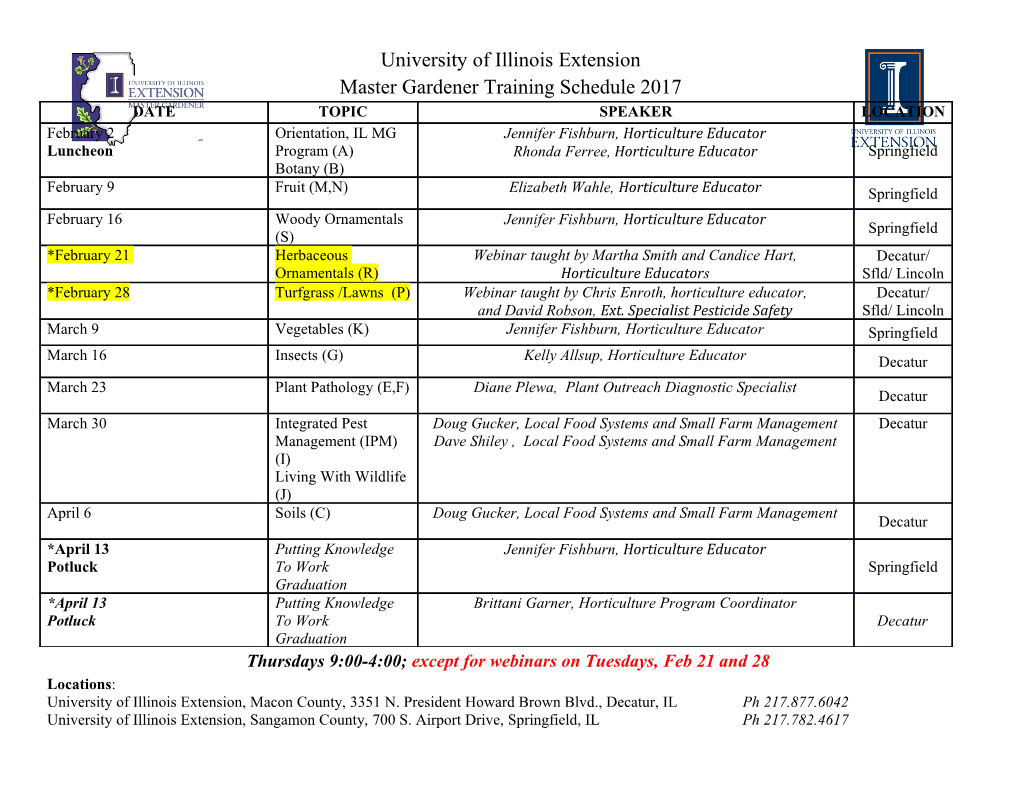
International Journal of Innovative Research in Advanced Engineering (IJIRAE) ISSN: 2349-2163 Issue 09, Volume 4 (September 2017) www.ijirae.com NANO SILICA IN INORGANIC POLYMER CONCRETE K. Kalaivani., Ph.D., Research Scholar Environmental Technology Division Central Leather Research Institute, Adayar, INDIA Manuscript History Number: IJIRAE/RS/Vol.04/Issue09/SISPAE10104 Received: 20, August 2017 Final Correction: 30, August 2017 Final Accepted: 05, September 2017 Published: September 2017 Editor: Dr.A.Arul L.S, Chief Editor, IJIRAE, AM Publications, India Copyright: ©2017 This is an open access article distributed under the terms of the Creative Commons Attribution License, Which Permits unrestricted use, distribution, and reproduction in any medium, provided the original author and source are credited. Abstract-- Nanoparticles are defined as those materials whose scale length lies within the nanometric range, i.e. from one to a hundred nanometers. Within this scale length, the properties of matter are considerably different from the individual atoms, molecules and bulk materials. The physical, chemical of these materials are different depending on the size and shape and they exhibit different important bulk properties. These properties of the nano materials have attracted many researchers in various fields to establish a new trend in the research from material science to genetics etc. This interest has been stimulated by the large variety of applications in industries such as fabrication of ceramics, sensors, batteries, capacitors, corrosion-resistant coatings, thermal barrier coatings, solid electrolytes for fuel cells, catalysts, cosmetics, health, automotive, bioengineering, optoelectronics, computers, civil and electronics etc. Currently, the importance of nanomaterials in the field of civil has increased; especially they exhibit enhanced structural strength. Nanoparticles and nanorods of several ceramic materials have been produced which can be utilized as building material in civil works. More recent studies have revealed that flyash based inorganic polymers has much compressive strength and easy workability at different site can be utilized as new concrete. This inorganic polymer concrete includes less emission of carbon dioxide; a more efficient use of mineral and metal resources; increase the use of recycled materials and issues of long-term durability. As the flyash mainly contains silicates of aluminum, addition of nano silica to these might increase the strength and density of concrete. This paper put forth its idea of incorporating nano silica with the inorganic polymer structures thereby increasing the strength and workability of the concrete. Key words: Nano Silica, flyash, inorganic polymer, characteristic properties, structure. I. INTRODUCTION Cement is a durable construction material produced by mixing clay and lime in fixed proportion. When mixed with water, aggregates and additives with special proportion concrete is obtained. High consumption of concrete causes vast requirements of cement production. Portland cement is used as a binder in the production of concrete. It is produced by mixing selected raw materials like clay and lime with a given proportion, grinding and heating it at high temperature of nearly 1500 ˚C. In the process of producing 1 tonn cement, 150 lit fossil fuel and 125 KWH electricity is consumed while cement transportation is 12% percent of the country roads transportation (Vazinram and Khodaparast, 2009). Unfortunately, the production of Portland cement releases large amounts of CO2 into the atmosphere and this gas is a major contributor to the greenhouse effect and the global warming (Bilodeau and Malhotra, 2000). Hence a new type of inorganic polymers are introduced to reduce the consumption of cement. These inorganic polymers are capable of reducing cement consumption decreasing the production of cement thereby reduction in environmental impacts to move toward sustainable development which is defined as the optimum usage with correct and efficient operation of basic and natural resources for providing the requirements of the future generation. _________________________________________________________________________________________________ IJIRAE: Impact Factor Value – SJIF: Innospace, Morocco (2016): 3.916 | PIF: 2.469 | Jour Info: 4.085 | ISRAJIF (2016): 3.715 | Indexcopernicus: (ICV 2015): 47.91 IJIRAE © 2014- 17, All Rights Reserved Page -58 International Journal of Innovative Research in Advanced Engineering (IJIRAE) ISSN: 2349-2163 Issue 09, Volume 4 (September 2017) www.ijirae.com Inorganic polymers were first discovered by Professor V.D. Glukhovsky of the former Soviet Union during 1950s and was given the name ‘soil cements’. A French man by the name of Davidovits began similar work in the 1970s naming these