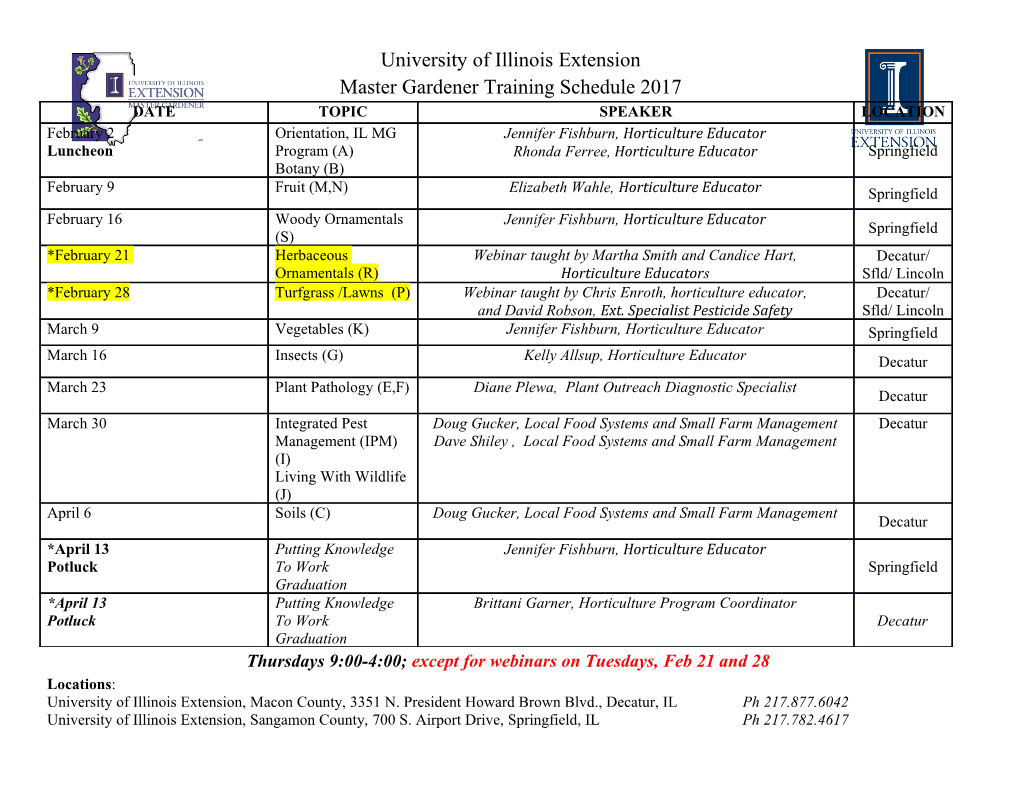
ISIJ International, Vol. 45 (2005), No. 2, pp. 221–228 Modelling Upper and Lower Bainite Trasformation in Steels M. AZUMA, N. FUJITA, M. TAKAHASHI, T. SENUMA, D. QUIDORT1) and T. LUNG1) Steel Products Lab.-1, Steel Research Laboratories, Nippon Steel Corporation, 20-1 Shintomi, Futtsu Chiba, Japan. E-mail: [email protected], [email protected], [email protected] 1) Physical Metallurgy Department, ARCELOR R&D, IRSID, Voie Romaine, BP30320; F-57283 Maizierés-les-Metz Cedex, France. E-mail: [email protected], [email protected] (Received on February 19, 2004; accepted in final form on December 13, 2004 ) Bainite is of considerable importance in the design of high strength steels. There are two types of mor- phologies, upper and lower bainite. In upper bainite, cementite forms between adjacent bainitic ferrite plates. In certain steels, however, the cementite reaction is suppressed so that carbon-enriched austenite remains untransformed between bainitic ferrite plates. In lower bainite, cementite also has the opportunity to precipitate within bainitic ferrite plates. In order to model the development of these microstructures, it is necessary to treat the simultaneous formation of both the ferritic and carbide components of the mi- crostructure. A theory has been developed to do exactly this, enabling the estimation of the phase fractions, the cementite particle size and the transition from upper to lower bainite. The results have been compared against experimental data. KEY WORDS: simultaneous reaction; upper/lower bainite; bainitic ferrite; cementite; austenite. up to 1 000°C and cooled at 50°C/s with helium gas to the 1. Introduction temperatures between 300 and 450°C for isothermal trans- High strength steels are used widely as structural materi- formation to bainite. The austenite grain size was 60 mm als. Their microstructures frequently contain bainite. A after reaustenitisation at 1 000°C. Specimens were etched number of models for the evolution of bainitic microstruc- using 2 vol% nital (nitric acid in methanol) and the mi- tures have been developed1–5) but they either neglect the crostructures were observed using optical, scanning and precipitation of cementite, or treat the whole event as a sin- transmission electron microscopy. Precipitates were charac- gle reaction. It is in principle necessary to permit the simul- terized in a transmission electron microscope (TEM) using taneous formation of cementite and bainitic ferrite, albeit at X-ray energy-dispersive analysis and electron diffraction. different rates, in order to properly deal with upper and Cementite particle sizes were measured directly from TEM lower bainitic microstructures. The latter is distinguished micrographs of the carbon replicas. At least 100 particles from the former by the fact that some cementite is found were analyzed in each case. The carbide shape was found to within the bainitic ferrite plates, whereas in upper bainite be in the form of discs whose thickness and diameters were the carbides only precipitate between the plates. measured. The purpose of the present work was to develop a full ki- netic theory for the bainite reaction and to compare the pre- 3. Modelling dicted phase fractions, particle sizes and the nature of