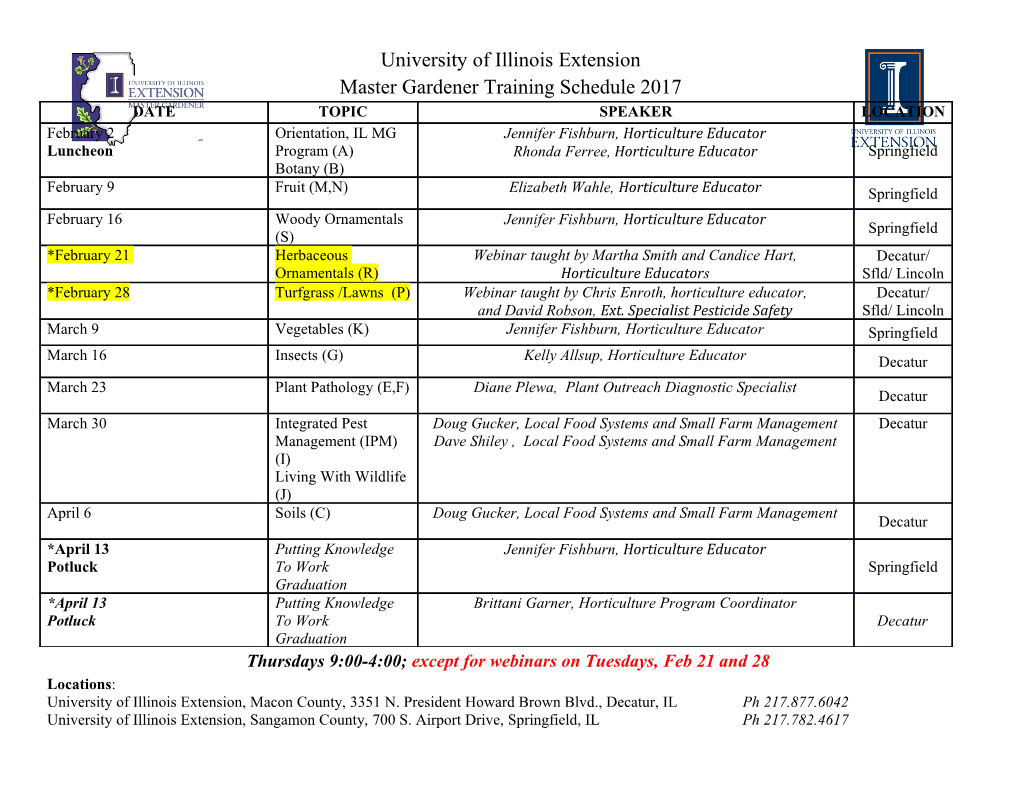
ECONOMICS OF ACID GAS REINJECTION: AN INNOVATIVE CO2 STORAGE OPPORTUNITY Sam Wong1, David Keith2, Edward Wichert3, Bill Gunter1and Tom McCann4 1 Alberta Research Council, Edmonton, Alberta, Canada 2 Carnegie Mellon University, Pittsburgh, PA, USA 3 Sogapro Engineering, Calgary, Alberta, Canada 4 McCann & Associates, Calgary, Alberta, Canada ABSTRACT Acid gas streams, consisting primarily of hydrogen sulfide (H2S) and carbon dioxide (CO2), are commonly generated as a by-product of the gas sweetening process used to bring produced gases and solution gases up to pipeline specifications for sales and transport. In the past, the conventional methods for acid gas disposal are to use a Claus process or to flare the acid gas. A new technology called acid gas reinjection has emerged over the past ten years in Canada as an effective way of ensuring that acid gases are not emitted into the atmosphere. There are 38 acid gas reinjection projects presently operating in Alberta. This technology involves compressing the acid gas and injecting it into a suitable underground zone, similar to deep well disposal of produced water. Essentially, the sulfur compounds and CO2 are permanently stored in the deep geological formation preventing their release to the atmosphere. Therefore most acid gas reinjection projects can be considered as existing examples of CO2 geological storage projects. These projects provide important practical experience with CO2 storage. In addition, this technology could be extended to capture a significant fraction of the natural gas-associated CO2 stream at low cost. In this paper, a cursory economic analysis is made on one of the Alberta acid gas reinjection projects relative to sulfur recovery for determining the amount of CO2 avoided. INTRODUCTION The capture of CO2 from the production and use of fossil fuels and its storage in geological formations may offer the ability to make early and deep reductions in CO2 emissions without abruptly abandoning our fossil-based energy infrastructure [1, 2, 3]. While the economics of CO2 mitigation are uncertain, to a rough approximation it appears that CO2 capture and storage (CCS) fills the gap between the lowest costs, most immediately available measures of CO2 mitigation, such as moderate energy efficiency improvements, and the higher costs associated with a transition to a non-fossil primary energy supply. Given its intermediate cost, one might expect that CCS technologies would play no role in achieving small, near term reductions in emissions. There is however an important, though limited, suite of technological niches where CCS technologies may be applied at low cost. The most important of these opportunities involve non-combustion sources of CO2. The cost of capturing CO2 and compressing it to the pressures required for geological storage (of order 100 atmospheres) is primarily dependent on the scale and purity of the CO2 stream to be captured. Combustion sources have CO2 concentrations of 5 to 15%; and for these dilute streams the cost of capturing CO2 dominates the cost of storage, accounting for perhaps 3/4 of the overall cost of CCS [4]. For non-combustion sources the cost of capture is smaller, and can be zero for sources of nearly pure CO2. Greenhouse Gas Control Technologies, J. Gale and Y. Kaya (Eds.) © 2003 Elsevier Science Ltd. All rights reserved Although the great majority of CO2 emissions arise from combustion, significant non-combustion sources of CO2 exist. In Canada, the three most important non-combustion sources of CO2 are natural gas processing, hydrogen production and ammonia manufacture. These sources have high concentration of CO2 and they in turn can provide important opportunities for early application of CCS technologies. This paper focuses on an application from the natural gas processing industry. ACID GAS REINJECTION Raw natural gas may contain significant impurities, with CO2, H2S, and N2 being the most important. “Sour gas” by definition is natural gas that contains H2S. In order to meet sales gas contract specification, sour gas must be treated for the removal of virtually all of the H2S. For very low H2S content (ppm level), disposable chemical such as SulfaTreat may be used to remove the sulfur. For higher H2S content, a chemical absorption process with amine may be used. Typically, the amine absorption method captures most of the CO2 in addition to the H2S. The resulting CO2 + H2S (acid gas) must then be processed to eliminate the H2S. The least cost method to eliminate H2S is to flare the acid gas stream burning the H2S to SO2 and releasing the CO2 to the atmosphere, along with the SO2. Over recent decades, concerns for the environmental effects of sulfur emissions have eliminated flaring as an option for all except the smallest facilities. Another option is to process the acid gas in a sulfur recovery unit such