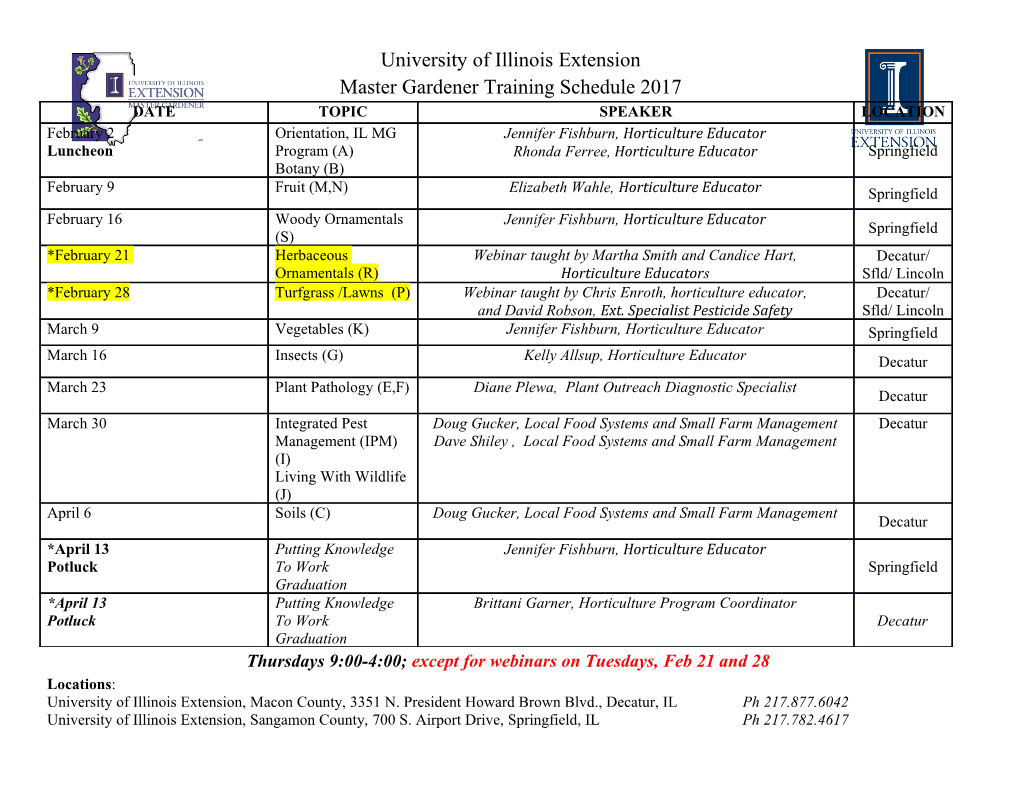
NASA/CR—2019–220236 Airfoil Selection for Mars Rotor Applications Witold J. F. Koning Science and Technology Corporation Ames Research Center, Moffett Field, California Click here: Press F1 key (Windows) or Help key (Mac) for help July 2019 This page is required and contains approved text that cannot be changed. NASA STI Program ... in Profile Since its founding, NASA has been dedicated CONFERENCE PUBLICATION. to the advancement of aeronautics and space Collected papers from scientific and science. The NASA scientific and technical technical conferences, symposia, seminars, information (STI) program plays a key part in or other meetings sponsored or co- helping NASA maintain this important role. sponsored by NASA. The NASA STI program operates under the SPECIAL PUBLICATION. Scientific, auspices of the Agency Chief Information technical, or historical information from Officer. It collects, organizes, provides for NASA programs, projects, and missions, archiving, and disseminates NASA’s STI. The often concerned with subjects having NASA STI program provides access to the NTRS substantial public interest. Registered and its public interface, the NASA Technical Reports Server, thus providing one of TECHNICAL TRANSLATION. the largest collections of aeronautical and space English-language translations of foreign science STI in the world. Results are published in scientific and technical material pertinent to both non-NASA channels and by NASA in the NASA’s mission. NASA STI Report Series, which includes the following report types: Specialized services also include organizing and publishing research results, distributing TECHNICAL PUBLICATION. Reports of specialized research announcements and feeds, completed research or a major significant providing information desk and personal search phase of research that present the results of support, and enabling data exchange services. NASA Programs and include extensive data or theoretical analysis. Includes compilations For more information about the NASA STI of significant scientific and technical data program, see the following: and information deemed to be of continuing reference value. NASA counterpart of peer- Access the NASA STI program home page reviewed formal professional papers but has at http://www.sti.nasa.gov less stringent limitations on manuscript length and extent of graphic presentations. E-mail your question to [email protected] TECHNICAL MEMORANDUM. Phone the NASA STI Information Desk at Scientific and technical findings that are 757-864-9658 preliminary or of specialized interest, e.g., quick release reports, working Write to: papers, and bibliographies that contain NASA STI Information Desk minimal annotation. Does not contain Mail Stop 148 extensive analysis. NASA Langley Research Center Hampton, VA 23681-2199 CONTRACTOR REPORT. Scientific and technical findings by NASA-sponsored contractors and grantees. NASA/CR—2019–220236 Airfoil Selection for Mars Rotor Applications Witold J. F. Koning Science and Technology Corporation Ames Research Center, Moffett Field, California National Aeronautics and Space Administration Ames Research Center Moffett Field, CA 94035-1000 July 2019 ACKNOWLEDGMENTS The author thanks Wayne Johnson, Larry Young, and Alan Wadcock for their helpful discussions while writing this paper. Available from: NASA STI Support Services National Technical Information Service Mail Stop 148 5301 Shawnee Road NASA Langley Research Center Alexandria, VA 22312 Hampton, VA 23681-2199 [email protected] 757-864-9658 703-605-6000 This report is also available in electronic form at http://ntrs.nasa.gov TABLE OF CONTENTS List of Figures ................................................................................................................................ iv List of Tables ................................................................................................................................. iv Introduction ......................................................................................................................................1 Low-Reynolds-Number Airfoil Performance ..................................................................................1 Performance Evaluation of Unconventional Airfoil Shapes ............................................................2 Conventional Airfoil ..................................................................................................................3 Tripped Airfoil ...........................................................................................................................3 Cambered Plate ..........................................................................................................................4 Corrugated Airfoil ......................................................................................................................4 Thickness Variation ...................................................................................................................5 Shape Optimization Efforts..............................................................................................................6 References ........................................................................................................................................7 iii LIST OF FIGURES Figure 1. Maximum lift-to-drag ratio versus Reynolds number. .................................................... 