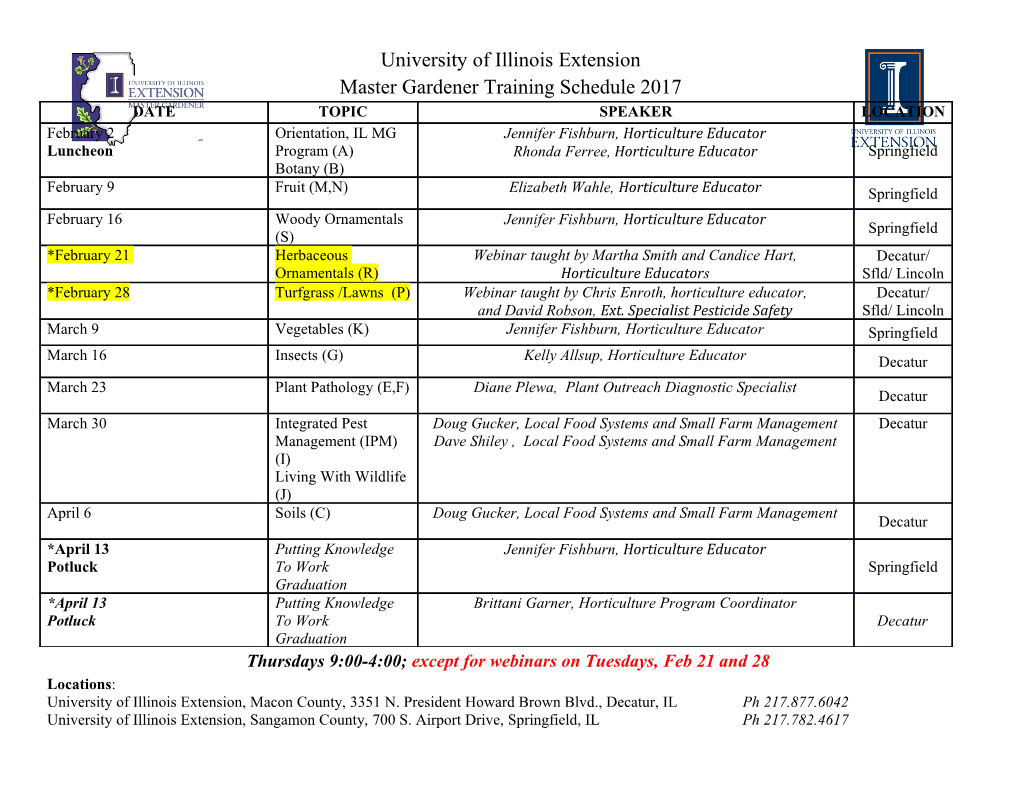
Chapter 20. Modeling Engine Ignition This chapter discusses how to use the engine ignition models available in ANSYS FLUENT in the following sections. For information about the theory behind these ignition models, see Chapter 12: Engine Ignition in the separate Theory Guide. • Section 20.1: Spark Model • Section 20.2: Autoignition Models • Section 20.3: Crevice Model 20.1 Spark Model The spark model in ANSYS FLUENT will be described in the context of the premixed turbulent combustion model. For information regarding the theory of this model, see Section 12.1: Spark Model in the separate Theory Guide. Information regarding the use of this model is detailed in the following section: • Section 20.1.1: Using the Spark Model 20.1.1 Using the Spark Model To activate the spark model, perform the following steps: 1. Select Transient from the Time list in the General task page. 2. Select an appropriate reaction model in the Species Model dialog box. Models −→ Species −→ Edit... 3. Select Species Transport under Model in the Species Model dialog box and enable Volumetric under Reactions. 4. The Spark Ignition model will now appear in the Models task page. Select the Spark Ignition model and click Edit.... This will open the Spark Ignition Model dialog box. Models −→ Spark Ignition −→ Edit... 5. Define the spark model as either Fixed Spark Size or Time-Varying Spark Radius. Release 12.0 c ANSYS, Inc. January 30, 2009 20-1 Modeling Engine Ignition Figure 20.1.1: The Spark Ignition Model Dialog Box When the Fixed Spark Size is enabled, the dialog box expands to include the main spark model inputs (Figure 20.1.2). The shape of the spark can be spherical, cylindrical or hexahedral in three dimensional simulations, or circular or quadrilateral in two dimen- sional simulations. Depending on the shape selected, appropriate inputs are highlighted or grayed out. Figure 20.1.2: The Expanded Spark Ignition Model Dialog Box 20-2 Release 12.0 c ANSYS, Inc. January 30, 2009 20.2 Autoignition Models • To define a spherical spark, the shape parameters can be selected by clicking the Select Points with Mouse button at the bottom of the dialog box, and highlighting the center and radius of the spark kernel. • Enter Energy, Start Time, Duration, and Diffusion Time in the Spark Ignition Model dialog box. i When the in-cylinder model is turned on, the Start Time is entered in crank angle degrees instead of seconds (as shown in Figure 20.1.2), while the spark Duration is still in seconds. • While the Energy input is in Joules by default, you can redefine the units as needed. The rate of energy input into the domain is constant so that the total energy will be evenly distributed over the duration that you set. The Energy input in the spark model should result in an appropriate temperature rise in the cell that is high enough to initiate combustion. The Energy input is only a model parameter and does not reflect energy input in actual automotive ignition systems, which typically range between 50 and 150 millijoules. If you select the Time-Varying Spark Radius option, you will need to specify the Energy, Start Time, Duration, Diffusion Time, and Time Exponent. The spark is assumed spherical and will grow from an Initial Radius, r0, to a Final Radius, rf , over the spark Duration, with a cube root dependence on time so that the radius will grow faster at the beginning and more slowly near the end. This time-dependent behavior is consistent with experimental findings [31]. The Time-Varying Spark Radius option is recommended as it has been found to be less sensitive to model parameters. 