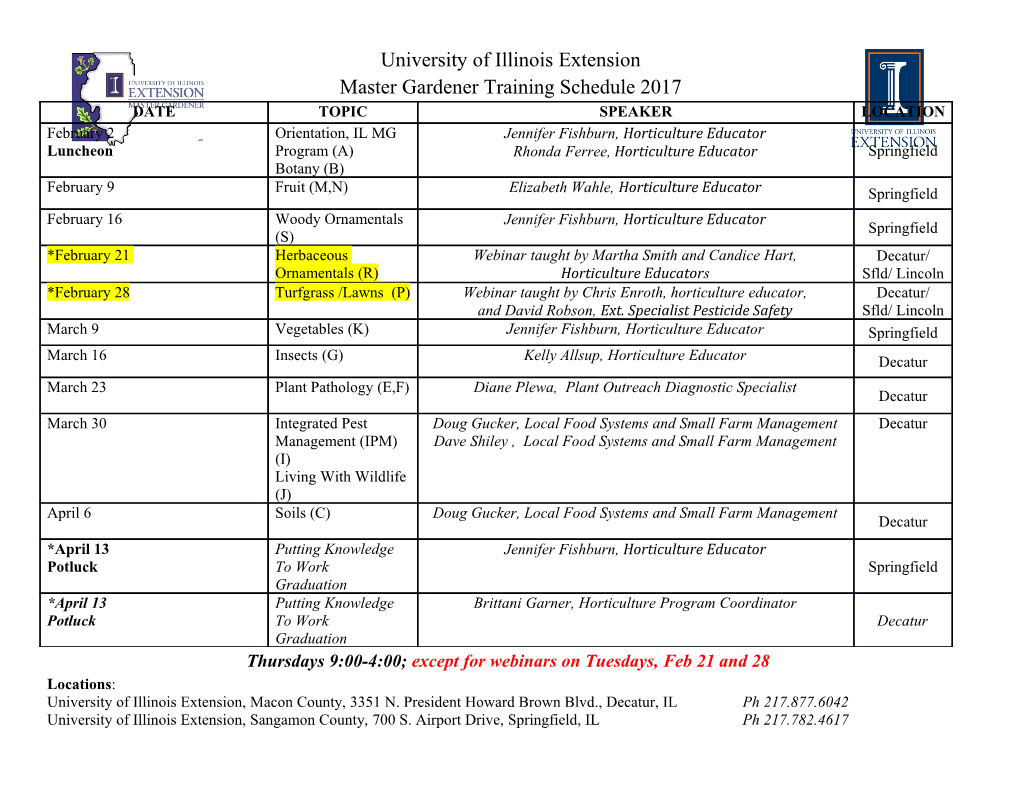
The Impact of Composites to Aircraft Structural Integrity Management Aaron J. Warren A thesis in fulfillment of the requirements for the degree of Masters by Research July 2013 School of Engineering & Information Technology Faculty of UNSW Canberra at ADFA - 1 - Table of Contents 1 - INTRODUCTION 1.1 - WHAT IS A COMPOSITE? 1.2 - AIM OF RESEARCH 1.3 - SCOPE OF RESEARCH 2 - STRUCTURAL INTEGRITY MANAGEMENT 2.1 - EVOLUTION OF AIRCRAFT STRUCTURAL INTEGRITY 2.1.1 - In the Beginning 2.1.2 - The Post-War Years 2.1.3 − 1954 – de Havilland Comet Accidents 2.1.4 − 1958 - Boeing B-47 Accidents 2.1.5 − 1969 - General Dynamics F-111 Accident 2.1.6 − 1977 - Dan Air Boeing 707 Accident 2.1.7 − 1978 – Issue of Advisory Circular 20-107 2.1.8 − 1988 - Aloha Airlines Boeing 737 Accident 2.1.9 − 2010 – Introduction of Limit of Validity 2.1.10 - Summary 2.2 - REVIEW OF STRUCTURAL INTEGRITY REGULATIONS 2.2.1 - Military Aircraft Structural Integrity Regulations 2.2.2 - Civil Aircraft Structural Integrity Regulations 3 - DRIFTING INTO STRUCTURAL FAILURE 3.1 - WHAT IS OUR EXPERIENCE WITH COMPOSITE AIRCRAFT STRUCTURES? 3.1.1 - United States Navy Boeing F/A-18 3.1.2 - Beechcraft Starship 3.1.3 - Sailplane Experience 3.1.4 - NASA Research into Composite Aging 3.1.5 - Boeing 787 Certification 3.1.6 - In-Service Summary 3.1.7 - Future Direction of Composite Structures 3.2 - ACCIDENT THEORY 3.2.1 - Introduction to Resilience 3.2.2 - Structural Resilience 3.2.3 - Total Structural Residual Strength 3.2.4 - Unruly Technology 3.3 - RESILIENCE OF THE AIRCRAFT STRUCTURAL INTEGRITY ‘SYSTEM’ 3.3.1 - Aircraft Structural Integrity System 3.3.2 - Resilience Classification of ASI System 3.3.3 - Resilience of ASI System 4 - SIMULATING STRUCTURAL INTEGRITY 4.1 - STRUCTURAL INTEGRITY MODELS 4.1.1 - Probabilistic 4.1.2 - The Diamond 4.1.3 - The Three-Legged Stool 4.1.4 - Holistic Structural Integrity Process 4.2 - STRUCTURE TO BE MODELED 4.2.1 - Evolution of Aircraft Structures 4.2.2 - Principal Structural Elements (PSE) 4.2.3 - Significant Structural Items (SSI) 4.2.4 - Structure for Simulation - 3 - 4.2.5 - When does the Structure of Interest fail? 4.3 - MODELING STRUCTURAL INTEGRITY (THE SIFCM) 4.4 - SIFCM SIMULATION 5 - STRUCTURAL DEGRADATION 5.1 - ACCIDENTAL DAMAGE (AD) 5.1.1 - Design Induced Damage 5.1.2 - Manufacture Induced Damage 5.1.3 - Structural Overload 5.1.4 - Impact 5.2 - ENVIRONMENT DAMAGE (ED) 5.2.1 - Chemical Degradation 5.2.2 - Corrosion Initiated Damage 5.2.3 - Absorption 5.2.4 - Desorption 5.2.5 - Thermal Effects 5.2.6 - Ultraviolet Degradation 5.3 - FATIGUE DAMAGE (FD) 5.4 - SIMULATION OF DEGRADATION 5.4.1 - Accidental Degradation Simulation 5.4.2 - Environmental Degradation Simulation 5.4.3 - Fatigue Degradation Simulation 5.4.4 - Black Swan In-Service Damage Simulation 5.5 - DEGRADATION SUMMARY 6 – MAINTENANCE 6.1 - DEVELOPMENT OF SCHEDULED MAINTENANCE 6.2 - DEGRADATION DETECTION 6.2.1 - Detection Methods 6.2.2 - Probability of Detection 6.3 - REPAIR METHODS 6.3.1 - Replacement 6.3.2 - Non-Patch Repairs 6.3.3 - Patch Repairs 6.4 – SIMULATION OF MAINTENANCE 6.4.1 - Damage Detected? 