2 Figure 2. Minimum section drag coefficient versus Reynolds number. ......................................... 2 Figure 3. Various representative airfoil shapes versus Reynolds number. ..................................... 3 Figure 4. Performance of various airfoil shapes versus Reynolds number. .................................... 4 LIST OF TABLES 3 4 Table 1. Overview of candidate airfoil shapes evaluated for Rec = O(10 -10 ) ..............................5 iv AIRFOIL SELECTION FOR MARS ROTOR APPLICATIONS Witold J. F. Koning1 Ames Research Center INTRODUCTION This paper provides an overview of design considerations for airfoil choices with rotor applications in the Martian atmosphere, at very low chord-based Reynolds number flows, around 3 4 Rec = O (10 -10 ). The low Reynolds number typical of rotorcraft operation in the Martian atmosphere reduces the rotor lifting force and efficiency, which is only partially compensated for by a lower gravity on Mars compared to Earth. Additionally, the low temperature and largely CO2-based atmosphere of Mars compound the overall aerodynamic problem by resulting in a lower speed of sound, further constraining rotor operation in the Martian atmosphere by limiting the maximum rotor tip speed possible so as not to exceed an acceptable tip Mach number. In light of the expected reduced rotor efficiency, evaluation of airfoils for compressible, low- Reynolds-number Mars rotor applications is key. Prior research on airfoil optimization and performance evaluation at low Reynolds numbers, especially in the compressible regime, is scarce and further investigation is needed. Specifically, the proposed goal stemming from this overview is to develop airfoils tailored to the unique demands of the second generation of Mars rotorcraft, i.e. the Mars Science Helicopter (MSH). This research focuses on the airfoil performance at low Reynolds numbers and hopes to add to the work performed by Kroo et al.,1 Kunz and Kroo,2 Oyama and Fujii,3 Anyoji et al.,4–6 and others. LOW-REYNOLDS-NUMBER AIRFOIL PERFORMANCE McMasters and Henderson7 provide a summary of attainable airfoil lift-to-drag ratios over a wide Reynolds number range in Figure 1. Results are collected from a wide variety of experiments, mostly with conventional airfoil geometries. 3 4 At the Reynolds number range under consideration, Rec = O (10 -10 ), the boundary layer can be fully laminar up to the point of separation without subsequent (turbulent) flow reattachment or on-body transition. 1 Science and Technology Corporation, NASA Research Park, Moffett Field, CA 94035. 1 Figure 1. Maximum lift-to-drag ratio versus Reynolds number.7 Figure 2. Minimum section drag coefficient versus Reynolds number.7 The Reynolds number effect on the minimum airfoil drag coefficient is presented in Figure 2. The flow state in absence of laminar-to-turbulent transition is called subcritical and derives its relatively low efficiency because of (a) the increased pressure drag component from early separation, and (b), to lesser extent, reduced lift due to an effective camber reduction. The Reynolds number at which laminar flow over an airfoil begins to exhibit turbulent features (either due to on-body transition or turbulent reattachment) is called the critical Reynolds number. Reynolds numbers where turbulent transition always occurs before laminar separation, or during/after reattachment, are referred to as supercritical. Finally, compressible flow—versus incompressible airfoil flow—is not well understood for low- Reynolds-number airfoils. Limited experimental and computational work in the literature—and performed previously by the author8—suggests that conventional airfoil geometries exhibit Mach-number sensitivities whereas cambered, flat-plate airfoils seem to be insensitive to Mach number.4,6 PERFORMANCE EVALUATION OF UNCONVENTIONAL AIRFOIL SHAPES Overall airfoil performance changes with Reynolds number, especially the relatively poor performance (in terms of lift-to-drag ratio,7 minimum section drag,7,9 and maximum section 10 5 lift ) up to Rec = O (10 ), serves as the main motivation for (unconventional)
Details
-
File Typepdf
-
Upload Time-
-
Content LanguagesEnglish
-
Upload UserAnonymous/Not logged-in
-
File Pages14 Page
-
File Size-