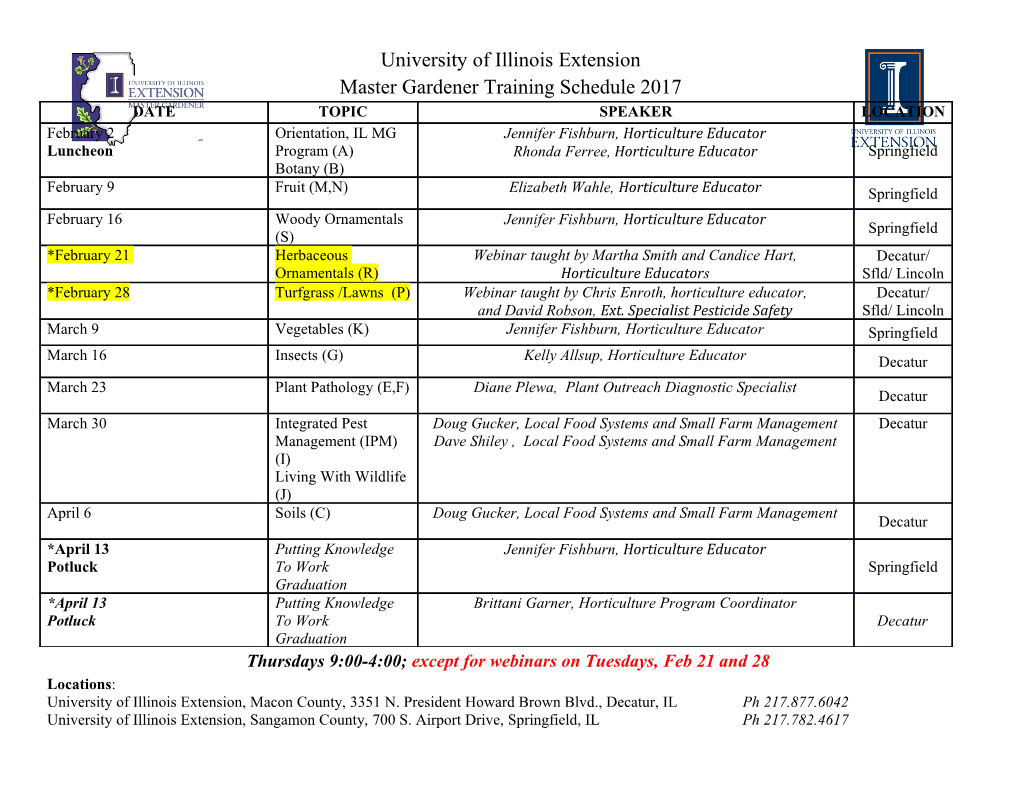
SERl/TP-252-2569 UC Category: 62a DE85000534 High Temperature Sensible Heat Storage Options K. Y. Wang (Solar Energy Research Institute) F. Kreith (Solar Energy Research Institute) R. E. West (University of Colorado) P. Lynn (P. P. Lynn, Inc.) November 1984 Prepared for the Solar Energy 1985 ASME/ASES Conference Knoxville, Tennessee 25-29 March 1985 Prepared under Task No. 4253.11 FTP No. 455 Solar Energy Research Institute A Division of Midwest Research Institute 1617 Cole Boulevard Golden, Colorado 80401 Prepared for the U.S. Department of Energy Contract No. DE-AC02-83CH10093 ·. Printed in the United States of America Available from: National Technical Information Service U.S. Department of Commerce 5285 Port Royal Road Springfield, VA 22161 Price: Microfiche A01 Printed Copy A02 NOTICE This report was prepared as an account of work sponsored by the United States Government. Neither the United States nor the United States Department of Energy, nor any of their employees, nor any of their contractors, subcontractors, or their employees, makes any warranty, express or implied, or assumes any legal liability or responsibility for the accuracy, completeness or usefulness of any information, apparatus, product or process disclosed, or represents that its use would not infringe privately owned rights. HIGH TEMPERATURE SENSIBLE HEAT STORA GE OPTIONS K. Y. Wang F. Kre ith SOLAR ENERGY RESEARCH INSTITUTE Golden, Colorado 80401 R. E. West Department of Chemical Engineering University of Colorado Boulder, Colorado 80309 P. Lynn P. P. Lynn, Inc. Boulder, Colorado 80302 ABSTRACT transfer becomes significant. Transpare nt liquid salt offe rs no resistance to ra diant transfer, and ra diation for Alkali-metal ca rbonate salts meet the requirements between a hot ce iling and a cooler bottom can induce high temperature solar ce ntral re ceiver systems, but convection currents that destroy the thermocline . Two due to their corrosiveness, spe cial problems arise in ways of re ducing ra diant transfer and maintaining a the design of storage ta nks. In pa rticular, to reduce. thermocline are : a "raft" that us es a disc and is corrosion and temperature sufficiently to re tain impervious to radiation with a de nsity ·between that of stre ngth in the containing wall, internal thermal the hotter a11d colde r storage liquid so that it floats insulation is required. This pa pe r prese nts design between them, and a two-me dia system consisting of a options and operation crite ria for se nsible heat molten pa cked be d of nontransparent solid particles with the salt storage with inte rnal insulation. liquid me dium occupying the interparticle voids. The INTRODUCTION two-me dia concept has be en used at Solar One, the 10 MW central rece iver power plant in Barstow, Calif., at e o 4 An energy storage subsystem is important for the con­ temperatures up to 3oo c and as phase change thermal 5 tinuous operation of solar central receiver systems 1. storage at temperatures up to soo0c , whereas the ra ft Copeland et al.2 identified