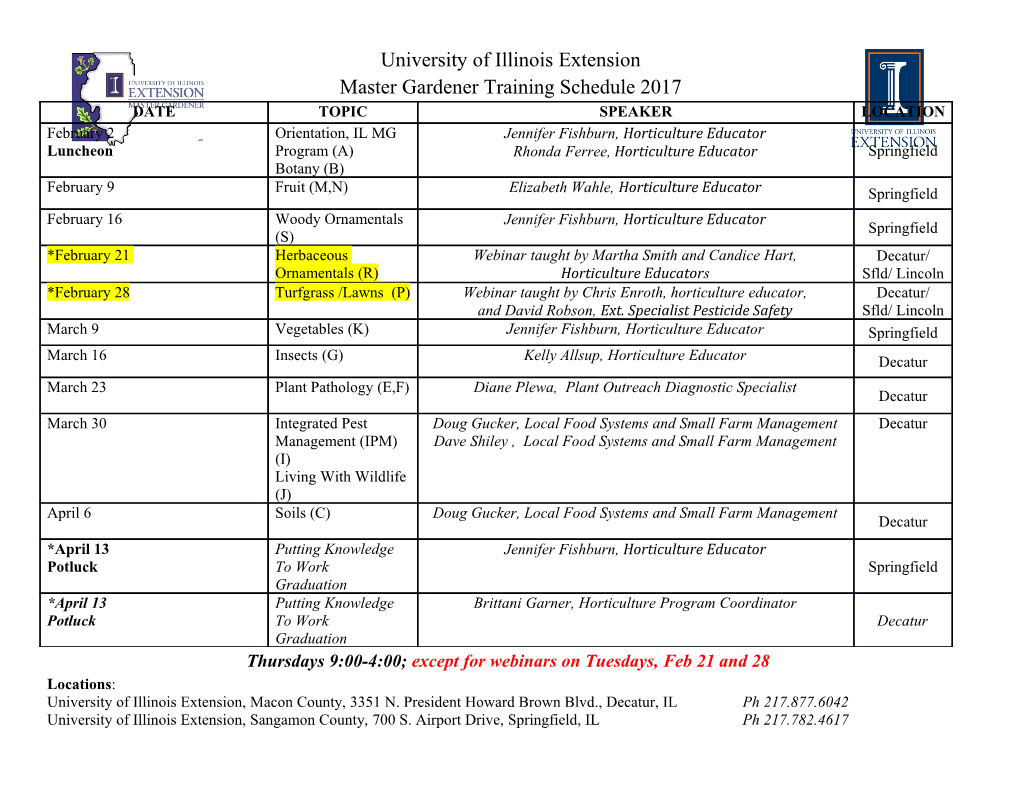
View metadata, citation and similar papers at core.ac.uk brought to you by CORE provided by Universiteit Twente Repository Springback Compensation: Fundamental Topics and Practical Application R. Lingbeek1,2, T. Meinders3, S. Ohnimus2, M. Petzoldt2, J. Weiher2 1 Netherlands Institute for Metals Research, Mekelweg 2 P.O.Box 5008, 2600 GA Delft, The Netherlands URL: www.nimr.nl e-mail: [email protected] 2 INPRO Innovationsgesellschaft für fortgeschrittene Produktionssysteme in der Fahrzeugindustrie mbH Hallerstraße 1, D-10587 Berlin URL: www.inpro.de e-mail: [email protected] 3 University of Twente, Faculty of Engineering Technology, P.O.Box 217, 7500AE Enschede, The Netherlands URL: www.utwente.nl e-mail:[email protected] ABSTRACT: Now that the simulation of deep drawing processes has become more reliable the virtual compensation of the forming tools has become reality. In literature, the Displacement Adjustment (DA) algorithm has proved to be most effective. In this article it is shown how the compensation factor, required for (one-step) DA depends on material, process and geometrical parameters. For this an analytical bar stretch- bending model was used. A compensation factor is not required when DA is applied iteratively and the products geometrical accuracy is improved further. This was demonstrated on an industrial part. The compensation varies over the product, leading to a reduction in shape deviation of 90% and more, a result that could not have been achieved with one-step compensation. Key words: forming simulation, springback, compensation compensation, but the remaining shape difference 1 INTRODUCTION between the desired shape and the actual shape of the blank. The Finite Elements (FE) prediction of springback in industrial deep drawn products has become more and more accurate recently. Even though some 2 ONE-STEP DA COMPENSATION accuracy issues still need to be addressed, the next step in computer aided process planning is already In industry it is most common to compensate in one investigated: automated springback compensation of step only. If springback remains the same after the forming tools. The demand for such an algorithm compensating the tools, a compensation factor of 1.0 is high, as the process planning for automotive sheet can be used to obtain an accurate product shape. metal parts can be very time-consuming and cost- However, springback generally becomes different intensive. after compensation, making springback compensation a non-linear process. For real products The first literature on springback compensation this factor can be anywhere between 0.7 and 2.5, and algorithms dates back to 1992 [1], but especially only an ‘educated guess’ can be made on forehand. during the recent NUMISHEET ’05 conference, the subject has caught a lot of attention [2]. Most algorithms are based on the Displacement Adjustment (DA) method [3], which is a mathematical description of the intuitive way of springback compensation, already applied by process engineers. The shape change of the product due to springback is reversed, multiplied by the so- called compensation factor and applied to the tool geometry. With the compensated tools a new FE simulation can be carried out. The DA method can Fig. 1. The stretch-bending model also be applied iteratively. In consecutive iterations, To obtain more insight in how this factor depends on not the springback deformation is used for material, geometry and process properties, an analytical model of the stretch-bending forming process [4] was used (Fig.1). With this simple model some phenomena from more complex forming processes can already be demonstrated. An elasto- plastic material model was included and it was assumed that the stress profile is constant along the entire bar. In [4] the model is explained in more detail. Only springback due to the internal moment M after forming was considered. R is the forming- radius, εT is the strain due to the tension force T and z is the coordinate in the thickness direction, w and t are the width and thickness of the bar, respectively. t / 2 Fig. 3. Optimal compensation factor for IS-Steel and DP600 M (R, ) (R, )wzdz (1) # T = !