figure 3. Comparison of results from Equations (2a) and (2b). K: core swirl ratio at z = 0.5; Cqr: local rateflow coefficient; rate coefficient; Eq: equation. Eq: equation. A number of studies, such as those by Kurokawa et al. [6], Poncet et al. [9], Coren et al. [13], and Barabas et al. [15], show that the pressure distribution along the radius of the disk can be Int. J. Turbomach. Propuls. Power 2017, 2, 18 4 of 17 estimated with the core swirl ratio K both with and without through-flow. Will et al. [16–18] determined Equation (3) to evaluate the pressure distribution along the radius of the disk for the incompressible, steady flow. It is obtained directly from the radial momentum equation when the turbulent shear stress is neglected. In a rotor-stator cavity, the cross sectional area changes in radial direction. Consequently, the pressure must also change since the mean velocity changes in radial direction according to the continuity equation. 2 ! 2 ¶p vj ¶vr 2 2 r · Q = r − vr = r · K · W · r + (3) ¶r r ¶r 4 · p2 · s2 · r3 The difference of the force on both sides of the disk is the main source for axial thrust, noted as Fa, calculated with Equation (4a).
Details
-
File Typepdf
-
Upload Time-
-
Content LanguagesEnglish
-
Upload UserAnonymous/Not logged-in
-
File Pages17 Page
-
File Size-