a pote ntially large indus­ concept has be en de monstrated only at near ambient 6 trial market for solar systems able to deliver heat at conditions . aFproximately 900°c, preliminary cost estimates for some high-temperature storage concepts were also made, A study has been conducted at the Solar Energy Research and established syste m design and performance Institute (SERI) to identify the most promising high criteria. Using a nominal thermal storage temperature temperature storage conce pts, considering corrosion of 900°c and conside ring power generation efficiency, resistance, strength at high te mperature, reliability 6 material properties, solar thermal collector per­ of pe rformance of the te chnical concept, and cost . A formance, and other issues, they conclude d that molten summary of the material properties and costs used in salts are the storage me dium with the fewest te chnical this study are shown in Table 1. A storage capacity of 1800 MWh (e.g., 300 MW for 6 h) was selected and a problems and among them alkali-metal ca rbonate sa lts 'iih t.h show the most promise when cost and corrosiveness are maximum eat-loss ra te or- 2%/day (36 MWh/day, 1. 5 MW) taken into account. The lithium-sodium-potassium ca r­ was specified. The quantity of Li-K-Na eutectic .S 6 bonate eutectic mixture (approximately 1/3 wt. fraction required for this thermal capacity is about 7 x 10 3 each) was se lected for this study be cause of its low kg (8.2 x 10 tons) and the volume of the medium is 3 3 melting point (397° C), good stability at higher tem­ about 3.6 x 10 m with ta nk dimensions of approxi­ peratures, and re latively low corrosiveness. With this mately 8 m in depth by 24 m in diame ter for a salt mixture, a lower operating temperature of 42S° C is cylindrical storage vessel. Corrosion measurements attainable, providing a 42S0c to 900°c overall te m­ have been made for the mate rials used in the various perature swing for sensible heat stor�ge. designs and the available data are summarized in Refs. 2 and 6. There are two ge neric types of the rmal storage ta nk designs: a two-tank system, with one tank for the hot­ ter fluid and a second for the colder fluid or a DESIGN <l>NCEPTS single-tank, thermocline system, in which the de nsity difference between the hot and cold fluids inhibits In this section the characteristics of ra ft thermocline conve ctive mixing and heat transfer. Thermocline syste ms, two-tank systems, and two-me dia thermocline storage has been proven for lowe r-te mperature systems are discussed. Only one typical design for systems, 3, 4 but a unique problem occurs with thermo­ each system will be presented. Additional information clines at highe r te mpe ratures because ra diant heat ca n be found in Ref. 6. 