6.4.2 - Determine Response 6.4.3 - Repair Damage 6.4.4 - Document Inspection Requirements 6.5 – MAINTENANCE SUMMARY 7 - SICFM MODELS 7.1 - SIFCM_PSE 7.1.1 - Block 1 - Establish ‘as-manufactured’ Residual Strength for each DDP 7.1.2 - Block 2 - Determine the degradation at each DDP per time step 7.1.3 - Block 3 - Perform Maintenance Activities 7.1.4 - Block 4 - Determine if the structure has failed 7.2 - SIFCMSIM 7.2.1 - Block 0 - Establish the Structure on Interest (SoI) matrix 7.2.2 - Block 0.5 - Define Variables 7.2.3 - Block 1 - Establish ‘as-manufacture’ Residual Strength for each DDP 7.2.4 - Block 2 - Determine the degradation at each DDP per time step 7.2.5 - Block 3 - Perform Maintenance Activities 7.2.6 - Block 4 - Determine if the structure has failed 8. DISCUSSION - 4 - 8.1 - COMPOSITES AND MIL-STD-1530C 8.1.1 - Task I - Design Information 8.1.2 - Task II - Design Analyses and Development Testing 8.1.3 - Task III - Full-Scale Testing 8.1.4 - Task IV - Certification and Force Management Development 8.1.5 - Task V - Force Management Execution 8.2 - SIFCM RESULTS 8.2.1 - SIFCM_PSE Results 8.2.2 - SIFCMsim Results 8.3 - SIFCM ANALYSIS 8.3.1 - Impact Damage 8.3.2 – PoD Sensitivity Analysis 8.3.3 – Moisture Proportionality Variable Sensitivity Analysis 9. CONCLUSION 10. RECOMMENDATIONS REFERENCES APPENDIX A – SIFCM_PSE FILES SIFCM_PSE.M PSE_INITIALISATION.M APPENDIX B – SIFCMSIM FILES SIFCMSIM.M PSE_INITIALISATION.M (MODIFIED FOR SIFCMSIM) APPENDIX C – SIFCM_PSE OUTPUT VARIATION IN INSPECTION INTERVAL (LINEAR POD) VARIATION IN INSPECTION INTERVAL (LOGARITHMIC POD) VARIATION IN MOISTURE CONTENT (LOGARITHMIC POD) VARIATION IN IMPACT DAMAGE REDUCTION IN RESIDUAL STRENGTH (LOGARITHMIC POD) APPENDIX D – SIFCMSIM INPUT FILES STRUCTURE OF INTEREST 1 INPUT FILE STRUCTURE OF INTEREST 2 INPUT FILE STRUCTURE OF INTEREST 3 INPUT FILE - 5 - List of Tables Table 1: MIL-STD-1530C Tasks and activities ......................................................................33 Table 2: ACEE Composite Component Experience................................................................50 Table 3: Large Fixed Wing Aircraft Composite Component Experience ...............................51 Table 4: Helicopter Composite Component Experience .........................................................52 Table 5: ASI System Organisations.........................................................................................59 Table 6: System Resilience Classifications (adapted from Amalberti (2006)) .......................63 Table 7: Degradation Sources for ASI Milestones ..................................................................86 Table 8: Recommended values for H0 and b (from DOT/FAA/AR-01/55, 2002). ...............100 Table 9: Degradation Summary.............................................................................................117 Table 10: Inspection Summary..............................................................................................129 Table 11: Repair Summary....................................................................................................130 Table 12: Detail Design Point Matrix Definition ..................................................................137 Table 13: Impact Probabilities for various