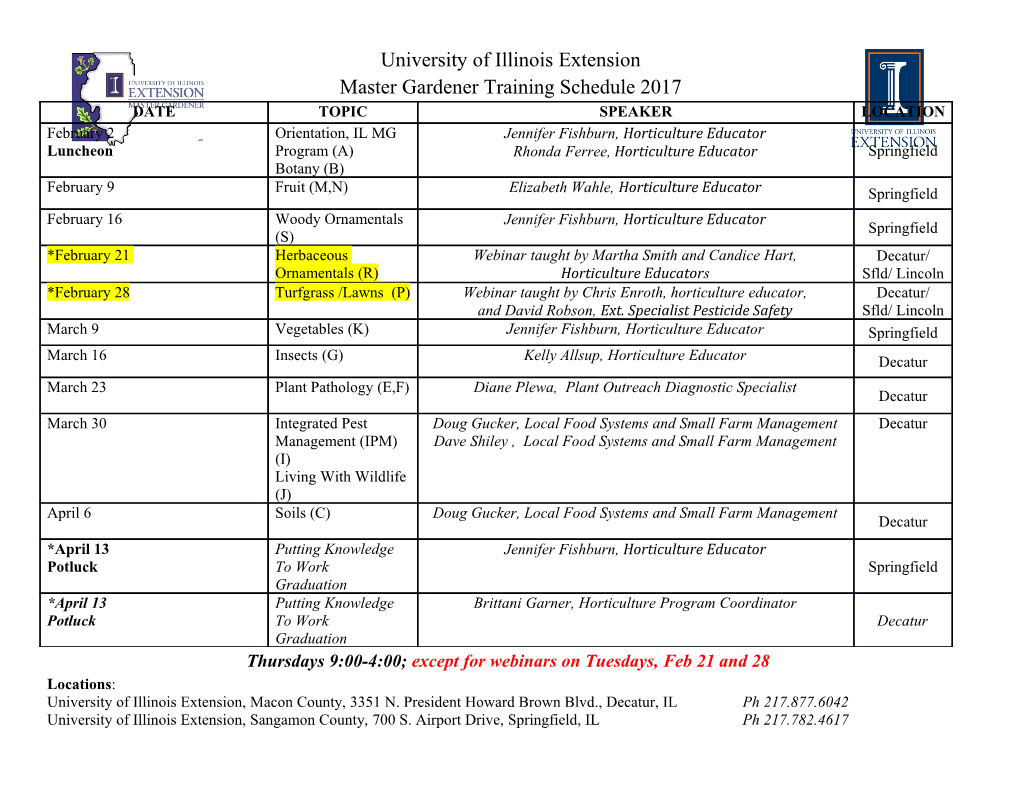
SAE TECHNICAL PAPER SERIES 2007-01-0382 Effect of Primary Intake Runner Tapers and Bellmouths on the Performance of a Single Cylinder Engine V. Mariucci and A. Selamet The Ohio State University K. D. Miazgowicz Ford Motor Company Reprinted From: Modeling of SI and Diesel Engines, 2007 (SP-2079) 2007 World Congress Detroit, Michigan April 16-19, 2007 400 Commonwealth Drive, Warrendale, PA 15096-0001 U.S.A. Tel: (724) 776-4841 Fax: (724) 776-0790 Web: www.sae.org Author:Gilligan-SID:12324-GUID:50206991-164.107.10.90 By mandate of the Engineering Meetings Board, this paper has been approved for SAE publication upon completion of a peer review process by a minimum of three (3) industry experts under the supervision of the session organizer. All rights reserved. No part of this publication may be reproduced, stored in a retrieval system, or transmitted, in any form or by any means, electronic, mechanical, photocopying, recording, or otherwise, without the prior written permission of SAE. For permission and licensing requests contact: SAE Permissions 400 Commonwealth Drive Warrendale, PA 15096-0001-USA Email: [email protected] Fax: 724-776-3036 Tel: 724-772-4028 For multiple print copies contact: SAE Customer Service Tel: 877-606-7323 (inside USA and Canada) Tel: 724-776-4970 (outside USA) Fax: 724-776-0790 Email: [email protected] ISSN 0148-7191 Copyright © 2007 SAE International Positions and opinions advanced in this paper are those of the author(s) and not necessarily those of SAE. The author is solely responsible for the content of the paper. A process is available by which discussions will be printed with the paper if it is published in SAE Transactions. Persons wishing to submit papers to be considered for presentation or publication by SAE should send the manuscript or a 300 word abstract of a proposed manuscript to: Secretary, Engineering Meetings Board, SAE. Printed in USA Author:Gilligan-SID:12324-GUID:50206991-164.107.10.90 2007-01-0382 Effect of Primary Intake Runner Tapers and Bellmouths on the Performance of a Single Cylinder Engine V. Mariucci and A. Selamet The Ohio State University K. D. Miazgowicz Ford Motor Company Copyright © 2007 SAE International ABSTRACT the piston draws in fresh charge, an expansion wave propagates toward the inlet of the intake pipe. When The present experimental study investigates this expansion wave reaches the inlet of the pipe, it is systematically the effects of primary intake runner partially reflected as a compression wave. If this configurations on a firing single cylinder research compression wave arrives back at the intake valve while engine. Twelve different intake configurations were it is still open, it can aid the breathing process of the fabricated to investigate runners with tapers and engine, thus increasing the volumetric efficiency (Șv). bellmouths. For each configuration, the length from the This charging effect will happen near certain engine base of the test configuration to the start of the inlet speeds, governed by the intake geometry, giving rise to radius and pressure measurement locations were “tuning peaks.” retained in an