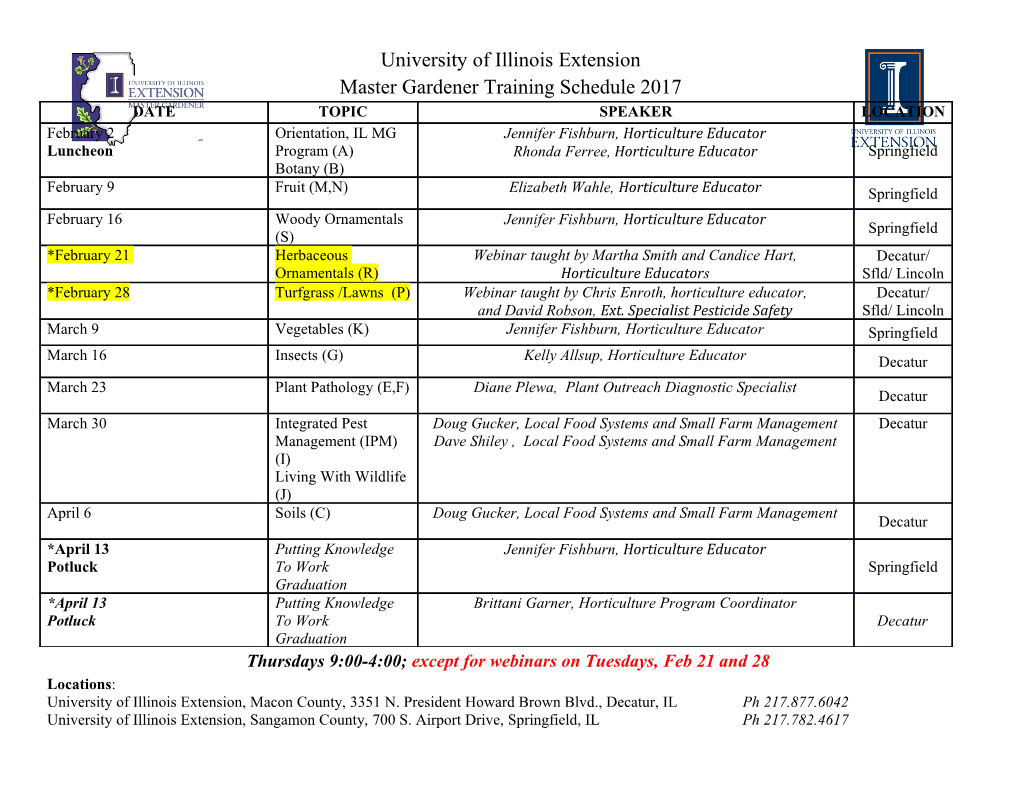
14th International Planetary Probes Workshop Overview of the ASPIRE Project June 12-16, 2017 - The Hague, NL. Clara O’Farrell, Ian Clark & Mark Adler Jet Propulsion Laboratory, California Institute of Technology © 2017 California Institute of Technology. Government Sponsorship Acknowledged. ASPIRE Disk-Gap-Band (DGB) Parachute Heritage MSL (2012) MER (2004) • Developed in the 60s & 70s Viking (1974) for Viking – High Altitude Testing – Wind Tunnel Testing – Low Altitude Drop • Successfully used on 5 Mars missions – Leveraged Viking development Viking BLDT Test MER Drop Test MSL Wind Tunnel Test Image credit: mars.nasa.gov June 12-16, 2017 14th International Planetary Probes Workshop 2 jpl.nasa.gov Aerospace in recent DGB designs: Clark & Tanner, IEEE Broadcloth stress Conference Paper 2466 (2017): (per unit length) Broadcloth ultimate load estimated by treating the disk as a pressure vessel: Disk diameter have been eroding jpl.nasa.gov 3 180 Actual Flight Load ASPIRE 160 Parachute Design Load Broadcloth Ultimate Load DGB Heritage & Design Margins Strength margins may 140 f b l 120 • 3 0 1 x , 100 d a o L e 80 t u h c a r 60 a P 40 parachutes well below those achieved in supersonic tests 20 stresses seen in subsonic testing may not bound the 14th International Planetary Probes Workshop -Densityringsail Supersonic0 Decelerators Project saw failures of two 9. 19 12 12 12 S V V V V P S O P M 1 . P ik ik ik ik at pi p ho S m 7 2 2 2 E i i i i h r p e L m m m m D n n n n f it o n M - g g g g in rt i 1 M M M M II A A I I d u x . 1 1 2 3 V V I e n 5 . r it 6 5 9 7 3 - - y 9 1 2 1 1 4 The Low • supersonic LDSD experience • stresses seen in supersonic testing, at least for some parachutes -16, 2017 June 12 ASPIRE The ASPIRE Project • Advanced Supersonic Parachute Inflation Research Experiments Project established to investigate the physics of supersonic DGB inflation • DGBs to be tested on sounding rocket flights out of Wallops Flight Facility (WFF) starting summer 2017 • Expose two candidate M2020 parachute designs to a supersonic inflation environment Payload Sep Mortar Fire L+104 s L+160-170 s Alt: ~50 km Alt: 39-45 km Mach: 1.8 q∞: 360-820 Pa Line Stretch Mach: 1.65-1.9 MF+~1 s q∞: 400-930 Pa Mach: 1.68 2nd stage Brant burnout L+35.5 s Alt: 16.7 km Peak Load Mach: 3.2 MF+~2 s q∞: 400-900 Pa Mach: 1.64 2nd stage Brant Ignition L+8.0 s Alt: 1.5 km Nosecone Jettison Alt: 3 km 1st stage Terrier burnout L+5.2 s Alt: 0.7 km WFF Launch Site Splashdown Atlantic Ocean L + ~30 min ~60 -100 km jpl.nasa.gov ASPIRE Test Architecture st a l l a • Rail-launched Terrier Black Brant Ballast b (jettisoned before • Spin-stabilized at 4 Hz splashdown) • Yo-yo de-spin after 2nd stage Payload (7.54 m) burnout Buoyancy Aid (foam) & m a • Mortar-deployed full-scale DGB o electronics f • Cold gas ACS active from payload separation to before mortar fire Telemetry (sealed) cs i n o 17. 7 m vi • Recovery aids: a – Foam provides buoyancy – Nosecone ballast (for aerodynamic 2nd Stage Black Attitude Control Brant IX stability) is jettisoned before System S AC BLACK BLACK BRANT (5.89 m) splashdown m a o f • Payload mass: / Experiment r a – Launch: 1268 kg rt mo / e – Post-separation: 1157 kg t u ch – Splashdown: 128 kg ra a 1st Stage Terrier Aft transition & p (4.3 m) separation Hardware TERRIER TERRIER r e De-spin hardware t p a d a June 12-16, 2017 14th International Planetary Probes Workshop 5 jpl.nasa.gov ASPIRE Parachutes Test two full-scale mortar-deployed DGBs: • MSL built-to-print • Strengthened version of MSL DGB with a stronger broadcloth MSL built-to-print Strengthened D0 21.35 m 21.45 m SL length 37.0 m (1.73 D0) 36.44 m (1.70 D0) Riser length 7.05 m 7.78 m Geometric Porosity 12.5% 12.5% No. of gores 80 80 SL line material 2100 lb Technora 3500 lb