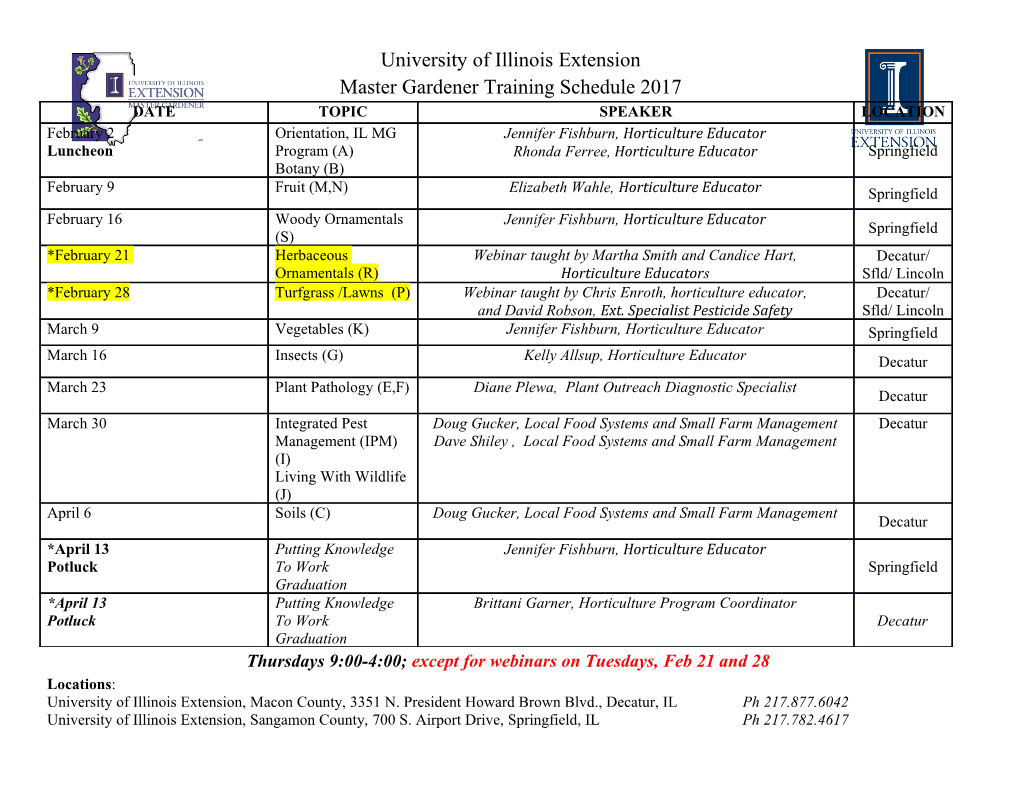
Master of Science Thesis Passive Flow Separation Control on an Airfoil-Flap Model The Effect of Cylinders and Vortex Generators D.P. Jansen August 2012 Faculty of Aerospace Engineering · Delft University of Technology Passive Flow Separation Control on an Airfoil-Flap Model The Effect of Cylinders and Vortex Generators Master of Science Thesis For obtaining the degree of Master of Science in Aerospace Engineering at Delft University of Technology D.P. Jansen August 2012 Faculty of Aerospace Engineering · Delft University of Technology Delft University of Technology Copyright ¥c Aerospace Engineering, Delft University of Technology All rights reserved. Delft University Of Technology Department of Aerodynamics The undersigned hereby certify that they have read and recommend to the Faculty of Aerospace En- gineering for acceptance a thesis entitled “Passive Flow Separation Control on an Airfoil-Flap Model” by D.P. Jansen in partial fulfillment of the requirements for the degree of Master of Science . Dated: August 2012 Head of department: Prof.dr.ir.drs. H. Bijl Supervisor: Dr.ir. L.L.M. Veldhuis Reader: Dr.ir. B.W. van Oudheusden Reader: Ir. W.A. Timmer Acknowledgements This report is written as a thesis for the degree of Master of Science at the Faculty of Aerospace Engi- neering, Department of Aerodynamics, at Delft University of Technology. I would like to take the opportunity to thank all the people who have helped me in accomplishing this graduation research. I would like to thank Dr. ir. L.L.M. Veldhuis, my supervisor, for his full support, enthusiasm and sharing of his in depth knowledge on experimental research and the field of flow separation control. I could not have wished for a better advisor for this project. I also would like to thank Dipl. ing. S. Bernardy and L. Molenwijk for their willingness in answering my questions and their assistance in performing the wind tunnel experiments. Then I would like to thank my parents for their motivation and advice in times most needed. Special thanks goes to R. Peacock for his sincere curiosity and help on the project. Finally I also want to mention Kim-Lan, my girlfriend, because without her love and unlimited support I definitely would not have achieved this result. Delft, The Netherlands D.P. Jansen August 2012 v D.P. Jansen vi MSc. Thesis Summary In the on-going search for improvements in high lift device performance, the field of flow separation control has seen explosive growth in recent years. This is due to a continuously improved understanding of fluid mechanics, the development in experimental and computational techniques and the variety of flow control mechanisms existing today. These multiple mechanisms can be differentiated into active and passive flow control techniques. In this research two passive flow separation control methods are tested on their ability to postpone flow separation on an airfoil with trailing edge flap model of the Extra EA-400. The two methods are the application of vortex generators on the airfoil and the positioning of vortex producing cylinders in the slot of the airfoil flap system. The 2D airfoil flap model was tested by experimental and numerical investigation. The flap