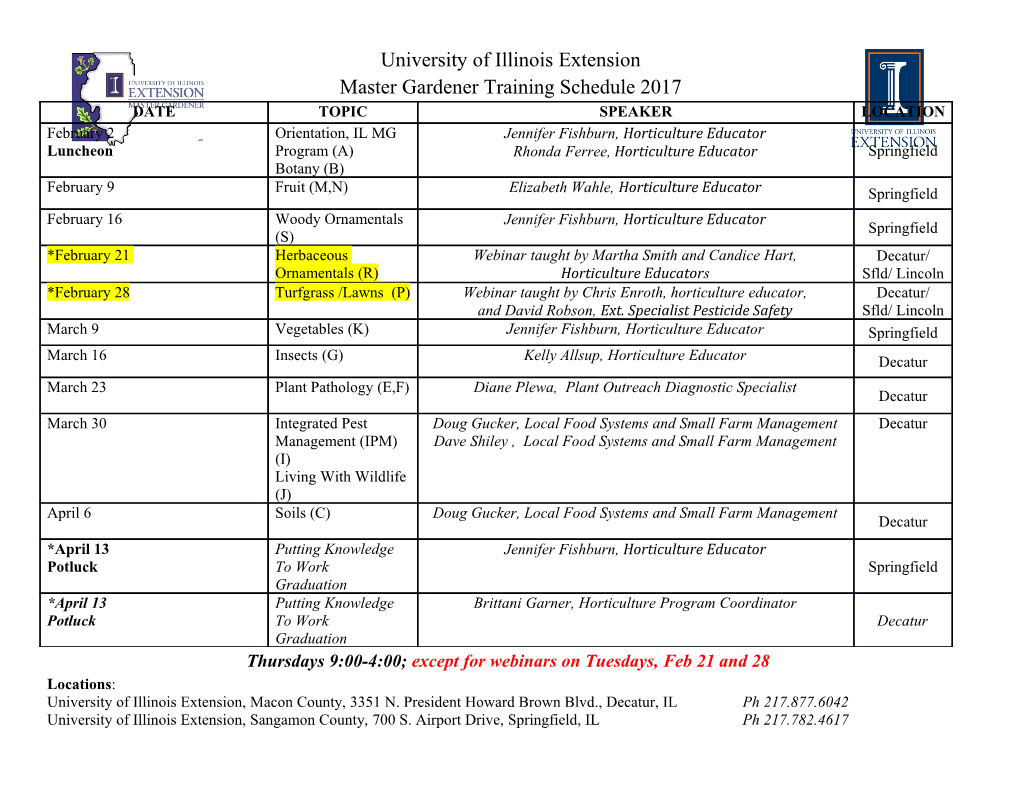
S S symmetry Article Determination of Young’s Moduli of the Phases of Composite Materials Reinforced with Longitudinal Fibers, by Global Measurements Renata Ildikó Szavá 1, Ioan Szavá 2, Sorin Vlase 2,3,* and Arina Modrea 4 1 Autolive SA, B-dul Eroilor, 20, 500036 Bras, ov, Romania; [email protected] or [email protected] 2 Department of Mechanical Engineering, Transilvania University of Bras, ov, B-dul Eroilor, 20, 500036 Bras, ov, Romania; [email protected] 3 Romanian Academy of Technical Sciences, Bucharest, B-dul Dacia, 26, 030167 Bucharest, Romania 4 Farmacy, Science and Tehnology George Emil Palade of Tg, University of Medicine, 517519 Mures, Romania; [email protected] * Correspondence: [email protected] Received: 11 August 2020; Accepted: 19 September 2020; Published: 27 September 2020 Abstract: The properties of a composite material are determined by the properties of the constitutive materials. In engineering practice, there are many situations in which we have composite material, but we do not have information about the properties of each phase component. The measurements we can make in such cases are on the existing material, thus being able to determine, experimentally, the global physical properties of the composite. The possibility of realizing an estimate of the mechanical properties of each component poses a problem if we start from these measurements. The paper proposes a method to achieve this, starting from the theoretical estimates established in the literature, then illustrated by an example to determine the properties of wood. Wood is a transverse isotropic material and therefore the constitutive law has symmetries that are manifested in the decrease of the number of parameters that define the stress-strain liason, defined only by five independent parameters. The proposed method can be extended to a diversity of models and materials used in the study of composite materials. Keywords: composite; longitudinal fibers; mechanical measurements; early wood; late wood; Young’s modulus; Video Image Correlation 1. Introduction Composite materials are made up of two or more phases, to finally obtain a new material with better properties, at a lower price. The properties obtained are determined by the concentration of the components, the arrangement mode, the geometry, the shape, the layout, etc. A multitude of composite materials can be obtained, and their properties can vary in an extensive range. The analysis of composite materials composed of several firmly bounded (visco) elastic materials that on a macroscopic scale can be treated as a homogeneous, isotropic/transverse isotropic or orthotropic material has long been done in the literature [1]. In general, we know the engineering constants of the materials that are put together, we know the proportion in which they appear in the composite, and we want to determine the properties of the resulting composite material. To obtain the engineering constant values of the resulting material, different methods have been applied in the literature (variational methods, boundedness methods, homogenization theory, minimum theorems, etc. [2]). Thus, sometimes very precise values of the properties of the resulting material were obtained. The literature dealing with these issues is very rich and was developed in the sixth, seventh, and eighth decades of the 20th century. Symmetry 2020, 12, 1607; doi:10.3390/sym12101607 www.mdpi.com/journal/symmetry Symmetry 2020, 12, 1607 2 of 13 However, in many cases encountered in engineering practice, there are situations in which we have a composite material, but we do not have information on the mechanical properties of its components. Measurements can be made on the existing composite material, determining, with classical methods, the values of the main engineering constants. Thus, global measurements can be made on the material, without being able to separate and determine the properties of its components. However, there are situations when knowledge of these properties becomes necessary. The problem is, therefore, that, if the values of some sizes of the composite are known measurements, it is possible to determine the values of these sizes of the composite components. The information obtained by measurements should be useful for the mechanical identification of its components. To achieve this, appropriate theoretical models must be used that provide formulas for calculating the properties of the composite starting from the properties of its phases. The diversity of composite materials is enormous, and that is why we will deal with the situations encountered more often in engineering, namely that of macroscopically homogeneous multiphasic linearly elastic composites, representing the classic part in the study of micromechanics of composites. The aim of this domain is the characterizations of the macroscopic (overall) elastic behavior of the composite formed by a mixture of solid phases bounded together [2]. One of the phases is the matrix. The others are the inclusions (fibers