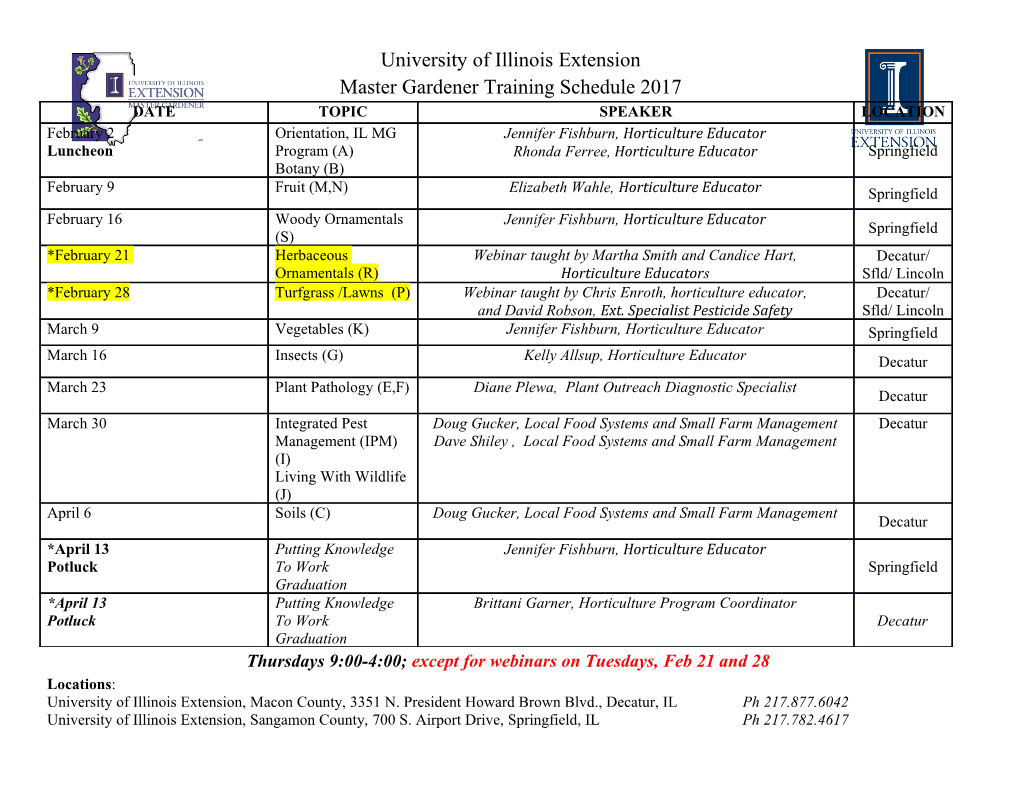
Shrinkage Calculation in the Continuous Casting of Duplex Stainless Steel Thaís Ávila Braz Materials Engineering, master's level (120 credits) 2019 Luleå University of Technology department. Abstract This MSc. project has been carried out to evaluate the evolution temperatures in the mold and resulting shell shrinkage during continuous casting of LDX 2101 duplex stainless steel. This included the analysis of thermocouple measurements to produce thermal maps for a number of casting sequences as well as calculation of the shrinkage and air gap evolution for a specific case based on modelling performed by SWERIM AB. Furthermore, the thermal expansion coefficient of the steel was determined by means of dilatometer experiments while the phase fraction evolution was assessed through thermodynamic software (Thermo- calc and IDS). Lastly, samples collected from a slab were metallographically inspected at micro and macro scale, to observe the transition between the columnar and equiaxed grain zones, which allows to measure the length of the shell thickness at the mold exit. In this case, calculations in IDS provided a closer result to the metallographic methods with 63% austenite and 37% delta ferrite. The thermal analysis shows that the heat flux in the narrow faces is in the same range, but it differs significantly compared to the wide faces. This is likely due to the force generated during the bending of the slab after leaving the mold and the hot spots patterns that are associated with the jet flow from the SEN. This thermal profile makes possible to calculate the shrinkage and air gap resistance using a 2D approach. Separately, the macro/micro structural analysis revealed that the shell thickness in the wide face is perceptibly larger than the narrow faces and also discovered additional thinning close to the corner region in the wide face. The length of the columnar zone in the macro-etchings was compared to the simulated shell thickness which point to a delay in solidification in the corner of the slab possibly linked to the metal flow pattern inside the mold and to a lower heat transfer at this position. 1 Acknowledgments I would first like to thank Pavel Ramirez, not only for giving me the opportunity to work together but also for the great mentoring during the course of this master thesis project. His guidance has inspired me to achieve more and become a better professional. My sincere gratitude to Esa Vuorinen, for always being prone to help and share his immense knowledge. To Rosa Pineda for the several discussions on the topic, for the advices and conversations, I greatly appreciate your support and contributions to this work. Thanks Marko Petäjäjärvi at Outokumpu for valuable insights on the continuous casting process. Thanks to SWERIM AB, Outokumpu and LTU for providing the essential material and equipment for this project to be developed. To my colleagues at SWERIM and LTU for the important technical support and motivation throughout the course of this master program. A special thanks to the Advanced Materials Science and Engineering (AMASE) secretary for their effort into best shaping the program in an important tool for our career developments. This master’s degree could not be accomplished without the financial support of the European School of Materials (EUSMAT), thus, my sincere gratitude to this institution and the opportunities it has given me to succeed and grow, both personally and professionally. Lastly but not least, to the friends I have made along the way in Barcelona and Luleå, I am thankful I could count on these ‘AMASEing’ people during these two years. 2 Table of Contents 1. Overview and objectives ........................................................................................................................... 8 2. Introduction ................................................................................................................................................... 9 2.1. The primary cooling zone (mold) .................................................................................................. 11 2.2. Solidification in continuous casting ............................................................................................... 13 2.2.1. Segregation fundamentals ............................................................................................................ 14 2.3. Surface defects ....................................................................................................................................... 15 2.4. Continuous casting of Stainless Steel ............................................................................................ 16 3. Processing of data supplied by Outokumpu ................................................................................... 