Technora Band fabric PIA-C-7020 Type I Custom nylon Heathcoat Ltd. Disk fabric PIA-C-7020 Type I (skirt)/Polyester 8860 (crown) (1.86 yd/oz, 100 lbf/in) Radials 2100 lb Technora 3500 lb Technora Mass 49.8 kg 75.4 kg Fabric permeability 100 cfm 90 cfm June 12-16, 2017 14th International Planetary Probes Workshop 6 jpl.nasa.gov ASPIRE Schedule & Test Matrix • Top Level Objectives • Expose two candidate designs to a supersonic inflation environment • Acquire data sufficient to characterize the flight environment, loads, and performance of the parachute • Baseline strategy requires four successful flights: Parachute Load Purpose Target date SR01 35 klbf Ensure test approach doesn’t introduce Built-to-print Sept. 19, 2017 (MSL @ Mars) new parameters. SR02 Ensure strengthened design survives 35 klbf Strengthened MSL load; calibrate targeting for next two Nov. 1, 2017 (MSL @ Mars) flights SR03 Strengthened 70 klbf Strength test of new design Dec. 19, 2017 SR04 Strengthened 70 klbf Address testing variability Feb. 4, 2018 SR05 TBD SR06 • Six flights planned to provide margin on four required tests June 12-16, 2017 14th International Planetary Probes Workshop 7 jpl.nasa.gov ASPIRE Instrumentation Experiment section: 3x load pins at triple- Instrument Ring: bridle attachments Parachute Pack Mortar Tube Instrument Ring 3x HS/HR cameras 3x SitVid cameras for stereo imaging • Additional on-board instrumentation: – GLN-MAC IMU – GPS – C-band transponder (radar tracking) • Meteorological instrumentation: – 3x meteorological balloons carrying Radiosondes: temperature, density, winds to 35 km – 2x SuperLoki rockets w/inflatable ROBIN spheres: temperature, density, winds for 30 - 60km • Allow reconstruction of: – Parachute loads – Conditions at parachute deploy (Mach, dynamic pressure, angle of attack) – Parachute shape & position • See B. Sonneveldt et al “Instrumentation and Reconstruction for the ASPIRE Supersonic Parachute Test Campaign” (poster) June 12-16, 2017 14th International Planetary Probes Workshop 8 jpl.nasa.gov ASPIRE ASPIRE Data Products & Success Criteria • Data products: • Payload trajectory from separation until mortar fire + 60 sec: position, velocity, acceleration, attitudes rates • Payload aerodynamic states trajectory from separation until mortar fire + 60 sec: Mach, dynamic pressure, angles of attack, sideslip • Synchronized parachute load history • Synchronized HS/HR camera imagery • Parachute inspection report • Minimum success criteria • Deliver the experiment to the required test conditions. • Acquire, transmit, and record the required experiment data. • Recover the experiment section without recovery induced damage to the data. • Recover sufficient data to determine the parachute peak load, assuming proper payload functionality. • Comprehensives success criteria • Recover the parachute assembly (that remains attached to the experiment section) without recovery-induced damage. June 12-16, 2017 14th International Planetary Probes Workshop 9 jpl.nasa.gov ASPIRE Acknowledgments The authors are grateful for the many contributions from the ASPIRE team. Project Manager: Tom Randolph Deputy Project Manager: Mike Hughes Project Manager Emeritus: Mark Adler Principal Investigator: Ian Clark Parachute CogE: Chris Tanner Flight Performance (JPL): Mark Ivanov Flight Performance (LaRC): Eric Queen Aerosciences: Suman Muppidi Sounding Rocket Lead: Brian Hall NSROC Mission Manager: Jay Scott WFF Range Lead: Dave Wilcox This research was carried out at the Jet Propulsion Laboratory, California Institute of Technology, under a contract with NASA. June 12-16, 2017 14th International Planetary Probes Workshop 10 jpl.nasa.gov jpl.nasa.gov.
Details
-
File Typepdf
-
Upload Time-
-
Content LanguagesEnglish
-
Upload UserAnonymous/Not logged-in
-
File Pages11 Page
-
File Size-