20.2 Autoignition Models Autoignition phenomena in engines are due to the effects of chemical kinetics of the reacting flow inside the cylinder. There are two types of autoignition models considered in ANSYS FLUENT: • knock model in spark-ignited (SI) engines • ignition delay model in diesel engines For information regarding the theory behind autoignition models, see Section 12.2: Au- toignition Models in the separate Theory Guide. Section 20.2.1: Using the Autoignition Models descibes how to use the autoignition models in ANSYS FLUENT. Release 12.0 c ANSYS, Inc. January 30, 2009 20-3 Modeling Engine Ignition 20.2.1 Using the Autoignition Models To activate the autoignition model, perform the following steps: 1. Select Transient from the Time list in the General task page. 2. Select an appropriate reaction model in the Species Model dialog box. iModels −→ Species −→ Edit... 3. The models in the Species Model dialog box that are compatible with the autoigni- tion model are Species Transport, Premixed Combustion, and Partially Premixed Com- bustion. If you select Species Transport, you must also enable the Volumetric option in the Reactions group box. The Premixed Combustion and Partially Premixed Combustion models are only available for turbulent flows using the pressure-based solver. 4. The Autoignition model will now appear in the Models task page. Models −→ Autoignition −→ Edit... • If Species Transport is selected in the Species Model dialog box, you can only select the Ignition Delay Model. Figure 20.2.1: The Ignition Delay Model in the Autoignition Model Dialog Box • If Premixed Combustion is selected in the Species Model dialog box, you can only select the Knock Model. • If Partially Premixed Combustion is selected in the Species Model dialog box, you can select either the Knock Model or the Ignition Delay Model. 5. When the Ignition Delay Model is enabled, the dialog box expands to include the modeling parameters for this model (Figure 20.2.3). The two correlation options that exist with this model are Hardenburg and Generalized. Depending on which 20-4 Release 12.0 c ANSYS, Inc. January 30, 2009 20.2 Autoignition Models Figure 20.2.2: The Knock Model in the Autoignition Model Dialog Box correlation option is selected, the appropriate modeling parameters will appear in the dialog box. Figure 20.2.3: The Ignition Delay Model for the Partially Premixed Combustion Model • The Hardenburg option is typically used for heavy duty diesel engines. A Fuel Species is selected from the drop-down list and the Pre-Exponential, Pressure Exponent, Activation Energy, and Cetane Number are entered using the GUI. Default values of these parameters can be found in Table 12.2.1 in the separate Theory Guide. • The Generalized option is described by Equation 12.2-3 in the separate Theory Release 12.0 c ANSYS, Inc. January 30, 2009 20-5 