18 3.1. Thermal monitoring in the mold .................................................................................................... 18 3.2. Thermocouple measurements at OUTOKUMPU Avesta ........................................................ 20 4. Experimental work ................................................................................................................................... 23 4.1. Strand shrinkage and gap formation ............................................................................................. 23 4.2. Measurement of thermal expansion coefficient........................................................................ 24 4.3. Phase transformation predictions by IDS and Thermocalc .................................................. 25 4.4. Macro and microstructural characterization techniques ...................................................... 26 5. Results and discussion ............................................................................................................................ 28 5.1. Thermal Analysis .................................................................................................................................. 28 5.1.1. Interpolated temperature maps ................................................................................................. 28 5.2. Shrinkage calculation .......................................................................................................................... 31 5.2.1. Shell thickness at x=0 ..................................................................................................................... 32 5.2.2. Shell thickness at z=0 ..................................................................................................................... 34 5.2.3. Shell temperature distribution at the mold exit ................................................................... 34 5.1. Heat Flux analysis ................................................................................................................................. 36 3 5.1.1. Air gap resistance analysis ............................................................................................................ 37 5.2. Macrostructural analysis ................................................................................................................... 42 5.3. Microstructural analysis .................................................................................................................... 44 6. Conclusions .................................................................................................................................................. 50 7. Future work ................................................................................................................................................. 51 8. References .................................................................................................................................................... 52 4 Table of Figures Figure 1: Curved continuous caster [5]. .................................................................................................... 10 Figure 2: Phenomena that govern the continuous casting process [9]. ........................................ 11 Figure 3: Schema of temperature across continuous casting mold and shell [13]. .................. 12 Figure 4: Representation of final solidification structure of continuous casted strands [7].13 Figure 5: "Mini-ingot" formation in CC [15]. ........................................................................................... 14 Figure 6: Variations in OM spacing [19]. ................................................................................................... 15 Figure 7: (a) Dark bands in the subsurface of a bloom depression and (b) : Mechanism for the formation of transversal depression and cracks (Longitudinal view of the slab) [19]. 16 Figure 8: (a) Fe-Cr-Ni phase diagram and (b) Schaeffler diagram for stainless steel [20]. .. 17 Figure 9: Thermocouples location in the mold wide face. ................................................................. 20 Figure 10: Temperature profile in the outer bow wide face of the mold. .................................... 21 Figure 11: mold heat flux versus casting time ........................................................................................ 21 Figure 12: Schematic of a dilatometer device and sample dimensions. ....................................... 24 Figure 13: Dilatometer results showing the thermal expansion coefficient variation. .......... 25 Figure 14: Picture of the top of the LDX 2101 slab used for macrostructure analysis. .......... 26 Figure 15: Scheme of the
Details
-
File Typepdf
-
Upload Time-
-
Content LanguagesEnglish
-
Upload UserAnonymous/Not logged-in
-
File Pages57 Page
-
File Size-