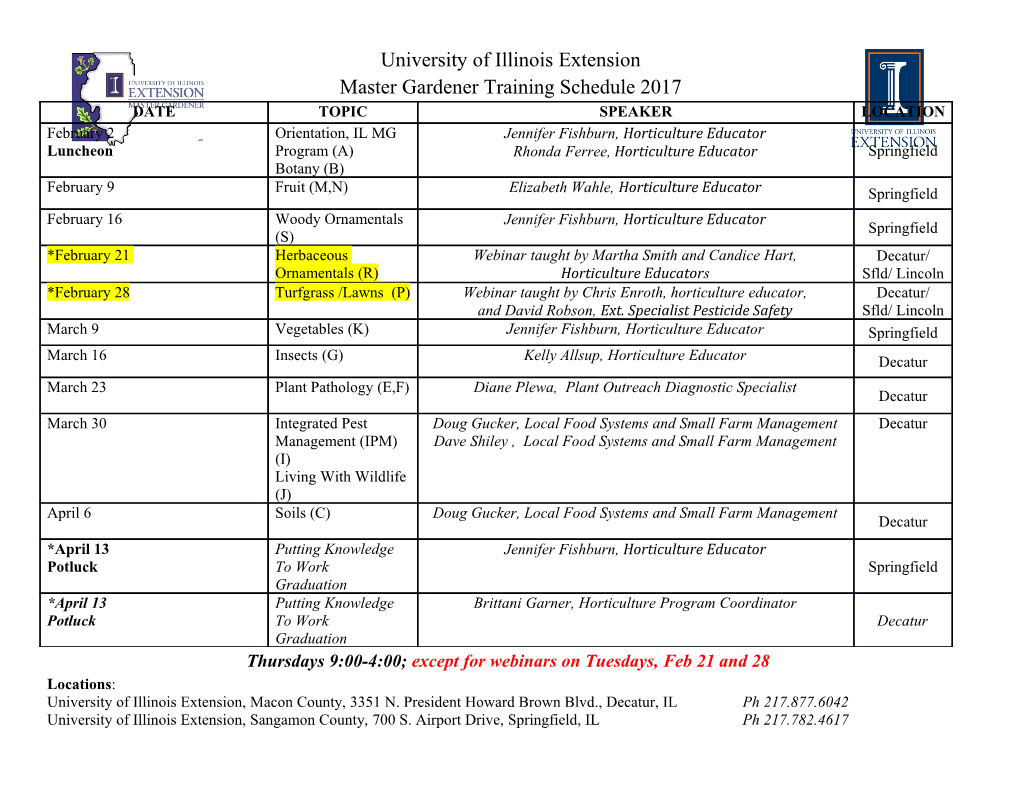
University of Pennsylvania ScholarlyCommons Department of Chemical & Biomolecular Senior Design Reports (CBE) Engineering 4-14-2009 Butanol by Two Stage Fermentation Christina Chen University of Pennsylvania Amira Fawcett University of Pennsylvania Amy Posner University of Pennsylvania Tal Raviv University of Pennsylvania Follow this and additional works at: https://repository.upenn.edu/cbe_sdr Part of the Chemical Engineering Commons Chen, Christina; Fawcett, Amira; Posner, Amy; and Raviv, Tal, "Butanol by Two Stage Fermentation" (2009). Senior Design Reports (CBE). 4. https://repository.upenn.edu/cbe_sdr/4 This paper is posted at ScholarlyCommons. https://repository.upenn.edu/cbe_sdr/4 For more information, please contact [email protected]. Butanol by Two Stage Fermentation Abstract Current techniques for producing butanol tend to have a low yield and form a large amount of other solvents, because there is only one stage for fermentation. Having one stage limits the type of bacteria that can be used, because the chosen bacteria must be able to both convert glucose to butyric acid, and then convert butyric acid to butanol. The only types of bacteria that can perform both these tasks also create a lot of other acids, which are turned to other solvents in the product stream. This is most prevalent in ABE fermentation, which creates significant amounts of acetone and ethanol along with the butanol. David Ramey, of ButylFuel LLC, has created a distinct process that generates butanol, without significant amounts of acetone or ethanol, using a two-stage fermentation process. The first stage converts glucose to butyric acid through acidogenesis, while the second stage converts the butyric acid to butanol via solventogenesis. This process optimizes the efficiency and specificoduction pr of the desired solvent, butanol. The purpose of this report is to scale-up Ramey’s process and build a plant based on a two-stage fermentation procedure. The economical viability of producing 50 million gallons of butanol per year, at a purity of 99.5% from the plant will also been discussed. These results will allow the organization to determine the worth of licensing the technology from ButylFuel. Additionally, because this process will compete with many ethanol plants, it is necessary for the design to mirror a typical ethanol plant as much as possible. Because of this, aspects of the current production of ethanol were implemented in the design, including the Dry Grind process and the Dried Distillers Grain Drying process. These implementations allow the process to be constructed from modified ethanol plants, atherr than having to rebuild a new plant. The fermentation phase of the design utilizes a series of fibrous bed reactors and two different strands of Clostridium bacteria for each stage. The product stream out of the second fermentation stage, containing butanol, is separated using a liquid-liquid extractor, and a series of distillation columns, to extract the butanol from water. Different separation options were researched, including pervaporation, decanters, and stripping. The liquid-liquid extractor with distillation columns was chosen in the end, because it was the simplest and most economical process for dealing with a product stream that was over 90% water. Also, a butanol/water azeotrope surfaces during the separations process that is efficiently dealt with by the extractor. For the economic analysis, this report uses 50 million gallons per year producing ethanol plant as a comparison with the butanol process. The total capital investment for the ethanol plant is about $74.1 million with an investment rate of return (IRR) of 33.1%. This correlates to a total capital investment of $1.48/gallon of ethanol produced. Since the design specifications involved the modification of an existing ethanol plant, it was assumed that some existing ethanol equipment would be integrated into the system. Specifically, the Dried Distiller’s Grains (DDGS) dryer and the Dry Grind process are assumed to be installed and operational in year one. Additionally, it was assumed this equipment had been fully depreciated by the time of construction of the butanol plant. The results of this report were based on 54.3 million gallons per year producing butanol plant. , For this design, a total capital investment of $219 million was determined. This is a substantial investment cost highlighted by the fact that the overall net present value (NPV) of the design, after 15 years, was found to be a negative $3.55 billion. The poor investment opportunity stems from the high cost of utilities needed to run the plant. Of the total annual costs, 94.5% is derived from the overall utility costs. The profitability analysis and a er view of current market conditions indicate that this investment should not be undertaken due to its high degree of