in our study). The mixture becomes homogeneous at macroscale but is not necessary to be isotropic. Most of the studies consider the phases being too homogeneous and isotropic. For the study that will be undertaken in this paper, it is necessary to know the relations that allow obtaining, with sufficiently good precision, the overall elastic constants of the composite material depending on the elastic constants of the composite phases. At the macroscopic level, the composite can be treated using the mechanics of continua, as a homogeneous material. From a theoretical point of view, an analysis of a composite made by different phases with different geometries to determine the elastic state of the material is a very complex task and useless for practical applications. For this reason, the problem of knowing the strain–stress in detail of a composite is replaced with the problem of the study of a statistically homogeneous composite [3–5]. To do this is necessary to determine the overall moduli as functions on the mechanical properties of the phases, their geometry, and other parameters that can occur. Classical results are offered by Reuss and Voigt bound, but a rich literature presents numerous methods to compute these constants [6–23]. They can be used to determine the parameters of the phases using a set of measurements on the overall elastic parameters of the composite. Generally, the domain of macroscopically or statistically homogeneous composite materials, has as the main subject, the characterization of the macroscopic/overall/equivalent elastic behavior of a resulting material formed by two or more solid phases bounded together. The matrix represents one of the phases, the others being the inclusions. There are no restrictions on the shape of the reinforcements materials, which may be fibrous or spherical, as an example. It is considered that the mixture is homogeneous on a macroscale, but not necessarily isotropic. Their elastic engineering constants are different, and, as a consequence, the stress and strain fields through composite become microscopically inhomogeneous [24–28]. 2. Mathematical Method to Determine the Engineering Elastic Constants of Components Using Global Experimental Measurements Consider a characteristic parameter of the composite that we denote by E (the most commonly used size is Young’s modulus or bulk modulus but can be shear modulus or Poisson ratio). This quantity can be expressed in terms of other unknown mechanical characteristics of the component phases x1, x2, ::: xs and geometric known parameters p1, p2, ::: pr: E = g(x1, x2, ::: xs, p1, p2, ::: pr), k = 1, s (1) Symmetry 2020, 12, 1607 3 of 13 The parameter considered is a parameter that can be measured. For example, in the case of Young’s modulus, a traction–compression machine can be used. Video Image Correlation is another common method used to determine other elastic constants. For this, a large number of specimens will be manufactured to perform the measurements. Let us say we made n specimens and n measurements were made. In this case, Equation (1) becomes, for each measurement: j = ( j j j) = = E g x1, x2, ::: xs, p1, p2, ::: pr , k 1, s, j 1, n (2) From these measurements, we have the problem of determining a regression formula for (1), calculating the unknowns so that the last square S of the measured values from the values given by the regression function is minimum. If we denote: Xn h j j j j i2 S = E g(x , x , ::: xs, p , p , ::: p ) (3) − 1 2 1 2 r j=1 we obtain s equations: n j j j @S X h i@g(x1, x2, ::: xs, p , p , ::: pr) = j ( j j j)) 1 2 = = 2 E g x1, x2, ::: xs, p1, p2, ::: pr 0, i 1, s (4) @xi − @xi j=1 which can be written as: Gi(x1, x2, ::: xs) = 0, i = 1, s (5) Relation (5) represents a system of s equations with s unknowns. Solving this system, we can first determine the unknowns x1, x2, ::: xs, and we can establish the Regression Function (1) for parameter E. In this way, the unknown elastic constants of the component phases were determined. We mention that, generally, Equation (5) can be complicated, and it can be a difficult task to obtain solutions. 3. Determination of Young’s Moduli of a Multiphase Composite with Longitudinal Fibers 3.1. Using Measured Longitudinal Young’s Modulus From a theoretical point of view, any quantity can be determined by measurements, which appears in a theoretically determined formula for any engineering constant. If the formula in which this constant appears is relatively complicated, then, of course, the necessary calculations can be particularly complicated. The system of Equation (4) can be nonlinear and sometimes difficult to solve. In these situations, it is necessary to apply specific numerical methods to solve them. However, there are also situations in which equations can be solved relatively simply. The example presented is of an important mechanical constant in engineering, Young’s modulus (longitudinal and transverse).
Details
-
File Typepdf
-
Upload Time-
-
Content LanguagesEnglish
-
Upload UserAnonymous/Not logged-in
-
File Pages13 Page
-
File Size-