Impact Type Structure .......................................139 Table 14: Time to Failure Comparison..................................................................................152 Table 15: PoD Equation Comparison....................................................................................154 - 6 - List of Figures Figure 1: Growth of composite structure on major aircraft programs (1975-2010) as a percentage of weight (adapted from ATSB, 2007)..........................................................22 Figure 2: Milestones in Aircraft Structural Integrity. .............................................................26 Figure 3: US Military Aircraft Structural Integrity related certification requirements...........28 Figure 4: Building Block Approach (from MIL-HDBK-17-3F).............................................38 Figure 5: Total Structural Residual Strength...........................................................................57 Figure 6: Civil Aircraft Structural Integrity System ..............................................................60 Figure 7: FAA Type Certification Process for New Aircraft Design (from GAO-11-849)....62 Figure 8: Probabilistic Analysis Concept (from FAA, 1999) .................................................71 Figure 9: Hawker Hurricane Cutaway (from Fiddlersgreen (2013)) ......................................75 Figure 10: Boeing 747-400 Cutaway Diagram (retrieved from www.flightglobal.com) .......76 Figure 11: Generic SoI for simulation.....................................................................................77 Figure 12: Structural Integrity Failure Causation Model (SIFCM) (from Warren, 2012)......79 Figure 13: SIFCMsim process.................................................................................................82 Figure 14: Degradation with SIFCMsim.................................................................................84 Figure 15: Hierarchy of structural degradation modes............................................................87 Figure 16: Types of In-Service Damage (from DOT/FAA/AR/01-55, 2002). .......................97 Figure 17: Probability density function for various impact threats (from DOT/FAA/AR- 96/111, 1997). ..................................................................................................................98 Figure 18: Cumulative probability of occurrence versus impact energy for various impact threats (from DOT/FAA/AR-96/111, 1997)....................................................................98 Figure 19: Damage growth for 31.63 N.m (280 in-lb) impacted specimen (from Smith and Wilson, 1985).................................................................................................................110 Figure 20: Maintenance with SIFCMsim..............................................................................118 Figure 21: Maintenance Review Board Process Flowchart (from AC 121-22C). ................120 Figure 22: PoD curve for different inspection methods applied to the same flaw specimen (from
Details
-
File Typepdf
-
Upload Time-
-
Content LanguagesEnglish
-
Upload UserAnonymous/Not logged-in
-
File Pages200 Page
-
File Size-