Modeling Engine Ignition Guide. Similarly to the Hardenburg option, a Fuel Species is selected from the drop-down list and the Pre-Exponential, Temperature Exponent, Activation Energy, RPM Exponent, Pressure Exponent, Equivalence Ratio Exponent, Octane Number, and Octane Number Exponent are entered using the GUI. 6. When the Knock Model is enabled, the dialog box expands to include modeling parameters for this model (Figure 20.2.4). The two correlation options that exist with this model are Douaud and Generalized. Depending on which correlation option is selected, the appropriate modeling parameters will appear in the dialog box. Figure 20.2.4: The Knock Model with the Partially Premixed Combustion Model Enabled • The Douaud option is used for knock in SI engines. The modeling parameters that are specified in the GUI for this option are the Pre-Exponential, Pres- sure Exponent, Activation Temperature, Octane Number, and Octane Exponent (Equation 12.2-2 in the separate Theory Guide). • The Generalized option (Equation 12.2-3 in the separate Theory Guide) in the knock model requires the same parameters as in the ignition delay model. 20-6 Release 12.0 c ANSYS, Inc. January 30, 2009 20.3 Crevice Model 20.3 Crevice Model For information regarding the theory behind the crevice model, see Section 12.3: Crevice Model in the separate Theory Guide. Using the crevice models in ANSYS FLUENT are described in the following sections: • Section 20.3.1: Using the Crevice Model • Section 20.3.2: Crevice Model Solution Details • Section 20.3.3: Postprocessing for the Crevice Model 20.3.1 Using the Crevice Model An optical experimental engine [18] is used below to show a working example of how to use the crevice model as it is implemented in ANSYS FLUENT. The mesh at ten crank angle degrees before top center is shown in Figure 20.3.1. Z Y X Grid (Time=2.2222e-02) Crank Angle=-5.00(deg) Figure 20.3.1: Experimental Engine Mesh Release 12.0 c ANSYS, Inc. January 30, 2009 20-7 Modeling Engine Ignition The following example shows the necessary steps to enable the crevice model for a typical in-cylinder flow. 1. From the > prompt, enter the define/models menu by using the following text command: define −→models 2. Enable the crevice model, as follows: /define/models> crevice-model? Enable crevice model? [no] yes /define/models> acoustics/ frozen-flux? sox? addon-module multiphase/ species/ axisymmetric? noniterative-time-advance? steady? crevice-model-controls/ nox? unsteady-1st-order? crevice-model? radiation/ unsteady-2nd-order? dpm/ solidification-melting? viscous/ dynamic-mesh? solver/ energy? soot? 20-8 Release 12.0 c ANSYS, Inc. January 30, 2009 20.3 Crevice Model 3. Enter the ring pack geometry: /define/models> crevice-model-controls Cylinder bore (m) [0.1] 0.1397 Piston to bore clearance (m) [3.0e-5] 5.08e-05 Piston crevice temperature (K) [400] 433 Piston sector angle (deg) [360] 45 Ring discharge coefficient [0.8] 0.7 Pressure in crankcase (exit pressure) (Pa) [101325] Write out crevice data to a file? [no] yes output file name ["crev.out"] Available wall threads are: (wall.1 wall wall-8)
Details
-
File Typepdf
-
Upload Time-
-
Content LanguagesEnglish
-
Upload UserAnonymous/Not logged-in
-
File Pages14 Page
-
File Size-