$ # T "t / 2 So, when the deformation of a blank is in the plastic area, not only springback is reduced heavily, it also The radius r of the bar after (elastic) springback becomes easier to compensate. As Figure 3 shows, follows from: the compensation factor is higher for higher strength 1 1 M (R,! ) steels. " = T [4] (2) R r E(1 12wt 3 ) When r is set at the desired radius, the optimal forming radius R can be calculated numerically from this (nonlinear) equation. The desired radius was set at 1.0 and R/t=100, producing the following graph (Fig.2) Fig. 4. Optimal compensation factor for various forming radii Finally, the optimal compensation factor was calculated for various desired radii (Fig. 4). Note that with decreasing radius, the strip is bent further, so this graph leads to the interesting conclusion that with increased bending deformation the compensation factor decreases. Fig. 2. The optimal forming radius for various tension loads Not only do these results provide insight in the behaviour of the compensation factor, a more As in industrial practise, springback decreases as the advanced springback compensation algorithm could in-plane tension in the bar increases. In the case of be developed based on the calculation of the optimal pure bending, εT=0, springback is the largest and the compensation factor. As 2D bar elements from a FE bar has to be bent to a much smaller radius to spring simulation are in principle interconnected stretch back to r=1.0. When the tension force increases bending models, the optimal compensation can be springback eventually decreases to zero, obviously calculated separately for each element. This might the optimal forming radius converges to 1.0. lead to a much more effective one-step compensation algorithm. The optimal compensation factor aopt can now be calculated by dividing the compensation displacement (ucomp) at the end of the bar by the 3 ITERATIVE APPLICATION OF DA springback displacement (usb in Fig.1). The result is shown in Figure 3. The compensation factor rises The DA method can also be applied iteratively. No with increasing tension until the entire bar is compensation factor is required anymore, and the deformed plastically (as indicated for DP600 in the geometrical accuracy can be significantly higher. Figure), then drops to a value of 1.0. The first compensated (tool)geometry is called C1, and with this geometry a new FE simulation is displacement on this part is visualized in Figure 6. carried out. The resulting springback mesh S1 and the The maximum shape deviation amounts 22mm, outer (fixed) reference mesh R are used to modify C1, body panels are not necessarily very rigid. delivering the second compensated geometry C2. This is expressed by the following equation: C n+1 = C n ! (S n ! R) (4) Iterative DA was applied to the analytical model. As the optimal compensation factor varies considerably for various levels of tension force, it was expected that the speed of convergence is also different for different loads. Fig.6 The VW front fender and springback deformation The displacement field of the nodes in the blank- mesh are used as input for the DA algorithm. In [5] it is described how a smooth function is used to be able to extrapolate the shape modification field outside the blank area. This is necessary as the deep drawing tools are larger than the blank, and the meshes are th topologically different. Many other functionalities Fig. 5. Shape error for various tension strains in the 5 iteration were added to make the compensated tools From Figure 5 it can be concluded that iterative practically usable. For example, the gap width compensation is much more effective when the between the tools is maintained precisely, and tension strain is so large that the entire bar is under possible undercuts in the tools are prevented for. The plastic deformation. Note that in the graph the shape extended version of the algorithm is referred to as error (at the end of the bar) was normalized by the Smooth DA or SDA. shape error of the uncompensated forming process, because with increasing tension springback is reduced considerably. So, iterative DA compensation is most effective in areas with much plastic deformation, whereas springback is the largest in areas with dominantly elastic deformation. This might be a problem in low- strain areas in a product, for example in car roof panels. The analytical model has provided great insight in the behaviour of the DA algorithm. However, it should be stated that the analytical model on which these results are based is a gross simplification, especially since compensation is carried out via the displacement at the end of the bar only. In real processes, the entire tools are compensated. 4 APPLICATION TO AN INDUSTRIAL PART The DA algorithm was tested on an industrial part, a front fender supplied by Volkswagen. The fender is Fig.7 Shape deviation for one-step (top) and iterative DA produced with a regular deep drawing process, The results of the iterative compensation are shown followed by a trimming operation. The springback in Figure 7 (bottom). The maximum shape deviation was reduced from 22mm to 2.1mm, in most parts of of iterative SDA (Fig. 7 bottom) are much better than the product even below 0.25mm. the one-step results (Fig. 7 top), there is no one optimal compensation factor for the entire product. As the DA process is carried out individually for each node in the blank mesh, the compensation After several iterations, the direction of the shape varies over the product.
Details
-
File Typepdf
-
Upload Time-
-
Content LanguagesEnglish
-
Upload UserAnonymous/Not logged-in
-
File Pages4 Page
-
File Size-