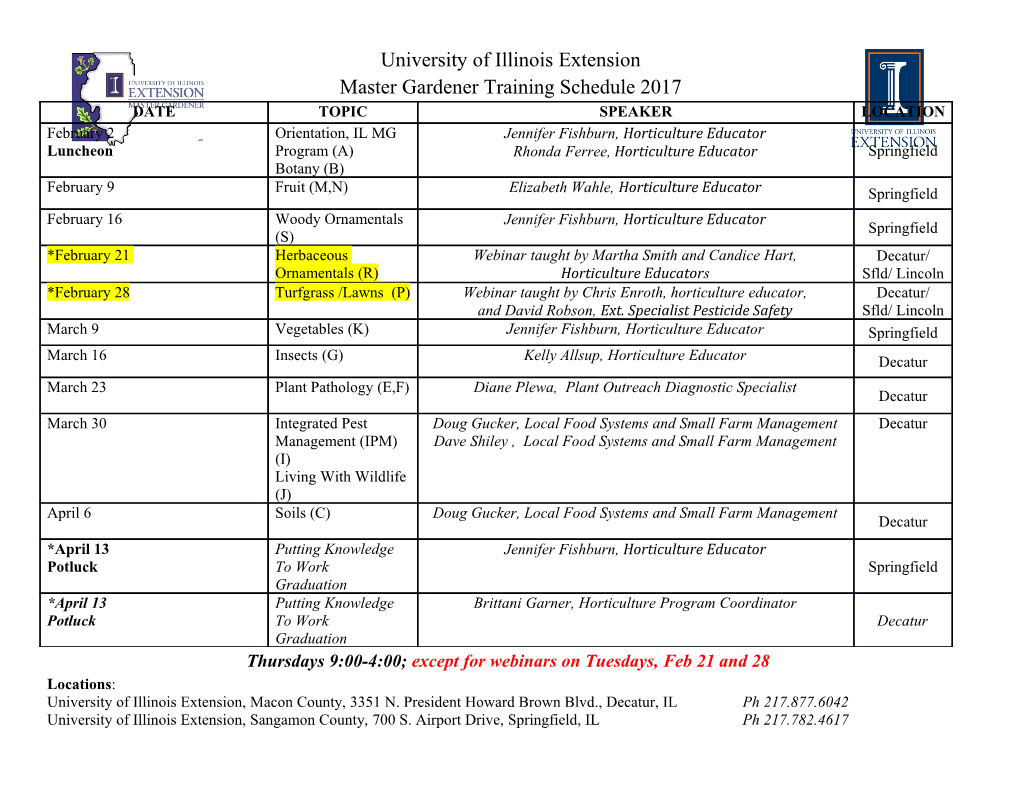
Glossary of Lean Terminology Lean Term Definition Use 5S: Used for Improving organization of the Create an workplace: Sort > Set in order > Shine > organized Standardize > Sustain work area A3 Thinking: Forces consensus building: unifies culture Value Stream around a simple, systematic methodology; A3 Analysis = metric nomenclature for a paper size (VSA), Rapid equivalent to 11”x17” Improvement Event (RIE), problem solving Affinity A process for organizing ideas by placing Problem Diagram: them on cards and grouping the cards that go solving, together in a creative way. “Header” cards brainstorming are then used to summarize each group of cards. Andon: A device that calls attention to defects, Visual equipment abnormalities, other problems, or management reports the status and needs of a system tool typically by means of light - red light for failure mode, yellow light to show marginal performance, and green light for normal operation mode. Annual Current year objectives that will allow you to Strategic focus Objectives reach your 3-5 year breakthrough objectives. Bottleneck: The place in the value stream that negatively Constraint or affects the flow; inhibiting a process/system flow stopper from meeting the demand of the customer. Breakthrough Objectives characterized by multi-functional Strategic focus Objectives: teamwork, significant change in the organization, significant competitive advantage and major stretch for the organization. Catch Ball: The process of selecting strategies to meet an Strategy objective at any level then getting managers deployment, and their teams to engage in dialogue to reach collaborative agreement on strategies to achieve their goals. goal setting Cause and A problem-solving tool used to establish Problem Effect relationships between effects and multiple solving Diagram: causes. Counter Action needed to improve the performance of Problem Measures: a process that is underperforming. Requires solving root cause analysis. Fishbone A chart that resembles a fish skeleton, with a Problem Diagram: main spine and branches (bones) drawn at a solving, slant off the spine: used for quality control in quality two main ways: improvement 1. Cause-and-effect diagram, where the spine denotes an effect and the branches are cause factors. 2. As a subdivision of quality requirements, where the spine represents a quality objective and the branches describe subsidiary traits or measurements that are important but are not the end in themselves. Five Whys: The practice of asking “why” five times Problem whenever a problem is encountered; repeated solving; questions helps identify the root cause of a determining problem so that effective countermeasures root causes can be developed and implements. Flow: The progressive achievement of tasks and/or Principle of information as it proceeds along the value Lean stream. Makes value flow by removing waste. Gemba: Japanese word which means “the real place”; Go and see the where the actual services are provided or work where the work is done. Heijunka: Production leveling process that attempts to Creating flow minimize the impact of peaks and valleys in customer demand. Hoshin Kanri: Strategic Planning/Strategic Management Strategic methodology, developed by Dr. Yoji Akao. planning and Also known as policy deployment. execution Jidoka: Building quality into the process: accept no Creating flow defects, make no defects, pass no defects. If a and defect is detected production is ceased until eliminating there is a resolution. waste Just-in-time A system of managing production processes Creating flow (JIT): that result in line-balancing, one-piece flow, and and little or no excess material inventory on eliminating hand. A strategy of making quality products, waste in the quantity needed, when needed. Kaizen: Japanese term meaning “change for the Continuous better”; implying continuing improvement improvement involving everyone. Also refers to REI - Rapid Improvement Event. Kanban: Japanese term, in the literal sense, for Creating flow “signboard” and refers to a visual pull system. and A card or sheet used to authorize production eliminating or movement of an item. waste Key A method of tracking or monitoring the Daily Performance progress of existing daily management management Indicators systems. (K.P.I.): Muda: Japanese term for activity that is wasteful and Seeing and does not add value or is unproductive. eliminating the Removing waste is an effective way to waste increase value. Mura: Japanese term for “unevenness”. It is the Seeing and waste of variation in the production process. eliminating the waste Nagara: Japanese term for smooth production flow; Creating flow ideally one piece at a time, characterized by and synchronization (balancing) of production eliminating processes and maximum utilization of waste available time, including overlapping of operations. Non Value Those process steps in a value stream that Seeing the Added (NVA): take time, resource or space, but do not waste transform or shape the product or service to meet the needs of the customer. Operator Cycle The total time it takes someone to complete Data collection