the bainite against experimental data. Figure 1 illustrates the essence of the model, which con- sists of four processes: 1) Diffusionless transformation of austenite into supersat- 2. Experimental Procedure urated bainite. Table 1 shows the chemical composition of steel, which 2) The escape of carbon evacuation from bainitic ferrite with its high carbon concentration should be amenable to into austenite. the upper to lower bainite transition. The steel was melted 3) Cementite precipitation in bainitic ferrite. using vacuum induction heating followed by casting. The 4) Cementite precipitation in carbon-enriched residual ingot was re-heated to 1 200°C and hot-rolled. The sheets austenite. were homogenized at 1 250°C for 3 d and cooled rapidly These reactions can be handled simultaneously using the with air, resulting in a martensitic microstructure which framework developed by Bhadeshia et al.6–8) Extended vol- proved difficult to machine. The samples were therefore austenitised at 850°C, cooled to 600°C and held for 3 000 s Table 1. The chemical composition (mass%). in order to generate softer pearlite which could easily be machined into cylindrical specimens of 10 mm length and 3 mm diameter. These samples were heated in a dilatometer 221 © 2005 ISIJ ISIJ International, Vol. 45 (2005), No. 2 austenite grain boundary sub-unit lower bainite upper bainite microstructure microstructure cementite carbon evacuation carbon evacuation cementite Fig. 1. Schematic illustration of upper and lower bainite mi- crostructure development. Fig. 2. Schematic illustration of the carbon concentration profile at austenite (g)/bainitic ferrite (aB) interface. ume corrections9) were made for the major phases (austen- ite and bainitic ferrite) but were neglected for the cementite which has a small overall fraction.8) The resulting numeri- tion of temperature.12) cal scheme allowed the matrix composition to be modified The transformation exhibits an incomplete reaction in at each stage using the mean-field approximation.7,8) which growth is arrested well before the austenite achieves its para-equilibrium composition, consistent with diffusion- 3.1. Bainitic Ferrite less growth.10) It is therefore reasonable to assume that once The first stage in the transformation is the nucleation and nucleated, the growth rapidly to a finite volume.1,2) The sub- growth of laths or plates of ferrite in the form of arrays of unit size is as a function of temperature, austenite strength sub-units.10) Consistent with experimental evidence,10) it is and driving force for bainitic ferrite formation under para- 13) assumed that nucleation occurs with the diffusion of car- equilibrium. The width of sub-unit WaB, of which unit is bon, and that each plate of bainite also generates other nu- m m, is given by13): clei by autocatalysis. The nucleation rate IaB is then given → Ϫ 1) ϭ g a ϭ ϩ ϫ 4 by : WaB f(T, Sg, DG ) 0.478 1.20 10 T Ϫ → Ϫ ϭ ϩ ϩ1.25ϫ10 4TϪDG g aϪ2.20ϫ10 3Sg.........(6) IaB (1 bVaB)Io ............................(1) where VaB is volume fraction of bainitic ferrite and b is au- where Sg is the strength of austenite in MPa, which has also tocatalysis constant, indicating that the nucleation sites in- been obtained empirically.13) However, the original equation crease in compliance with sub-unit formation. The initial doesn’t include Si effect on the strength, so it was added:14) nucleation rate Io is by classical nucleation theory11): Sgϭ(1Ϫ0.26ϫ10Ϫ2 (TϪ298) RT Qγ ∆Gγα→ B* IoϭϪϪ N exp C exp ......