1 2 T_P_-__5__ $5�1 ,.1 ---------------------------------------- 6 9 Table !. Properties of Materials for Molten Carbonate Salt Storage Thermal Conductivity k, Heat Capacity Cp, Density, p ) Price Material 3 3 W/m•K (x 0.578 .. Btu/hr•ft•°F kJ/kg•K (x 0.239 = Btu/lb Op) kg/m (x 0.062 = lb/ft ) $/kg @900°c unless noted Mean, 400-900°C Refractories 3 High Purity 3.8 x 10 12.1@ 4000C 1.2 5.5 Alumina (99.8%) 6.3 @ aoooc 3 High Purity 2.9 x 10 4.1 (dry) 3.5 Alumina Bricks, 4.4 (wetted with carbonates) ($10,000/m3) filled with MgO powder 3 Alumina Bricks 3.0 x 10 l. 7 1.6 (95.1%) Magnesia (95.5) 3 Bricks 2.6 x 10 z.3 !.25 1 •.1 Powder 2.3 x 103 (bulk) 2.0 1.25 0.33 Pellets 2.1 x 103 (bulk) 1.8 1.25 0.66 Concrete Ordinary struc­ 1.9 x 103 1.4 0.072 tural concrete ($135/m3) Ordinary insulating 0.8 x 103 0.33 0.45 concrete ($360/m3) 3 Castable Refractory 1.2 x 10 0.27 o. 57 ($680fm3) Salt --zN"a-K-Li) 2 C03 !.03 Eutectic Insulations Mineral Fiber Blanket (200°C max .. ) 0.051 (!OODC) $9.5/m2 (O. lm) Board ( 9aooc max.) 0.116 (4000C) $25./m2x(O. lm) 3 Calcium Silicate .58 x 10 0.126 (2Q00C) $45./mZx(O.lm) Board (65o0c max.) Diatomaceous Earth (looo0c max.) 0.13 (5400C) $4.3/mZ(O. lm) Raft 'lbermocline System The g1meral features of a raft thermocline system are shown in Fig. 1. and a suitable sidewall design concept is shown in Fig. 2. This sidewall has an inner layer of high-purity, fused-cast-alumina bricks that can 1r1ithstand 900°C molten carbonates, but is very expen­ 7 sive . Across the insulating bricks the temperature decreases to below about 8S8°c, the melting point of sodium carbonate, 1r1hich is a component of the insulation layer. The metal serves as a diffusion bar­ rier, not a structural member. The diffusion barrier consists of overlapping, but not joined sheets of Inconel. These will inhibit but not entirely prevent movement of the molten salt into the next layer, a pel­ leted magnesia insulation. The vertical Inconel sheets in place by horizontal bars anchored in the are held i'ig. 2 Single-tank raft thermocline system with alumina bricks and pellet insulation. outer structural wall. Sodium carbonate powder fills the voids between the magnesia pellets. As molten salt penetrates through the alloy diffusion barrier into the magnesia/ Na 2co3, it cools and dissolves NazC03 and increases its melting point. Thus, the salt will solidify after some distance preventing further liquid penetration, and preventing further dissolution of sodium carbonate. The raft itself is envisioned to be similar in design to the sidewall, but ballasted to float at the thermocline. Table 2 sho1r1s result.s of preliminary design and cost estimations for this concept. Optimistic and pessi­ Fig. l Single-tank storage concept . mistic refer to thermal performance and materials cost 2 s=�• TP-2569 Table 2. Cost Summary for Diffusion­ Hot Tank CoJdT•nll Barrier Raft TI!.ermocline (5a1ttromnea1e11:cnanger1ore<:e1ver1 �Floolstructure System (Figure 2) / _, Optimistic Inves ment Percentage Item G (10 $) of Total Sidewall 9.6 31.0 .. : -· Raft 3.1 10.0 . �:: � Top 1.3 4.0 Stde in1ern��:��1;1�:� j ; Bottom 0.4 1.0 1 ts FloOr1nsulat1on J Medium 16.3 54.0 "'�., .. , '"�'9"°l"'' '�·�· Total 3Q.T (17.1 $/kWh) 100.0 &��''• �'·��•<Q@<l HU'�·�· Fig.
Details
-
File Typepdf
-
Upload Time-
-
Content LanguagesEnglish
-
Upload UserAnonymous/Not logged-in
-
File Pages10 Page
-
File Size-