Time: one cycle of all standard work elements of a job. P.D.C.A. Plan-Do-Check-Act. An iterative four-step Problem Cycle: problem-solving process typically used in solving quality control. Also known as the Deming Cycle, Shewhart Cycle, and Deming Wheel. Perfection: A never ending pursuit of the complete Principle of elimination of non-value added waste so that Lean all activities along a value stream create value. Point of use: The condition in which all supplies are within Elimination of arms reach and positioned in the sequence in waste; storage which they are used to prevent extra reaching, at the worksite lifting, straining, turning, and twisting. Poka-Yoke: Japanese expression meaning “common or Quality at the simple, mistake proof”. In reference to error source proofing, the implementation of a fail safe mechanism to prevent a process from producing defects or automatically detect them. Policy A one year plan, reflecting the long-term Strategic Deployment vision and the 3-5 year strategic planning planning and (PD): objectives. A planning/implementation execution process that focuses on a few, major, long- term, customer-focused breakthrough objectives that are critical to an organization’s long-term success. Policy Form used by the team working on a PD Strategic Deployment objective, detailing specific activities required planning and Action Plan: for success, milestones, responsibilities and execution due dates. Policy Form used to show relationships between 3-5 Strategic Deployment year objectives, improvement priorities, planning and Matrix: targets, resources required and benefits to the execution organization. Process Map: A visual representation of the sequential flow Problem of a process. Used as a tool in problem solving solving; this technique makes opportunities for improvement apparent. Pull: Based on the principle that goods and Principle of services will ultimately be produced/provided Lean when the customer asks for it. Pull System: System where the upstream supplier will not Principle of produce goods/services until it receives a Lean signal from the downstream supplier; as opposed to a push system which schedules upstream operation according to theoretical downstream results based on a plan which may not be current. Rapid Process utilizing a team based methodology Implementing Improvement to apply the lean tools for seeing waste and change Event (REI): making immediate improvement. Root Cause: Drilling down to the main concern of the Problem problem before implementing solutions solving Single Minute Term used to describe the complications of Creating flow Exchange of tools and techniques used to dramatically and Die (SMED) reduce the time required to complete the eliminating changeover of production and support of one waste “product” to another. Six Sigma: A statistical measure of quality that strives for Analysis and near perfection. A disciplined, data-driven, elimination of customer-centered approach for eliminating variation defects in a process. Standard The most efficient and effective way to Written Work: complete an activity or process. description of the “best known way” to do work Takt Time: The rate of production based on the rate of Set the pace customer consumption. It is calculated by for product taking the available minutes of work divided flow by the units required by the customer in that period of time. Value: From the perspective of the customer, a Principle of product or service that has been perceived or Lean appraised to fulfill a need or desire. Components of value may include quality, utility, functionality, capacity, aesthetics, timeliness or availability, price, etc. Value Stream: All the activities (both value-added and Principle of nonvalue-added) required within an Lean organization to deliver a specific service in order to deliver value from the customer perspective. Value Stream The identification of all activities occurring Analysis used Analysis (VSA) along a value stream; represented visually in to create an /Value Stream a value stream map in order to see waste, action plan for Mapping unevenness, and overburden points within a improvement (VSM): process and to identify areas for incremental improvement. Visual The presentation of a wide variety of At a glance Management: information in the workplace. May pertain to rule - jobs themselves, to the business as a whole, to abnormalities how work teams are progressing on a project. are obvious (ie. Kanban cards, shadow boards, story boards, etc.) Voice of the The desires and expectations of the customer Listening to Customer: which are of primary importance in the and acting on development of products, services and the customer daily conduct of the business. feedback Waste/Muda: Any operation or activity that takes time and Non-value resources but does not add value to the added work; product or service received by the customer. Identification of non-value 8 Wastes: added 1) Unused talent activities 2) Waiting 3) Inventory 4) Transportation 5) Defects 6) Motion 7) Overproduction 8) Processing .
Details
-
File Typepdf
-
Upload Time-
-
Content LanguagesEnglish
-
Upload UserAnonymous/Not logged-in
-
File Pages7 Page
-
File Size-