effort to isolate the effect of runner geometry only. Each configuration is presented against Numerous early works have investigated the a baseline case with constant cross-sectional area and a effect of varying primary intake runner geometry on ratio of inlet radius, Ri, to internal diameter, D, of 0.35. intake tuning. In 1924, Matthews and Gardiner, working For the seven tapered runners, the length of the taper with a one-cylinder diesel engine, found that the engine varied from 25% to 100% of the overall length of the test would not start unless the compression pressure was piece, and the taper area ratios (TAR) varied from 1.5 - increased. They found that a long suction pipe attached 3; all tapers retained the inlet radius of the baseline. to the inlet port gave them the pressure increase they The four bellmouth runners had a constant cross- needed, and proceeded to test several lengths of pipe sectional area, and varying inlet radii from Ri/D = 0.05 to up to 177.8 cm in addition to the case where no pipe 1.0. The time-averaged quantities such as volumetric was present from 500 to 1800 RPM; they noticed an efficiency and brake power, and time-resolved intake increase in compression pressure of 17% with the 62 in. pressures are presented for each configuration. For the pipe compared to no inlet pipe. The study was purely bellmouth runners, Ri/D > 0.20 was found to be most experimental and did not attempt to explain the reason beneficial to volumetric efficiency, and a TAR larger than for the increase in pressure. 1.5 was detrimental to the intake tuning for higher-speed tuning peaks. Morse et al. (1938) developed a simple method of intake tuning prediction, assuming linear, acoustic INTRODUCTION behavior in the intake duct. This method suggests that the quasi-standing wave (QSW) developed in the intake Whether the motivating factor is more power or pipe when the intake valves are closed dictates intake better fuel economy, several techniques have been tuning. It was found that when the ratio q of pipe employed throughout the years to improve the IC frequency ( = c/4Ɛ) to engine frequency ( = RPM/120) engine. One of the most well-known and used methods was equal to 3, 4, or 5, beneficial resonance would of enhancing an engine’s performance is by intake occur since the pressure fluctuations at the valves will tuning. Due to the unsteady nature of the gas exchange be large, leading to process in the IC engine, pressure fluctuations are generated when the engine takes in air. During the 30 c intake stroke of a single cylinder engine with intake pipe N , (1) leading from atmosphere to the cylinder, for example, as " q 1 Author:Gilligan-SID:12324-GUID:50206991-164.107.10.90 where N [RPM] is the engine speed of beneficial 2/1 resonance, c [m/s] is the speed of sound, [m] is the 955 § A · Ɛ N[] RPM c¨ ¸ , (3) length of the intake pipe, and q = 3, 4, or 5. They t ¨ ¸ K " Veff verified their method by testing several lengths of intake © ¹ pipe of 6.5 cm diameter at a constant engine speed of 1220 RPM. where c [m/s] is the speed of sound, A [cm²] is the effective cross-sectional area of the intake, Ɛ [cm] is the Kastner (1945) studied