unprofitability. Serious consideration of external factors and of the design itself must be taken before pursuing any investment. These factors, such as the price of corn, will be outlined more thoroughly at the end of the report. Disciplines Chemical Engineering This article is available at ScholarlyCommons: https://repository.upenn.edu/cbe_sdr/4 Butanol by Two Stage Fermentation Design Project by: Christina Chen Amira Fawcett Amy Posner Tal Raviv Presented To: Professor Leonard A. Fabiano Dr. Sean P. Holleran April 14th, 2009 Department of Chemical and Biomolecular Engineering University of Pennsylvania School of Engineering and Applied Science 1 2 April 3nd, 2009 Dr. Sean P. Holleran Professor Leonard K. Fabiano University of Pennsylvania School of Engineering and Applied Science Department of Chemical and Biomolecular Engineering Dear Professor Fabiano and Dr. Holleran, Enclosed you will find our written report and solution to the design project proposed to us by Bruce Vrana, of DuPont, Butanol by Two-Stage Fermentation. The process involves the use of two strains of bacteria to convert glucose, derived from corn, into butanol fuel. The entire process is broken up into two main sections: the fermentation phase and the separations phase. The fermentation phase begins with a series of continuous Fibrous Bed Bioreactors immobilized with Clostridium tyrobutyricum, performing acidogenesis by converting glucose into butyric acid. The butyric acid is then fed into another series of bioreactors where Clostridium acetobutylicum converts butyric acid into butanol via solventogenesis. The separations phase details a continuous separations stream to recover the butanol product at 99.5% purity and recycle as much of the raw materials and process water as possible. The report outlines the necessary startup and investment costs required to implement the facility, as well as the potential profitability of the plant. The design requires 10 billion pounds of corn a year to produce 54.4 million gallons of butanol. Financial analysis on the design yielded an NPV of $217 million at an interest rate of 15%. This corresponds to a 32.3% IRR, when butanol is $4.00 per gallon. Further analysis of these estimations are detailed inside. Sincerely, Christina Chen Amira Fawcett Amy Posner Tal Raviv 3 4 Table of Contents Abstract ....................................................................................................................................................... 9 Introduction .............................................................................................................................................. 13 Importance of the Study ........................................................................................................................... 17 Project Charter .......................................................................................................................................... 20 Technology-Readiness Assessment ........................................................................................................... 21 Innovation Map ......................................................................................................................................... 27 Market Analysis ......................................................................................................................................... 29 Market Outlook ..................................................................................................................................... 29 Drivers ............................................................................................................................................... 31 Inhibitors ........................................................................................................................................... 32 Competitors ....................................................................................................................................... 33 Customer Requirements ........................................................................................................................... 36 Scope ..................................................................................................................................................... 36 Economic Considerations .................................................................................................................. 36 Sterilization ....................................................................................................................................... 36 Off-Gases ..........................................................................................................................................
Details
-
File Typepdf
-
Upload Time-
-
Content LanguagesEnglish
-
Upload UserAnonymous/Not logged-in
-
File Pages215 Page
-
File Size-