as a Claus plant, which produces sulfur as a salable byproduct, but releases the CO2 as before. In response to falling sulfur prices and increasingly stringent restrictions on residual SO2 emissions, the industry has recently begun to abandon sulfur recovery in favor of acid gas disposal. For the largest plants, the lowest cost route may still be sulfur recovery, but for plants with lower H2S fluxes the lowest cost option is to compress the full acid gas stream (CO2 and H2S) and dispose of it in a suitable geological formation (see Figure 1). Gas plant: Electricity NGL recovery, Sales gas output and other materials acid gas removal, NGL dehydration, Sour gas compression to Wastes and other emissions input pipeline pressure Electricity Electricity and other inputs Acid gas stream to AGI or Sulfur recovery CO and residual SO vented Acid Gas Injection: Sulfur recovery : 22 compression, dehydration Modified Claus or Sulfur to storage other process and injection Wastes and other emissions CO22 + HS to geological reservoir Figure 1. Schematic showing gas plant acid gas going to acid gas reinjection or sulfur recovery. The first acid gas reinjection operation in Alberta, Canada was started by Chevron Canada Ltd. in 1989 at Acheson, where 15% H2S and 85% CO2 were injected into a depleted oil pool. The number of injection sites in Alberta has since increased from 1 in 1989 to 11 in 1995, to 29 in 1998 and to 38 in 2002. There were another 6-8 acid gas reinjection sites in British Columbia, Canada. Acid gas compositions of the 38 Alberta projects range from 4-75% H2S and15-95%CO2, with minor amounts of C1+ gases making up the balance. The current average injection rates at all sites is ~0.4 Mt CO2/year. At 14 sites, acid gas is injected into depleted oil and gas reservoirs, while the remaining 24 sites into deep saline aquifers whose salinity reaches up to 340,000 mg/l. Injection depths vary between 700 and 2,920 m. The injection horizons, of which 14 are in sandstones and 24 in carbonate rocks, vary in thickness from 4 to >200 m. Acid gas reinjection involves three steps: compression, dehydration and injection. The acid gas exit from the amine absorption unit is saturated with water vapor. It is at low pressure and slightly above air temperature. The stream is sent to a compressor located at the plant, which boosts the pressure of the acid Greenhouse Gas Control Technologies, J. Gale and Y. Kaya (Eds.) © 2003 Elsevier Science Ltd. All rights reserved gas to the required injection pressure. The compressors are multistage reciprocating machines, mainly using four stages to boost the pressure of the acid gas to the required injection pressure level. The key to successful operation of injection facilities is the control of the water content. When the gas enters the injection line after compression, its water vapor content must be sufficiently low that the gas remains under-saturated in water content all the way to the bottom of the well. This can be done by dehydration during compression, or by appropriate inter-stage cooling if the final pressure is above about 7,000 kPa. Maintenance of the compressors is normal, similar to the maintenance requirement for sour gas compressors. Most injection lines are designed to operate at very low stress levels in the pipe. Emergency shutdown valves are installed at each end of the injection lines. The injection wells are equipped with sour gas tubing, and in most cases have premium threads. Subsurface safety valves are installed in most wells a few joints below surface. The overall experience of the projects in Alberta has been that the compression and injection of the acid gas into deep formations is readily achieved, and is trouble free. ECONOMICS OF ACID GAS REINJECTION For the acid gas reinjection projects currently operating in Alberta, they are typically small. Data for one such project are listed in the following: 3 3 Sales gas output: 620 10 m /day with a CO2 concentration of ~1.6% Acid gas compressor inlet pressure: ~0.1 MPa Outlet: 4.5 MPa Acid gas flow: 13 103 m3/day Acid gas composition: at 92.5% CO2, 6% H2S 3 CO2 flow to storage: at 92.5% CO2 is 12 10 /d or 22.3 t/d CO2 (8,140 t/year) 3 3 H2S flow to storage at 6% H2S is 0.8 10 m /d or 1.1 t/d sulfur (400 t/year) Power consumption for the acid gas compressor: 108 kW Depth of injection zone: 1,500 m This plant had a small Claus unit before, but as sour gas production from the surrounding area declined, it became technically and economically infeasible to run the Claus plant, as the sulfur throughput was reduced to about 1 t/d. With flaring not being an environmentally favorable option, the plant converted to acid gas reinjection. For an acid gas reinjection project of this size, capital costs would be of the order of Can.
Details
-
File Typepdf
-
Upload Time-
-
Content LanguagesEnglish
-
Upload UserAnonymous/Not logged-in
-
File Pages4 Page
-
File Size-