the intake tuning effect effective length of the inlet system, K is a factor usually of various lengths and diameters of primary runners on equal to 2.1, but that varies from 2.0 to 2.5 depending two separate single-cylinder engines. Standard air upon valve timing and other factors, and, consumption, intake port and in-cylinder pressures were analyzed. One engine, a Rolls-Royce, was motored V( r 1) V[] cm3 d c , (4) between 1000 and 2000 RPM with several lengths of eff 2(r 1) intake pipes of diameters 3.5, 5.3, and 7.3 cm. The c other engine, a J.A.P. motorcycle engine, was fired from 3 1200 to 4000 RPM with various runner lengths of where Vd [cm ] is the displacement volume and rc is the diameters 3.2, 3.5, and 5.3 cm. Kastner found that, for compression ratio. This method provides a simple tool an engine running over a wide range of speeds, the for calculating the location of a single intake tuning peak, intake pipe “natural period” should be between 160-180 yet gives no insight into its magnitude. Even though it crank angle degrees (CAD) at the engine speed of incorporates extra parameters over the organ pipe desired tuning, where natural period, p, is defined as method such as the pipe area and cylinder volume, which Thompson (1968) showed gives a predictive 24N " advantage over the organ pipe method, the value for K p [deg] , (2) is slightly ambiguous without experimental data. Intakes V p of non-constant cross-section, such as tapers, can be handled by using (Engelman, 1973) L N where N [RPM] is the engine speed, Ɛ [cm] is the " dx " j # . (5) effective intake length, and Vp [cm/s] is the velocity of ¦ A effective ³ AA propagation of the waves. Note that when p = 180 CAD, 0 j 1 j the expression is equal to Eq. (1) with q = 4. Kastner also noted that Vp increased as the intake diameter In 1968, Thompson investigated the effects of increased. not only different lengths and areas of primary runners, but also of curved runners, pipes with and without well- Downing (1958) performed a study on the rounded inlets, non-circular tubes, and runners of effects of primary runner length and diameter using one varying cross-sectional area. His experiments were cylinder of a motored six-cylinder engine. He tested performed on individual cylinders of a motored Cummins runner lengths of 13.3, 27.9, 38.1, 54.6, and 82.6 cm for V6 diesel engine and compression pressure was diameters of 4.0 and 5.0 cm from 1500 to 6000 RPM for acquired from 500 to 3000 RPM. The main purpose of the purposes of designing a complete fuel-injection his thesis was to validate Engelman’s approach to intake system for a racing engine, including intake manifold. tuning prediction. He found that, for both intake diameters, as the length increased, the tuning peak moved toward lower speeds. In a precursor to the present study, Howard Also, for same-length runners, the tuning peak of the 5.0 (2003) studied the effects of tapered runners on a cm diameter pipe was at a higher speed than the 4.0 cm motored single cylinder research engine.
Details
-
File Typepdf
-
Upload Time-
-
Content LanguagesEnglish
-
Upload UserAnonymous/Not logged-in
-
File Pages19 Page
-
File Size-