materials as ‘geopolymers’, which refers to an amorphous “inorganic polymer” formed through the ionic bonding reaction between an aluminosilicate (Al-Si) material and a strong alkaline solution (Sodium hydroixide or potassium hydroxide) (Tavor et al. 2007). Inorganic polymers are synthesized from a variety of aluminosilicate sources such as polysilicates, zeolites, kaolin, metakaolin, calcium, rocks, silica, fly-ash, blast furnace slag, phosphate and organic minerals. More than 70% of the earth crust consists of Al-Si minerals and use of lesser amounts of calcium-based cement do not release large quantities of CO2, so it is most useful to understand how these minerals convert to cement (Davidovits, 1994). For inorganic-polymeric cement production, no temperature higher than 750 degree centigrade is ever needed. The above fuel requirement is very less needed for this kind of cement production. Therefore inorganic-polymeric cements never rely on the calcinations of calcium carbonate, not require high temperature kilns, with large expenditure of fuel, so the chemical process and fuel much less reduce the carbon dioxide production for geopolymeric concrete manufacture. The amalgamation of nano materials like nanosilica with flyash is immensely used in the concrete field. Nanotechnology in concrete has increased the life of concrete, create fire-resistant materials and give high qualities to building materials such as “self-healing” and “self-cleaning.” II. COMPOSITION OF CONCRETE Fly Ash Fly ash is one of the most abundant materials on the earth which is also a crucial ingredient in the creation of inorganic polymer concrete due to its role in the geopolymerization process. Fly ash is a powdery pozzolan material. A pozzolan is a material that exhibits cementitious properties when combined with calcium hydroxide. Fly ash is the main byproduct created from the combustion of coal in coal-fired power plants and there are two types of fly ash Class F and Class C. Each type of fly ash has its own unique properties. Class F fly ash is created from the burning of either anthracite or bituminous coal. [toolbase.org]. This Class of fly ash has little to no self- cementing properties and contains very little calcium oxide. In Class C fly ash, on the other hand, is produced through the combustion of lignite or sub bituminous coal. Fine Aggregates In concrete mix, aggregates occupy between 60% to 80%. This high content of aggregates influences the properties of inorganic polymer concrete both in the fresh and hardened state. Therefore, they must be well selected. Aggregate is classified as two different types, coarse and fine. Coarse aggregate is usually greater than 4.75 mm while fine aggregate is less than 4.75 mm. Fine sand was collected from local river sand having specific gravity of 2.67 and fineness modulus 2.75, water absorption 0.81%. Unit mass (W) 1425 kg/m3. The sand is sieved using IS sieves of sizes 1.18 mm, 600 micron, 300 micron,150 micron and 75 micron. These size fractions are combined in equal proportion to maintain grading complying with standard sand as per IS 650:1991. Alkali Sodium hydroxide pellets (98 percent purity) of 8M concentration is used for the experimental analysis. This solution is prepared by using 320gm by mass of NaOH dissolved in 1litre of distilled water. Sodium Silicate Sodium silicate solution (Na2O= 8%, SiO2 =26.5% and 65.5% water) with silicate modulus ~ 3.3 and a bulk density of 1410 kg/m3 is used. The alkaline activating solution was a mixture of sodium hydroxide and sodium silicate solution. Admixture In order to improve the workability of the inorganic polymer concrete, high-range water-reducing super plasticizer is added to the mixture. The polymer admixture used for experimental analysis is sulphonated naphthalene formaldehyde. Silica Nano Particles As reported, the preparation of silica nanoparticles is done by Sol - Gel - Synthesis –precipitation method. The chemical reaction involved in this method is hydrolysis –polycondensation. When tetra ethyl orthosilicate in ethanol is hydroysed at a pH range of 11-12, silicon tetraoxide is formed. This silicon tetra hydroxide on poly condensation, nano silica is obtained. This nano silica is dried, powdered in ball milling and again dried at 120 C in oven and used as nano silica powder. A specific gravity of 2.2-2.4 at 25 °C, bulk density of 0.068 g.mL–1, average particle size of 15 nm and specific surface area of 640m2.g–1 were the listed physical properties of this batch of nano silica(.nanoamr.Europe) Silicates and Silicate Structure of Inorganic Polymer In classifying silicates, distinct silicate or aluminate anions are the basic unit of constitution. This fundamental unit is a tetrahedral
Details
-
File Typepdf
-
Upload Time-
-
Content LanguagesEnglish
-
Upload UserAnonymous/Not logged-in
-
File Pages5 Page
-
File Size-