deflection was ◦ ◦ ◦ set at δf = 45 , δf = 50 and δf = 55 to test the flap at moderate to highly separated flow conditions. Measurements in the experiment were done by pressure holes and probes and oil flow visualization. Numerical calculations were performed in FLUENT as part of the ANSYS 13.0 package, which was also used to create the grid. The model is a RANS analysis with the k − ω SST turbulence model and low Re near wall treatment. It was found in the experiments that both the vortex generators and the cylinders were able to delay flow separation and thereby increase the lift of the airfoil flap system. Both devices are able to create vortices that entrain flow into the boundary layer, which gets re-energized. The cylinders proved to be superior compared to the vortex generators in the ability to postpone the point of flow separation. With respect to size and positioning the cylinders also showed a larger bandwidth than the vortex generators at which the devices were effective. The results from the experiments indicated that the reduced frequency for the cylinder vortex shedding resulting in the largest delay in flow separation, matched the theoretical predictions found in literature. Especially at high flap deflections significant lift gains were obtained up to ◦ 6% for the vortex generators and 18% for the cylinders at a deflection of δf = 55 . At the flap deflection ◦ of δf = 45 the flow separation delay capabilities of the cylinders are less effective. The frequency tests, oil flow visualization and boundary layer measurements were used to understand the performance and working principles of the cylinders. The numerical simulations showed difficulties in reproducing the results for the cylinders obtained from the experiment. While for the attached airfoil flow the numerical simulations showed good agreement with the experiment, the flow separation on the flap at high deflections was not accurately modelled for both the baseline and cylinder configuration of the airfoil flap. The vortices created in the simulation showed a different frequency than found in the experiment and only minor effects of the cylinder were observed. Separation on the flap was very slightly delayed, although no significant mixing effects of the vortices were visible in the boundary layer. vii D.P. Jansen viii MSc. Thesis Contents Acknowledgements v Summary vii List of Figures xii List of Tables xvii Nomenclature xxi 1 Introduction 1 1.1 The need for high lift systems . 1 1.2 Limits in high lift performance . 3 1.3 Flow separation in high lift performance . 5 1.3.1 Plain airfoil characteristics . 5 1.3.2 Flapped airfoil characteristics . 6 1.4 Flow separation control . 8 1.4.1 Active flow separation control techniques . 8 1.4.2 Passive flow separation control techniques . 10 1.5 Opportunity of research . 13 1.6 Layout of the report . 13 2 Experimental model setup 15 2.1 Introduction . 15 2.2 The wind tunnel and model . 15 2.3 Passive flow separation methods . 18 2.3.1 Vortex generators . 19 ix Contents 2.3.2 Cylinders . 20 2.4 Measurement techniques . 23 2.4.1 Pressure measurements and calculation of Cl and Cd ................. 23 2.4.2 Frequency measurements . 25 2.4.3 Oil flow visualization . 26 3 Experimental results 27 3.1 Introduction . 