(2) ϩ0.47ϫ10Ϫ5 (TϪ298)20.326ϫ10Ϫ8(TϪ298)3 0 h RT RT ϫ ϫ ϩ ϩ ϩ 15.4 (3.6 23Wc 1.3WSi 0.65WMn) ............(7) where N0 is the initial site density, R and h are gas and g Planck constants respectively and T is temperature in K. QC where Wi is mass% of i-th alloying element. It is assumed is the activation energy for carbon diffusion in austenite be- that the aspect ratio of sub-unit is constant in the tempera- cause the nucleation process has been reported to involve tures between 300 and 500°C. The value is obtained experi- 10) g→aB the diffusion of carbon. DG * is the driving force for mentally to be six so that the length of sub-unit LaB is given bainitic ferrite formation. It is given by12): by: g → aB g → a ϭ DG *ϭDG *ϪGN .....................(3) LaB 6WaB ..................................(8) 16 σ 3 ∆Gγα→ *ϭ π .....................(4) 3.2. Carbon Evacuation From Bainitic Ferrite to ∆ γα→ 3 Gv Austenite GNϭ3.637ϫ(TϪ273.18)Ϫ2 540.................(5) Since the initial growth event is diffusionless, the excess carbon in the ferrite is expected to partition into the resid- where DG g → a* is the driving force for ferrite nucleation. ual austenite or precipitate as cementite. Since carbon diffu- g → a DG v is the chemical free energy change per unit volume sion in austenite is slower than in ferrite, the former is as- for ferrite nucleation under para-equilibrium.10) s is the in- sumed to control the partitioning. Figre 2 illustrates the terfacial energy per unit area. GN is the critical energy carbon concentration profile at the interface between change to form bainitic ferrite nucleus, which is as a func- austenite (g) and bainitic ferrite (aB). The carbon concen- © 2005 ISIJ 222 ISIJ International, Vol. 45 (2005), No. 2 g 15) tration in gX C is given by : servations. The diameter Lq in aB is, then, given by: L ϭ5W ...........................(14) Z q in aB q in aB γγϭϩ γαγ Ϫ .........(9) XXCC() X C X Cerfc γ It is reported that cementite within bainitic ferrite has 2()Dt05. C orientation relationship with bainitic ferrite.19,20) This is g ga ¯ g where X C , X C and XC are carbon concentrations normal caused by decreasing the interfacial energy, which is dealt to g/a B interface in austenite, at the interface under para- as one of fitting parameters in this model. equilibrium and average concentration in austenite respec- g 3.4. Cementite Precipitation in Austenite tively. DC is the diffusion coefficient of carbon in austenite. Z is the distance normal to austenite/bainitic ferrite inter- In upper bainite, cementite grows by a para-equilibrium face. Based on this profile, carbon flux in austenite is de- mechanism from the carbon-enriched residual austen- g 16,17) fined by carbon gradient at g/a B interface. X C increases as ite. Cementite precipitation is modelled by the same carbon evacuation into austenite from bainitic ferrite pro- way as from supersaturated bainitic ferrite as in the previ- ceeds.
Details
-
File Typepdf
-
Upload Time-
-
Content LanguagesEnglish
-
Upload UserAnonymous/Not logged-in
-
File Pages8 Page
-
File Size-