27 3.2 Baseline model . 27 3.3 Vortex generators . 31 3.4 Cylinders . 34 ◦ 3.4.1 Flap deflection δf = 55 ................................. 34 ◦ 3.4.2 Flap deflection δf = 50 ................................ 42 ◦ 3.4.3 Flap deflection δf = 45 ................................. 43 3.4.4 Comparison of δf effects on cylinder performance and further investigation . 47 3.5 Conclusion experimental investigation . 52 4 Numerical investigation 55 4.1 Introduction . 55 4.2 General setup . 55 4.3 The numerical domain . 56 4.4 Model validation . 61 ◦ 4.4.1 Low flap deflection δf = 15 , no flow separation . 61 ◦ 4.4.2 High flap deflection δf = 45 .............................. 62 ◦ 4.4.3 Very high flap deflection δf = 55 ........................... 63 4.4.4 Conclusion on baseline model validation . 63 4.4.5 Influence of tunnel wall at large flap deflection . 63 4.4.6 Modelling laminar zones in CFD . 65 4.5 Results for baseline and cylinder configurations . 67 4.5.1 Baseline and cylinder velocity field . 68 4.5.2 Vortex development . 68 4.5.3 Vortex influence on the flap . 74 4.6 Conclusion on numerical investigation . 76 5 Conclusion and Recommendations 79 5.1 Conclusion . 79 5.2 Recommendations . 80 D.P. Jansen x MSc. Thesis Contents Bibliography 81 A Test matrix for the wind tunnel experiments 83 B Additional pictures on the wind tunnel and model layout 85 C Output file example of pressure measurements from Profmeasure 89 MSc. Thesis xi D.P. Jansen Contents D.P. Jansen xii MSc. Thesis List of Figures 1.1 General high lift system with single slotted trailing edge and leading edge flap. 2 1.2 Lift polar showing the effects of a trailing edge and leading flap deflection on a plain airfoil. 2 1.3 Circular-arc mean lines A, B, C obtained from the Joukowski transformation. Figure from Smith [1975]. 3 1.4 Flow around a cylinder with a very high circulation, such that the two stagnation points coincide. Figure from Smith [1975]. 4 1.5 Visualization of flow separation on a flap. Figure from Little et al. [2009]. 4 1.6 Visualization of a laminar separation bubble. 5 1.7 Visualization of flow separation. 6 1.8 Lift polar showing the general effect of increasing trailing edge flap deflection. 7 1.9 Triple-slot flap system of the B727-200. Figure from Rudolph [1996]. 8 1.10 PIV visualization of flow separation postponement on a wind turbine blade by applying synthetic jets at α = 16 ◦ and Re = 1 .6 · 10 5. Figure from Maldonado et al. [2010]. 9 1.11 Components of an electrodynamic synthetic jet. Figure from Cattafesta [2011]. 9 1.12 Working principle of boundary layer suction. Figure from Boermans [2008]. 10 1.13 Schematization of a piezoelectric flap. Figure from Veldhuis and van der Jagt [2010]. 10 1.14 Schematization of a DBD plasma actuator. Figure from LeBeau [2007]. 11 1.15 Vortex generators displayed in different setups. Figures from von Stillfried et al. [2010]. 11 1.16 Effect of counter-rotating micro VG’s on RMS anemometer output from hot-film sensors ◦ on flap upper surface with α = 8 and M∞ = 0 .2. Figure from Lin [1999]. 12 1.17 Lift-enhancing tabs as used by Lee et al.
Details
-
File Typepdf
-
Upload Time-
-
Content LanguagesEnglish
-
Upload UserAnonymous/Not logged-in
-
File Pages116 Page
-
File Size-